In ambito industriale è ormai possibile disporre di grandi quantità di dati in diverse applicazioni che vanno dal monitoraggio di processo al controllo adattativo. Tale ambiente “data rich” è favorito principalmente da due fattori: il continuo sviluppo di sensori ad alte prestazioni, a basso costo, a bassa intrusività e dotati di funzionalità “smart”, e il continuo miglioramento degli strumenti di calcolo e analisi del segnale in tempo reale. In tale contesto le tecniche di Multi-Sensor Data Fusion sono necessarie per raggiungere una caratterizzazione sintetica di processi e sistemi produttivi che sia più robusta, affidabile ed efficace rispetto alla normale pratica industriale.
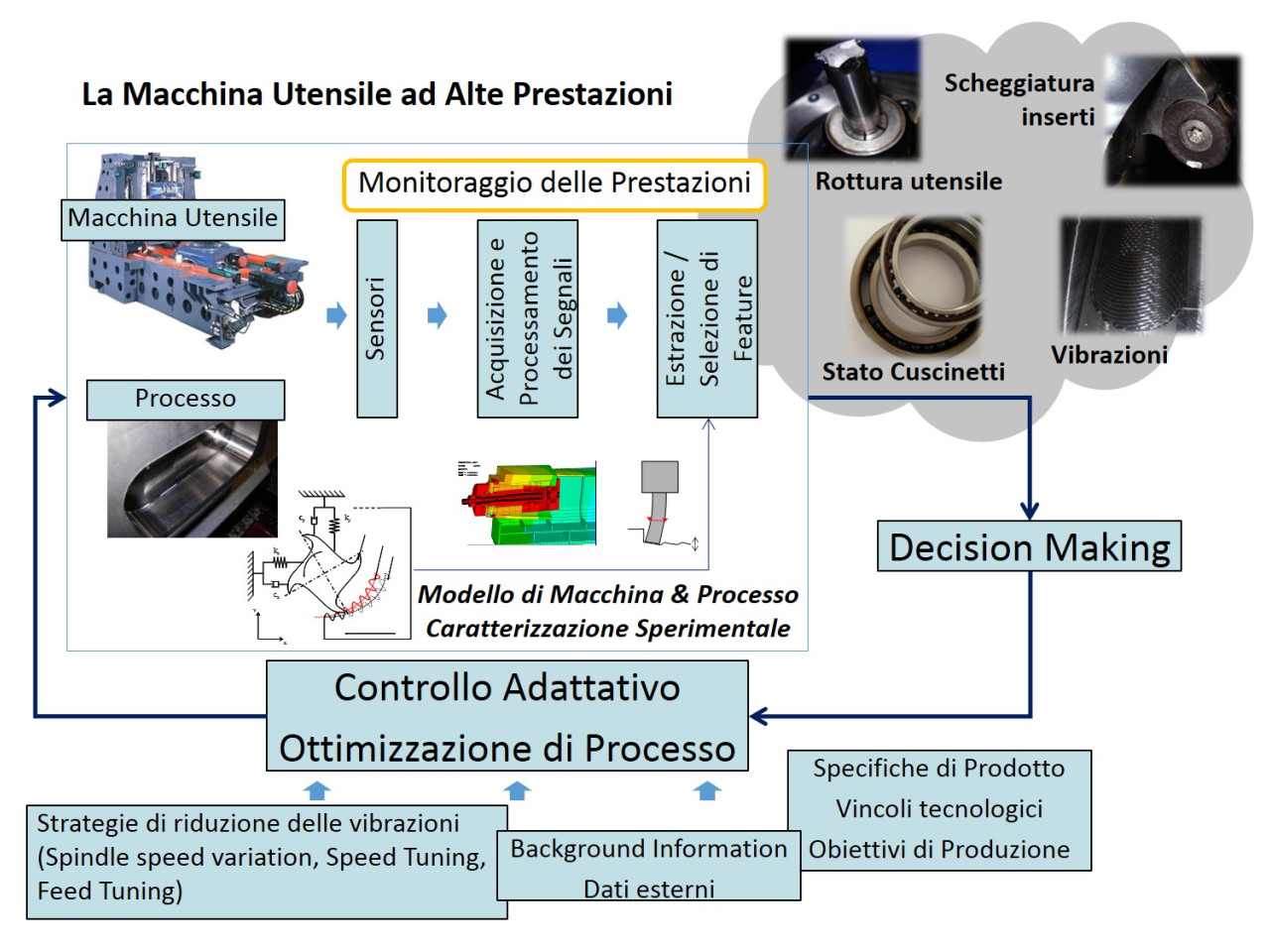
L'Area 2 - Precision Engineering - del Laboratorio MUSP studia e sviluppa soluzioni e strumenti per il monitoraggio della qualità dei processi tecnologici, nell'ambito di lavorazioni convenzionali (per asportazione di truciolo) e non-convenzionali (e.g. taglio a getto d'acqua). L'obiettivo consiste nell'incrementare le prestazioni del sistema tramite l'impiego di tecniche più robuste, affidabili ed efficaci di quelle tradizionalmente applicate in ambito industriale. Si studiano problemi legati al trattamento on-line di segnali provenienti da sorgenti multiple per il riconoscimento in tempo reale di anomalie e instabilità di processo. Gli strumenti sviluppati sono validati sul campo con il supporto di end-user, costruttori di macchine utensili e sviluppatori di sistemi accessori.
