Benchmarking di tecnologie per l'identificazione di difetti interni, come trucioli o errori di lavorazione, nelle sedi interne o fori ricavati da lavorazioni meccaniche o da fusione, che possono portare a malfunzionamenti. Lo studio si è focalizzato su soluzioni tecnologiche automatizzabili, in grado di svolgere la misura e il controllo senza la supervisione di un operatore che al contrario, nel processo attuale di controllo manuale, è necessario.
La prima tecnologia testata è la misura mediante interferometro laser rotante. Questo approccio prevede l'uso di una testina laser rotante inserita nella cavità da ispezionare per ricostruire una nuvola di punti tridimensionale della superficie interna. Questa tecnologia è usata solo in industrie high-tech come avionica e automotive. La tecnologia non nasce in senso stretto per misurare diametri, ma permette di ricostruire il volume interno di una cavità con precisione micrometrica. Da qui la capacità di eseguire misure e controlli qualità. È stata da noi adattata al caso di studio, tramite specifici algoritmi di analisi del segnale ottimizzati per rilevare la presenza di trucioli. Tuttavia, il range di messa a fuoco di questa tipologia di strumenti è limitato e non è adatto a ricostruire geometrie con cavità profonde.
La seconda tecnologia testata è la misura mediante algoritmi automatici di analisi dell’immagine. Per la raccolta delle immagini si sono testati: endoscopi e panoramascopi, installabili su un robot collaborativo, per automatizzare le procedure d'ispezione.
I test sperimentali con le due tecnologie hanno generato un dataset di immagini rappresentativo, utilizzato per addestrare una rete neurale.
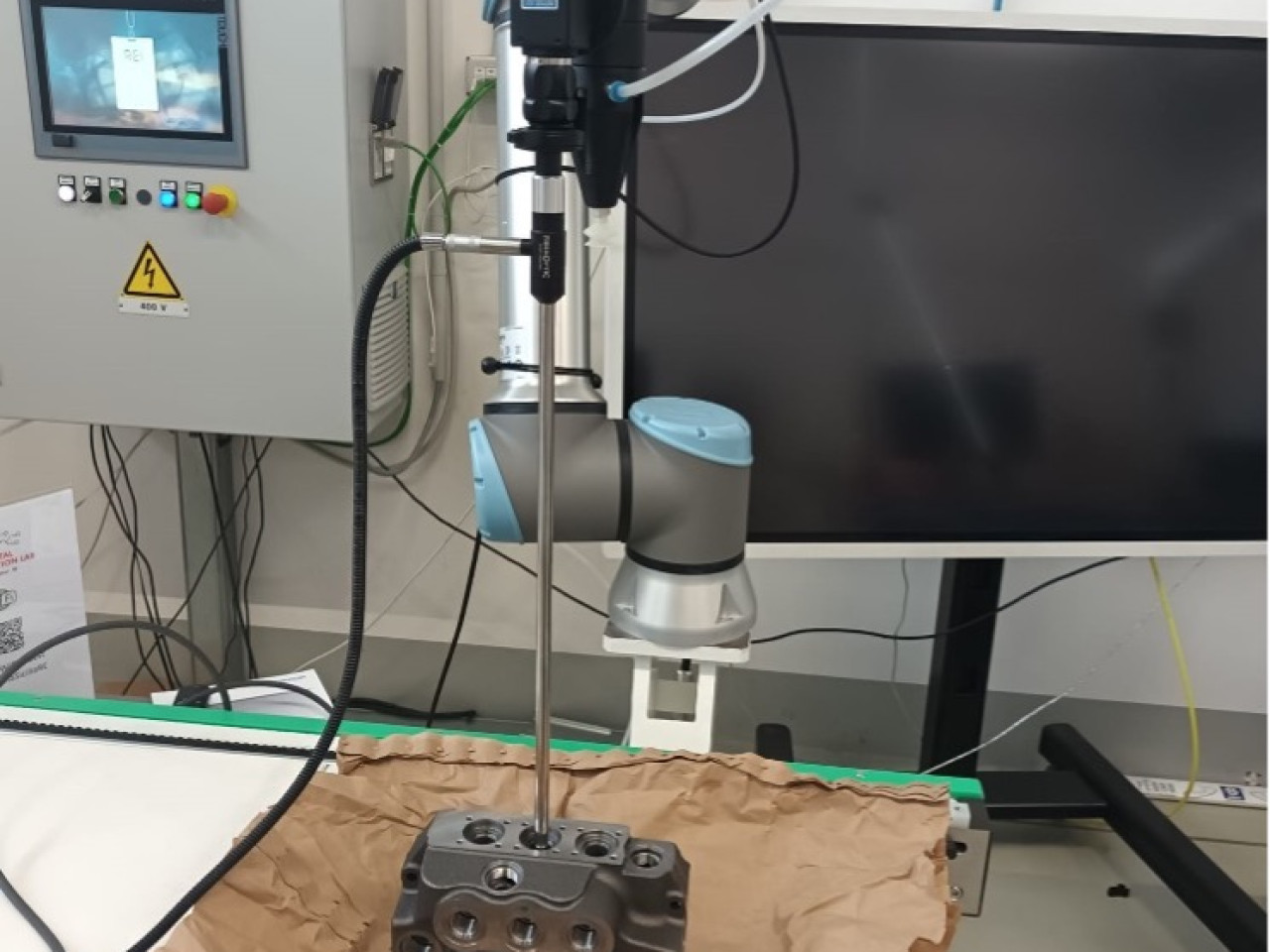
Il prodotto è un sistema automatizzato per l'ispezione e l'identificazione dei difetti interni nei distributori oleodinamici, mirato a migliorare l'efficienza e la precisione del controllo qualità nel settore manifatturiero.
Si rivolge principalmente a produttori di componenti meccanici che richiedono alta affidabilità e precisione nelle misurazioni e verifiche di qualità. Il sistema può essere installato su un braccio robotico o su un sistema di movimentazione automatico, ove vi sia la necessità di controllare al 100% i componenti con tempi ridotti ed alta efficienza. Il sistema di visione è usato anche per il centraggio automatico dell'endoscopio all'interno dei fori.
