The focus of the activity, inside the framework of the integrated knowledge centre UMA3 (Unique Materials for Advanced Aerospace Applications), is the development and test of advanced materials for powder metallurgy, additive manufacturing and surface technology (coatings) for lightweight aerospace applications.
The members of UMA3 have joined forces to develop new material systems and create new technological solutions, with the support of fully 3D investigations. The materials have been optimized at lab level, with final application on lightweight components for new generation aircraft and spacecraft.
The multi-step process implemented by the knowledge centre (from theoretical and experimental engineering to computational modelling and test on small components) remarkably contributes to existing know-how and concept-driven, market-based innovation and scientific & research progress as well. Knowledge transfer is realized on each topic, led by internationally recognized researchers.
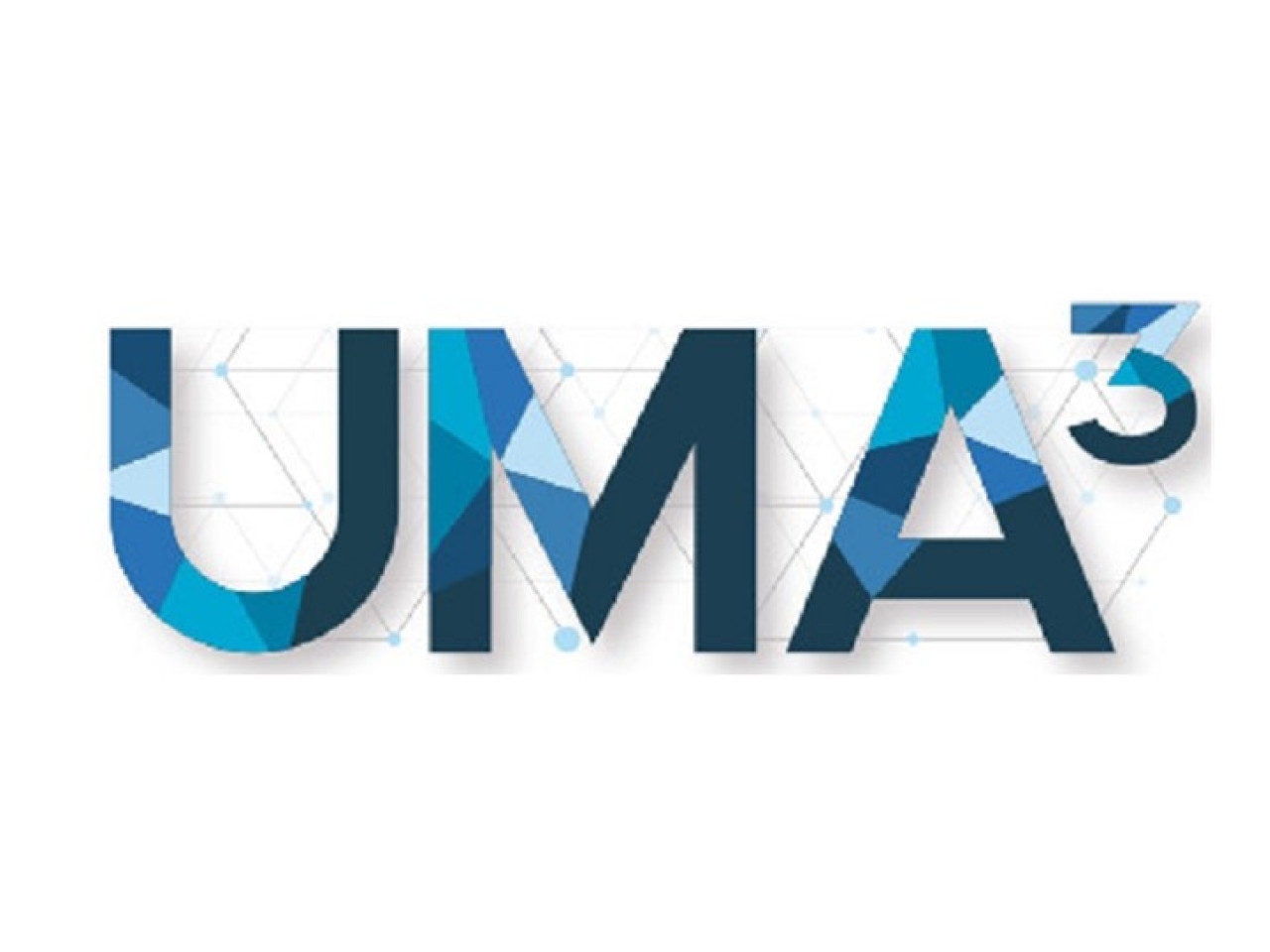
The aerospace industry's pursuit of reduced emissions and increased efficiency is driving the research and application of lightweight materials, especially innovative alloys like Aluminum-Scandium and Metal Matrix Composites. These materials show significant promise when paired with Powder Metallurgy and Additive Manufacturing (AM) due to their ability to create complex structures that lower assembly costs and enhance material efficiency.
