In the aerospace and fast transport sectors there is a growing demand for advanced structural materials capable of withstanding temperatures over 1500 °C in highly corrosive environments. Rocket nozzles and thermal protection systems for spacecraft flying at hypersonic speeds must be able to withstand intense heat flows and extreme mechanical stress upon launch and re-entry into the Earth's atmosphere. In fast transport, the braking systems are the components most subject to wear and temperature. The need for lightness, the combination of extreme temperatures, rapid heating / cooling cycles and chemically aggressive environments are requirements that led researchers to develop ceramic matrix composites (C/SiC, SiC/SiC) and carbon_carbon (C/C) in the 60s and 80s. There is currently a strong interest in innovating the production processes of these materials to reduce production times, costs and create a very high-durability version as an alternative to carbon_carbon composites.
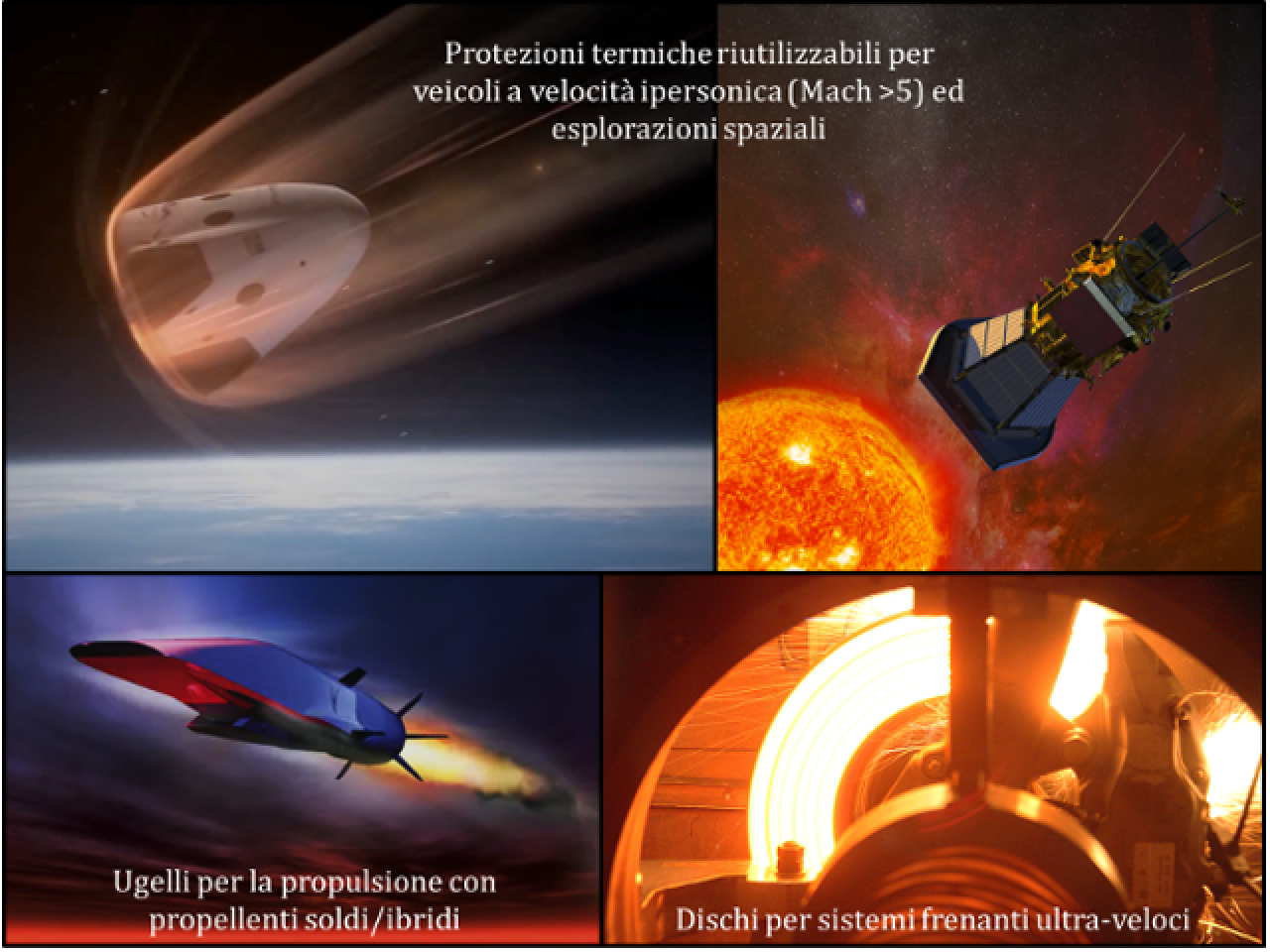
The new technology developed by the researchers of ISTEC allows to fabricate new generation CMCs with an ultra-high temperature ceramic matrix, called UHTCMCs in the scientific literature. The patented process is faster, cheaper, safer and more eco-friendly than industrials methods to realize current CMCs. From a technical point of view, the process is mainly based on 1) impregnation of carbon fiber fabrics with mixtures of ultra-high temperature ceramic powders and 2) consolidation by sintering. The new technology aims to obtain the first components for temperatures above 2000 ° C made in Italy, useful for equipping the next generation of satellite launchers, supercars, high-speed trains etc.
