Direct Laser Hardening (DLH) in numerical control machining centres is a process to superficially harden mechanical components at the end of removal processing and directly on the machining centre where they have been made, thus avoiding induction hardening. Finished components are obtained, less any grinding operations, by integrating a suitable laser source in removal machine tools and using adequate laser parameters to obtain optimal hardness and depth for operation. The hardening techniques to be used must be selected based on the geometry of the surfaces to be treated, but results are wholly comparable, if not better, than those obtained with conventional induction hardening. Modern laser sources are characterised by significantly easy handling and may be housed in common tool magazines of the machines and moved by the control like any tool.
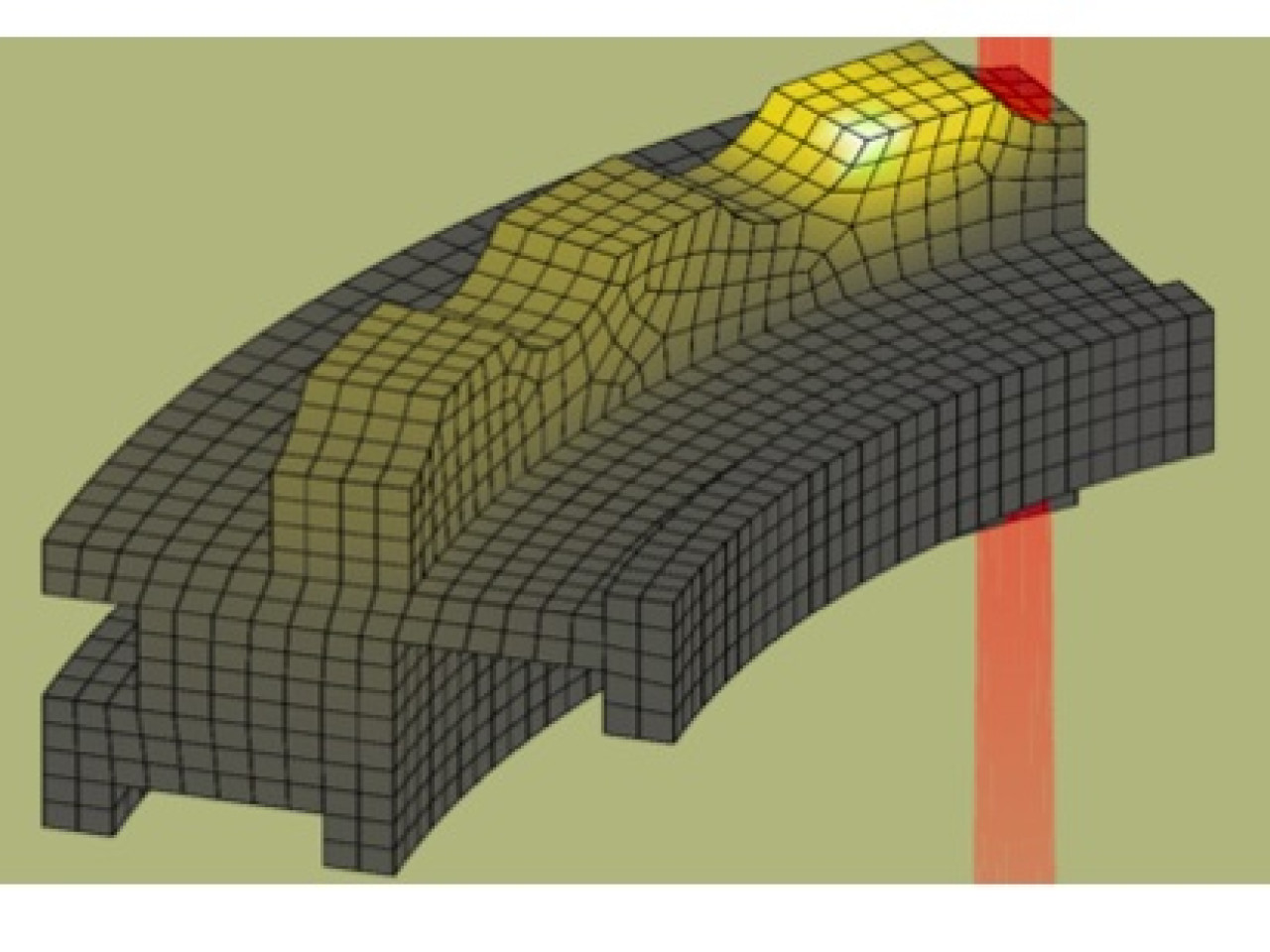
The innovative aspects consist in performing laser hardening directly on the machine tool that has made the component which will only need to undergo possible grinding operations. In some cases, if the component's aesthetics allows it, the component is ready for use. The DLH process affords a number of advantages compared to a conventional laser surface hardening process, which may be summarised as less thermal deformation on the component - leading to enhanced ability to obtain good dimensional tolerances - and greater flexibility in processing a variety of surfaces, which translates into faster response to market. If suitably designed, DLH makes it possible to obtain a part with good surface quality which does not need to undergo further finishing processes. Laser hardening processes also afford significant energy savings.
