The Green ceramic tiles made by 70% at least - and till 99% - of urban and industrial scraps. The production of these tiles contributes to the sustainable management of waste. The recovery of industrial scraps and materials such as packaging glass not reuse in the glass industry (about 30% of the total glass), allows the natural resources consumption traditionally used as raw materials for tiles. In this way the environmental performances of the productive cycles of the ceramic sector are improved due to the reduction of energy consumption, methane use, and CO2 emissions.
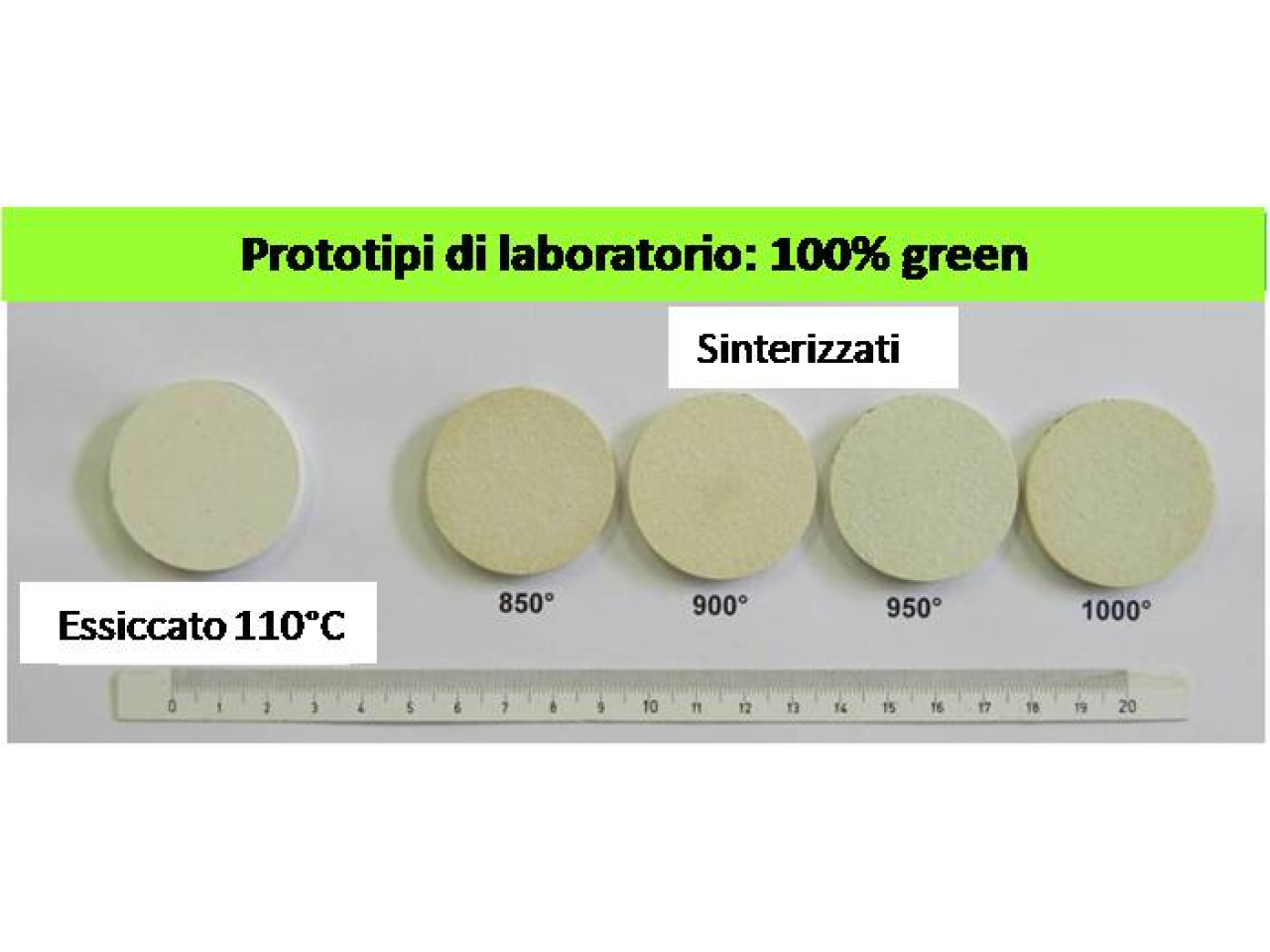
The Green ceramic tiles made almost exclusively by secondary raw materials allow: - Recovery of scraps, energy consumption and gas emissions reduction - Reaching of performances similar or improved respect to a traditional porcelain stoneware The innovative production process allows to ceramic industry to: - Diminish the costs for energy consumption (milling and firing steps) - Produce materials "Green"coming from the valorization of secondary raw materials, increasing the industry competitiveness and broadening the potential application of the ceramic products.
The production process of the Green tiles can be adopted by ceramic industries, allowing the setting-up of products very versatile for internal or external paving in this last case, with the target to conquer new market shares, in substitution of traditional materials such as cement or concrete. The interest for this type of products is demonstrated also by the EU-founded project WINCER (ECO/13/630426) "Waste synergy in the production of Innovative CERamic tiles".
Production of innovative and sustainable ceramice tiles in several formats (40x40 mm; 100x100 mm; 250x250 mm) and thickness (3, 5, 7, 12 mm). The laboratory prototypes fulfill the standard requirements, in particular EN 14411 (“Ceramic tiles: Definitions, classification, characteristics, evaluation of conformity and markingâ€
The laboratory prototypes are fired about 150-200°C lower respect to a traditional porcelain stoneware, allowing an energy saving of 10% at least. The physical-mechanical performances are still rather good: low water absorption (60MPa). It is possible to envisage that the industrialization of the innovative tile will allow a economic save for the body mix preparation (about -15%), energy and methane consumption (about -10%). Due to the lower methane consumption a consequent lower CO2 emission (about -10%) can be estimated. moreover the standard requirements will be fulfilled, in particular the standards UNI EN ISO 10545 and EN 14411.
Ceramic tile producer: FINCIBEC SpA Research centre: CENTRO CERAMICO Raw materials and waste supplier: MINERALI INDUSTRIALI SpA
The industrial transfer of Green Tiles allowed to verify several advantages, such as: - Reduction of energy consumption - Reduction of gas emission - Industrial fixed costs abatement for the preparation of the ceramic mixes The quantification of these reductions is necessary as baseline of the ceramic sector to promote further energy saving in agreement the National and European regulation.