L'obiettivo dell'attività, nell'ambito del centro UMA3 (Materiali Unici per Applicazioni Aerospaziali Avanzate), è lo sviluppo e il test di materiali avanzati per la metallurgia delle polveri, la produzione additiva e i trattamenti superficiali (rivestimenti) per applicazioni aerospaziali.
I membri di UMA3 hanno unito le forze per sviluppare nuovi sistemi di materiali e creare nuove soluzioni tecnologiche, supportate da indagini interamente in 3D. I materiali sono stati ottimizzati a livello di laboratorio, con applicazione finale su componenti ottimizzati per velivoli e veicoli spaziali di nuova generazione.
Il processo multi-fase implementato dal centro di conoscenza (dall'ingegneria teorica e sperimentale alla modellazione computazionale e ai test su piccoli componenti) contribuisce notevolmente al know-how esistente, favorendo l'innovazione concettuale e basata sul mercato, nonché il progresso scientifico e di ricerca.
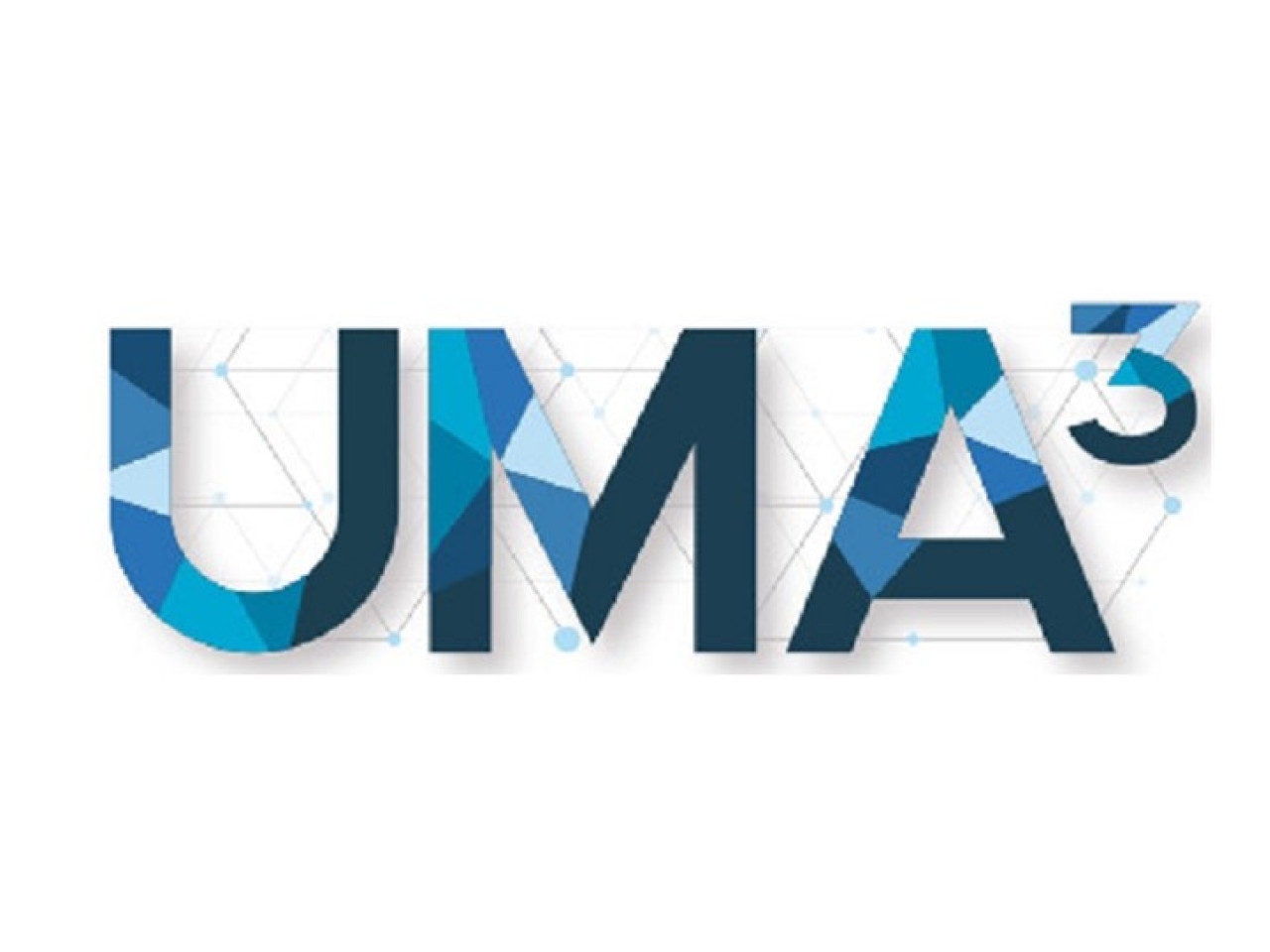
Le leghe leggere sono una delle chiavi dall'industria aerospaziale per ridurre le emissioni e aumentare l'efficienza, con particolare interesse per quelle innovative come l'Alluminio-Scandio e i Compositi a Matrice Metallica. Questi materiali mostrano un potenziale significativo se combinati con la Manifattura Additiva (AM), grazie alla creazione di strutture complesse con minori costi di assemblaggio e maggiore efficienza strutturale.