The potential applications include all mechanical components that require high surface hardness and that are currently induction hardened. In addition, DLH allows case-hardened steel to be replaced with quenched and tempered steel, thus eliminating the case-hardening process.
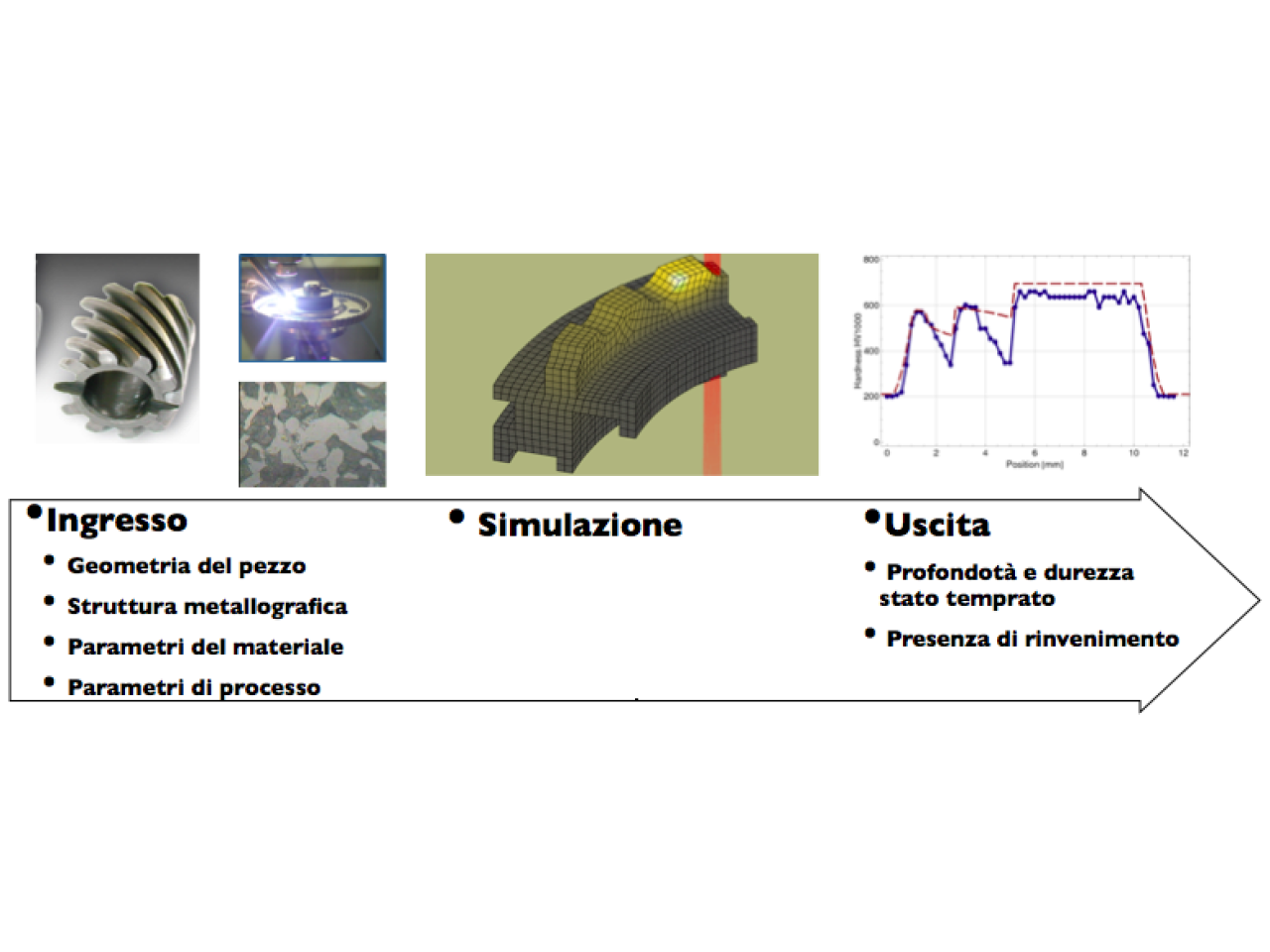
Thermal laser surface treatment on cams
A winning example of DLH application is in producing hard surfaces on cams for motion transmission in automatic wrapping and packaging machines Experimentation was conducted with IMA. The use of DLH highlighted the economic convenience and technological feasibility in replacing the old processing cycle based on induction hardening or NITEMPER with direct laser hardening in the machine, with marked advantages on product quality and processing time. The results obtained have proved the technical-economic feasibility of the process and led IMA to implementing a combined cutting and laser system.