Optimizing AM process parameters is essential for improving the quality, mechanical properties, and precision of fabricated parts. This involves fine-tuning factors like layer thickness, print speed, laser power, and material feed rate to minimize defects and enhance surface finish and dimensional accuracy. Advanced methods, including machine learning, simulations, and design of experiments, have been applied for the identification of ideal parameter combinations, leading to improved efficiency and reliability of the manufacturing process.
To ensure components made from these advanced materials meet operational standards, researchers have developed a bottom-up approach, including computational screening and multiscale modeling, followed by lab-scale production and testing under realistic conditions.
In Forlì laboratories, coupon-sized components have been produced and tested, contributing to material composition optimization and paving the way for scalable industrial applications.
The innovation starts from the candidate material selection, using new theoretical approach (e.g. nano-Calphad), with proposal of synthesis and sintering techniques, employment of analysis and full-scale 3D characterization methods. A deep analysis of new Aluminum alloy with Scandium has been similarly performed for its optimization in aerospace applications.
The novel metal matrix composite material and light alloy systems have been tested at coupon and small component level after advanced numerical multiscale modelling, ready for industrial applications.
Typical application are components for aeronautics and space applications. It is well known that those are two of the pioneering sectors for additive manufacturing and powder metallurgy, being characterized by small batch sizes and manufacturer-specific adaptations. General advantages of additive manufacturing (AM) in the aerospace industry are: great potential for lightweight construction (high strength figures coupled with a reduction in weight of around 40 - 60%), no waste as with traditional machining methods, high level of precision and consistently high quality of the components.