L'ottimizzazione dei parametri di processo della AM è essenziale per migliorare qualità, proprietà meccaniche e precisione delle parti. Questo richiede la regolazione di fattori come spessore degli strati, velocità di stampa, potenza del laser e velocità di alimentazione per minimizzare i difetti e migliorare la finitura superficiale. Metodi avanzati di simulazione come il machine learning sono stati applicati per identificare le migliori combinazioni di parametri, portando a una maggiore affidabilità del processo produttivo.
Per garantire che i componenti realizzati rispettino gli standard operativi, i ricercatori hanno sviluppato un approccio bottom-up, che comprende lo screening computazionale e la modellazione multiscala, seguiti dalla produzione e dai test in laboratorio su scala ridotta in condizioni realistiche.
Nei laboratori di Forlì, sono stati prodotti e verificati componenti in scala, contribuendo all'ottimizzazione della composizione dei materiali e aprendo la strada ad applicazioni industriali su scala più ampia.
L'innovazione inizia dalla selezione dei materiali candidati, utilizzando nuovi approcci teorici (ad es. nano-Calphad), con la proposta di tecniche di sintesi e sinterizzazione, l'impiego di metodi di analisi e di caratterizzazione 3D full-scale. È stata condotta un'analisi approfondita di una nuova lega di alluminio con scandio, mirata alla sua ottimizzazione per applicazioni aerospaziali.
Queste nuove tipologie di materiali, come i compositi a matrice metallica e le leghe leggere, sono stati verificati in laboratorio su campioni di dimensione ridotta e piccoli componenti dopo una modellazione numerica multiscala avanzata, pronti per applicazioni industriali.
Applicazioni tipiche sono componenti strutturali per aeronautica e spazio. Questi due settori sono tra i pionieri nella manifattura additiva (AM) e nella metallurgia delle polveri, caratterizzati da piccole dimensioni dei lotti e adattamenti specifici per ciascun produttore.
I principali vantaggi della AM nell'industria aerospaziale sono: ottimizzazione dei pesi (elevati valori di resistenza combinati con una riduzione del peso di circa il 40 - 60%), assenza di sprechi come nei metodi di lavorazione tradizionali, alto livello di precisione e qualità costante dei componenti.
