Per confezionamento in asettico s’intende il confezionamento in un contenitore sterile, in condizioni asettiche, di un prodotto precedentemente sterilizzato o pastorizzato.
Gli impianti di confezionamento asettico sono costituiti da una sezione di sterilizzazione/pastorizzazione e di raffreddamento del prodotto, da una di sterilizzazione del contenitore e da una camera di riempimento e di tappatura.
I punti critici di questa tecnologia sono rappresentati dalla sanitizzazione del materiale di confezionamento e dal mantenimento delle condizioni di asetticità nella camera di riempimento durante tutte le fasi del processo. Pertanto, un impianto di confezionamento asettico richiede, sia in fase di progettazione sia in fase di installazione, la validazione del processo adottato.
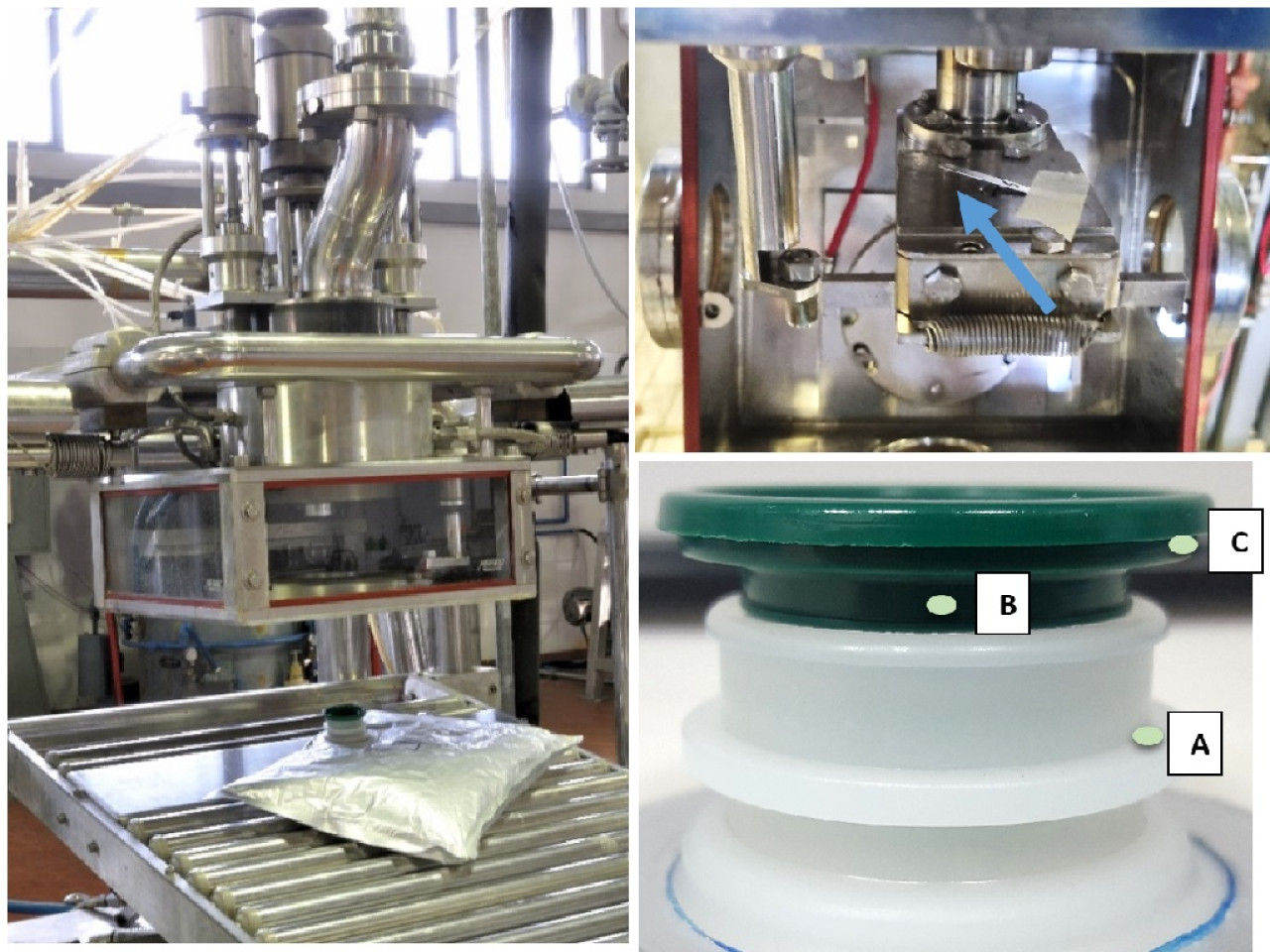
La validazione degli impianti asettici è la dimostrazione scientifica dell’efficacia del processo di sanitizzazione della camera di riempimento e dei contenitori utilizzati per il confezionamento di prodotti.