Il sistema funziona mediante l'utilizzo di tecnologie avanzate per l'analisi delle superfici interne delle cavità. Per ottenere questo risultato si utilizzano due diversi approcci tecnologici: la misura mediante interferometro laser rotante e l'analisi delle immagini tramite algoritmi automatici. L'interferometro laser rotante utilizza una testina laser per creare una mappa tridimensionale delle superfici interne, rilevando eventuali trucioli o difetti con alta precisione. Gli algoritmi di analisi delle immagini, invece, utilizzano endoscopi o panoramascopi per acquisire immagini delle cavità, che vengono poi analizzate da una rete neurale per classificare i pezzi come conformi o non conformi.
Questo sistema permette di sostituire l'ispezione manuale, riducendo il margine di errore umano e aumentando la velocità del processo di controllo qualità. L'implementazione di queste tecnologie aiuta le aziende a mantenere standard elevati di qualità e affidabilità nei loro prodotti, migliorando allo stesso tempo la produttività e riducendo i costi operativi.
Il sistema di ispezione automatica presenta diversi aspetti innovativi che migliorano significativamente il processo di rilevamento dei difetti nelle cavità, anche con diametri diversi. Uno degli aspetti principali è la capacità di rilevare difetti in luoghi angusti e di difficile illuminazione. Questo è possibile grazie all'uso di un endoscopio avanzato combinato con algoritmi di analisi delle immagini delle cavità interne, che consentono di analizzare in modo dettagliato le immagini dei condotti.
Il rilevamento dimensionale viene effettuato mediante un interferometro laser rotante, che crea una mappa tridimensionale della superficie interna della cavità, quindi una mappatura totale delle dimensioni interne, sostituendosi alla rilevazione puntuale effettuata con metodi di misura tradizionali. In combinazione con le altre tecniche di visione industriale, è possibile identificare con precisione eventuali trucioli o difetti di lavorazione che potrebbero compromettere il funzionamento del componente oleodinamico.