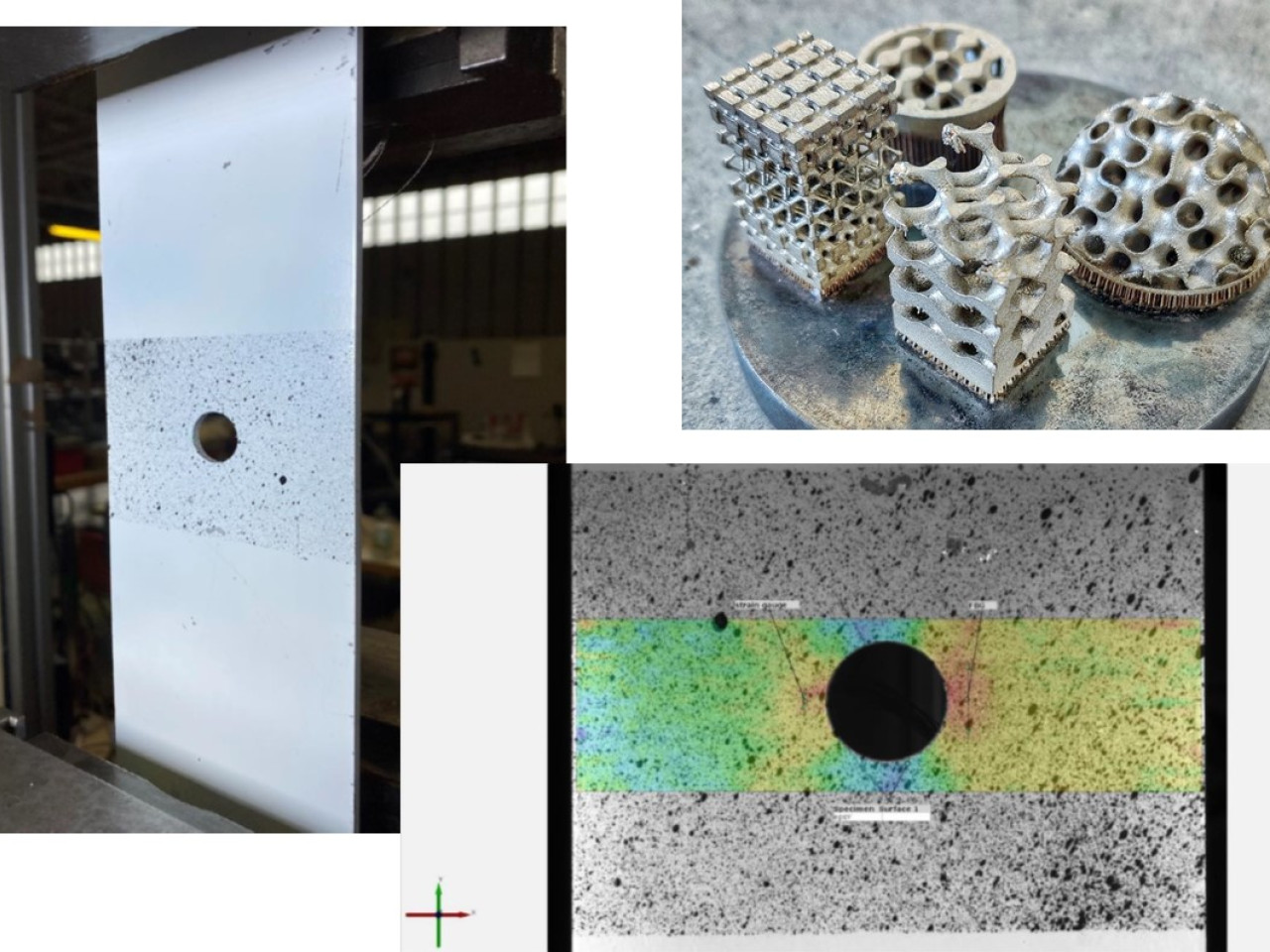
Laser Shock Peening su lega di Alluminio-Scandio per Applicazioni Aerospaziali
Le leghe di alluminio-scandio offrono un grande potenziale nelle applicazioni aerospaziali grazie alla loro elevata resistenza alla corrosione e alle ottime proprietà di resistenza. Inoltre, queste leghe sono qualificate per la produzione additiva (AM), ottenendo parti con resistenze statiche superiori rispetto ai metodi convenzionali. Tuttavia, la lavorazione laser genera anche elevate tensioni residue che possono ridurre le proprietà di fatica e provocare distorsioni geometriche.
Un metodo comprovato per ridurre i problemi di fatica è l'introduzione di tensioni residue compressive mediante Laser Shock Peening (LSP). L'industria aeronautica è attualmente molto interessata alla possibile applicazione dell'LSP in diverse fasi della vita dell'aeromobile, come soluzione conveniente in termini di costi e tempi.
L'obiettivo di questa applicazione è stato indagare gli effetti delle tensioni residue indotte da LSP sul comportamento a fatica di campioni di Al-Sc realizzati con la tecnica Selective Laser Melting. Partendo dai risultati dei test sperimentali, i risultati delle analisi numeriche sono stati utilizzati per la previsione della durata a fatica dei componenti. Sono stati identificati i parametri del materiale utili per le simulazioni numeriche e sono state fornite linee guida per la previsione del comportamento dell'Al-Sc.
