Nell’ambito dei compositi fibrorinforzati per l'alleggerimento, combinare riciclabilità e resistenza al fuoco vengono generalmente considerati obiettivi inconciliabili. ENEA-TEMAF si è dato come target nel progetto regionale a coordinamento FireMat (www.firemat.it) di sviluppare soluzioni riciclabili e resistenti al fuoco basate su materiali costituiti da FML (Fiber Metal Laminate), i relativi processi e di valutare i parametri necessari per migliorarne la sostenibilità ambientale. I compositi a matrice polimerica sono quelli che ottimizzano la resistenza meccanica specifica e quindi le potenzialità in termini di alleggerimento, ma tutti i polimeri sono, seppur in varia misura, combustibili. Il progetto ha cercato ovviare al problema, sviluppando semilavorati (prepreg) della stessa tipologia di quelli attualmente utilizzati, ma a partire da nuove materie prime riciclabili e associandoli a lamine metalliche sottili e funzionali.
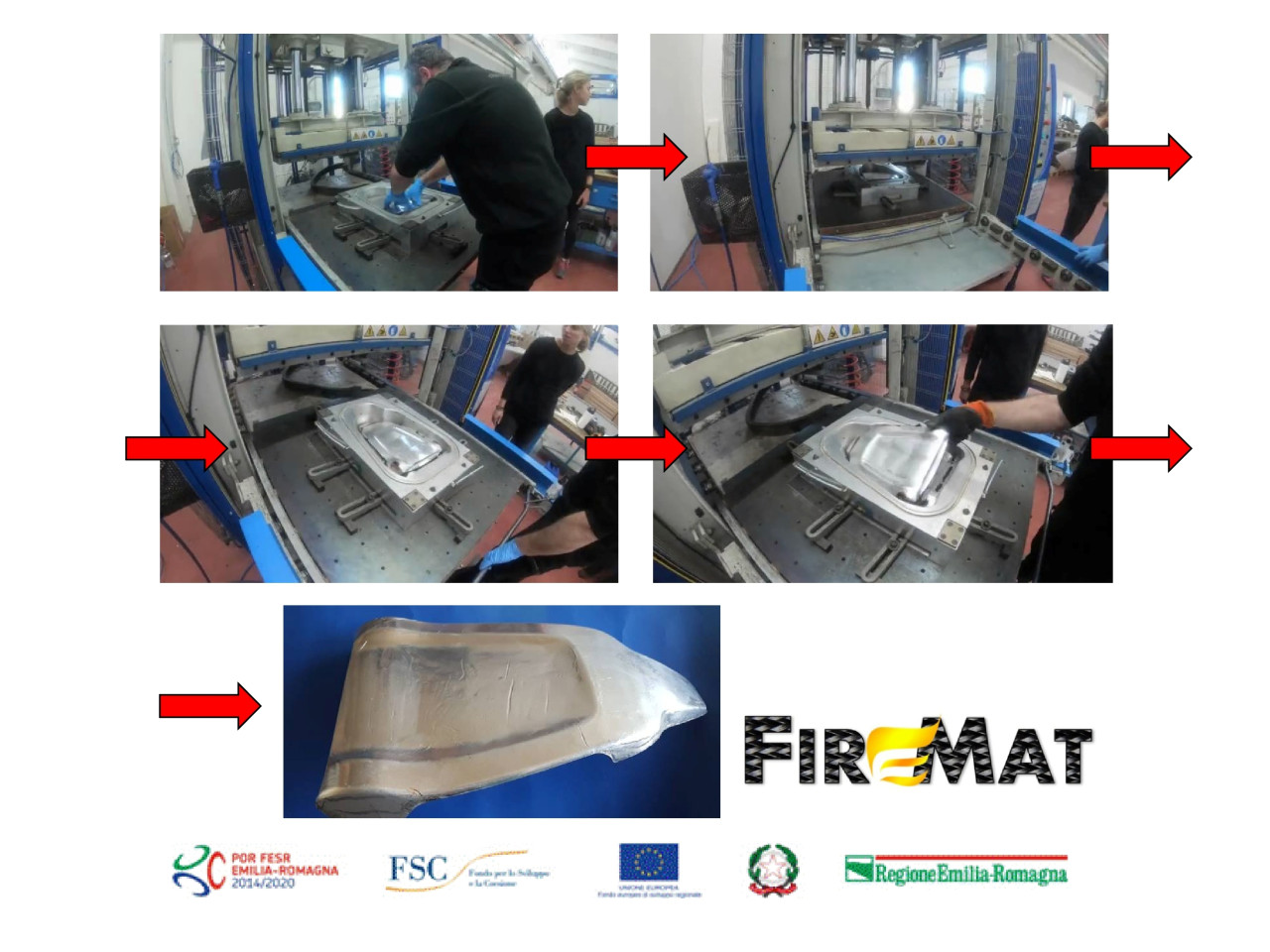
Il prodotto da fornire alle imprese del settore composito è il semilavorato costituito dall'accoppiamento di prepreg e alluminio, che si è dimostrato laminabile in forme complesse sia attraverso un processo in autoclave, sia (per aumentare la produttività) in pressatura a caldo (con un tempo di processo sul componente intorno ai 10 minuti, ma con costi iniziali per la realizzazione dello stampo industrialmente rilevanti). In Regione ER sono presenti molte imprese, potenziali utilizzatori del semilavorato, per produrre componenti in Laminato Composito Metallo (FML) anche come possibile opzione alternativa ai compositi high-end attualmente in produzione, aumentando la gamma di prodotto, senza richiedere investimenti in impianti.