The UHTCMC materials patented by CNR-ISTEC ( n ° 102016000008310) have been validated at temperature above 1800 °C (TRL 5) as thermal protections for the re-entry into the atmosphere of spacecraft at hypersonic speed and (TRL 6) as rocket nozzle for propulsion applications in hybrid and solid propellant bench-top motor. The design, manufacturing and testing were carried out within a consortium of 12 partners, including industries in the aerospace sector (AVIO, AIRBUS, ARIANE Group) in the frame of an European project - C3harme (Next Generation Ceramic composites for combustion harsh environment and space - GA 685594), coordinated by ISTEC. The next step is to test UHTCMC materials on the International Space Station (ISS) within a Wintertime project coordinate by ESA and CNES.
UHTCMC materials distinguish themselves from CMC materials industrially produced and under development in other research centers by:
• content of UHTC phase up to 60% and perfect homogenization of the fibre with the ceramic phases,
• consolidation by fast sintering (from a few hours to 1 day), which involves a considerable reduction in production times,
• absence of porosity, necessary to obtain exceptional resistance to wear and ablation,
• absence of protective coatings (not necessary due to the characteristics of the material),
• improvement of mechanical properties with increasing temperature,
• excellent workability to obtain complex shapes.
To manufacture reusable near-zero ablation heat shields for hypersonic vehicles and near-zero erosion rocket engine components of satellite launchers, it is necessary to engineer the production process to obtain prototypes suitable for achieving higher TRLs, 8-9 (aerospace) and TRL 5 (systems braking). In particular, it is necessary to collect the interest of private companies in testing the components with very high TRL e.g AVIO, SPACEX; VIRGIN GALATTICA, BREMBO etc. We aim to create the first network of Italian manufacturing companies on this technology.
