Titanium alloys and Ni-based super-alloys are notoriously difficult to machine materials mainly because of their low thermal conductivity. This causes high cutting temperatures with a consequent triggering of a series of problems related to thermal stresses.Titanium has a high chemical reactivity with tool material that, combined with high temperatures,causes adhesion phenomena, cratering and, therefore, strong wear rate. Because of the large volumes of material removed through roughing operations,which for aeronautical parts can reach even 90% of the raw material, a high productivity performance is required. The issues outlined above force operators to adopt limited cutting parameters, which obviously negatively influence the productivity. Hence, cryo-machining, with its strong cooling potential,could be considered a low environmental impact solution for the improvement of tool life and subsequently of productivity for hard to machine material.
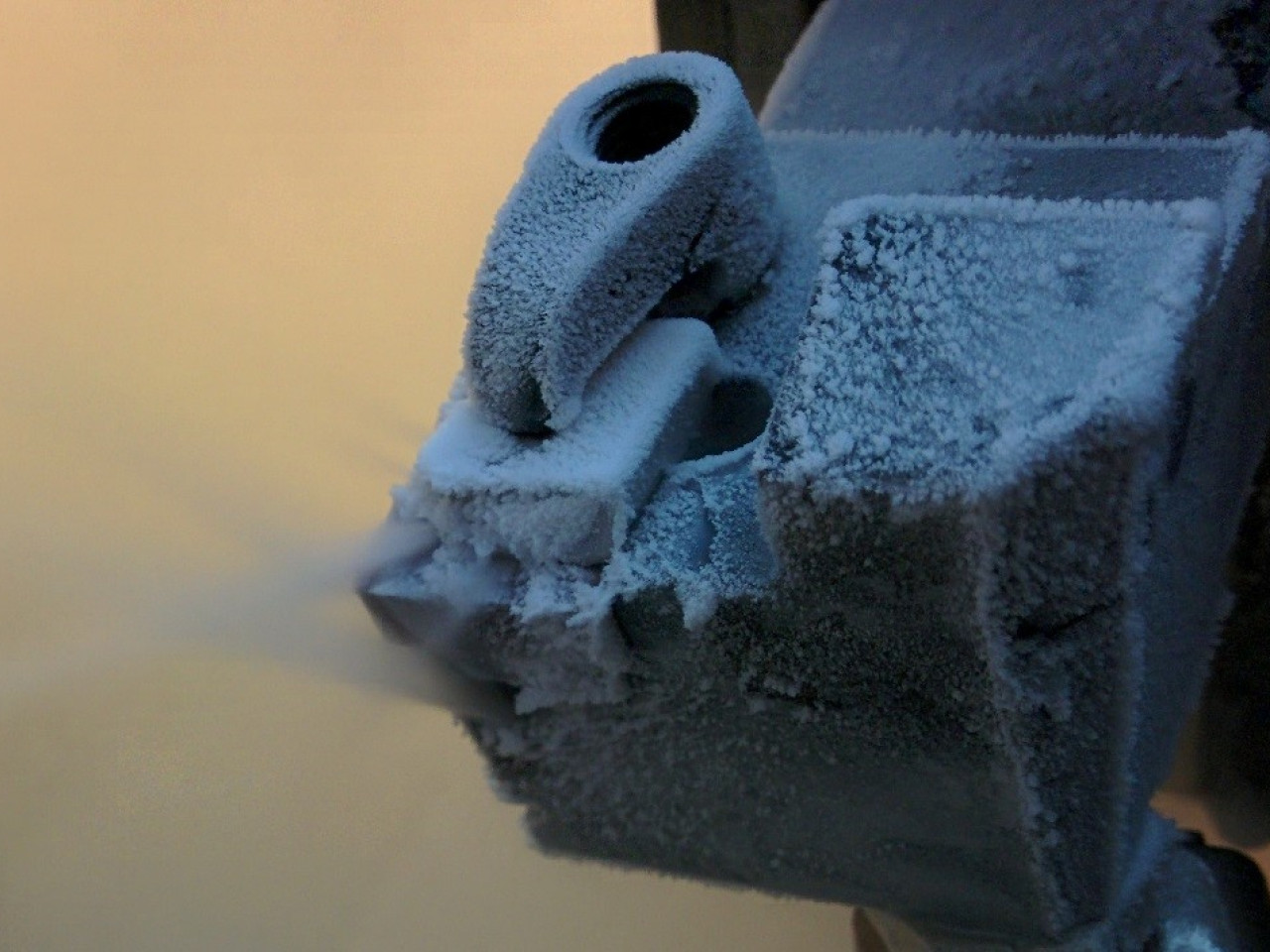
In standard industrial practice, the cooling of cutting operations for hard to machine materials is performed by adopting a large amount of flooding oil-water emulsion delivered in all the machining area. If compared to cryo-machining this method on one hand is not effective for productivity and tool life aspects (because liquid nitrogen has a very stronger cooling capability). On the other hand, mineral oil, which is used for the emulsions, needs to be disposed with costs and environmental impact. Furthermore the chip and the machined part are dirty of oil and need to be cleaned for the following operations (regeneration of raw material or assembly), also this problem is solved with cryo-cooling.
