Le Ricerca Scientifica sui materiali polimerici ha portato allo sviluppo di Polimeri ad Alte Prestazioni idonei per molte applicazioni industriali che un tempo erano monopolio di metalli e leghe metalliche. Abbiamo constatato che ci sono applicazioni in cui i metalli risultano sovradimensionati e vengono scelti, a prescindere da valutazioni ingegneristiche, per continuità con il passato. All'opposto, vi sono casi in cui i polimeri migliorano le prestazioni dei metalli. Un'adeguato livello di conoscenza dei materiali polimerici permetterebbe di selezionare il materiale migliore ed ottimizzare il prodotto da realizzare. GHEPI è specializzata nel Metal Replacement, con esperienze maturate fin dai primi anni ’80 per molteplici applicazioni e settori industriali. E' fondamentale il codesign con Clienti e Fornitori grazie al quale abbiamo raggiunto risultati di assoluto rilievo in termini di miglioramento delle performance e maggiore competitività.
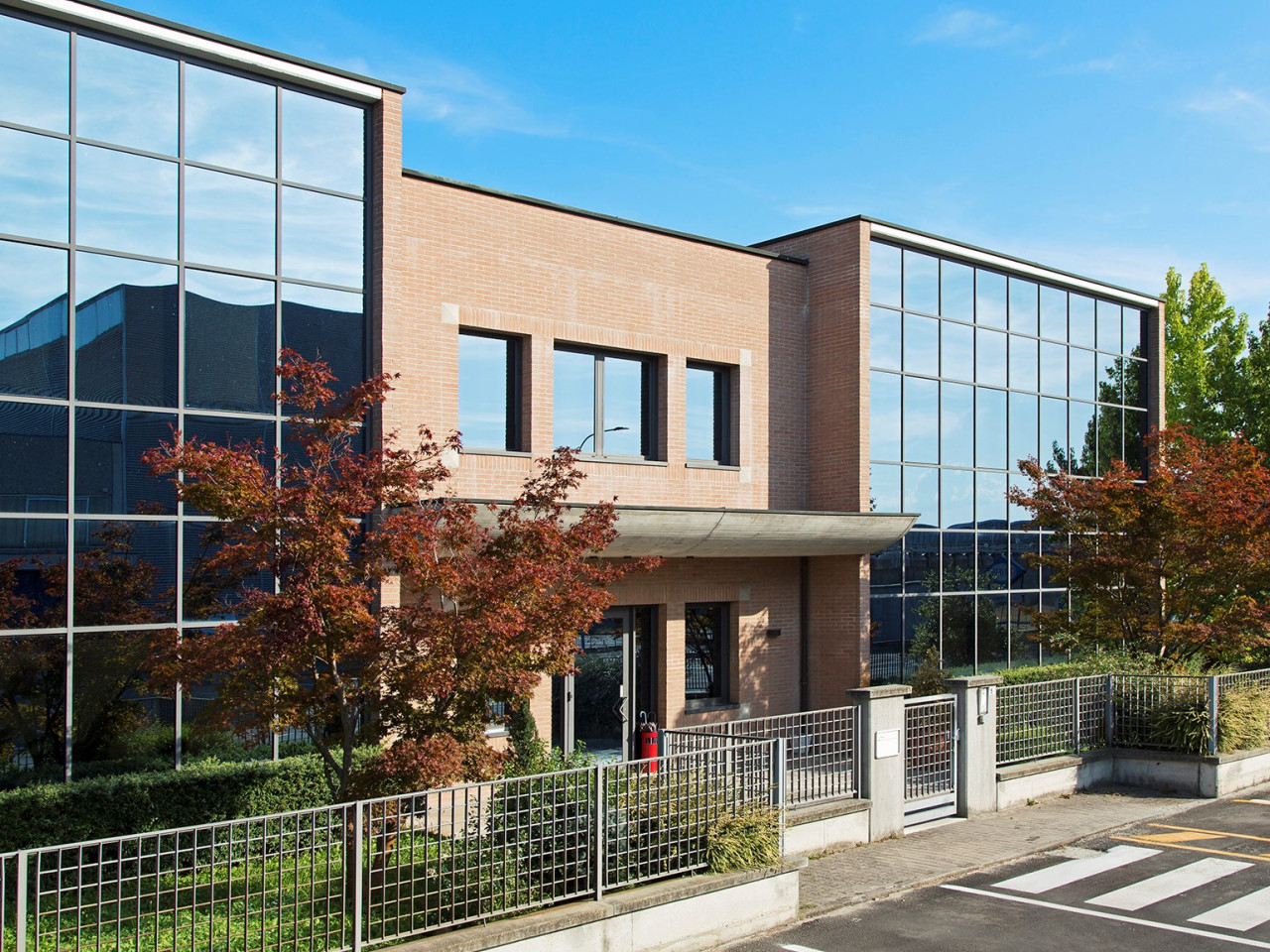
Lo sviluppo di un Progetto di Metal Replacement, gestito dalla funzione di project management, si articola in diversi step, a seconda della complessità del progetto stesso, ovvero della tipologia di applicazione e della numerosità di prodotti da realizzare. Gli step principali dello sviluppo di un Progetto di Metal Replacement sono: definizione dei requisiti di Progetto ed analisi di fattibilità, selezione dei polimeri idonei all’applicazione, analisi comparativa esperienziale, design review sul progetto del Cliente, progettazione e modellazione 3D, simulazione fluidodinamica (analisi CFD), analisi FEM, FMEA di Prodotto e di Processo, risk analysis, prototipazione (rapid prototyping and tooling, additive manufacturing, lavorazione meccanica, stampi pilota). Dopo il consolidamento della fase di engineering si passa alla fase di industrializzazione con la progettazione e costruzione stampo, collaudo stampo e campionatura articolo (prima impostazione dei parametri di processo), sperimentazione con i polimeri selezionati (comportamento in stampaggio, parametri di controllo e piano di campionamento), messa a punto dello stampo e successiva campionatura per la definizione degli standard di processo, process capability.
Sono riferiti a: funzionalità del prodotto, semplificazione del processo produttivo, tempi e costi. In particolare: riduzione di peso (peso specifico e progettazione); sostenibilità ambientale: il peso inferiore genera un minor dispendio di energia e la riduzione di emissioni di CO2; integrazione funzionale e riduzione delle fasi di lavorazione: un'accurata progettazione può consentire di eliminare componenti singoli da assemblare in seguito e/o lavorazioni di finitura; riduzione del time to market e del lead time; miglioramento delle prestazioni grazie a caratteristiche dei polimeri.
Le applicazioni potenziali sono molteplici e un primo livello di base è rappresentato da articoli che vengono realizzati in materiali metallici solo per tradizione, ovvero senza un'analisi ingegneristica, con sovradimensionamento delle prestazioni che provoca inutili e significativi sprechi. A seguire vi sono le applicazioni "pensate in plastica" ovvero progettate e industrializzate per i materiali polimerici. Gli ambiti industriali di applicazione sono i più svariati, dalla componentistica meccanica di precisione a prodotti finiti con caratteristiche estetiche.
