Nei settori dell’aerospazio e dei trasporti veloci vi è una crescente domanda di materiali avanzati strutturali in grado di sopportare temperature oltre 1500°C in ambienti altamente corrosivi. Gli ugelli per razzi e i sistemi di protezione termica per veicoli spaziali che volano a velocità ipersonica devono essere in grado di resistere a flussi di calore intenso e sollecitazioni meccaniche estreme al momento del lancio e del re-ingresso nell'atmosfera terrestre. Nei trasporti veloci sono i sistemi frenanti le componenti più soggette ad usura e temperatura.
La necessità di leggerezza, la combinazione di temperature estreme, rapidi cicli riscaldamento/raffreddamento e ambienti chimicamente aggressivi sono condizioni che hanno portato alla realizzazione dei compositi a matrice ceramica (C/SiC, SiC/SiC) e i compositi a matrice di carbonio (C/C) negli anni ‘60 e ’80. Attualmente c’è un forte interesse a innovare i processi di produzione di questi materiali per abbattere tempi, costi di produzione e realizzare una versione ad altissima durabilità alternativa ai compositi carbon_carbon.
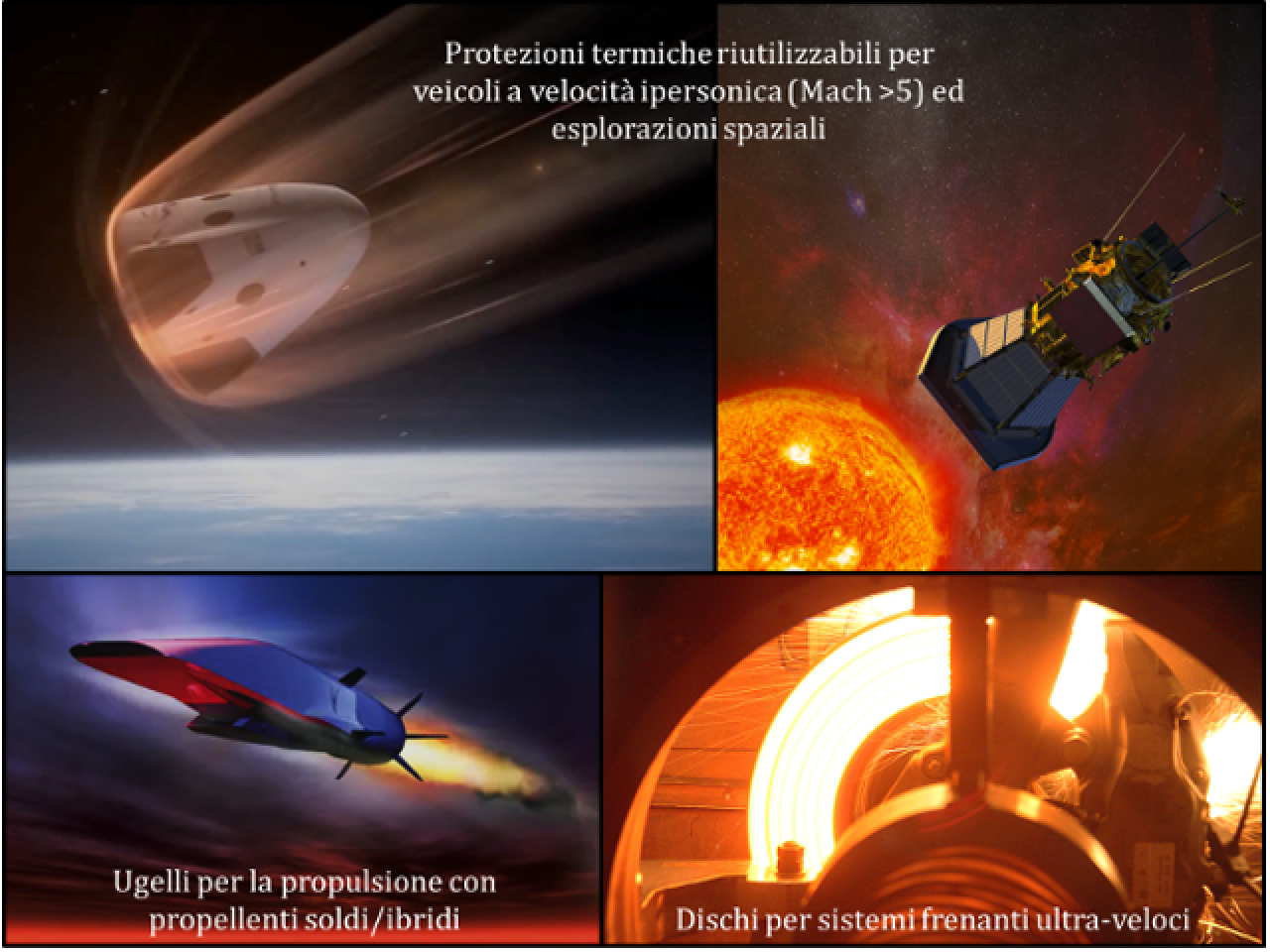
La nuova tecnologia messa a punto dai ricercatori ISTEC permette di realizzare CMC di nuova generazione a matrice ceramica ultra-refrattaria, chiamati nella letteratura scientifica UHTCMCs.
Il processo brevettato permette di realizzare materiali ad alto valore aggiunto in tempi rapidi, con riguardo all’aspetto eco-sostenibile del processo. Dal punto di vista tecnico il processo si basa principalmente su 1) impregnazione di tessuti in fibra di carbonio con miscele di polveri ceramiche ultra-refrattarie e 2) consolidamento mediante sinterizzazione. La nuova tecnologia mira a realizzare i primi componenti per temperature superiori ai 2000°C made in Italy, utili a equipaggiare la prossima generazione di lanciatori di satelliti, supercar, treni ad alta velocità etc.
