The efficiency requirements of household appliances are increasingly stringent in response to the growing global demand for saving energy resources. This process involved the use of new technologies and the development of cutting-edge techniques to improve the efficiency of products, such as the movement of the washing machine drum.
The objective of the activity was the development of an optimized control for internal permanent magnet (IPM) synchronous motors to be used in place of traditional asynchronous motors in household washing machines. This solution made it possible to increase the overall efficiency of the application and reduce costs, however greater complexity of the control algorithms had to be accepted. The main critical issues addressed were: development of a sensorless control capable of delivering the nominal torque at zero speed and optimization of the MTPA (Maximum Torque per Ampere) and field weakening trajectories to maximize efficiency.
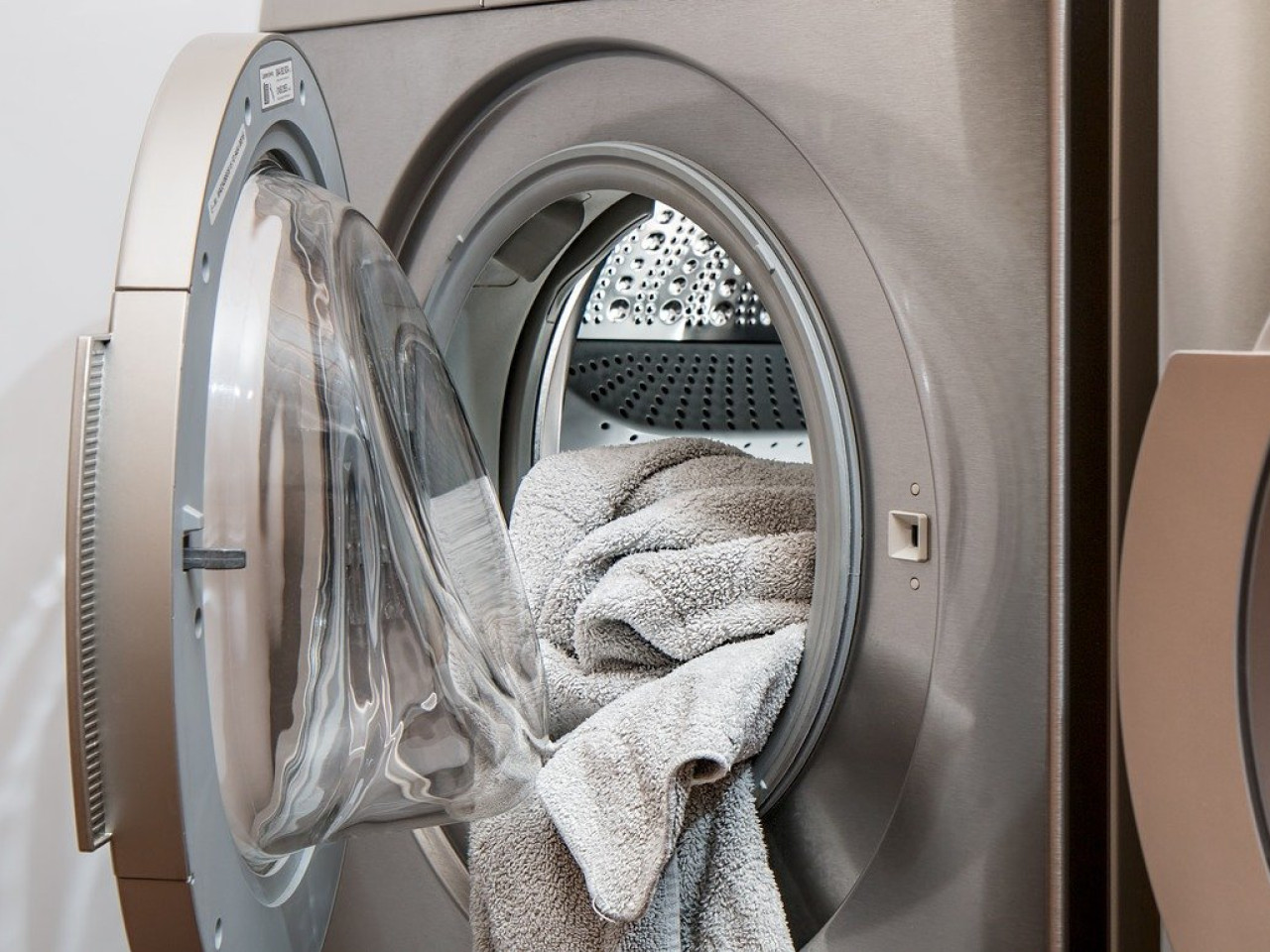
For the implementation of sensorless control, two algorithms were defined: the first with injection of a high frequency signal responsible for identifying the rotor position, from a stationary rotor up to a few hundred revolutions per minute; the second is used for higher speeds (up to 18,000 rpm) and exploits the estimate of the Back-electromotive (Back-EMF) forces starting from the mathematical model of the electric motor. The second method is ineffective at low speeds because the magnitude of the Back-EMF forces is proportional to the rotation speed of the rotor.
