L'evoluzione del settore della meccanica strumentale è legata alla richiesta degli stakeholder di una sempre maggiore produttività che necessità di un continuo miglioramento delle tecnologie. La ricerca nel settore delle macchine utensili di una crescente sostenibilità, combinata alla riduzione dell'impatto ambientale, dell'incremento delle prestazioni e dello sviluppo di capacità di auto-adattamento al mutare delle condizioni di lavoro sono le principali linee guida del progetto Hi-SCORE. Tali obiettivi sono stati ricercati attraverso tre linee di azione: 1. innovazione nella fase di progettazione della macchina mediante approcci di prototipazione virtuale e impiego di materiali innovativi; 2. innovazione nella fase di utilizzo della macchina mediante approcci di sensorizzazione e monitoraggio delle condizioni di lavoro così come dei consumi energetici; 3. innovazione nel processo di taglio mediante impiego di azoto liquido come fluido lubrorefrigerante.
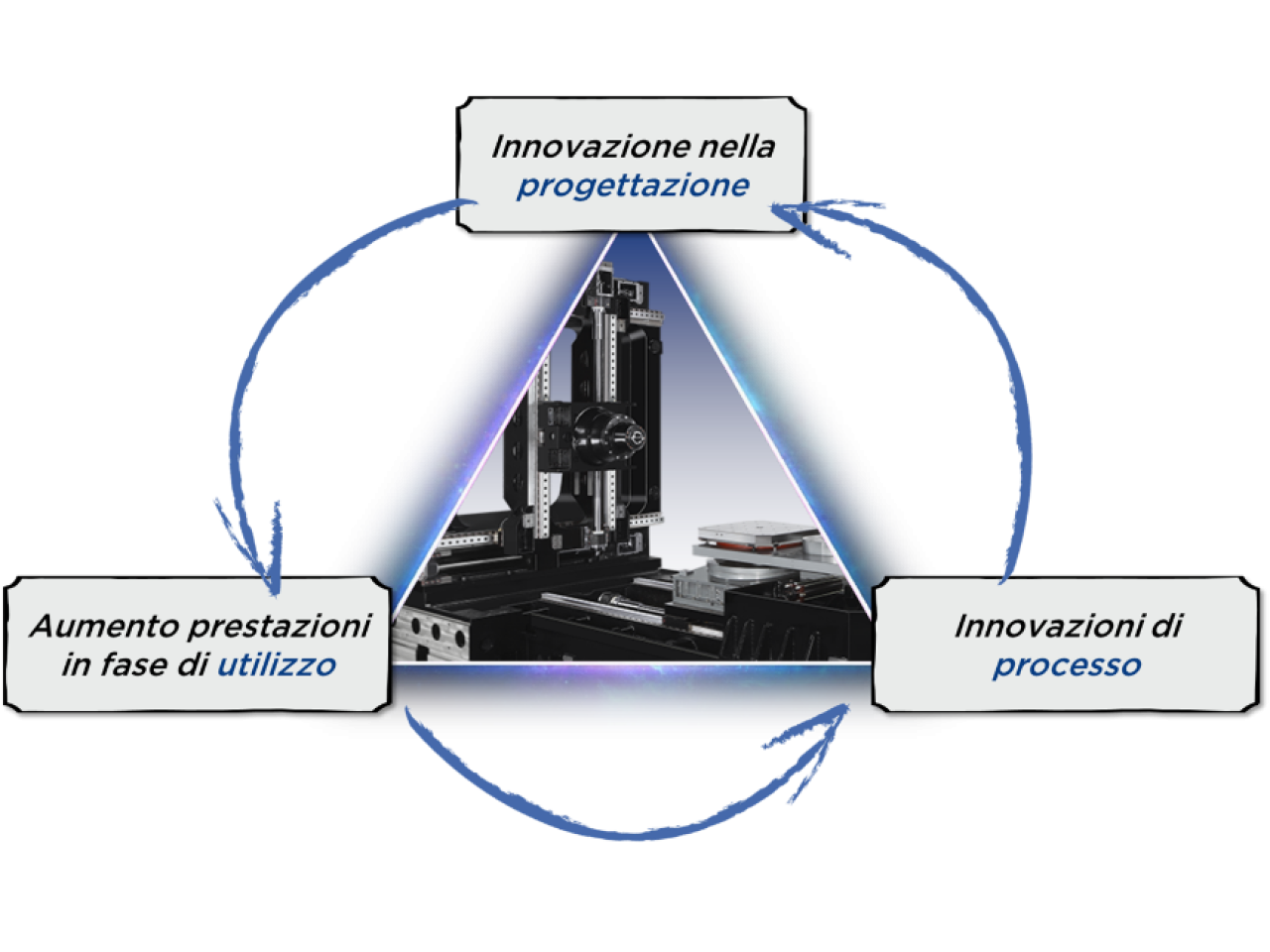
Il cuore del progetto Hi-SCORE ha permesso di sviluppare una piattaforma hardware/software flessibile rivolta al monitoraggio dei processi industriali ed accessibile a realtà aziendali di medio-piccola dimensione. Tale piattaforma può essere equipaggiata con una serie di strumenti di monitoraggio standard (e.g. consumi energetici), ma anche di algoritmi e indicatori di processo personalizzati per il cliente. L’estensione verso la rete permette infine di interfacciare la piattaforma con operatori e funzioni aziendali di diverso livello e competenza, garantendo un puntuale e immediato accesso alle informazioni estratte dal campo. Nel dettaglio, la soluzione è composta da tre principali componenti: i. una architettura hardware flessibile che comprende