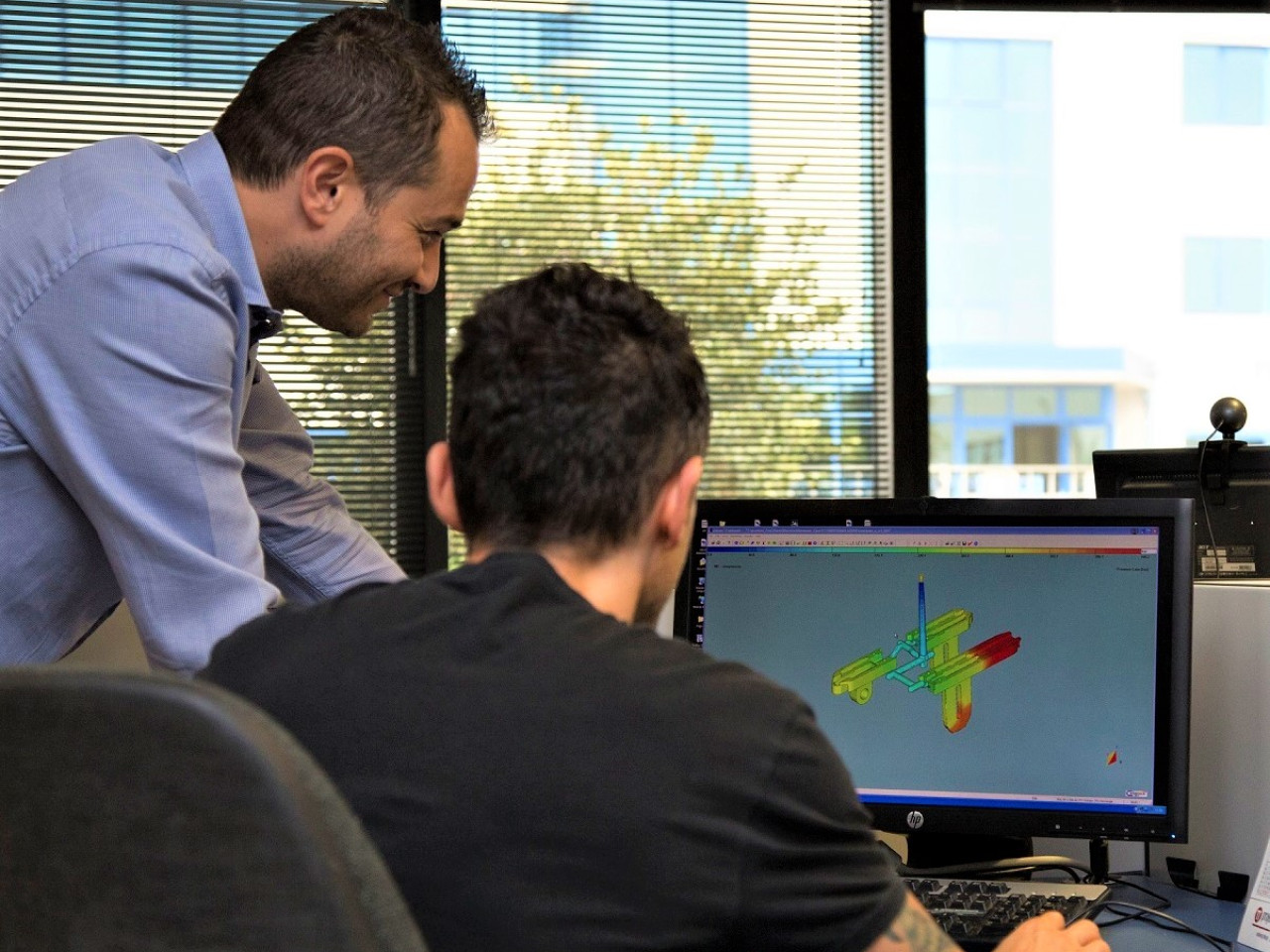
Pianale di supporto e scorrimento dei vassoi per macchine automatiche da food-packaging
Consiste in un pianale su cui vengono posizionati e devono scorrere i vassoi, riempiti di alimenti, prima di entrare nella macchina automatica per il confezionamento con film estensibile e l'etichettatura. Requisiti del progetto: elevata stabilità dimensionale e geometrica, autolubrificazione superficiale, elevata rigidità e resistenza all’urto. Criticità da affrontare: selezione di un unico polimero per soddisfare requisiti in parte contrastanti (l’anisotropia dovuta alla fibra di vetro ostacola la stabilità dimensionale e geometrica); grandi dimensioni (680x400mm) che amplificano le deformazioni; ritiro post-stampaggio molto differenziato tra longitudinale e trasversale alla fibra; superficie lucida per ottenere la massima autolubrificazione del PTFE. Risultati ottenuti: riduzione di peso del 35% (da 3,4 a 2.2 Kg); integrazione di funzioni con eliminazione delle guide riportate in PTFE e del successivo assemblaggio e della lavorazione di anodizzazione dell'alluminio. Vantaggi diretti: riduzione dei costi superiore al 25% e del Lead time per la riduzione delle fasi di lavorazione. Versione precedente: struttura in alluminio con guide riportate in PTFE, componentistica metallica a disegno e normalizzata per l'assemblaggio di tutti i componenti. Versione Metal Replacement: monoblocco in PA66 20FV e 20PTFE con 1/5 dei componenti precedenti.
Il progetto è stato gestito da GHEPI in codesign con il Cliente e i Fornitori dei polimeri selezionati.