Nella normale pratica industriale viene fatto un uso molto limitato di sensori e segnali durante i processi di lavorazione. I principali benefici riguardano: a) la robustezza rispetto a disturbi e condizioni operative che variano nel tempo; b) una migliore caratterizzazione del processo grazie all'uso sinergico delle fonti di informazione disponibili; c) la corretta gestione dell'incertezza associata ai dati raccolti grazie all'impiego di tecniche statistiche; d) la possibilità di auto-apprendimento e di adattamento a parametri e condizioni che cambiano in continuazione.
Monitoraggio in-process della qualità dei processi per riconoscere anomalie e/o instabilità di processo. Alcuni esempi: riconoscimento di scheggiature e rotture utensile; segnalazione di vibrazioni e fenomeni di chatter; valutazione dell'evoluzione dell'usura utensile nel tempo; identificazione di danneggiamenti a componenti critici della macchina; etc. I principali settori applicativi includono le lavorazioni - convenzionali e non - per il taglio e la deformazione di materiali di qualsiasi natura.
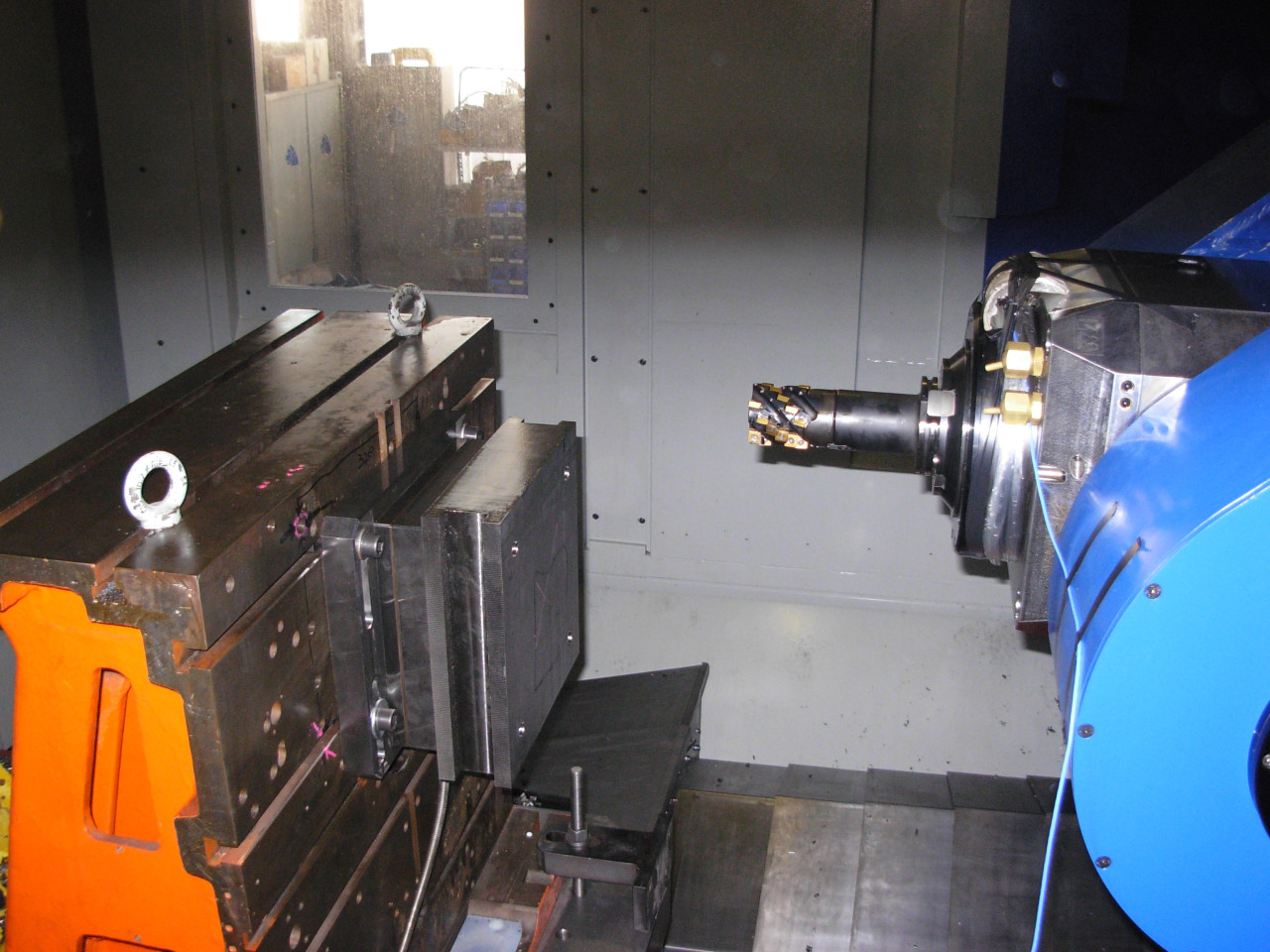
Monitoraggio e diagnostica di processi di taglio water-jet
Sviluppo di un sistema di monitoraggio e diagnostica dello stato di salute dei componenti più critici di una pompa ad altissima pressione per il taglio waterjet. Le estreme condizioni operative cui sono soggetti i componenti dell'intensificatore di