I materiali UHTCMC brevettati da CNR-ISTEC (concessione n° 102016000008310) sono stati validati fino a TRL 5 come protezioni termiche per il rientro in atmosfera di veicoli spaziali a velocità ipersonica e fino a TRL 6 per applicazione di propulsione nei lanciatori di satelliti a propellente solido. Il design, la produzione e i test sono stati realizzati all’interno del progetto europeo C3harme (Next Generation Ceramic composites for combustion harsh environment and space - GA 685594), coordinato da ISTEC. Tale progetto ha raccolto un consorzio di 12 partner, comprendente industrie del comparto aerospazio (AVIO, AIRBUS, ARIANE Group). Durante il progetto sono stati realizzati da ISTEC e testati dai partners numerosi prototipi di piastre e componenti dei motori a propulsione dimostrando durabilità e riusabilità a temperature > 1800°C. E’ in corso un progetto con ESA (Wintertime) dove i materiali UHTCMC saranno testati sulla stazione spaziale internazionale (ISS).
I materiali UHTCMC si distinguono dai materiali CMC prodotti industrialmente e in fase di sviluppo in altri centri di ricerca per:
- elevato contenuto di fase ultra-refrattaria UHTC (fino a 60%) e perfetta omogeneizzazione della fibra con la fase ceramica,
- consolidamento per sinterizzazione veloce (da poche ore a 1 giorno), il chè comporta notevole riduzione dei tempi di produzione,
- assenza di porosità, necessaria per ottenere un’eccezionale resistenza ad usura,
- assenza di rivestimenti protettivi (non necessari per le caratteristiche del materiale),
- miglioramento delle proprietà meccaniche all’aumentare della temperatura,
- ottima lavorabilità per ottenere forme complesse.
