In the industrial realm it is now possible to have large amounts of data in various applications, from process monitoring to adaptive control. This “data rich” environment is mainly supported by two factors: the continuous development of high performance, low cost, low intrusiveness sensors, featuring “smart” functionalities, and the ongoing improvement of computation and real time signal analysis instruments. Within this framework, Multi-Sensor Data Fusion techniques are necessary to achieve a synthetic characterisation of productive processes and systems that is more robust, reliable and effective compared to the standard industrial practice.
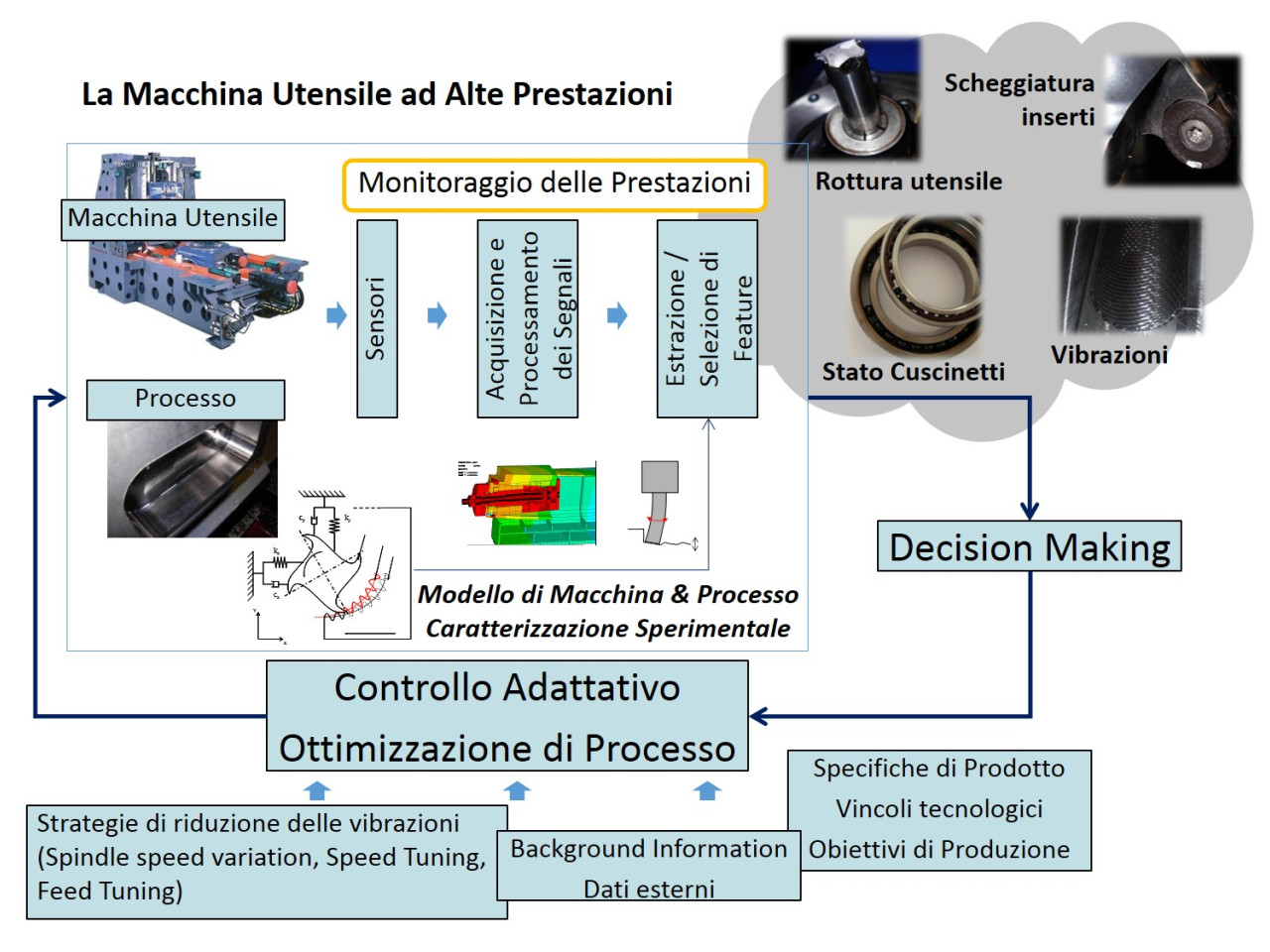
In standard industrial practice, a very limited use is made of sensors and signals during manufacturing processes, even when they are already available without using external instruments. Commercially available monitoring systems are based on very conservative logics which have often proved not very effective and not sturdy enough. Data fusion and statistic process monitoring techniques studied and developed at the MUSP Laboratory make it possible to overcome the main limits of conventional instruments. The main benefits concern: a) robustmess with respect to noise and operating conditions that vary over time; b) better process characterisation through the synergistic use of available information sources; c) the correct management of the uncertainty associated with data collected by using statistical techniques; d) the possibility of self-learning and adaptation to parameters and conditions that change continuously.
