The evolution of machine tool industry is linked to the stakeholders’ need to constantly increase productivity, which means constantly improving the applied technologies. The research for increased sustainability, combined with the reduction of environmental impact, improved performances (e.g. productivity, accuracy, machine surface quality) and the development of the ability to self-adapt to new working conditions, are the main guidelines of Hi-SCORE project that break down into three main themes: a. Innovation in the design stage – integrated design techniques (mechatronics), prediction of the quality of machined products, use of damping materials. b. Innovative strategies for increasing performance during use – reduction of consumption and performance improvement through process monitoring and control. c. Improving the performance of chip removal methods through innovative technologies – such as the use of cryogenic cooling lubricants, ceramic materials and coatings in tools
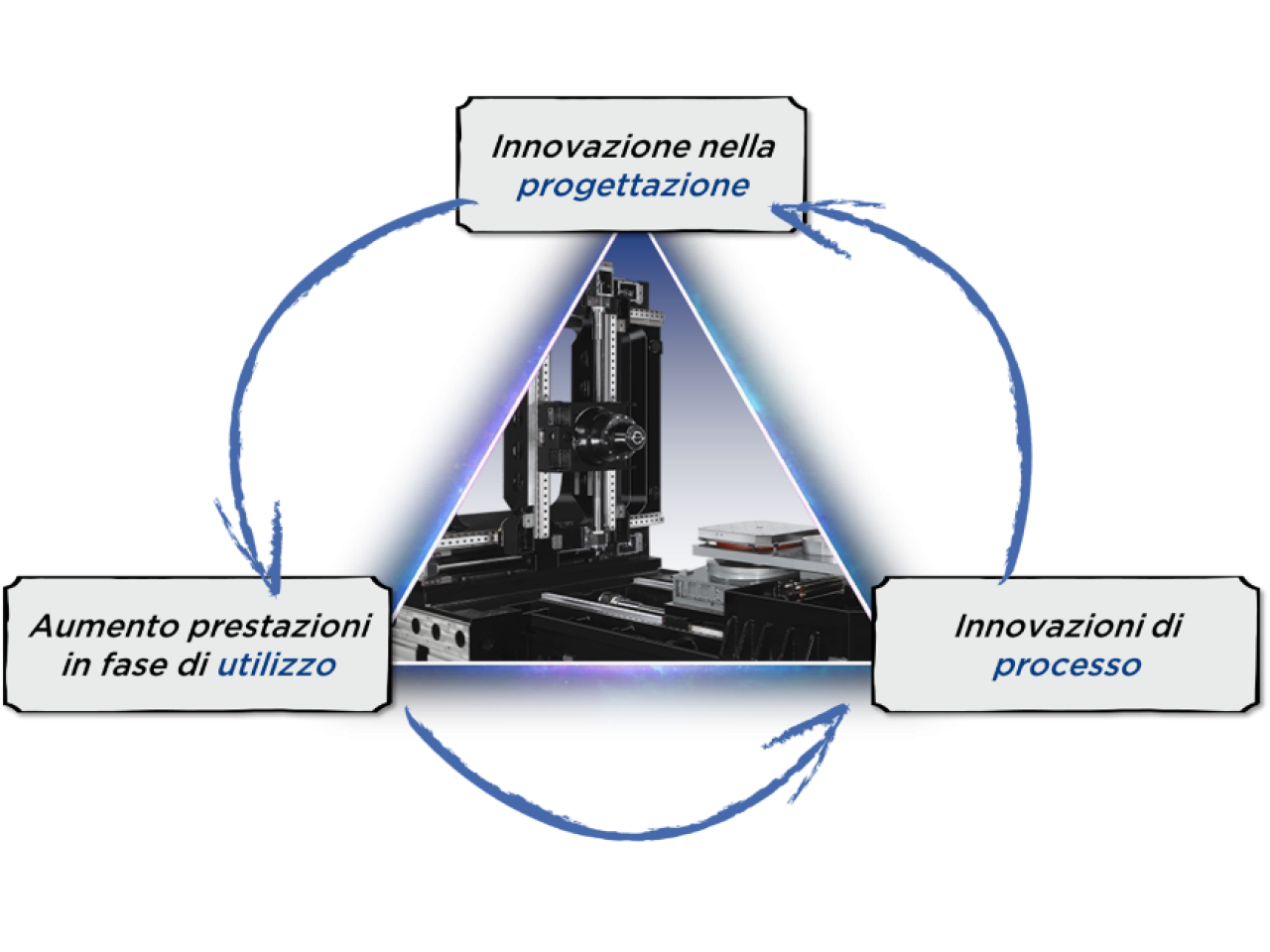
There are commercial monitoring solutions aimed at CBM (condition based maintenance) and the management / supervision of a production system; however they are confined to some large companies and / or to typically simplified and very rigid approaches (e.g. general purpose but simplified solutions or detailed but very rigid). MUSP solution adopts a different approach, it is in fact a true customization based on know-how that implements innovative solutions for energy monitoring, identification and control of chatter vibration and estimation of processing quality.