Per realizzare scudi termici riutilizzabili per veicoli ipersonici e componenti dei motori a razzo dei lanciatori di satelliti a zero usura è necessario ingegnerizzare il processo di produzione per ottenere prototipi adatti al raggiungimento di TRL maggiori, 8-9 (aerospazio) e TRL 5 (sistemi frenanti). In particolare è necessario ottenere le certificazioni delle agenzie spaziali (ESA e ASI) e/o l’interesse di aziende private a testare i componenti a altissimo TRL per aerospazio (AVIO, SPACEX; VIRGIN GALATTICA; THALES) e intermedio per i sistemi frenanti (BREMBO). E’ quindi necessario realizzare un network di aziende manifatturiere italiane per procedere all’implementazione industriale della tecnologia mediante la realizzazione di una linea pilota con eventuali processi automatici di formatura e di consolidamento del materiale che preveda sistemi di controllo della qualità del prodotto.
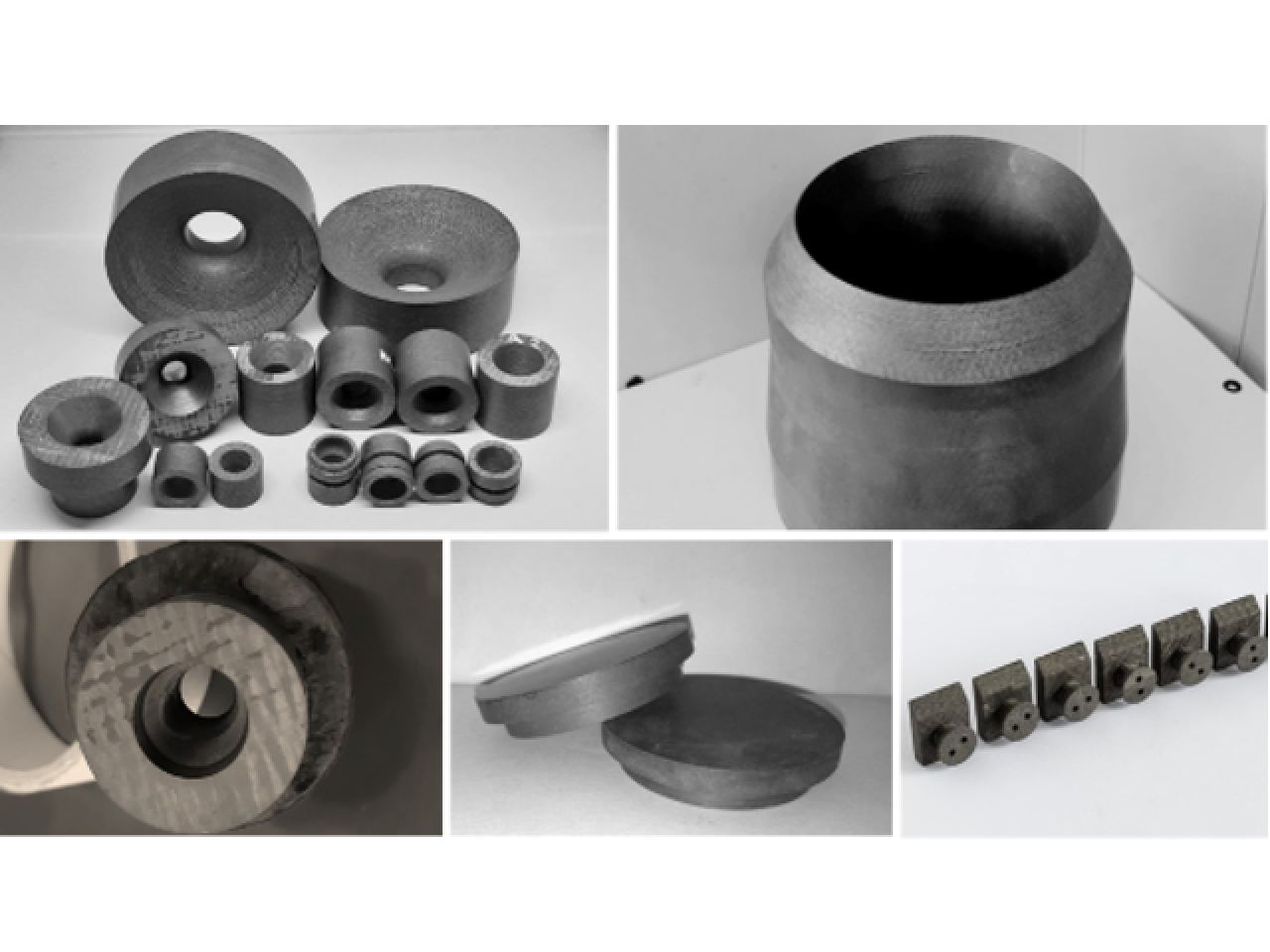
Nei settori dell’aerospazio e dei trasporti veloci vi è una crescente domanda di materiali avanzati strutturali in grado di sopportare temperature oltre 2000°C in ambienti altamente corrosivi. Gli ugelli per razzi e i sistemi di protezione termica per veicoli spaziali che volano a velocità ipersonica devono essere in grado di resistere a flussi di calore intenso (da 1 a 10 MW×m-2) e sollecitazioni meccaniche estreme al momento del lancio e del re-ingresso nell'atmosfera terrestre.