IMA S.p.A.
Another collaboration is currently under way for making ready a laser source onto a grinding machine, and two units are to be supplied. The service is actualised through research contracts for a period of not less than 9 months
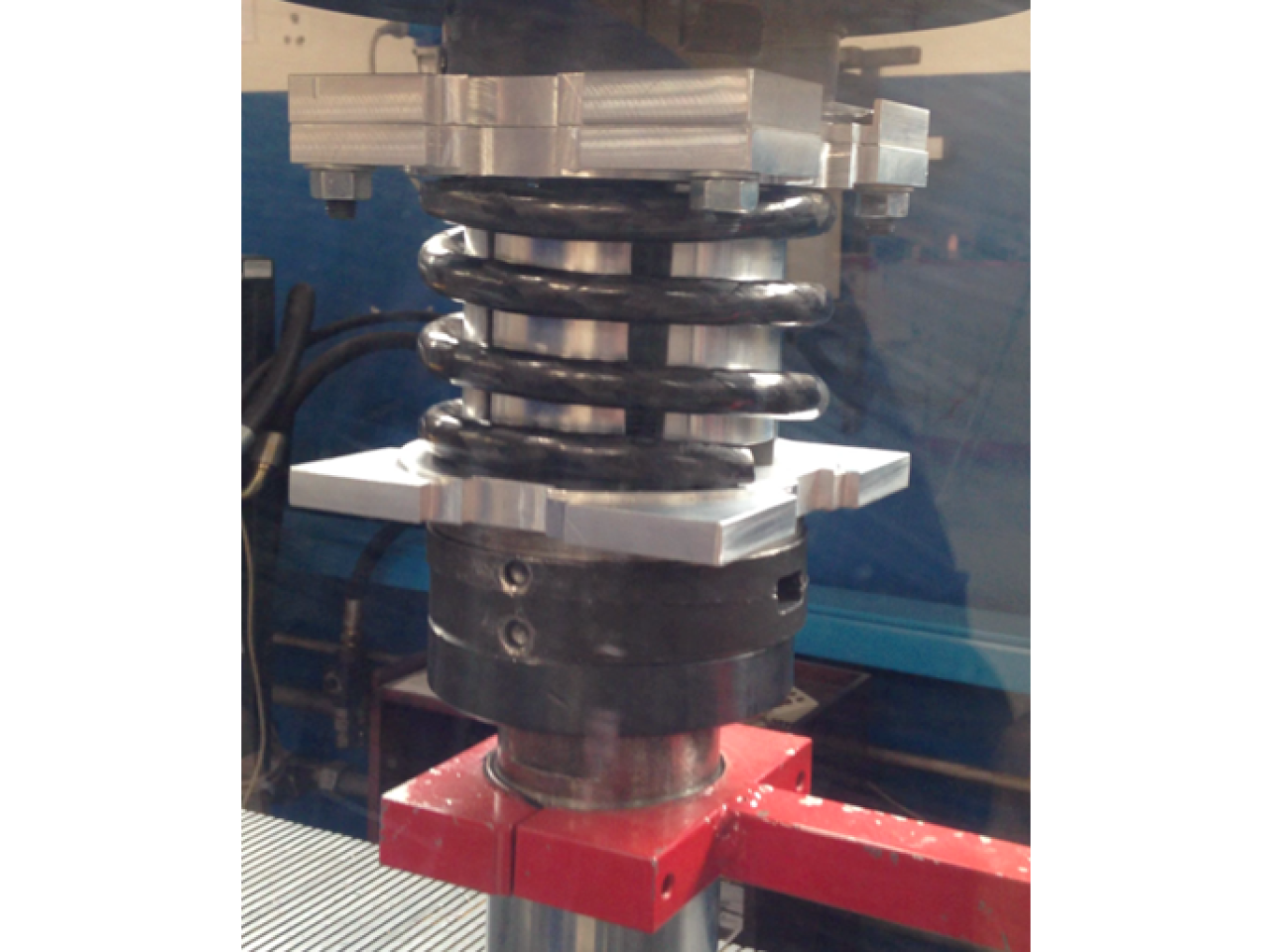