The main application areas concern machine tool manufacturers. In fact, interfacing with their NC allows to guarantee a solution with the highest level of integration with the machine and with greater performance thanks also to the connection with sensors such as internal rotary encoders. The system is also perfectly implementable for the retrofitting of machines already installed and in use. In this case the machine will be sensorized only externally, not guaranteeing the dialogue with the NC and, therefore, the closed loop control.
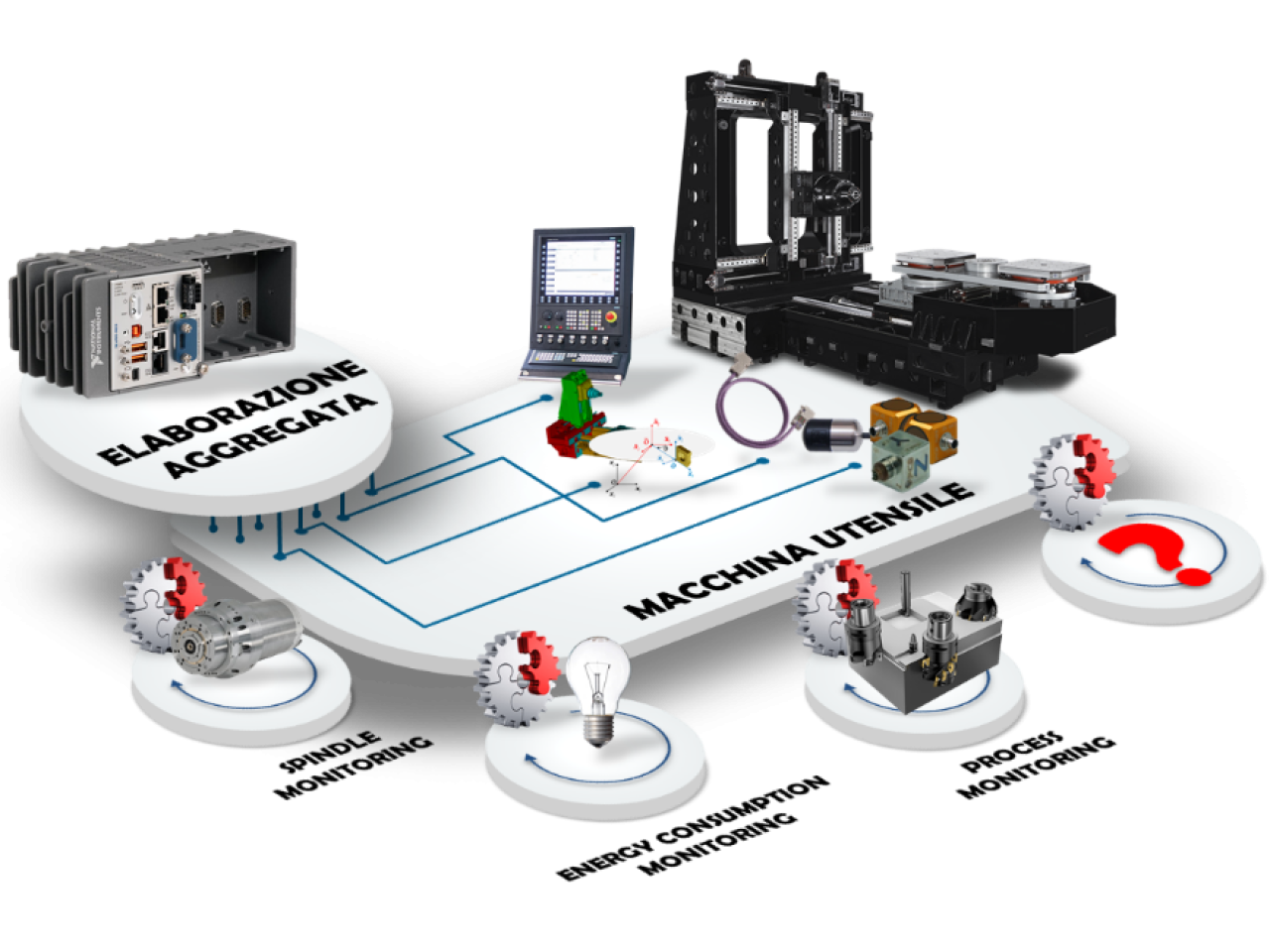
Use of the Hi-Score platform for monitoring and controlling unstable vibrations in a milling process
The platform was used in a particular case study with the aim of monitoring the cutting conditions in terms of process stability and operating a closed loop control to try to reduce or completely suppress any unstable vibrations. The company involved in the use case therefore identified a machine on which to test the platform, MUSP took care of the sensorization of the machine, the interfacing of the sensors (both additional and already present) with the platform and the definition of the cutting tests with which it has been tested. In particular, the machine was sensorized with a triaxial piezoelectric accelerometer on the spindle nose and the system was interfaced with the numerical control of the machine; the defined cutting tests concerned both stable and unstable machining performed with different cutting parameters and with different types of tools. The results of the tests showed that the platform recognizes process instability and identifies its spectral characteristics efficiently, as well as adapts cutting parameters to stabilize the process.