Viene effettuata mediante l’impiego di microrganismi target, scelti in funzione della tipologia di agente sanitizzante impiegato, che abbiano dimostrato una elevata resistenza allo stesso.
Per validare un impianto vengono utilizzati Indicatori Biologici (IB), composti dal microrganismo target e da un carrier su cui esso è depositato.
Gli IB sono costituiti da un materiale simile a quello da testare, per cui i più comuni sono quelli in acciaio inox o alluminio, sebbene si possano utilizzare anche IB in teflon, PET, HDPE, etc.
Gli IB vengono posizionati in punti specifici all’interno dell’impianto o del packaging e sottoposti al processo da validare: l’efficacia viene valutata in termini di riduzioni logaritmiche decimali del microrganismo impiegato.
Il numero di riduzioni logaritmiche viene, quindi, confrontato con i valori presenti in alcune delle linee guida internazionali, in quanto ad oggi non esiste alcuna normativa europea o extraeuropea da seguire.
Il processo di bio-validazione non solo consente di valutare l’effetto sterilizzante dei più comuni e conosciuti mezzi fisici (es. radiazione UV-C, radiazioni ionizzanti) e chimici (es. perossido di idrogeno, acido peracetico) attualmente in commercio, ma anche l’efficacia di tecnologie emergenti quali gli apparati a luce pulsata, a luce UVC-LED o ad infrarosso.
Molto interessante è risultata pure la possibilità di testare nuove tecnologie di inattivazione chimica mediante ozono in soluzione acquosa o in forma gassosa.
Il processo di bio-validazione risulta fondamentale per aziende produttrici di impianti ultra-clean o asettici, imprese alimentari per verificare l’efficacia del trattamento di sanificazione degli impianti e del packaging.
Il metodo è applicabile a differenti tipologie di packaging e impianti di confezionamento, così classificati:
- classe IV (ultra-clean), destinati al confezionamento di alimenti stabili a temperatura ambiente con pH ≤ 4,6 e alimenti refrigerati con pH> 4,6