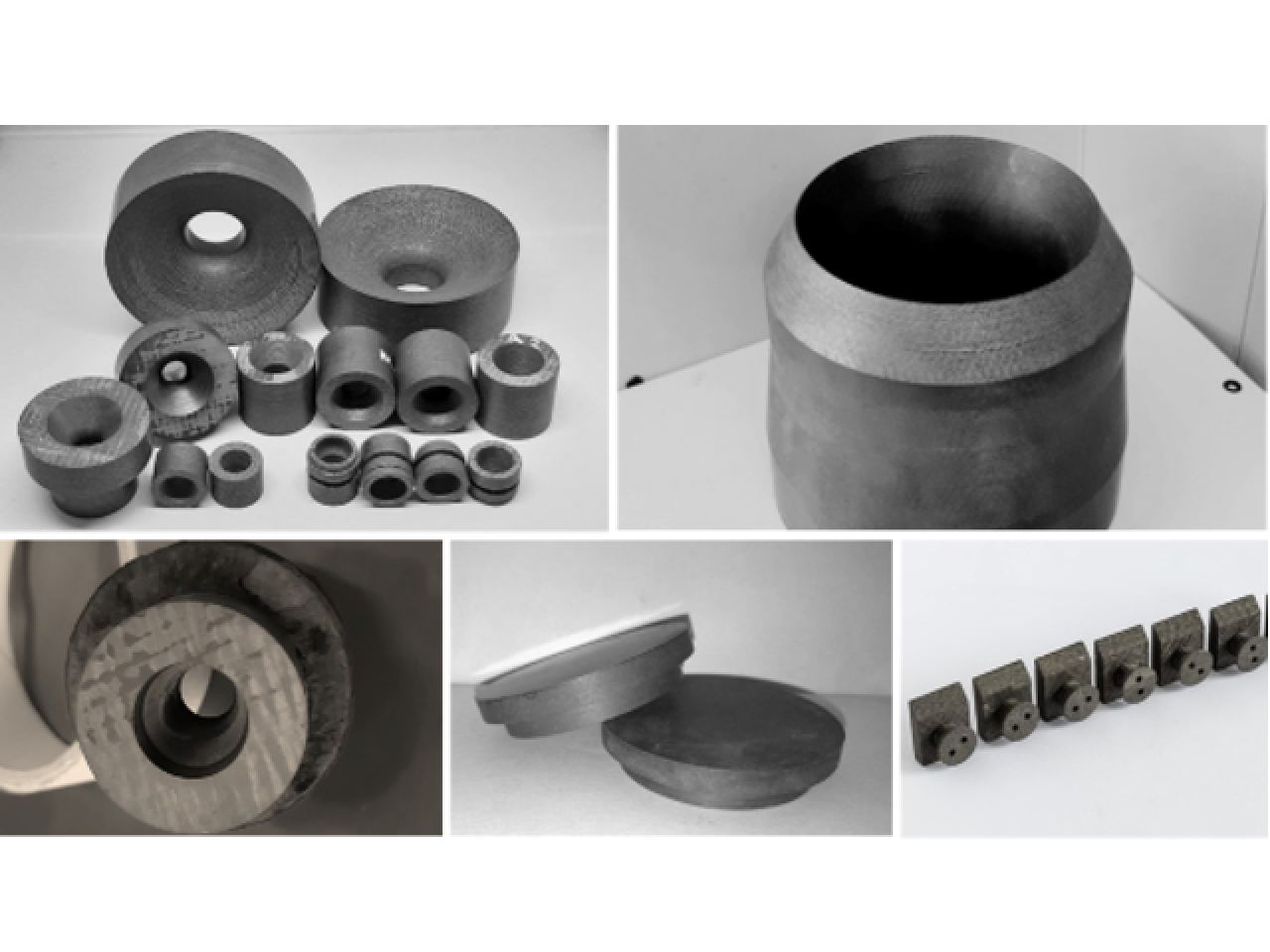
In the aerospace and fast transport sectors there is a growing demand for advanced structural materials capable of withstanding temperatures over 2000 °C in highly corrosive environments. Rocket nozzles and thermal protection systems for spacecraft flying at hypersonic speeds must be capable of withstanding intense heat flows (1 to 10 MW×m-2) and extreme mechanical stresses upon launch and re-entry into the earth's atmosphere.
During the C3harme project, dozens of prototypes of plates (spacecraft thermal protectors) and propulsion engine components (nozzles) were manufactured and tested by partners (AVIO, UNINA, DLR), demonstrating durability and reusability of the components at temperatures over 2000 °C and almost no erosion or ablation. The reusability tests (three times) were passed by a large margin.
For more information see www.c3harme.eu and some scientific publications:
S. Mungiguerra, G.e D. Di Martino, R. Savino, L. Zoli, L. Silvestroni, D. Sciti, Characterization of novel ceramic composites for rocket nozzles in high-temperature harsh environments, Int. J.Heat and Mass Transfer, 163 (2020), 120492, https://doi.org/10.1016/j.ijheatmasstransfer.2020.120492
S. Mungiguerra, G. D. Di Martino, A. Cecere, R. Savino, L. Zoli, L. Silvestroni, D. Sciti, Ultra-high-temperature testing of sintered ZrB2-based ceramic composites in atmospheric re-entry environment, International Journal of Heat and Mass Transfer, Volume 156, 2020, 119910, https://doi.org/10.1016/j.ijheatmasstransfer.2020.119910.
A. Vinci, L. Zoli, D. Sciti, J. Watts, G.E. Hilmas, W.G. Fahrenholtz, Influence of fibre content on the strength of carbon fibre reinforced HfC/SiC composites up to 2100 °C, J. Eur. Ceram. Soc. 39 (2019) 3594–3603. doi:https://doi.org/10.1016/j.jeurceramsoc.2019.04.049.
