The experiences accumulated within the MUSP Laboratory in the field of redesig and, more broadly, design of structural parts of various types of machine tools, with conventional materials (especially electro-welded steel) and innovative ones such as aluminium foams, hybrid aluminium-polymer foams and polymer concrete, have highlighted the need to define an integrated approach to the problem and a method to deal with the various stages of the work in an informed and structured manner. This method has been developed with a view to best exploiting the mechanical and technological features of the materials used. As a matter of fact, structural foams provide the designer with new possibilities in terms of greater freedom in the choice of sections and configurations and allow one's action to focus on structural components that limit the machine tool's overall performance.
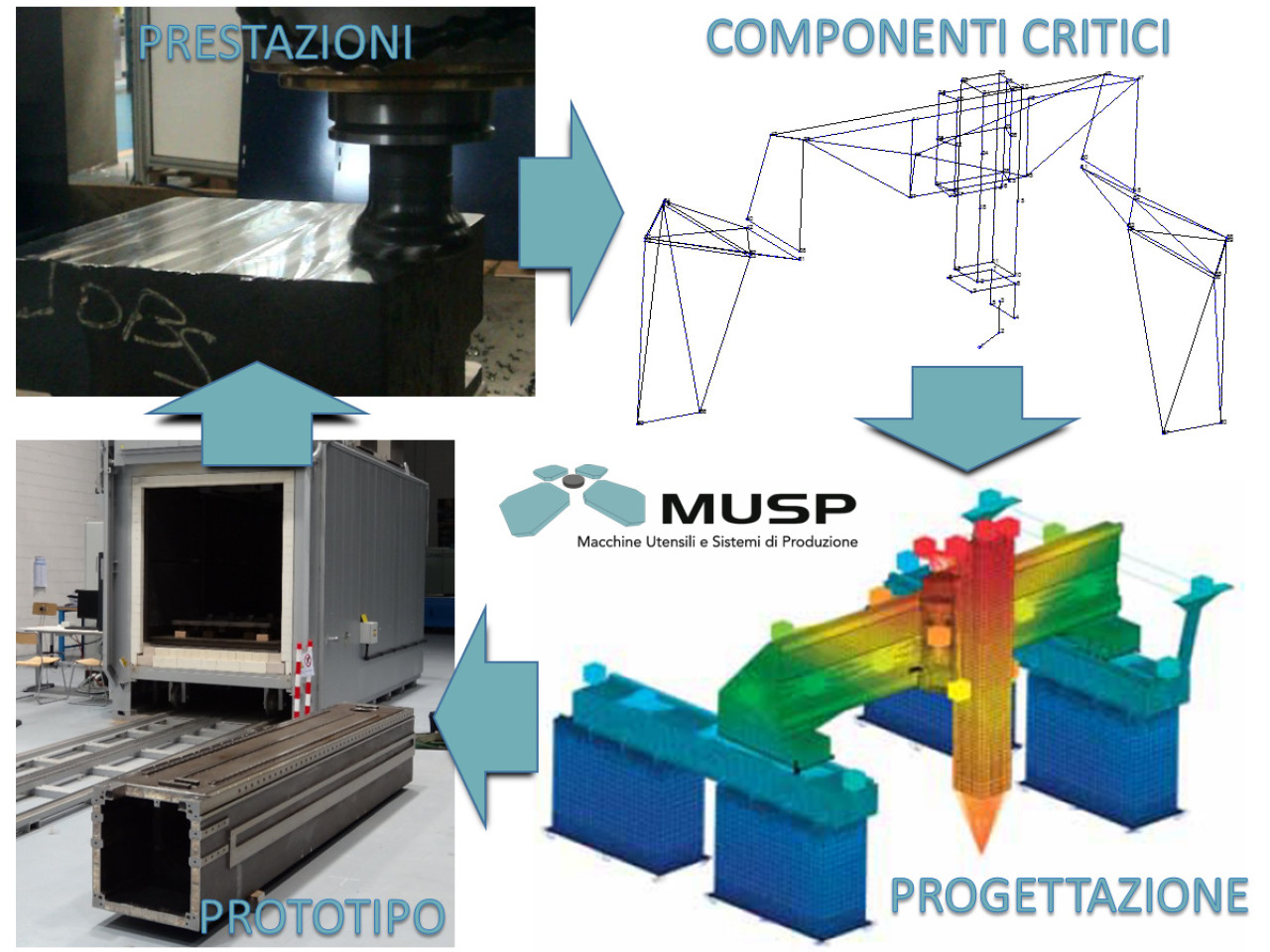
Aluminium and aluminium-polymer foams (Hybrid APM) are a new class of materials with regards to application to machine tools. Both the scientific literature and previous application cases indicate that the use of these materials - within a framework of integrated redesigning - may provide significant performance improvements and represents an important competitive edge. From the strategic point of view, it is of fundamental importance to introduce an integrated approach to design, that is directly connected to the performance perceived by the end user. In the wake of a comprehensive performance analysis, in fact, modelling provides a tool which - calibrated on experimental data - allows the performance behaviour of the redesigned machine to be forecast with good approximation, only moving to the prototyping stage when and if the expected results are satisfying.
The approach described here is applicable to redesigning structural components of machine tools and using aluminium foam fillings, it is especially suited to moving parts: however, it may be successfully applied - using different materials - also to beds and other fixed or low speed moving parts. Its applicability may also be extended to other machine structures in steel or aluminium alloy, both with a view to increasing stifness (static or dynamic) and strength. In the latter cases, however, it is required to select different methods for performance evaluation.