Un ulteriore elemento innovativo è l'utilizzo di un braccio robotico che compensa le limitazioni dell'endoscopio in termini di raggio di messa a fuoco e angolo di ispezione. Il robot permette la rotazione sull'asse, garantendo una copertura completa a 360 gradi della cavità. Nell’immagine possiamo notare come per la parte di movimentazione sia stato utilizzato un robot collaborativo. Sulla flangia del robot è stata montata una camera da 5 Megapixel con attacco C-mount e, tramite un opportuno adattatore, si è collegato l’endoscopio alla camera. L’adattatore utilizzato ha una messa a fuoco variabile da 18 a 35 mm ed è quello che viene utilizzato attualmente dagli operatori per effettuare il controllo manuale.
Questi aspetti innovativi consentono un'ispezione più accurata e affidabile, il margine di errore umano è ridotto, mentre aumenta l'efficienza del processo di controllo qualità.
Questa tecnologia è applicabile a controlli in linea che richiedano numerosi controlli di qualità su lavorazioni interne, come fori, filetti, passaggi di liquidi o aria. Gli endoscopi e panoramascopi permettono di generare foto che possono essere analizzate tramite algoritmi di visione industriale. Gli strumenti installati su un braccio robotico permettono verifiche veloci e precise, riducendo i tempi delle verifiche di qualità .
La misurazione tramite laser è ideale per condotti di forma o diametro irregolare, altrimenti difficili da misurare.
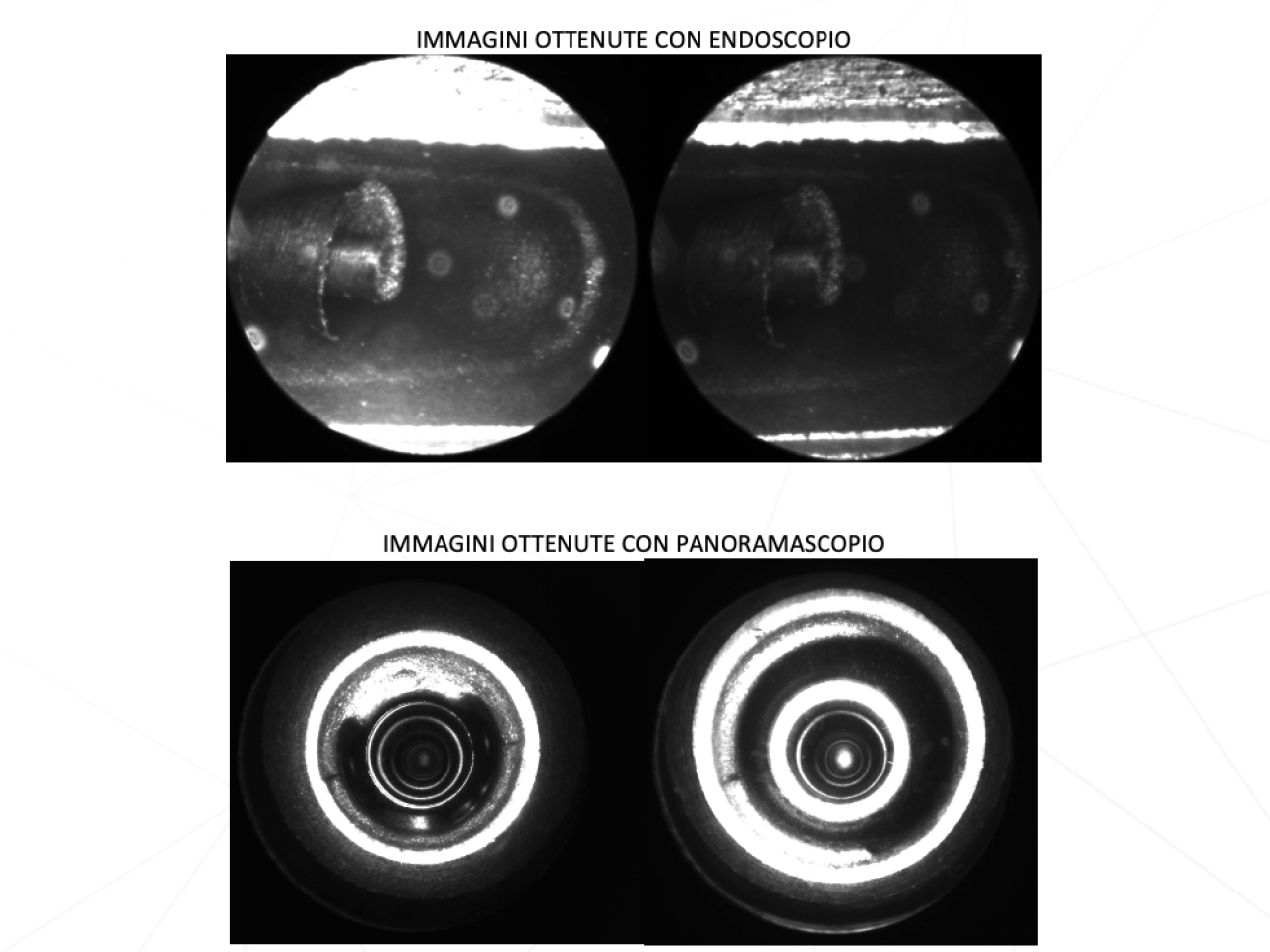
Identificazione di difetti interni alle sedi di distributori oleodinamici.