ENEA-TEMAF, nonostante abbia realizzato, presso i propri laboratori, una linea pilota con elevata flessibilità per lo sviluppo del semilavorato, non sarebbe però in grado di gestire una produzione in scala, che si pensa quindi trasferire a un produttore industriale di prepreg. In parallelo ENEA continuerà a sviluppare i materiali e i processi, sfruttando le nuove materie prime, sia come resine che come rinforzi fibrosi, riciclabili e biobased, che si stanno affacciando sul mercato, al fine di aumentare la sostenibilità e l'applicabilità alla produzione di massa, per esempio puntando a componenti per aumentare il livello di sicurezza nella mobilità elettrica, con problematiche di fuoco sia nelle versioni alimentate a batteria che ad idrogeno.
Gli FML sviluppati hanno una reazione al fuoco migliori rispetto ai materiali compositi attualmente disponibili, e sono facili da produrre in forme complesse. Il processo produttivo parte da prepreg altamente innovativi, ma compatibili con gli attuali metodi industriali di produzione. Il prepreg viene associato a lamine metalliche sottili, che svolgono una funzione di barriera all'ossigeno, migliorando la classe di resistenza al fuoco, senza però compromettere la riciclabilità o le proprietà meccaniche. La sostenibilità della soluzione è garantita da: (1) utilizzo di resine bio-based; (2) utilizzo di fibre con una energia immagazzinata (embodied energy) fra un decimo e un quinto di quella delle fibre di carbonio; (3) utilizzo di lamiere di alluminio da materie prime seconde, possibile in quanto il loro utilizzo non è strutturale ma funzionale (antifuoco). Inoltre nel progetto si sono indagati i processi di riciclo cradle-to-cradle (ovvero con chiusura del ciclo), verificando la possibilità di separare l'alluminio dalle fibre, e riutilizzare entrambi per la funzione originaria, partendo da sfridi o componenti a fine vita.
Gli ambiti applicativi sono tutti quelli che necessitano di materiali strutturali leggeri, resistenti, contemporaneamente, al fuoco, agli urti e alla fatica, in particolare, richiesti in edilizia e nel settore dei trasporti (individuali o collettivi): la caratteristica della riciclabilità li rende materiali ideali per box batteria antifuoco, porte e pareti tagliafuoco, nautica e energie rinnovabili. Le caratteristiche innovative permettono lo sviluppo di applicazioni e produzioni di massa di componenti anche in forma complessa