una rete sensoriale di volta in volta ritagliata sulla singola casistica e l’elaboratore embedded comprensiva dei moduli di acquisizione selezionati in base alla sensoristica; ii. algoritmi per la gestione dei segnali acquisiti e l’estrazione di informazioni di alto livello, si tratta ad esempio dell’identificazione del chatter, della stima delle forze di taglio e della qualità superficiale del pezzo lavorato, dell’identificazione dell’ingaggio utensile, ecc.; iii. infrastruttura di rete che permette alle informazioni acquisite di essere trasmesse e pubblicate in remoto.
Esistono soluzioni commerciali di monitoraggio rivolto alla CBM (Condition Based Maintenance) e alla gestione/supervisione di un sistema produttivo; però sono confinate ad alcune grandi aziende e/o ad approcci tipicamente semplificati e molto rigidi (e.g. soluzioni general purpose ma semplificate oppure di dettaglio ma molto rigide). La soluzione MUSP adotta un approccio in contrasto, è di fatto una vera customizzazione basata su know-how che implementa soluzioni innovative di monitoraggio energetico, identificazione e controllo del chatter e stima della qualità della lavorazione.
I principali ambiti applicativi riguardano certamente i costruttori delle macchine utensili. Interfacciarsi con essi permette infatti di garantire una soluzione dal massimo livello di integrazione con la macchina e dalle maggiori performance operative grazie anche alla connessione con sensori come encoder rotativi interni. Il sistema è inoltre perfettamente implementabile per il retrofitting di macchine già installate e in fase di utilizzo. In questo caso si andrà a sensorizzare la macchina soltanto esternamente non garantendo il dialogo con il CNC e, quindi, il controllo in loop chiuso.