Cryogenic cooling can be adopted for turning, milling and drilling operations. The aim is to define a new state of the art for the machining of titanium alloys easily accessible by those already working this type of materials but also inspiring anyone who designs and manufactures machine tools, for the creation of new models adopting cryogenic technology.
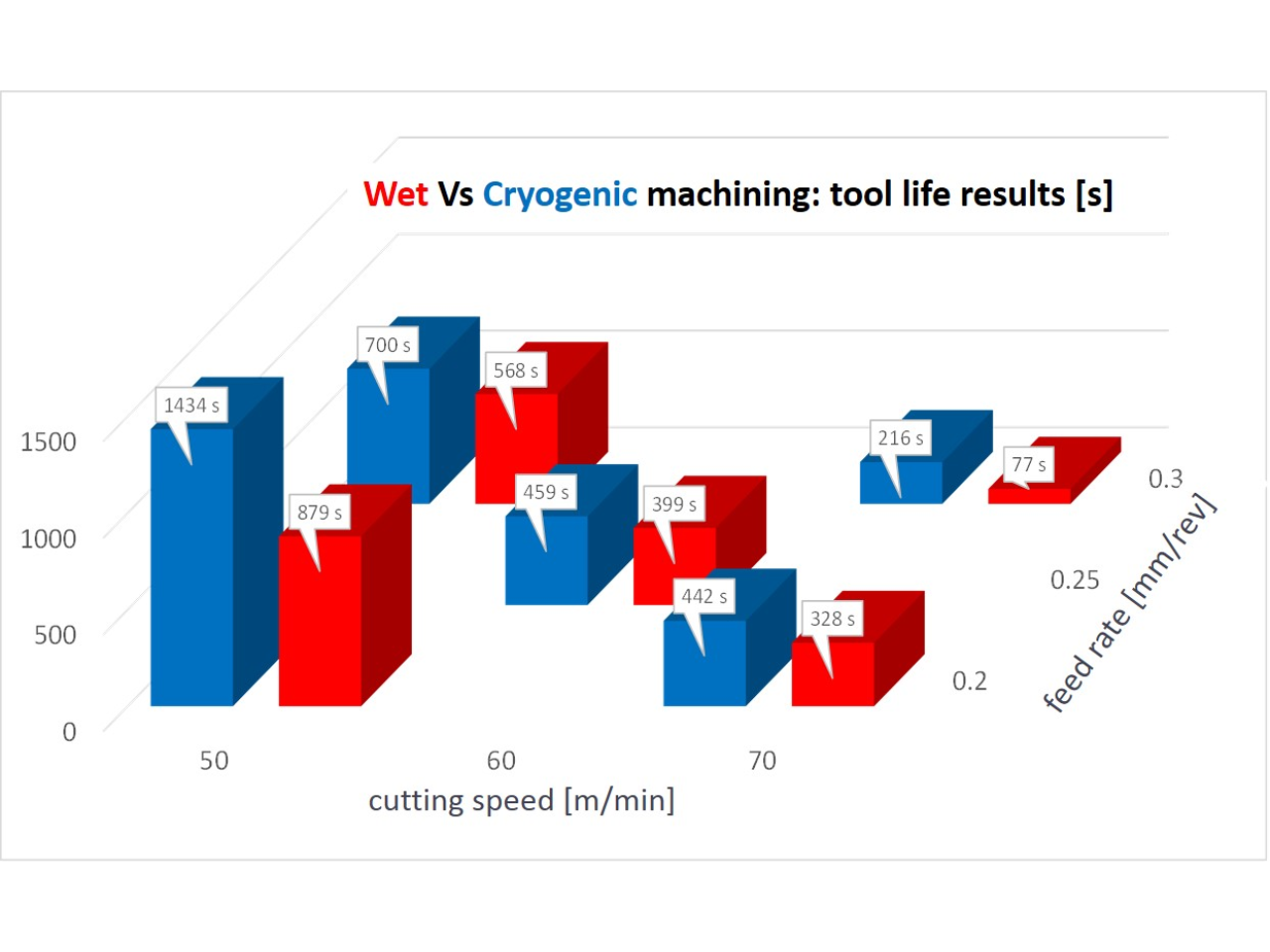
Cryogenic turning
MUSP lab has already tested with success an application for turning operations thanks to the cryogenic conversion of a traditional CN lathe. The features of the revamping system consist in a dewar for the stocking of liquid nitrogen positioned close to the lathe machine, a thermally insulated pipe which leads liquid nitrogen to the cutting zone, and a special turning tool-holder which delivers liquid nitrogen flow in three points of the material removal zone for a strongly localized cooling effect. A comparison, from an industrial point of view, of the benefits of the adoption of cryogenic cooling instead of traditional cooling systems was performed by hypothesizing a typical productive scenario. Time and costs of production were calculated. Cryogenic cooling can significantly improve tool life with respect to traditional oil water emulsion cooling. For the considered production scenario, which is typical of aeronautic parts, cryogenic cooling can improve productivity and reduce costs. The optimal cutting parameters are higher for cryo-machining both for the minimization of time and cost.