Grazie alla progettazione specifica per i polimeri e alle soluzioni proposte, il Progetto ha conseguito i risultati previsti. Elementi di rilievo: riduzione di peso ed integrazione di funzioni con riduzione del numero di componenti e fasi di lavorazione. Ciò conferma la fattibilità del Metal Replacement in applicazioni funzionali soggette a sollecitazioni che richiedono prestazioni meccaniche.
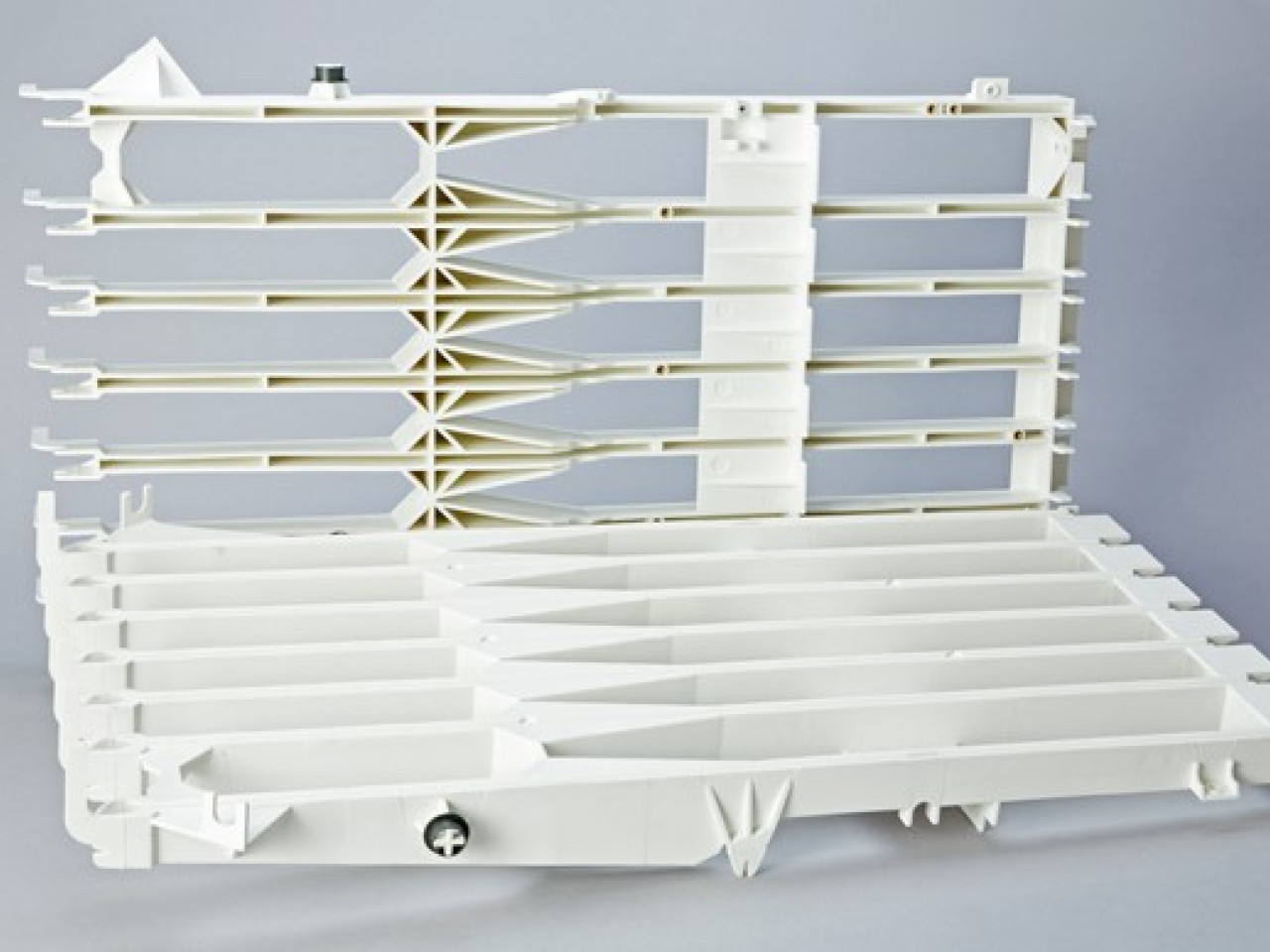