The signal injection algorithm exploits the anisotropy of the IPM electric machine to estimate the rotor position even at zero speed, thus making it possible to deliver the nominal torque efficiently right from the start.
Once the sensorless vector control was developed, the activity moved to the implementation of the MTPA strategy with the machine parameters; this strategy is able to provide the right contribution of direct axis current to exploit the torque given by the anisotropy of the machine (i.e. reluctance torque). The weakening strategy is necessary to reach the rotation speeds of 18,000 rpm; for the application, a closed loop control has been implemented capable of increasing the current contribution on the direct axis if the applicable voltage limit is reached.
The innovative aspects of the developed system are: the sensorless control of the motor with high frequency signal injection which allows to have an estimate of the rotor position at the start of the washing machine drum, i.e. at zero speed, and the optimization of the trajectories of the washing strategies control at low speeds (MTPA) and high speeds (weakening) to maximize overall system efficiency.
The developed control can be used in various industrial applications; in particular where an economical, efficient solution with good performance even at low rotation speeds is essential.
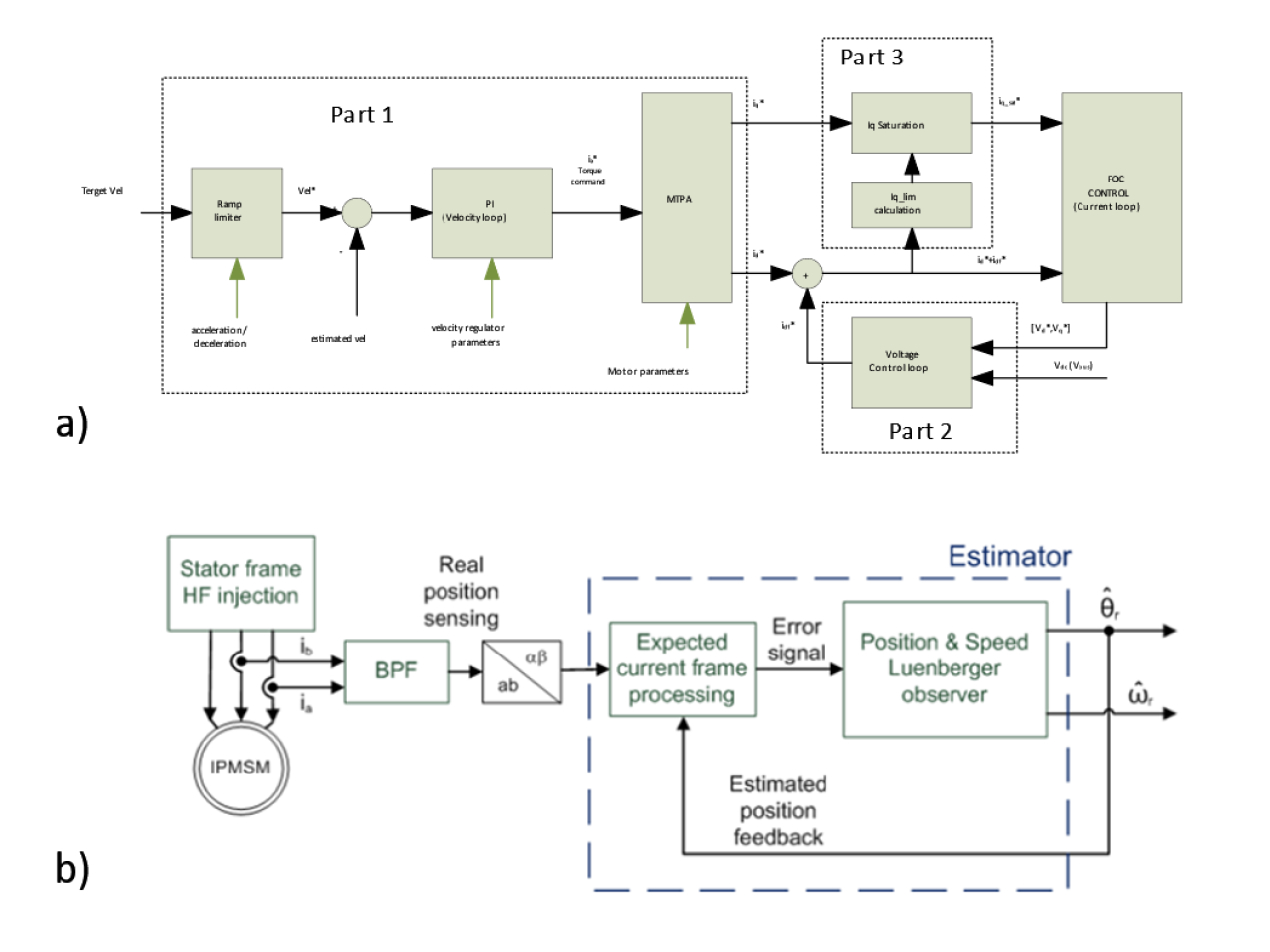
IPM brushless motor drive used to move the drum of domestic washing machines.
