The DIGIMAN project aims to develop tools to support the transformation of a generic industrial machinery into a Cyber-Physical System. This result will be possible thanks to the definition and implementation of a hardware-software platform, called Augmented Manufacturing Platform (AMP), which will integrate with the generic machinery, increasing its sensory capabilities as well as operational functions. The AMP interfaces with the processes both through hardware modules (sensors, data acquisition, etc.) and through software modules (data processing, monitoring, etc.) by integrating learning approaches from expert operators. The main objectives are the ability to improve, even in real-time, the quality of products and the ability to infer on the state of the process, machines and components by proposing intervention strategies.
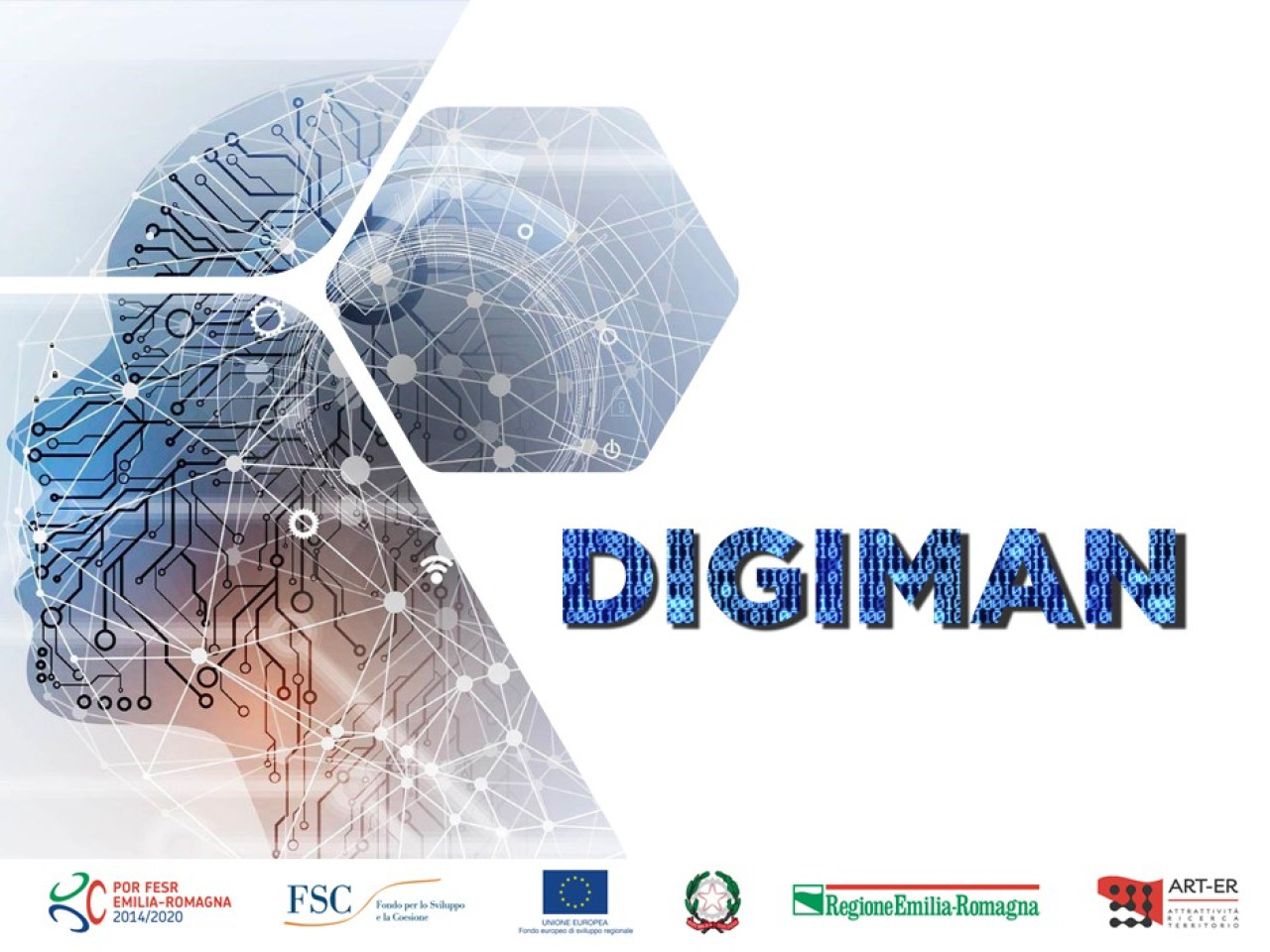
The AMP is a modular tool adaptable to a generic machine and process, selecting hardware interfaces to communicate with the machine control and sensors, integrating specific software modules according to the needed processing strategies and functionalities. The developed in/out-of -process functionalities concern chip removal processes performed by a machining centre. As for in-process functionalities, a cutting tool will be sensorised with an active element, capable of simultaneously moving the cutting edge and carrying out process monitoring and control in real time. A software module will simulate the cutting process (being its Digital Twin) and estimate the quality characteristics of the machined part. Out-of-process functionalities will consist of (1) an intelligent robotic solution equipped with a camera and analog sensors, able to move autonomously to inspect machined parts and characterize their output quality, (2) a supervision and cohesion tool of the entire platform (the Virtual Operator), integrated based on artificial intelligence approaches. It will categorize the characteristics of the process, formalize expert operators’ knowledge, associating them to the collected data and to infer on the state of the process to intervene, even in real-time, by modifying process parameters and suggesting corrective actions to optimize the output quality.
Considering all the modules envisaged, the DIGIMAN project will provide an extremely complex and innovative tool that will touch on all the aspects involved in the manufacturing process. For example, we will use a tool with autonomous sensory capabilities capable of extending the perceptive capabilities of the machinery on which it is used, and also a robotic arm equipped with a vision system capable of inspecting some technological features of the machined piece. All this information will be usable by the Virtual Operator for evaluating the quality of the piece and the state of the machine.
