The need to improve the efficiency of energy consumption is a key point of sustainable economic development. This view is also shared by the EU which adopted the directive Ecodesing directed towards the development of more efficient systems. The asynchronous motors are in the field of electricity consumption the most significant item of the inherent part of the electromechanical energy conversion and are therefore key elements of this process of improvement. The development of engines with a higher efficiency clashes with the need to keep production costs for content items that are normally produced in the tens of thousands of parts, and for which the cost of raw materials is a significant point. In particular, the project is the development and optimization of the magnetic circuit of the electric machine.

The project of the electric motor must be particularly accurate for simultaneously respond to the needs of performance while keeping production costs acceptable: it is necessary to develop optimized design procedures. One of the finest tools for sizing is the use of computational tools finite element, but it requires a rather long time solution. In this project, developed calculation algorithms analytical (very fast in their execution) that rest in turn on the finite element analysis tools for determining only the most sensitive magnitudes.
The applications of this type of engines ranging from ventilation and pumping, for industrial and civil use of automation applications. In general, the increasing focus on issues related to energy saving has prompted the EU to issue a directive which effectively imposes high efficiency motors for all to higher energy consumption applications (motors for continuous service, S1 service class). The levels of efficiency required in this type of engines is gradually increasing (From class IE2 the past few years to IE3 request from January 2015 to IE4 which will come into force in the coming years).
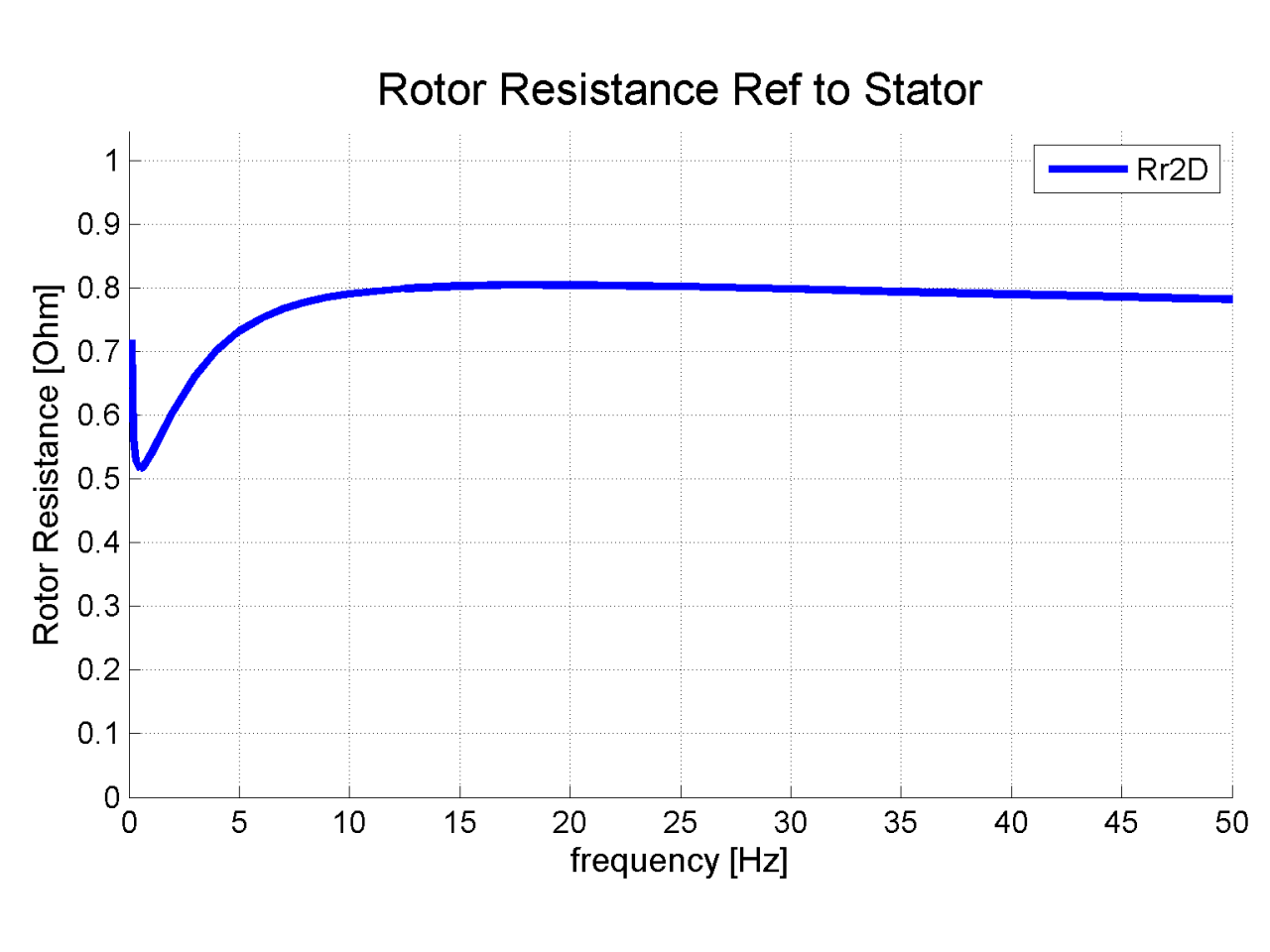
4-pole motor of 3 kW of power for pumping and ventilation applications
The developed method combines the analytical design of the asynchronous machine with a two-dimensional FEM solver. The analytical optimization process is very quick and allows you to make hundreds of iterations in a very short time. Once the preliminary design was identified through the analytical sizing, the finite element solver is invoked by the algorithm for the verification of the most important machine parameters (inductance of magnetization, rotor resistance, dispersed inductances). The methodology presented herein has been applied to the design of a 4-pole motor of 3 kW of power for ventilation and pumping applications. Starting from sheared commercial, the project has been enhanced to find the best balance between the different contributions of the electric motor loss. The engine was simulated on the computer playing the bench test conditions on an actual prototype of the company. As several prototypes of asynchronous motors with high efficiency have been designed and built, the engine bench test has confirmed the validity of the design methodology, because all the engines were found to comply with the required performance specifications.