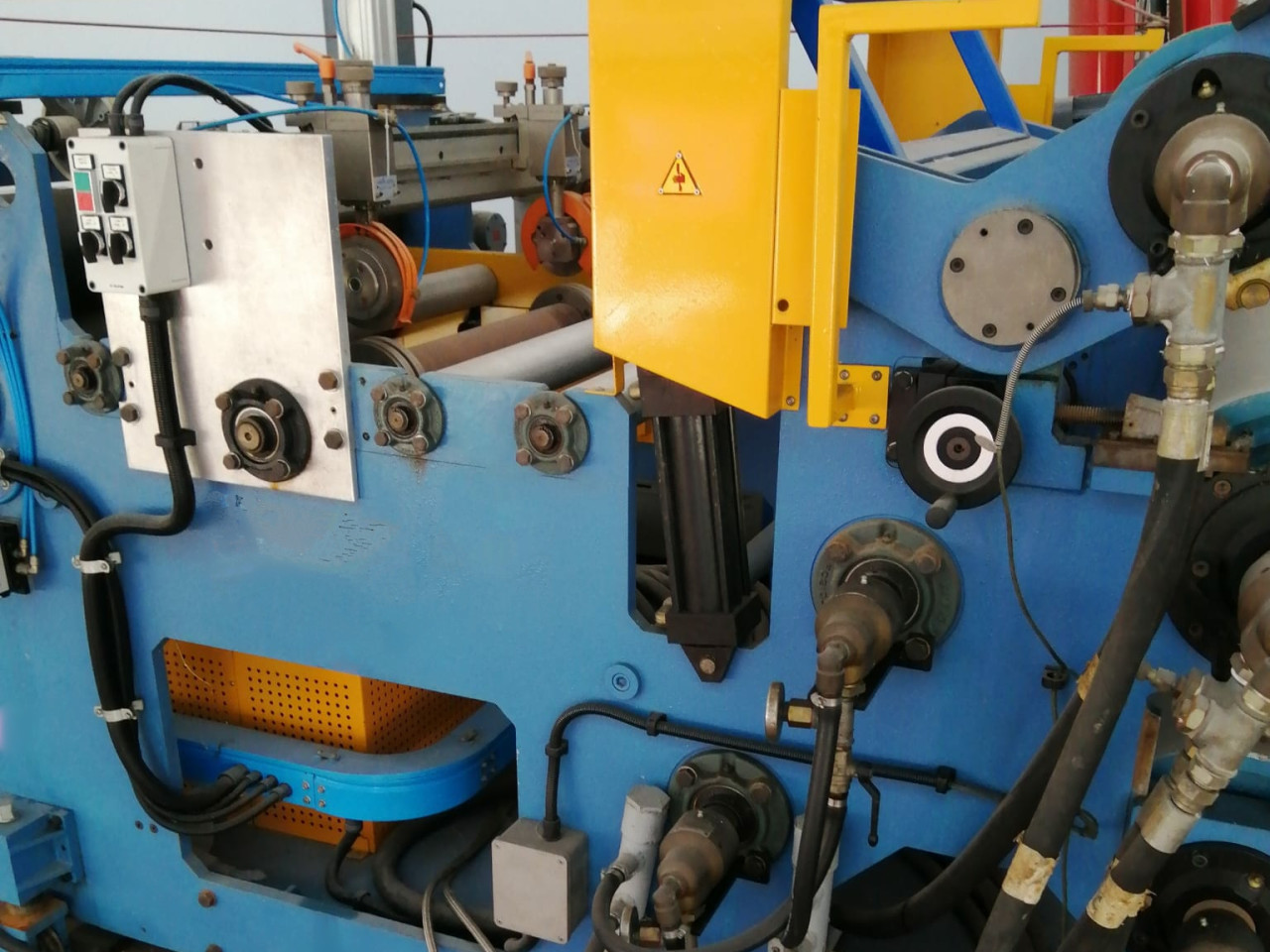
Cofano per vano turbina per applicazioni aeronautiche, elemento esemplificatvo di quelli cui la normativa richiede elevati requisiti antifuoco, a sicurezza del veicolo e dei suoi occupanti, e per i quali è al contempo necessario garantire una elevata resistenza specifica (per massimizzare l'alleggerimento e quindi l'autonomia). Altre categorie di componenti per le quali gli FML riciclabili antifuoco risultano una soluzione promettettente sono nel settore della mobilità elettrica
I materiali, sono stati ottimizzati in ENEA-TEMAF relativamente a sequenza e dimensionamento degli strati nella laminazione e processo produttivo, testando sia la pressatura a caldo che la cura in autoclave. Nell'ottimizzazione si è fatto riferimento alla resistenza a trazione e alla delaminazione, elementi richiesti dalla modellazione a Elementi Finiti (a carico di Consorzio MUSP, partner del progetto FireMat) per dimensionare lo spessore dell'elemento in funzione dell'applicazione al cofano turbina dell'elicottero Zefhir (Curti Costruzioni Meccaniche) sulla base degli input relativi alle sollecitazioni massime, prevedibili in volo. La modellazione FEM ha evidenziato che è necessaria una configurazione a sandwich, ovvero includere un honeycomb interno al fine aumentare la resistenza a flessione, senza appesantire significativamente la struttura, configurazione che è prima stata testata in laboratorio, producendo un pannello con la stessa laminazione e sottoponendolo a flessione. Infine CertiMaC, partner incaricato alle validazioni nel progetto FireMat, ha verificato la resistenza al fuoco, mediante prove al conocalorimetro su pannelli 10 x 10 cm. Infine il cofano è stato realizzato, laminando e curando in autoclave un componente identico a quello in composito finora considerato, non antifuoco. Infine il componente realizzato è stato montato sull'elicottero Zefhir stesso.