Lo scopo è individuare i trucioli o gli errori di lavorazione creatosi all’interno delle sedi durante il processo di fresatura e foratura, che portano al malfunzionamento del distributore stesso. Possono essere rilevate anche le imperfezioni del grezzo di fusione.
Attualmente, il controllo può essere effettuato solo manualmente da un operatore, il quale analizza le immagini che vengono fornite da un endoscopio inserito nella cavità da ispezionare.
Nella prima fase dello studio si è cercata la tecnologia più adatta per effettuare la misura in modo automatico e sono emerse due possibili soluzioni:
- Misura mediante interferometro laser rotante
- Misura mediante algoritmi automatici di analisi dell’immagine da endoscopio e da panoramoscopio
Risultati con l'Endoscopio:
Il procedimento di acquisizione delle immagini con l'endoscopio ha seguito questi passaggi: il robot ha posizionato l'endoscopio vicino alla gola da ispezionare e ha scattato diverse immagini ruotandolo sui 360 gradi. Sono state raccolte 151 immagini di gole conformi e 82 di gole con trucioli. Una rete neurale è stata addestrata su questo dataset per classificare le gole come conformi o non conformi. La matrice di confusione ha mostrato un'accuratezza del 95,2%, con 195 casi privi di difetti e 105 casi non conformi classificati correttamente.
Risultati con il Panoramascopio:
Con il panoramascopio, è possibile ottenere in una singola acquisizione un'immagine a 360 gradi della gola, eliminando la necessità di rotazione. Utilizzando il robot, sono state acquisite 156 immagini di cavità conformi e 32 di cavità non conformi. Una rete neurale è stata addestrata su questo dataset e validata, raggiungendo un'accuratezza globale dell'85,5%. La matrice di confusione ha mostrato che 158 immagini conformi su 188 e 43 immagini non conformi su 47 sono state classificate correttamente.
Analisi dei Tempi di Ciclo delle diverse soluzioni:
Il tempo ciclo dell'operatore manuale è di circa 6 minuti per distributore. Per l'interferometro laser, il ciclo automatico richiede circa 2 minuti per ispezionare un distributore. L'endoscopio classico richiede circa 4 minuti, mentre il panoramascopio è il più veloce, con un tempo stimato di circa 1 minuto e 30 secondi.
Tecnologia | Tempo di ciclo
- Controllo manuale da operatore: 6 minuti per distributore
- Controllo automatico con endoscopio: 4 minuti per distributore
- Controllo automatico con panoramascopio : 1 minuto e 30 secondi per distributore
- Controllo automatico con interferometro: 2 minuti per distributore
Indiotech
I test hanno dimostrato che il problema dei difetti nei distributori oleodinamici può essere affrontato con successo utilizzando sistemi di visione basati su reti neurali. Per ottenere un modello robusto, è necessario ampliare il dataset di immagini, in particolare dei pezzi difettosi. Inoltre, migliorare la qualità delle immagini utilizzando sorgenti luminose ottimali e filtri polarizzatori può aumentare la precisione della classificazione.
L'interferometro laser, che crea una nuvola di punti 3D della cavità, rappresenta un'alternativa valida poiché elimina problemi di riflessione e contrasto. Tuttavia, la disponibilità limitata di questi strumenti sul mercato italiano rende complessa la fase di test.