- classe V (asettici), utilizzati per alimenti stabili a temperatura ambiente con pH>4,6
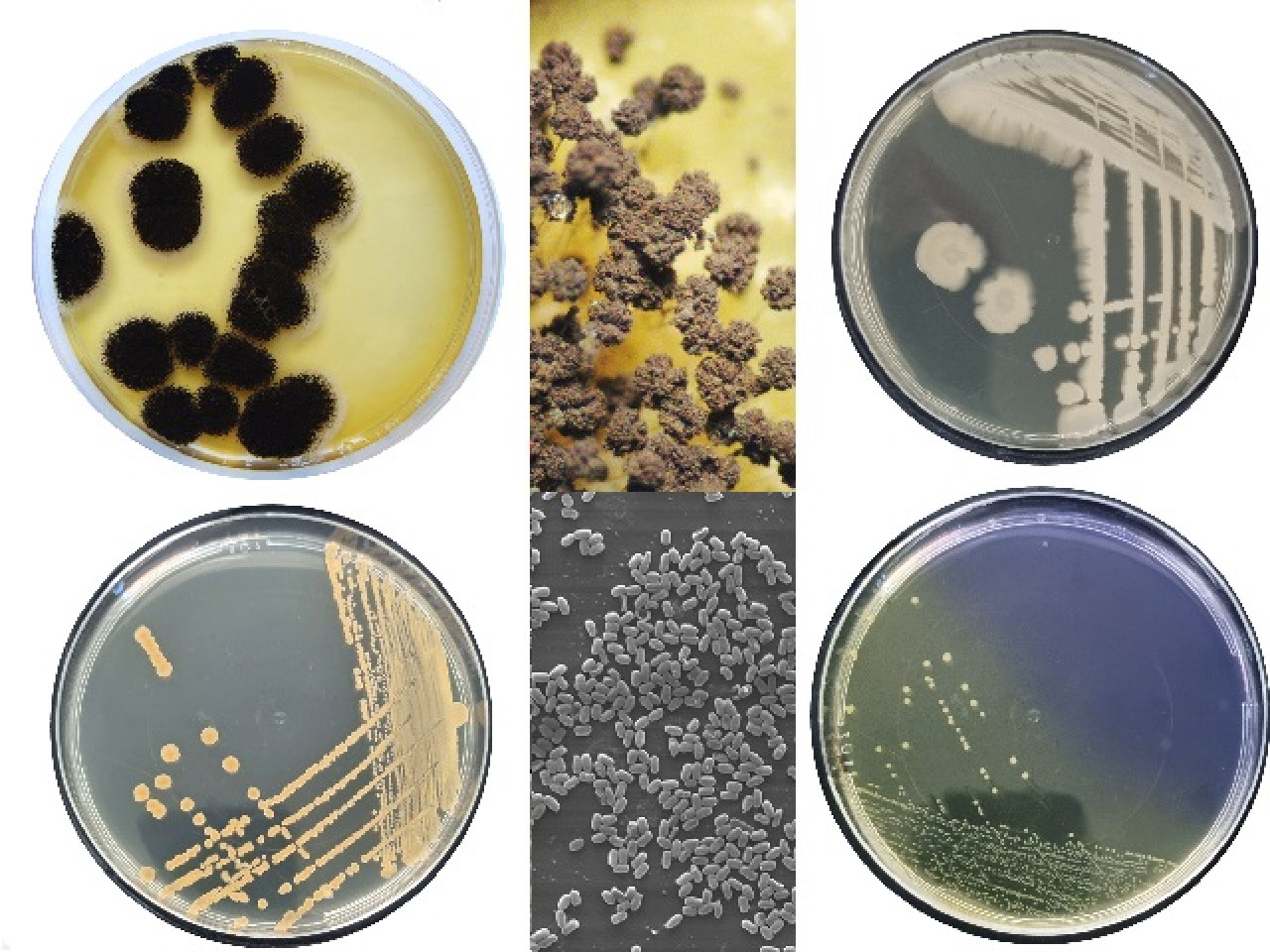
Valutazione dell’efficacia del trattamento di sterilizzazione mediante una soluzione di “ECOLAB P3 Oxonia active “perossido di idrogeno e acido peracetico al 3% su: - bocchelli di sacchi per il confezionamento asettico, precedentemente radio-gammati e inoculati nei “punti sfavoriti”, individuati tramite prove di mappatura preliminari;
Testata di riempimento asettica, anch’essa valutata mediante IB collocati nei “punti sfavoriti” del trattamento di sanitizzazione.
Le prove sono state condotte utilizzando una sospensione sporale a concentrazione nota del batterio Bacillus atrophaeus ATCC 9372, inoculato sia sui device non trattati (controlli positivi) sia sui device da sottoporre al processo di sterilizzazione.
Per quanto riguarda i bocchelli, le prove sono state effettuate prendendo in considerazione una numerosità campionaria minima pari a 5 unità per i campioni non trattati (controlli positivi) e pari a 20 unità per i campioni trattati.
Per quanto riguarda la testate di riempimento asettica, le prove sono state effettuate prendendo in considerazione una numerosità campionaria minima pari a 5 unità per i campioni non trattati (controlli positivi) e pari a 10 unità per i campioni trattati.
Per entrambi i device, le prove sono state effettuate in triplo, in modo da fornire una significatività statistica alle prove eseguite.
Al termine delle prove, tutti i campioni sono stati recuperati ed analizzati microbiologicamente.
Il numero di riduzioni logaritmiche impartite dal processo è stato ottenuto per differenza tra il logaritmo della concentrazione iniziale di spore (N0) e il logaritmo della concentrazione delle spore sopravvissute al processo succitato (Nf).
La bio-validazione ha avuto esito positivo poiché il numero di riduzioni logaritmiche ottenute è risultato in linea con gli obiettivi prefissati ( ≥ 5 Log).