ENEA-TEMAF (coordinatore)
ISTEC-CNR
CertiMaC
Consorzio MUSP
Romagna Tech
BUCCI Composites srl
Aliva srl
Curti Costruzioni Meccaniche SpA
Tampieri Energie srl
ENEA-TEMAF ha presentato una domanda di brevetto sul materiale (data 04/02/2021, domanda n° 102021000002504, titolo: Semilavorato per la Produzione di un Multimateriale Strutturale Resistente al Fuoco, per Termoformatura a Caldo). Come progetto FireMat, a giugno 2021 si è inoltre partecipato al congresso internazionale online ICEAF VI, nella sessione dedicata alla transizione green.
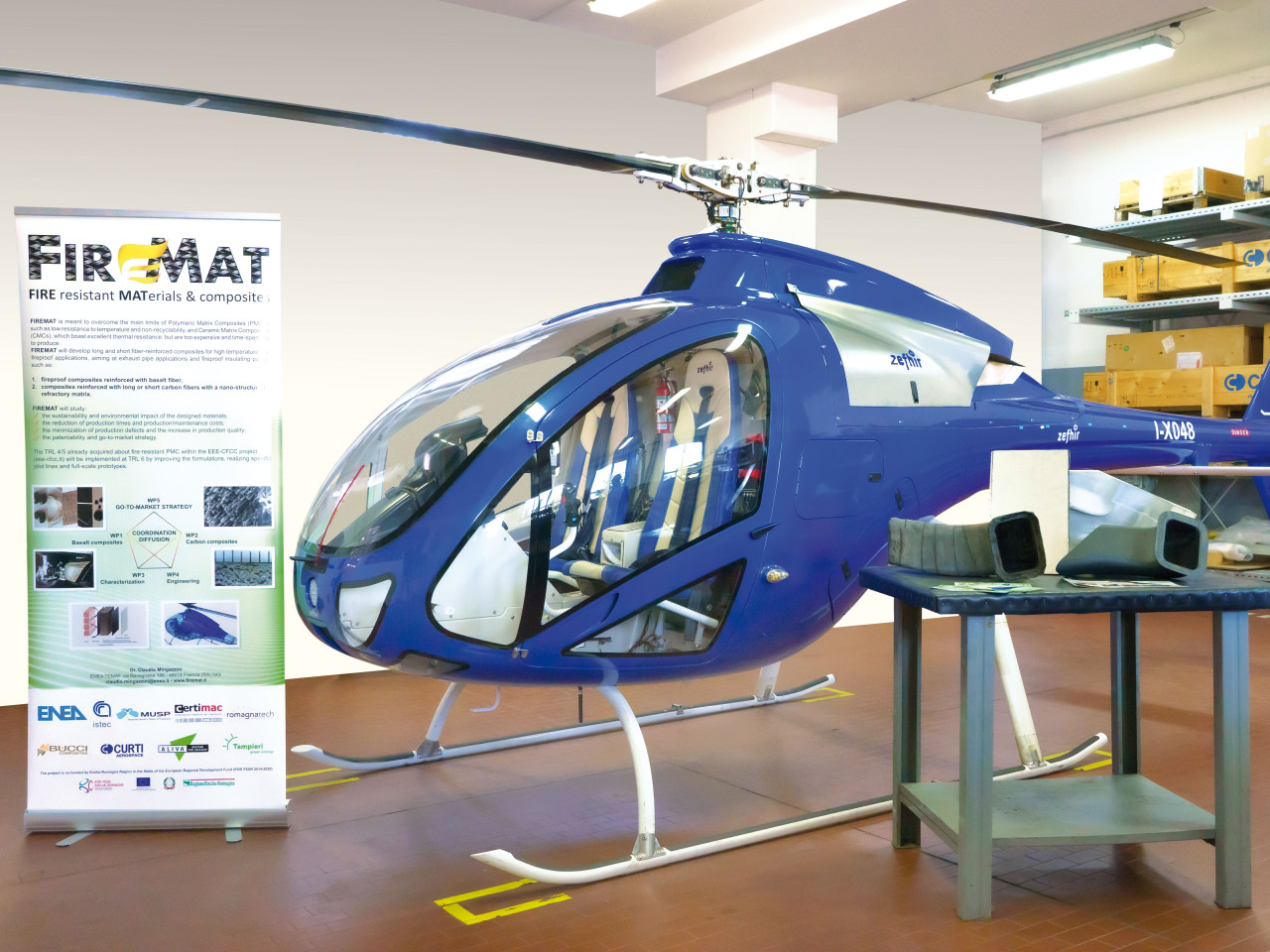