Durante il progetto C3harme sono stati realizzati da ISTEC e testati dai partners (AVIO, UNINA, DLR) decine di prototipi di piastre (protezioni termiche velivolo spaziale) e componenti dei motori a propulsione (ugelli) dimostrando durabilità e riusabilità delle componenti a temperature oltre i 2000°C ed una usura quasi nulla. I test di riusabilità (tre volte) sono stati superati con ampio margine.
Per ulteriori informazioni vedasi www.c3harme.eu e alcune pubblicazioni scientifiche:
S. Mungiguerra, G.e D. Di Martino, R. Savino, L. Zoli, L. Silvestroni, D. Sciti, Characterization of novel ceramic composites for rocket nozzles in high-temperature harsh environments, Int. J.Heat and Mass Transfer, 163 (2020), 120492, https://doi.org/10.1016/j.ijheatmasstransfer.2020.120492
S. Mungiguerra, G. D. Di Martino, A. Cecere, R. Savino, L. Zoli, L. Silvestroni, D. Sciti, Ultra-high-temperature testing of sintered ZrB2-based ceramic composites in atmospheric re-entry environment, International Journal of Heat and Mass Transfer, Volume 156, 2020, 119910, https://doi.org/10.1016/j.ijheatmasstransfer.2020.119910.
A. Vinci, L. Zoli, D. Sciti, J. Watts, G.E. Hilmas, W.G. Fahrenholtz, Influence of fibre content on the strength of carbon fibre reinforced HfC/SiC composites up to 2100 °C, J. Eur. Ceram. Soc. 39 (2019) 3594–3603. doi:https://doi.org/10.1016/j.jeurceramsoc.2019.04.049.