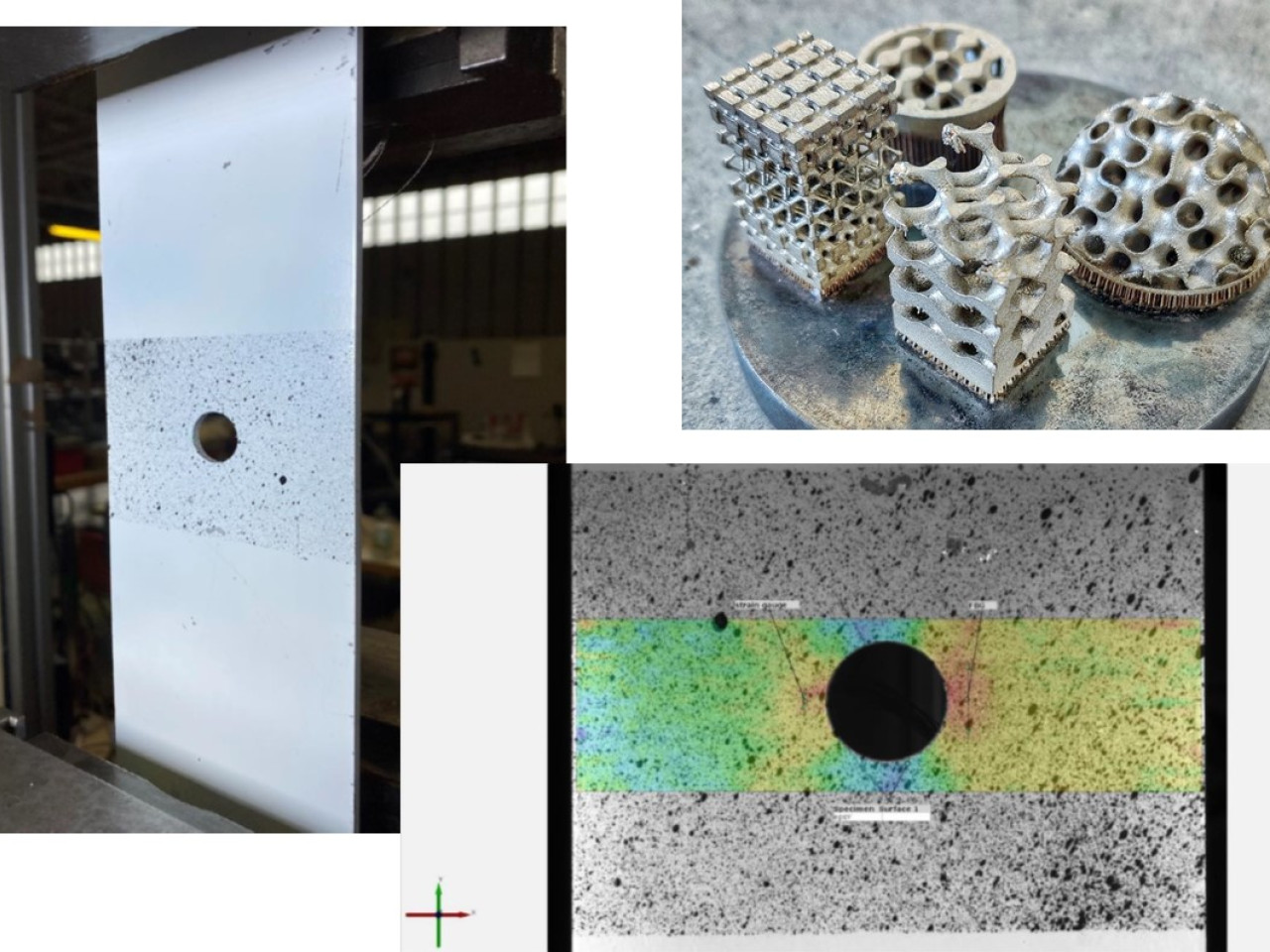
Laser Shock Peening on Aluminum-Scandium alloy for Aerospace Applications
Aluminum alloys with scandium content offer great potential in aerospace applications due their high corrosion resistance and improved strength properties. Furthermore, these alloys have been qualified for laser additive manufacturing (AM), producing parts with static strengths exceeding their conventionally manufactured counterparts. However, laser processing also results in large residual stresses that can severely affect fatigue properties and result in geometric distortion.
A proven method for reducing the fatigue related problems in metallic structures is to drive compressive residual stresses into the affected area by means of Laser Shock Peening (LSP). The aeronautical industry is currently strongly interested on the possible application of the LSP at different stages of the aircraft life, as a cost and time effective solution to correct adverse residual stress and distortions.
The aim of this application was the investigation of the effects of LSP-induced residual stress on the fatigue behaviour of Al-Sc coupons made by Selective Laser Melting AM technique. Starting from the results of experimental tests, the results of numerical analyses are used for the prediction of fatigue life in aerospace grade light alloys. The material parameters useful for the numerical simulations have been identified and guidelines for the prediction of Al-Sc behaviour have been provided.
- University of Miskolc, Hungary
- University of Patras, Greece
- Fraunhofer IFAM, Germany
- ALTRAN Deutschland, Germany
- Fundacion ICAMCYL, Spain
- EASN-Technology Innovation Services, Belgium
The results have been presented in international conferences and a follow-up activity has been proposed to lead aerospace companies in Europe.