La ricerca è ancora in corso per testare nuove architetture di rete neurale e combinazioni di algoritmi tradizionali e deep learning per ottimizzare i risultati.
Si ricercano altri casi studio in cui applicare questa tecnologia
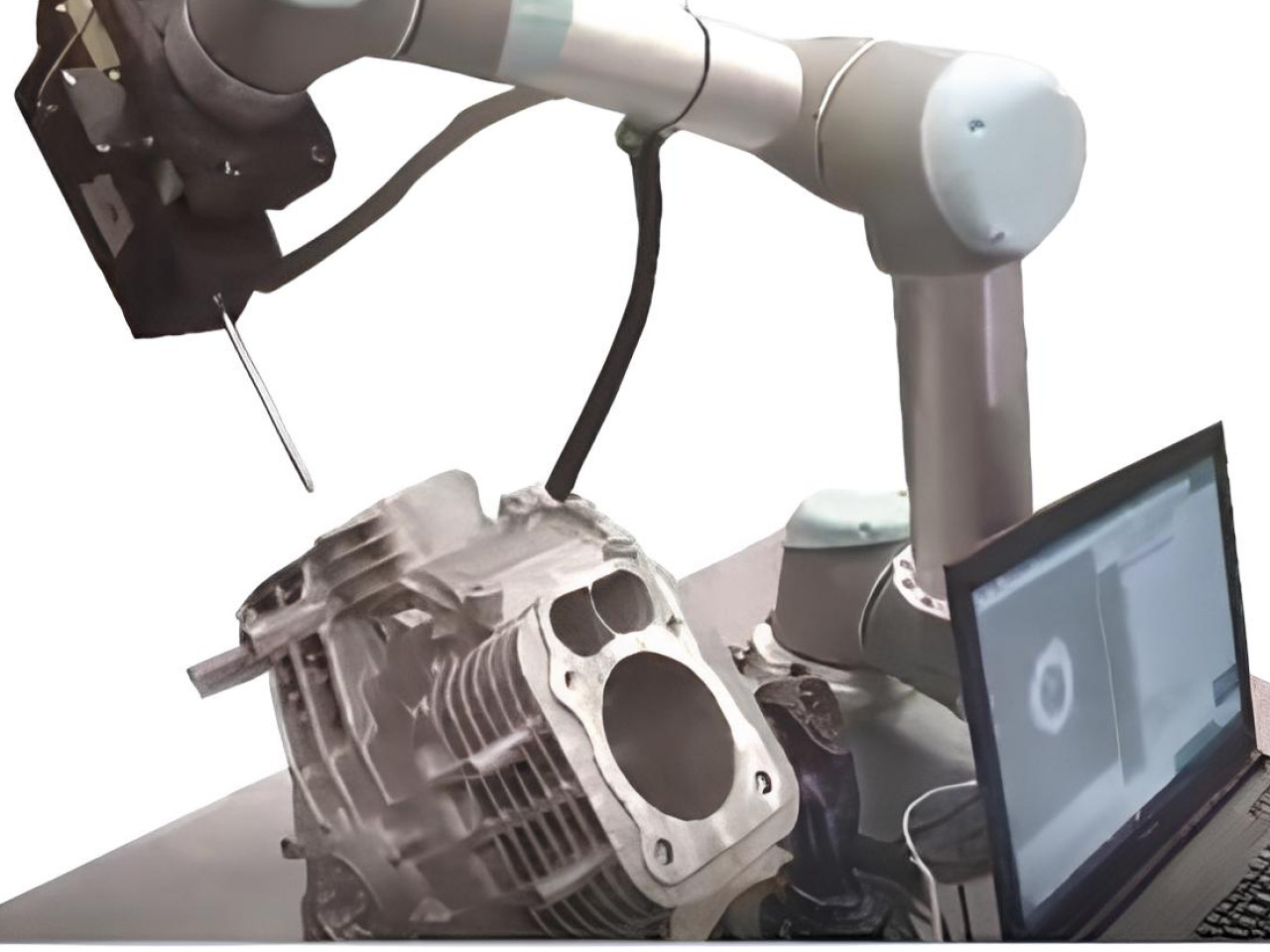