- University of Miskolc, Hungary
- University of Patras, Greece
- Fraunhofer IFAM, Germany
- ALTRAN Deutschland, Germany
- Fundacion ICAMCYL, Spain
- EASN-Technology Innovation Services, Belgium
I risultati sono stati presentati in conferenze internazionali ed è stata proposta un'attività di follow-up per guidare le aziende aerospaziali in Europa.
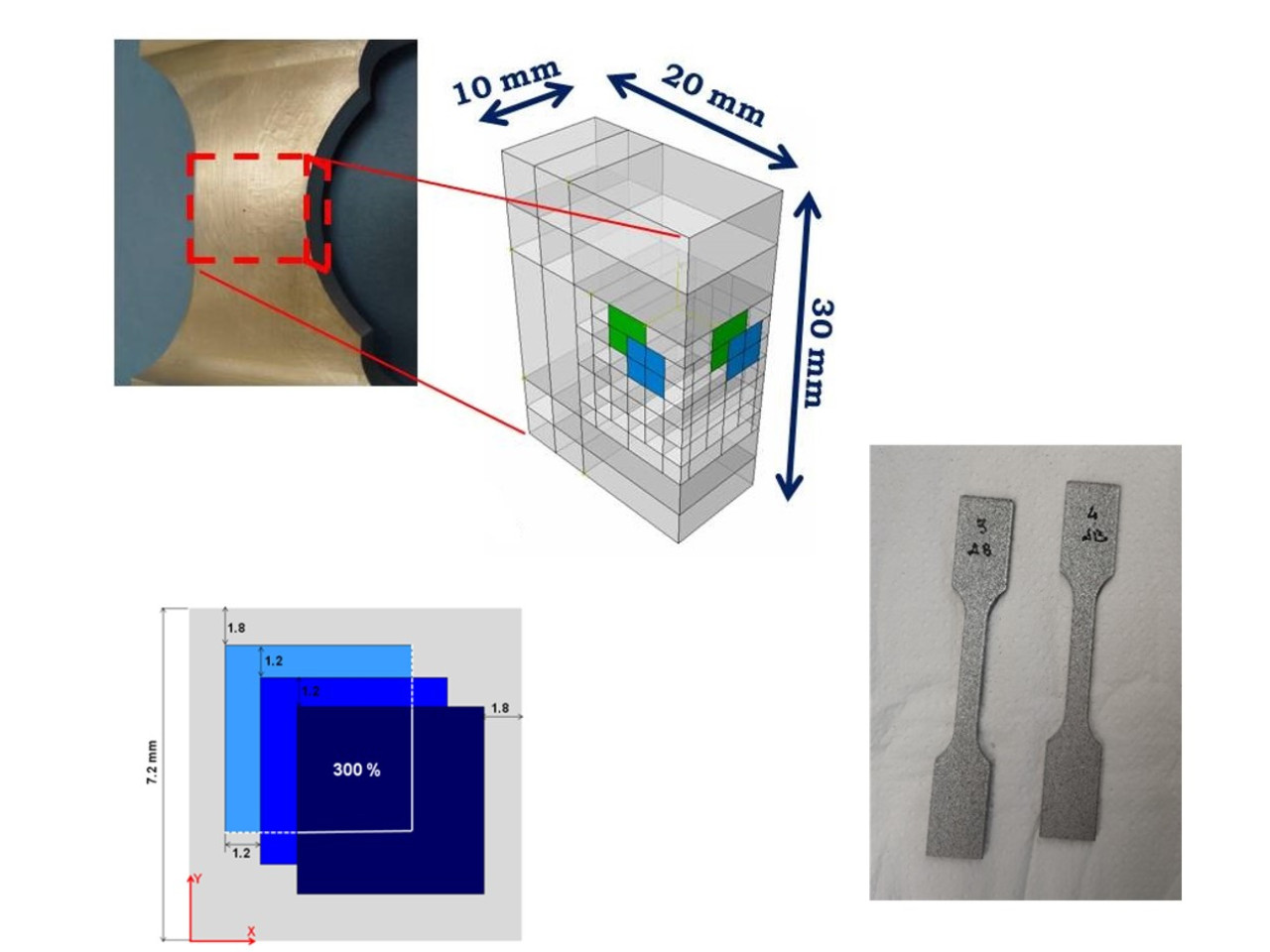