Avio S.p.A., Italia. https://www.avio.com/
Arianegroup, Germania, https://www.ariane.group/en/
Airbus Group, Germania http://www.airbus.com/
Nanoker research, Spagnia, http://www.nanoker.com/
Univesità di Napoli, http://www.unina.it/
DLR, Gemania, http://www.dlr.de
K3RX - Extraordinary Ceramics, è il nuovo spinoff del CNR la cui attività principale è quella di offrire componenti per il mercato spaziale e il trasporto ad alta/iper velocità sostituendo i prodotti attuali, con materiali più resistenti e meno costosi sfruttando i brevetti CNR:
a) Materiali compositi a base di fibre C/SiC con matrice ultrarefrattaria ad alta tenacità e resistenza all’ablazione, n° 102016000008310 27 (CNR10464)
b) Procedimento per ottenere ceramici ultra-refrattari compositi rinforzati con fibre n° 102018000010441, PCT/IB2019/059964 (CNR10561)
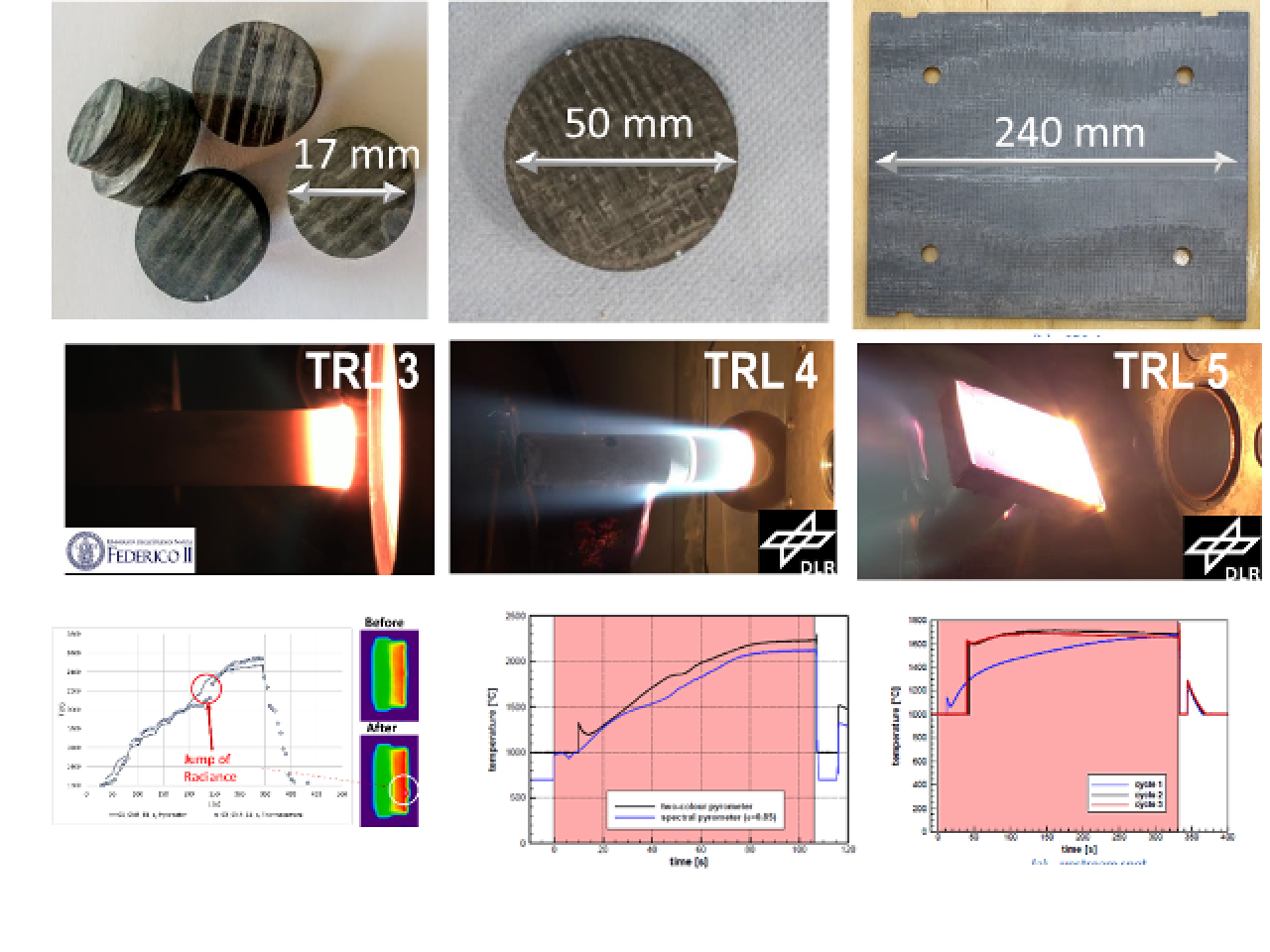