Il lavoro è stato svolto in collaborazione con aziende Italiane del settore conserviero e aziende costruttrici di impianti di confezionamento asettico.
Nell'ambito della produzione di alimenti fluidi a bassa e/o elevata acidità, il metodo può essere utilizzato per validare impianti di confezionamento asettico e differenti tipologie di packaging .
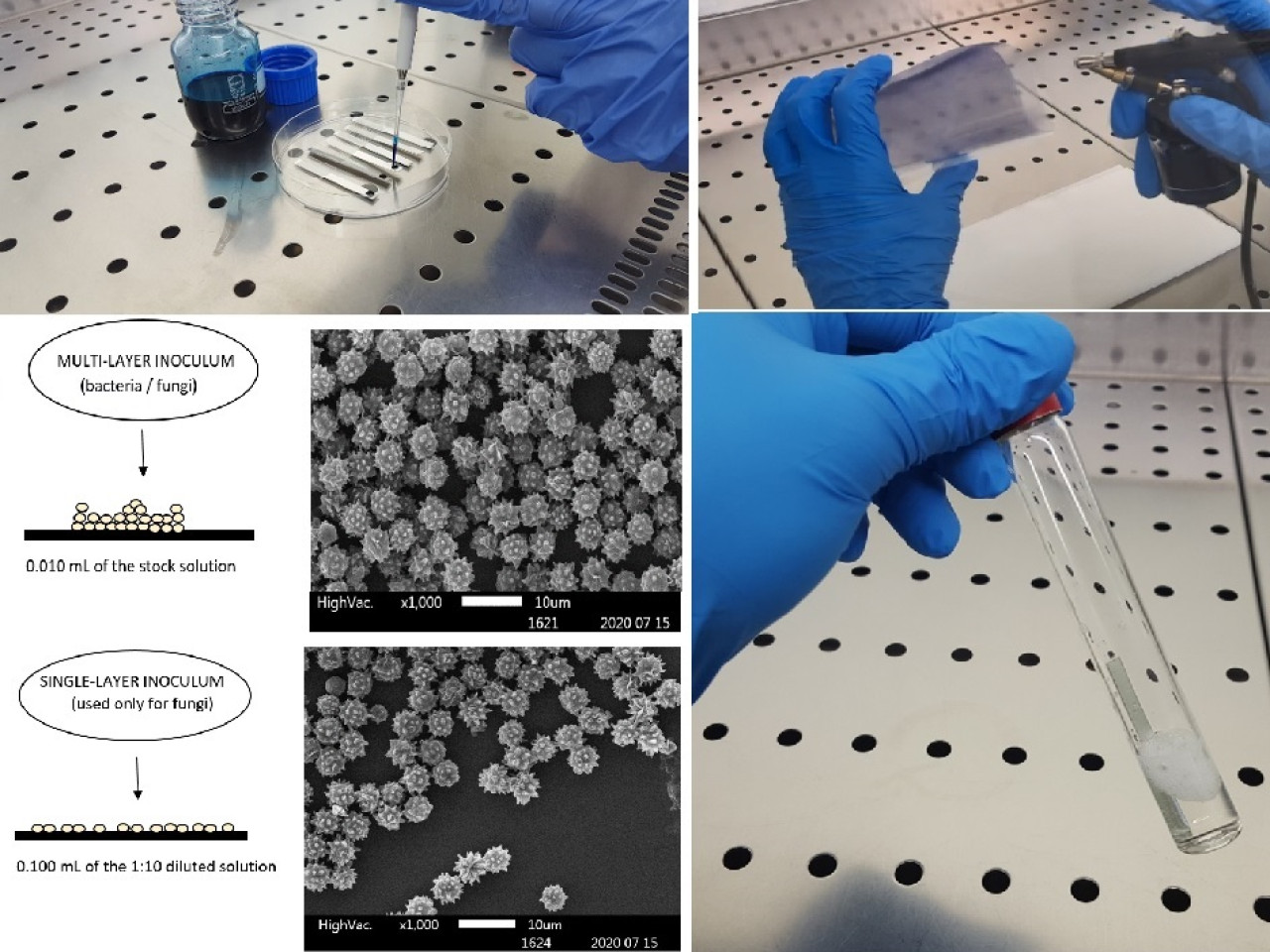