The control was developed and tested on applications for the home appliances sector, in particular on domestic washing machines. The application is characterized by very stringent constraints in terms of both costs and performance, in fact excellent performance is required at the start to be able to move even loads that require the nominal torque and excellent efficiency during the work cycle.
Thanks to the optimized control algorithms it was possible to improve the efficiency of the washing machines by 30% during the washing cycle which represents the longest working cycle of the application. The comparison was carried out with respect to the same work cycle with the traditional asynchronous motor.
- Raw Power S.r.l.
- Candy Hoover Group S.r.l.
The developed control will be adopted on commercial domestic washing machines.
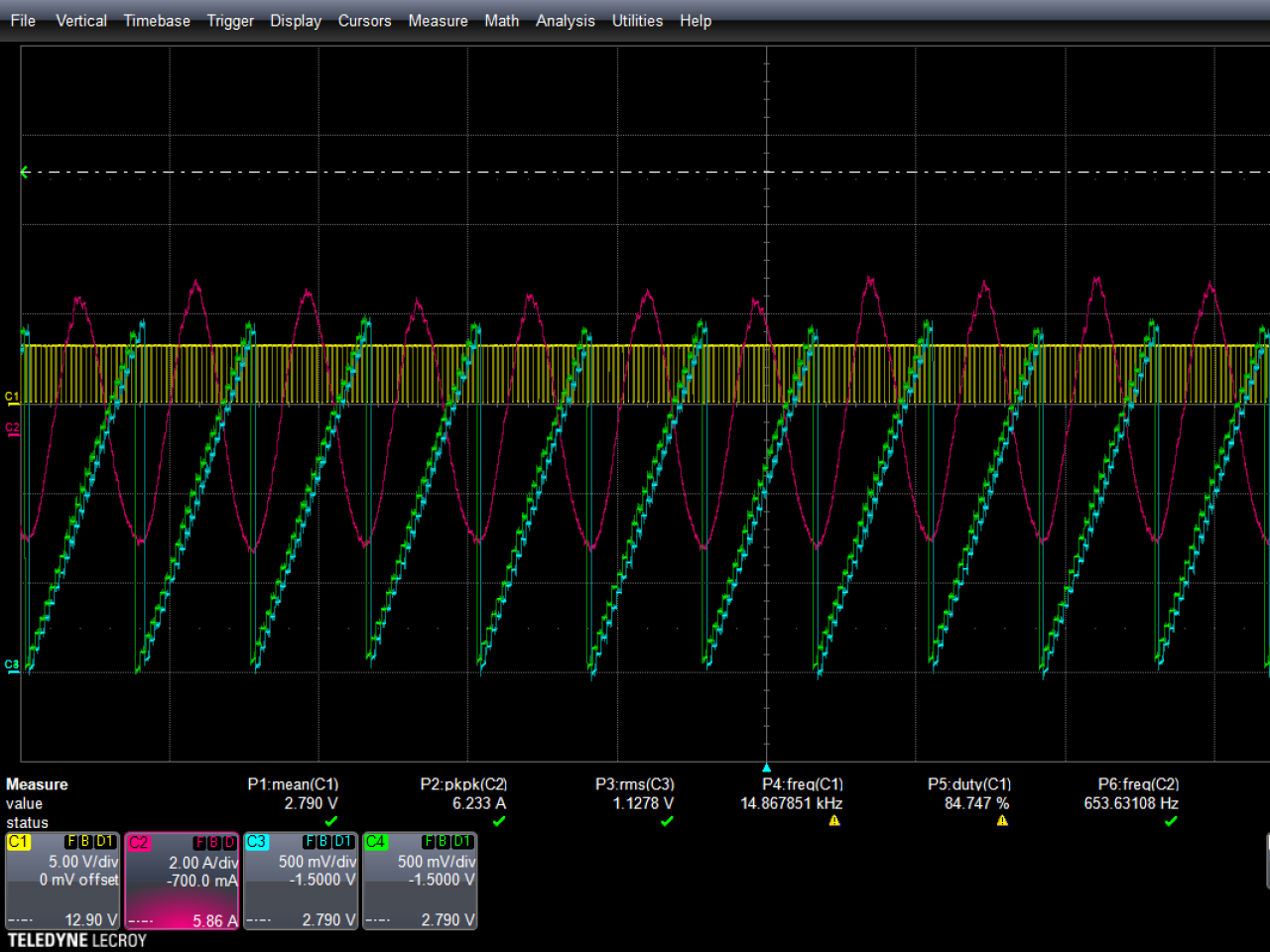