Nicolini &C.
It is believed that this design methodology and acquired skills can be of great interest to various companies in the region and more generally the Northern Italian industrial fabric, given the high concentration of manufacturing, and the use of asynchronous motors.
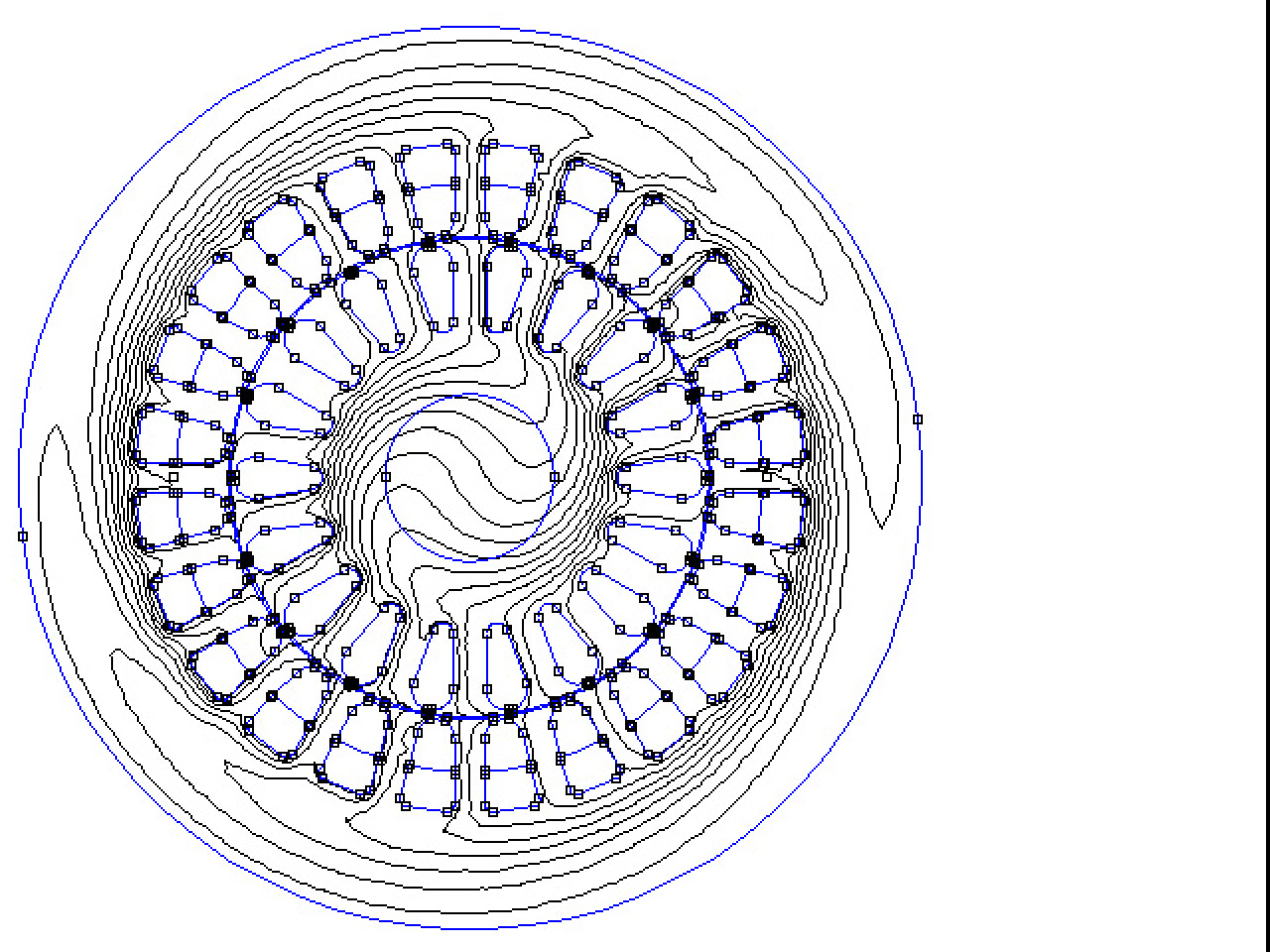