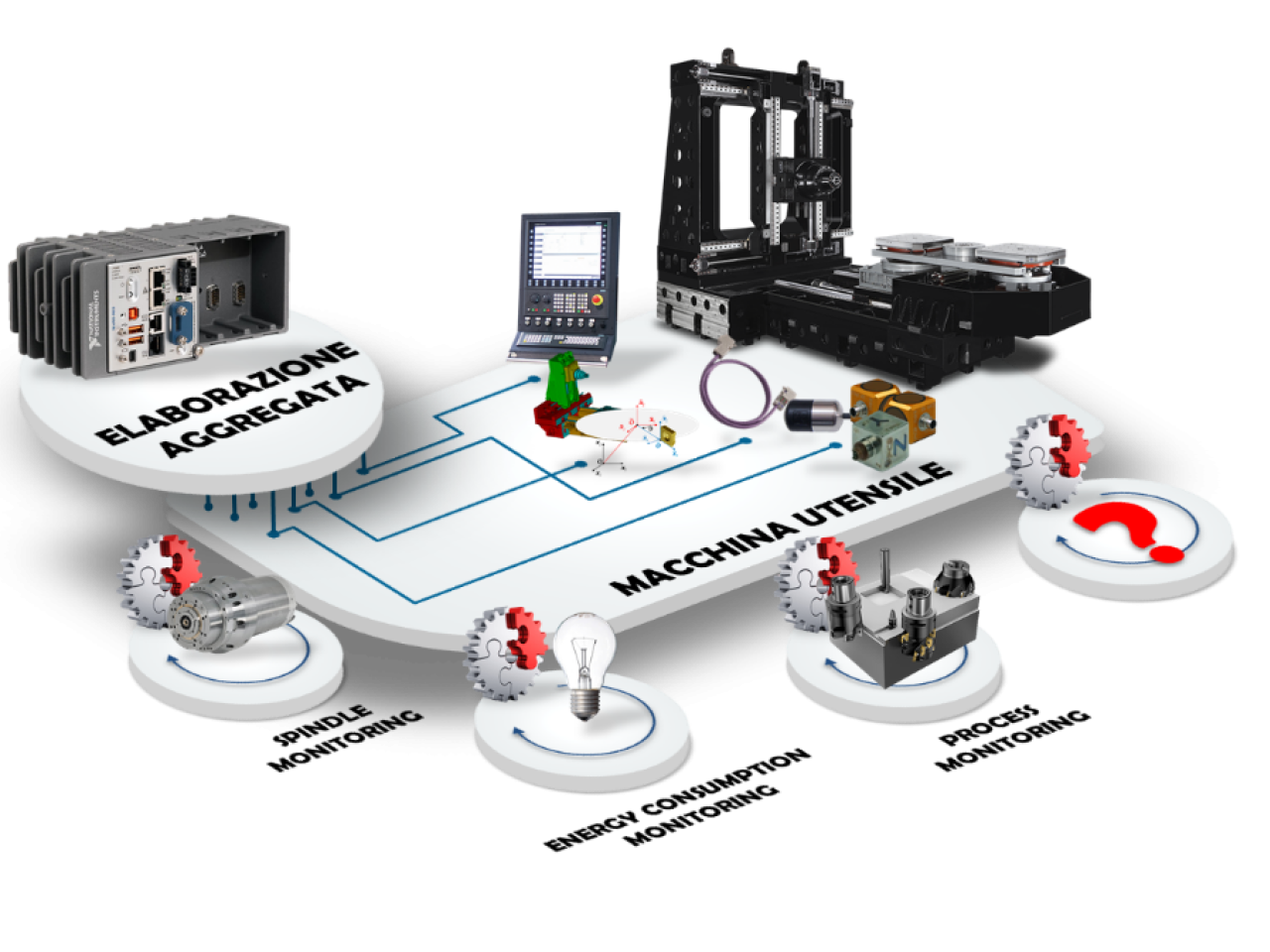
Impiego della piattaforma Hi-Score per il monitoraggio e il controllo delle vibrazioni instabili in un processo di fresatura
La piattaforma è stata impiegata in una particolare casistica applicativa con l’obiettivo di monitorare le condizioni di taglio in termini di stabilità del processo e di operare un controllo in anello chiuso per tentare di ridurre o sopprimere completamente le eventuali vibrazioni instabili. L’azienda coinvolta nel caso applicativo ha quindi individuato una macchina su cui testare la piattaforma, MUSP si è occupato della sensorizzazione della macchina, dell’interfacciamento della sensoristica (sia aggiuntiva che già presente) con la piattaforma e della definizione dei test di taglio con cui essa è stata messa alla prova. In particolare, la macchina è stata sensorizzata con accelerometro piezoelettrico triassiale su naso mandrino e il sistema è stato interfacciato con il controllo numerico della macchina; i test di taglio definiti hanno riguardato sia lavorazioni stabili che instabili eseguite con diversi parametri di taglio e con diverse tipologie di utensile. I risultati delle prove hanno mostrato una grande efficacia della piattaforma nel riconoscere l’instabilità di processo e nell’individuarne le caratteristiche spettrali, così come nel selezionare differenti parametri di taglio per stabilizzare adattativamente la lavorazione.