ISTEC-CNR Mandelli Sistemi Amada Capellini Gruppo CMS JOBS PAMA MCM Cohaerentia
Currently, one of the companies partners of the project has filed a patent application for the part relating to process control (vibration damping). Regarding the monitoring platform, with all the partners involved in the project, a real roll out of the technology is about to begin on different types of machines and for different manufacturers.
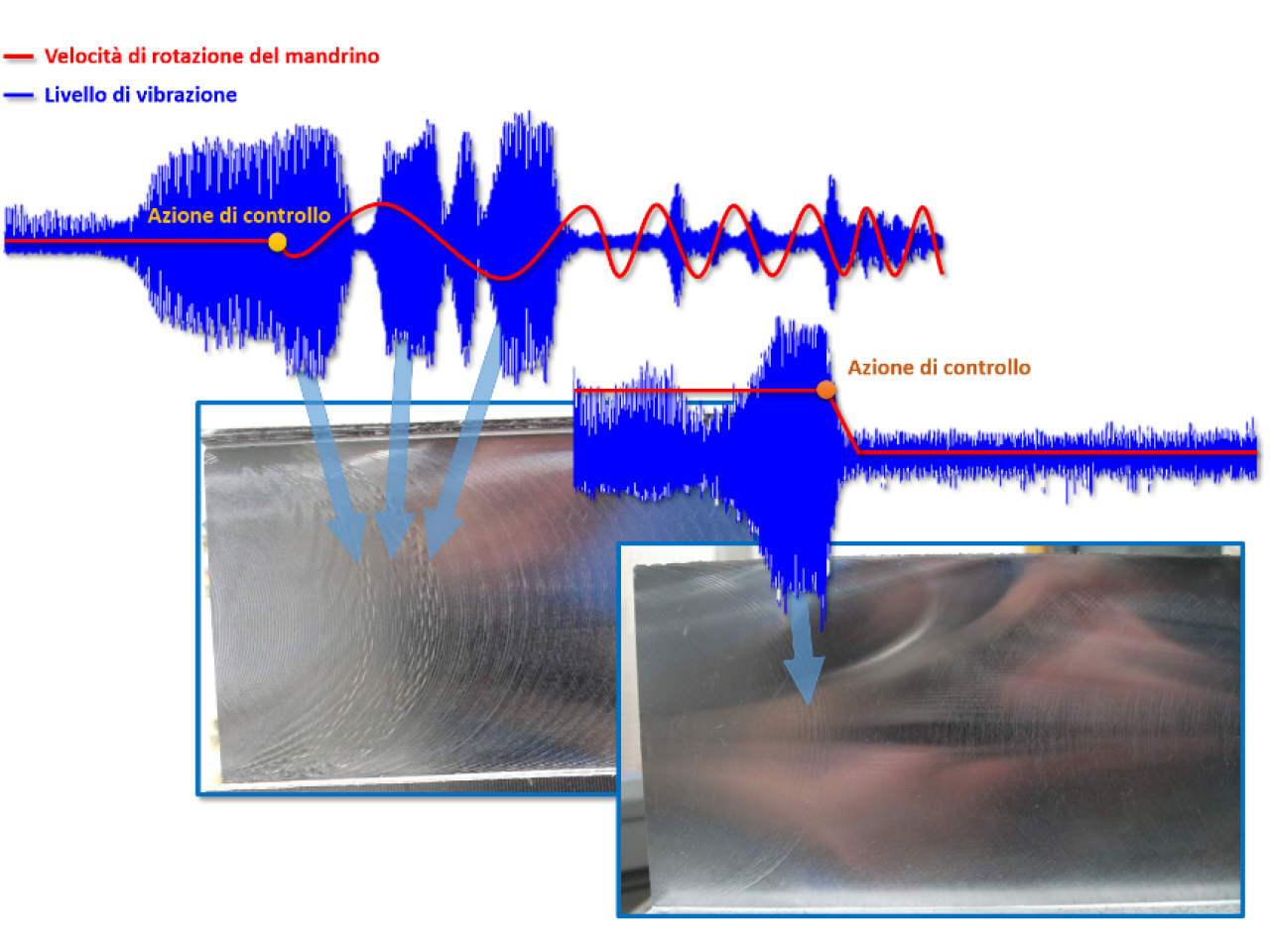