pressione porta a frequenti guasti che risultano difficili da prevedere e praticamente impossibili da prevenire. Un sistema a bordo macchina in grado di tenere sotto continuo controllo l'integrità dei componenti e la stabilità del processo risulta quindi di grande interesse industriale per incrementare intelligenza e autonomia del sistema. La presenza di un guasto può essere segnalata tempestivamente, permettendo di prendere le opportune decisioni in termini di manutenzione e pianificazione della produzione. In caso di guasti che hanno un impatto sulla qualità del processo è anche possibile chiudere il loop di controllo attraverso un'azione correttiva, per esempio una modifica dei parametri di taglio o un fermo macchina, nei casi più gravi. Le informazioni diagnostiche possono essere rese disponibili in locale (per l'operatore a bordo macchina) o anche in remoto (per permettere di tenere sotto controllo un parco macchine distribuito sul territorio). Il sistema è stato testato sul campo, dimostrando la possibilità di identificare rapidamente diverse tipologie di guasto e di riconoscere la natura del guasto.
CMS Tecnocut Altag Srl
Il progetto ha visto il coinvolgimento sia di end-user che di costruttori di macchine. E' stato sviluppato un primo prototipo con funzionalità ICT per il trasferimento dei dati a postazioni remote. La rilevanza scientifica dei risultati ottenuti ha inoltre portato alla pubblicazioni di alcuni lavori in ambito internazionale.