ISTEC-CNR Mandelli Sistemi Amada Capellini Gruppo CMS JOBS PAMA MCM Cohaerentia
Attualmente, una delle aziende partner di progetto ha presentato una domanda di brevetto per quanto riguarda la parte relativa al controllo di processo (smorzamento delle vibrazioni). Riguardo la piattaforma di monitoraggio, con tutti i partner coinvolti nel progetto sta per cominciare un vero e proprio roll out della tecnologia su differenti tipologie di macchine e per diversi produttori.
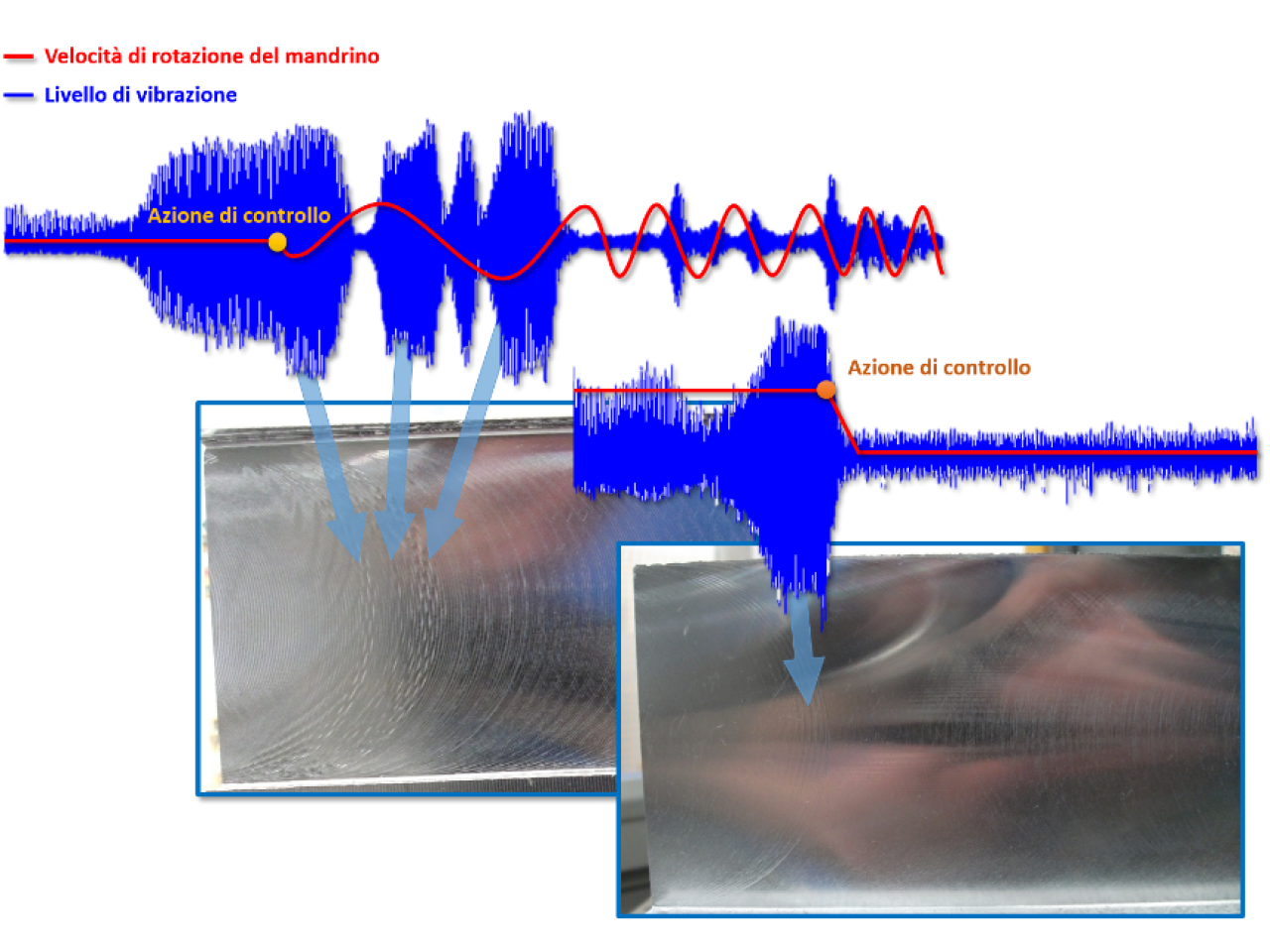