A possible application concerns in-process monitoring of process quality to recognise process anomalies and/or instabilities, in a more reactive way than classic quality control procedures. Some examples: recognition of tool chipping and breakages; signalling vibrations and chatter phenomena; assessment of the tool wear trend over time; identification of damage to critical machine components; etc. The immediate recognition of these anomalies makes it possible to implement adaptive control strategies, and in general to improve the intelligence and automation of the machine tool. Advanced monitoring instruments make it possible to reduce wastes and process costs/times, and to improve maintenance strategies. The main application sectors include machining - either conventional or not - for cutting and deformation of any kind of material.
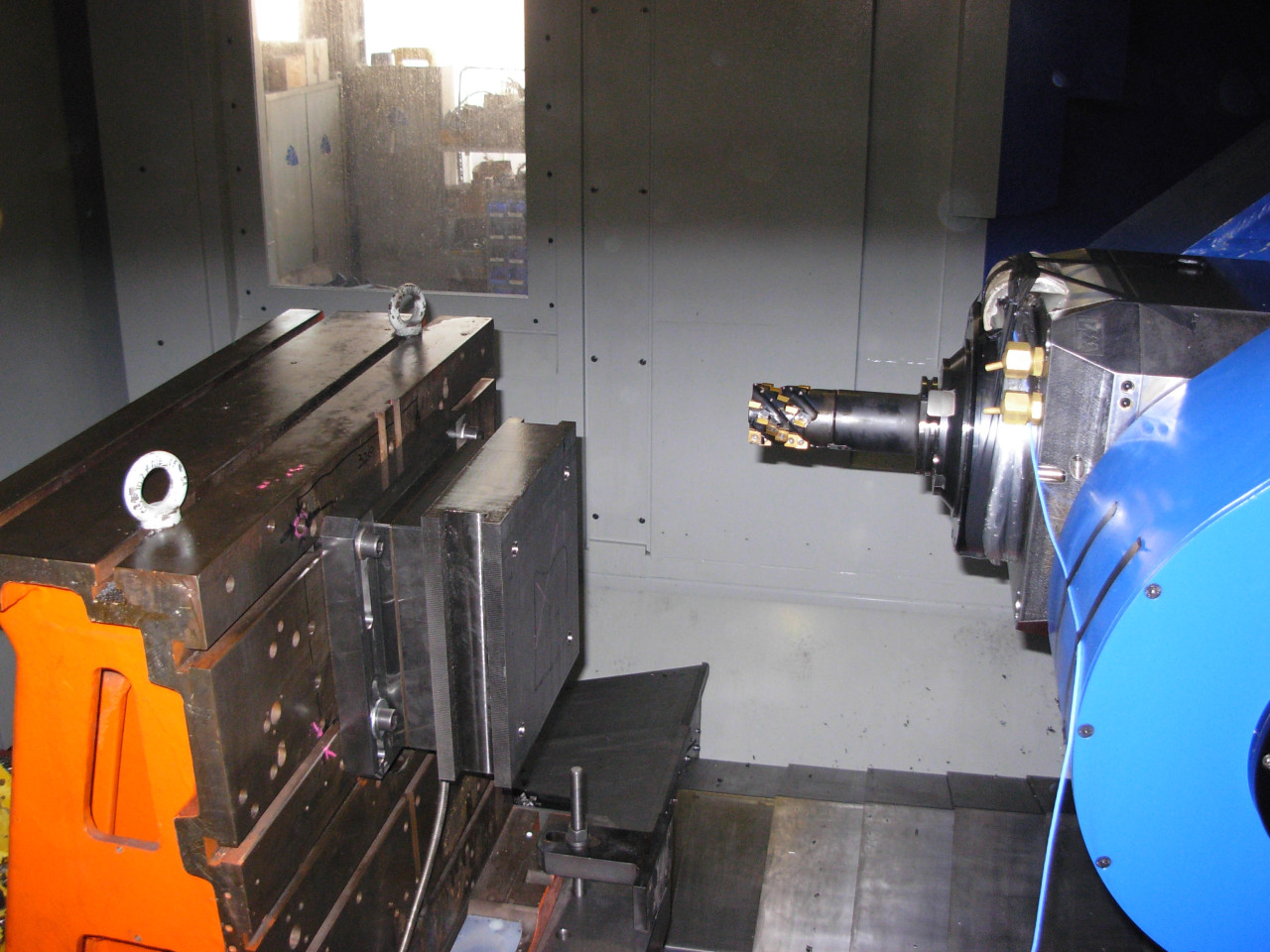
Monitoring and diagnostics of water-jet cut processes
The application concerned the development of a system for monitoring and diagnosing of the health condition of the most critical components of a very high pressure pump for waterjet cutting. The extreme operative conditions which the pressure intensifier components are subject to lead to frequent failures, which turn out to be difficult to foresee and practically impossible to prevent. A system on the machine able to keep the integrity of components and process stability under continuous control is therefore of great industrial interest to increase system intelligence and autonomy. The presence of a fault may be promptly signalled, making it possible to make the suitable decisions in terms of maintenance and production planning. In the event of faults that have an impact on process quality it is also possible to close the control loop through corrective action, e.g., a change of cutting parameters or, in the most severe cases, a process termination. The diagnostic information may be made available locally (for the operator on the machine) or even remotely (to control a machine fleet distributed over the territory). The system is based on a real-time analysis architecture of water pressure and plunger position signals, using low cost sensors which can be easily integrated in the machine. A first prototype was developed with ICT functionality to transfer data to remote stations. The system was tested in the field, proving the ability to quickly identify various types of failure and to recognise the nature of the failure (for instance by signalling whether it involves pressure intensifier components or cutting head components).