Machine tool producers, tool producers and aerospace companies
The results of the project were presented at international conferences, seminars and international scientific journals. Furthermore, commercial aspects and potentialities of the project were presented to companies both with direct presentations and with articles on national sector magazines. Important collaborations for the development of the project with industrial partners have already started
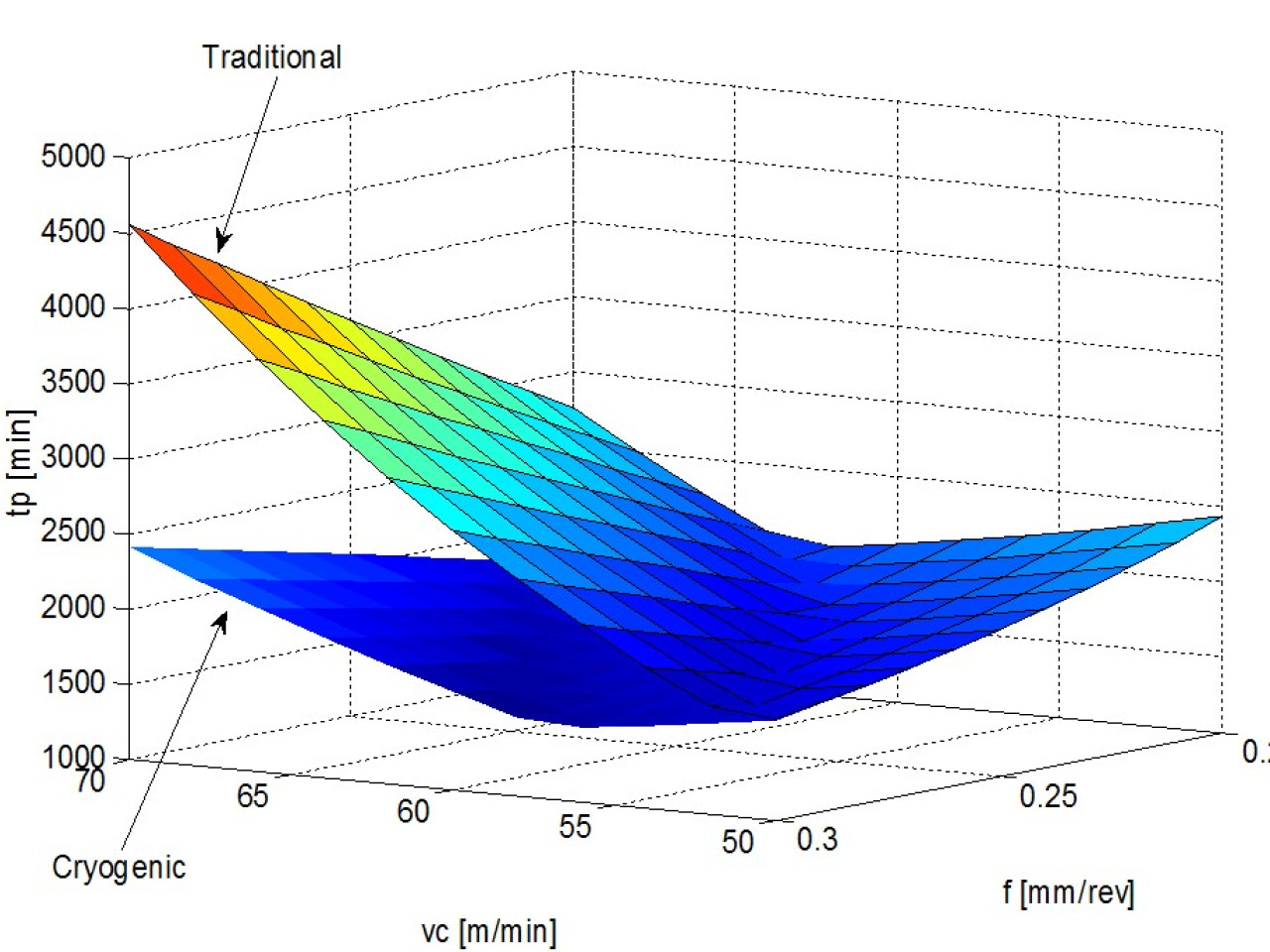