Through the use of Cyber Physical Systems, both of machine components and processes, it will be possible to develop technological models capable of understanding in real time, through the re-processing of data arriving from the machine, what the machine itself is doing or what is happening in the process. This approach is applicable to many technological aspects of the machine tool, whether it is a milling application, whether it is water jet cutting or other types of processes that involve the wear of certain components or the need for a evaluation of the quality of the process.
Application of the Digital Twin Module to the case of a hydraulic power unit
A particularly concrete example of the use of the tools provided by the DIGIMAN project is the application of the Digital Twin Module to the case of a hydraulic power unit, an auxiliary device to the machine tool.
Through the development and use of the digital twin of the control unit, it was in fact possible to simulate different failure states within different components of the control unit, such as a pressure sensor, a servo valve and a high pressure pump, thanks the development and training of an Artificial Intelligence model that can perform the diagnostics of these components.
After reading the sensors present directly on the machine, it was possible to compare, using Artificial Intelligence techniques, the real values with the simulations carried out by the Digital Twin Module and check the state of health of the analyzed components. Finally, a prognostic approach has been developed, which is not only able to indicate the remaining life time, but also its probability density, i.e. how the residual life time is distributed in probability over time, providing enormous support to the choice of maintenance.
LABORATORIES:
MUSP – Industrial research laboratory (LEADING PARTNER)
MISTER – Industrial research laboratory
ISTEC CNR – Research center
COMPANIES:
SCM Group
MCM
Mandelli Sistemi Spa
Jobs Spa
Marposs Spa
Poggiopollini Srl
Search for business partners for further applications;
Further validation in the operational environment.
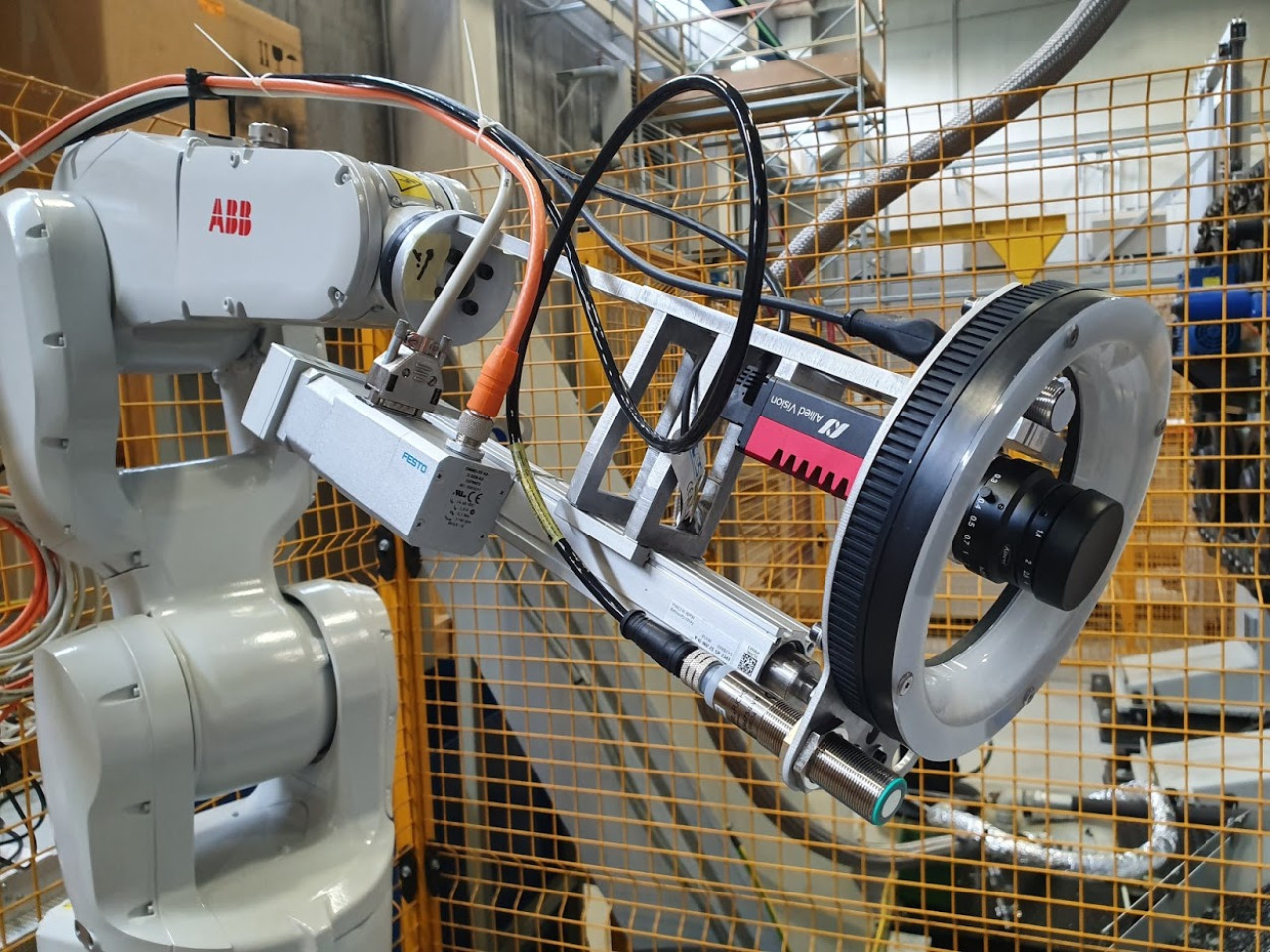