CMS Tecnocut Altag MUSP
The results of the project were presented at international conferences, seminars targeting firms in the sector and national and international scientific journals. The skills and tools developed during the activities have allowed us to offer new solutions for monitoring and diagnostics both to machine tool manufacturers and end-users. In this framework new collaboration initiatives are envisaged with companies in the region.
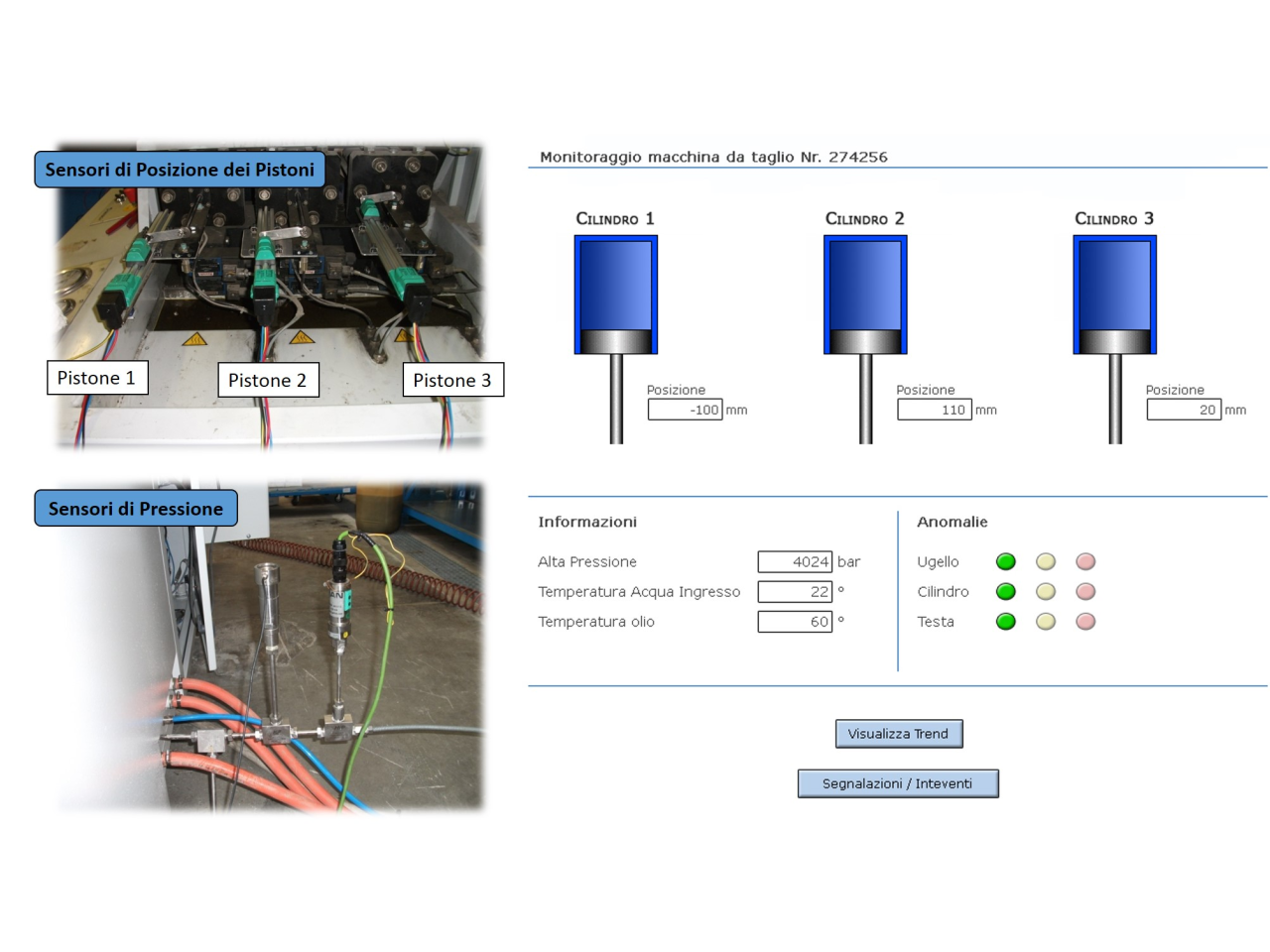