Avio S.p.A., Italy. https://www.avio.com/
Arianegroup, Germany, https://www.ariane.group/en/
Airbus Group, Germany http://www.airbus.com/
Nanoker research, Spain, http://www.nanoker.com/
Federico II, Italy http://www.unina.it/
DLR, Gemany, http://www.dlr.de
K3RX (www.k3rx.com) is the new CNR spinoff whose main activity is to offer components for the space market and high / hyper speed transport by exploiting CNR patents:
a)COMPOSITE MATERIAL BASED ON C/SIC FIBERS WITH ULTRA-REFRACTORY, HIGH TENACITY AND ABLATION RESISTANT MATRIX
b)PROCEDURE FOR OBTAINING ULTRA-REFRACTORY CERAMICS FIBER REINFORCED COMPOSITES
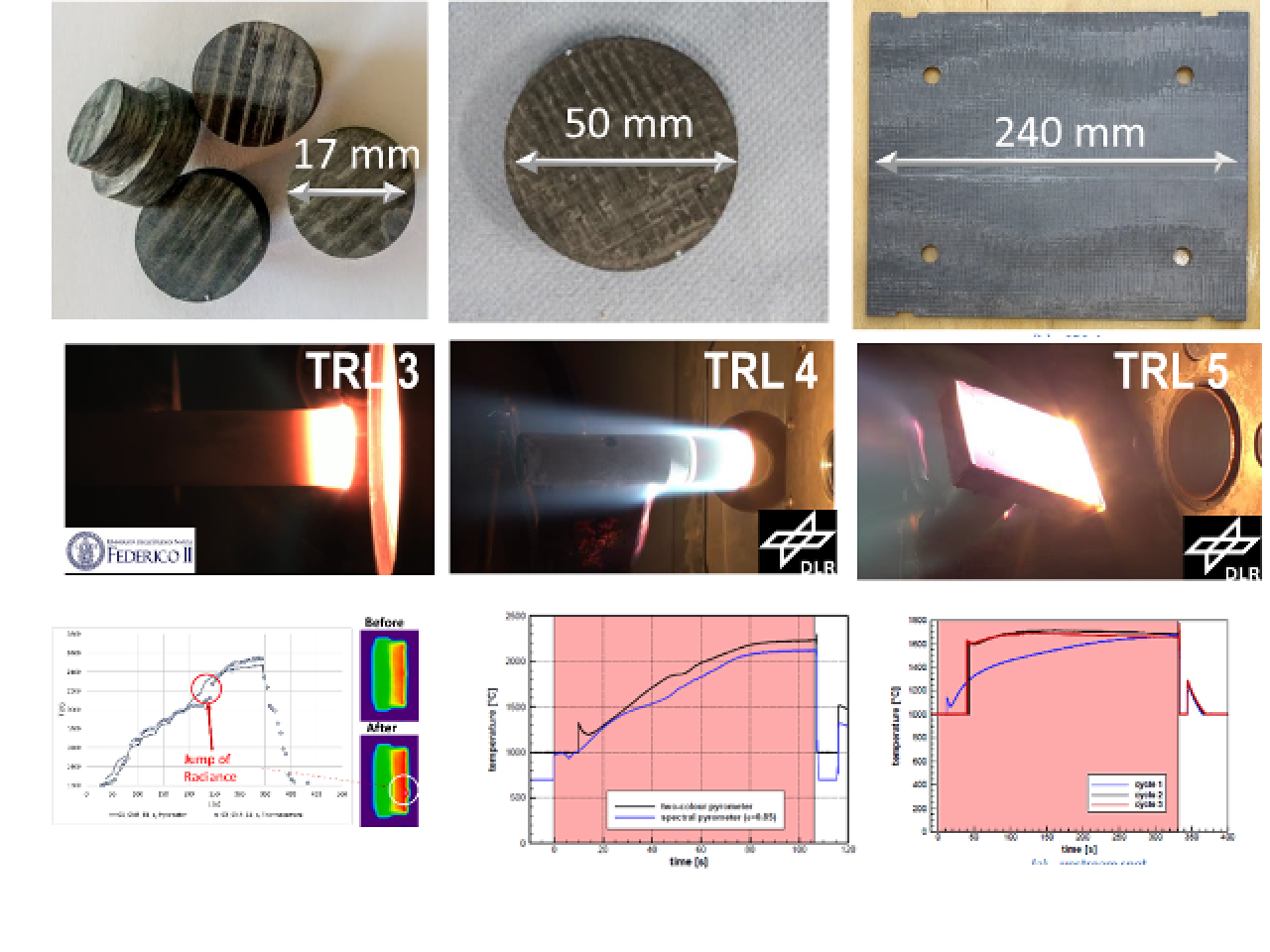