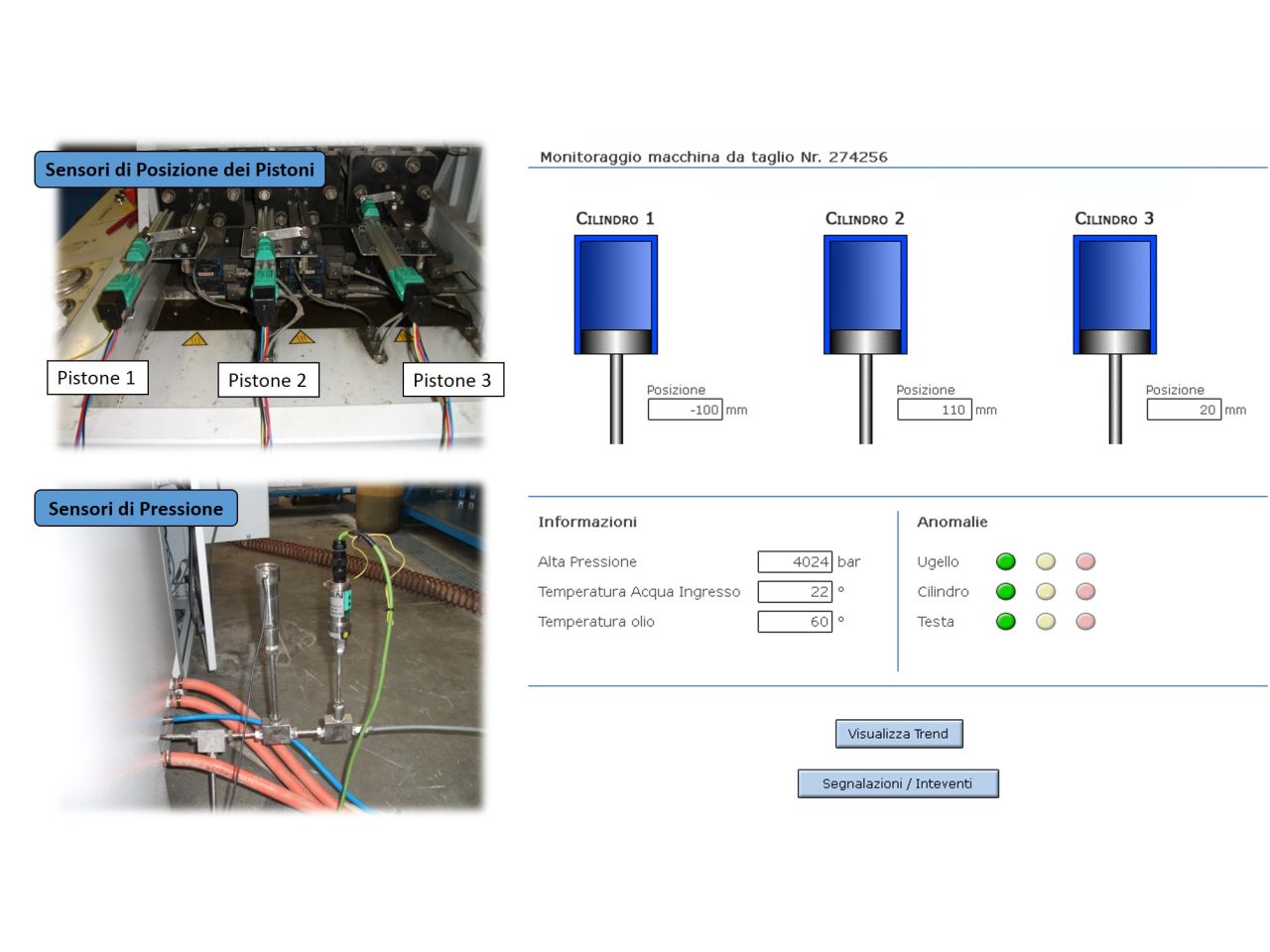