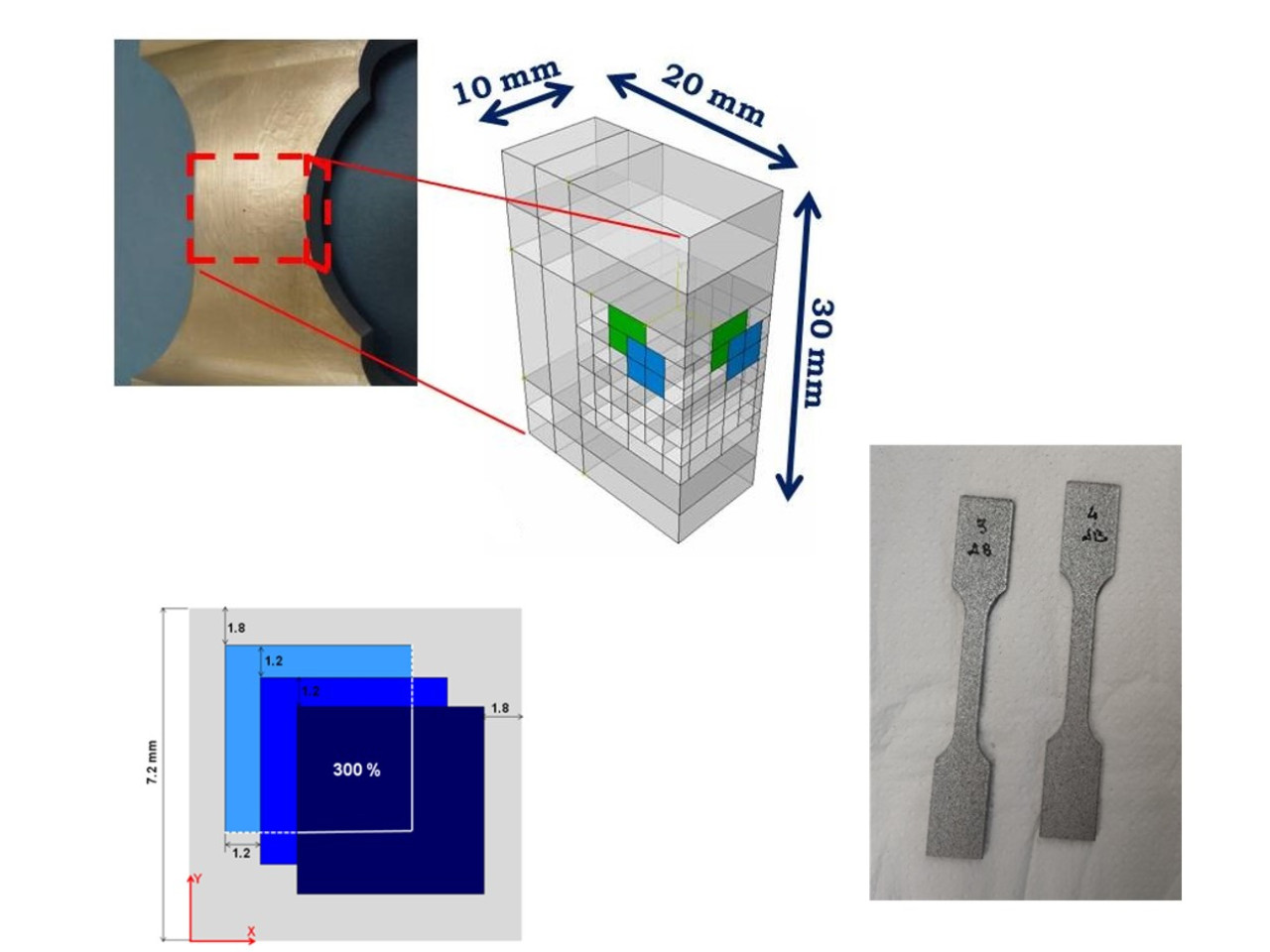