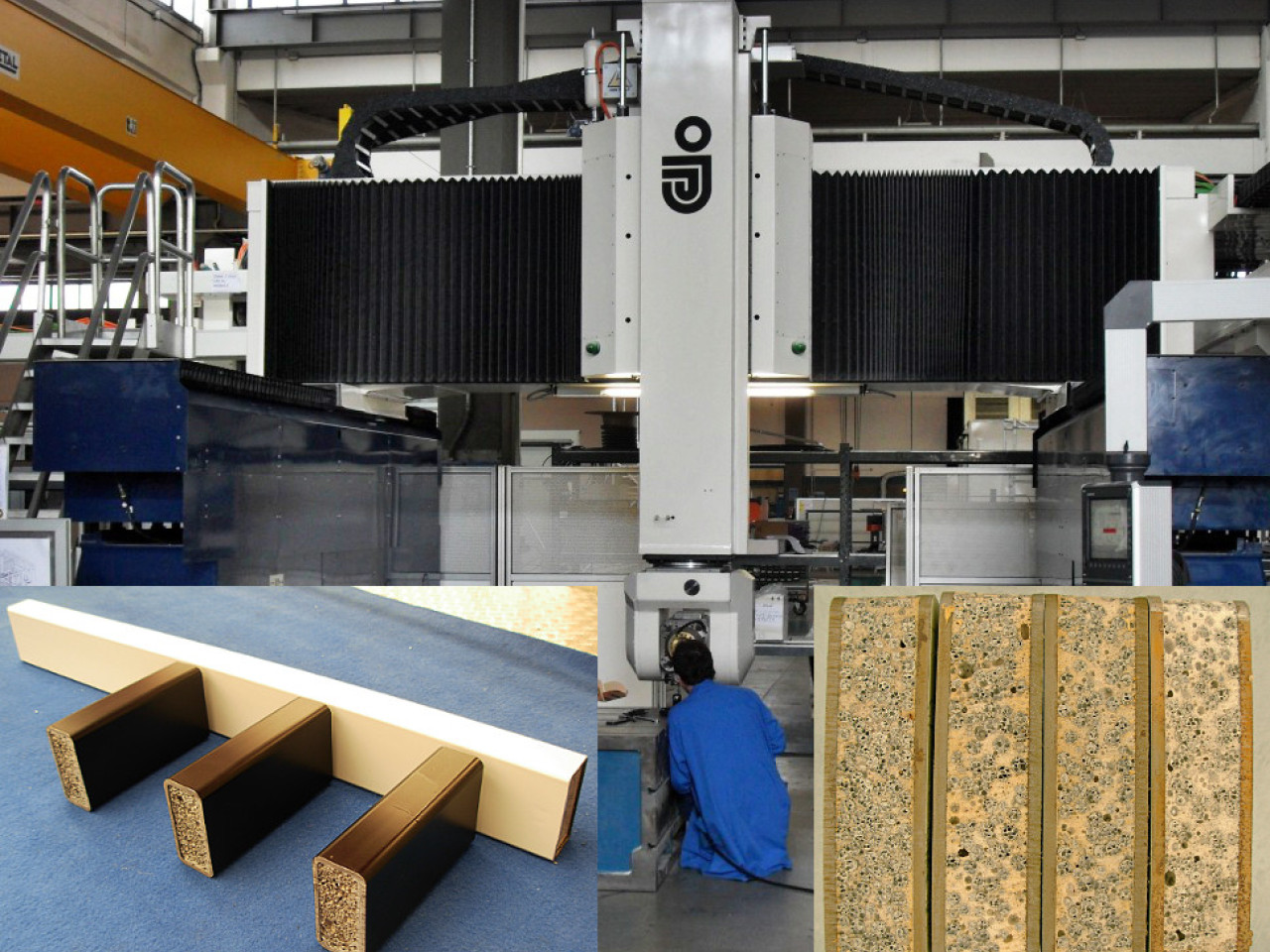
Improvement of the material removal rate of a machining centre
The method described here has been applied - in cooperation with JOBS s.p.a. - to redesign a component of the Linx Compact machining centre, especially designed for machining aluminium alloys and composites in the aerospace sector, which has 2200 mm x 3200 mm horizontal strokes and 1250 mm vertical stroke. During performance analysis, the company indicated the material removal rate on steel as the performance to be improved in order to widen the application field of this particular machine. After defining the objective function, the machine's performance has been measured by carrying out a set of machining tests to monitor cutting forces and a set of tracking tests with the grid encoder available to the laboratory. The machine's dynamic behaviour was then measured with experimental modal analysis, highlighting the ram as critical component. The component was thus redesigned with a new cross-section based on sandwich panels (with steel skins and core in hybrid aluminium-polymer foam) using optimal design and finite element analysis. The metal work was produced by JOBS, while the foam filling phase was carried out in the laboratory. Finally, the machine with the redesigned component was re-tested to assess its performance. The analysis of the machine tool's performance with the redesigned component highlighted a marked increase in the material removal rate on steel, achieving the pre-set objective and allowing the machine to broaden the range of successfully performed machining operations. A significant improvement in the accuracy of trajectory tracking was also detected. Finally, the analysis carried out showed the solution's feasibility from the economic point of view as well.
JOBS s.p.a. Politecnico di Milano
The outcome of the project led to applying the method to other products by the same company and to new service activities with other industrial partners.
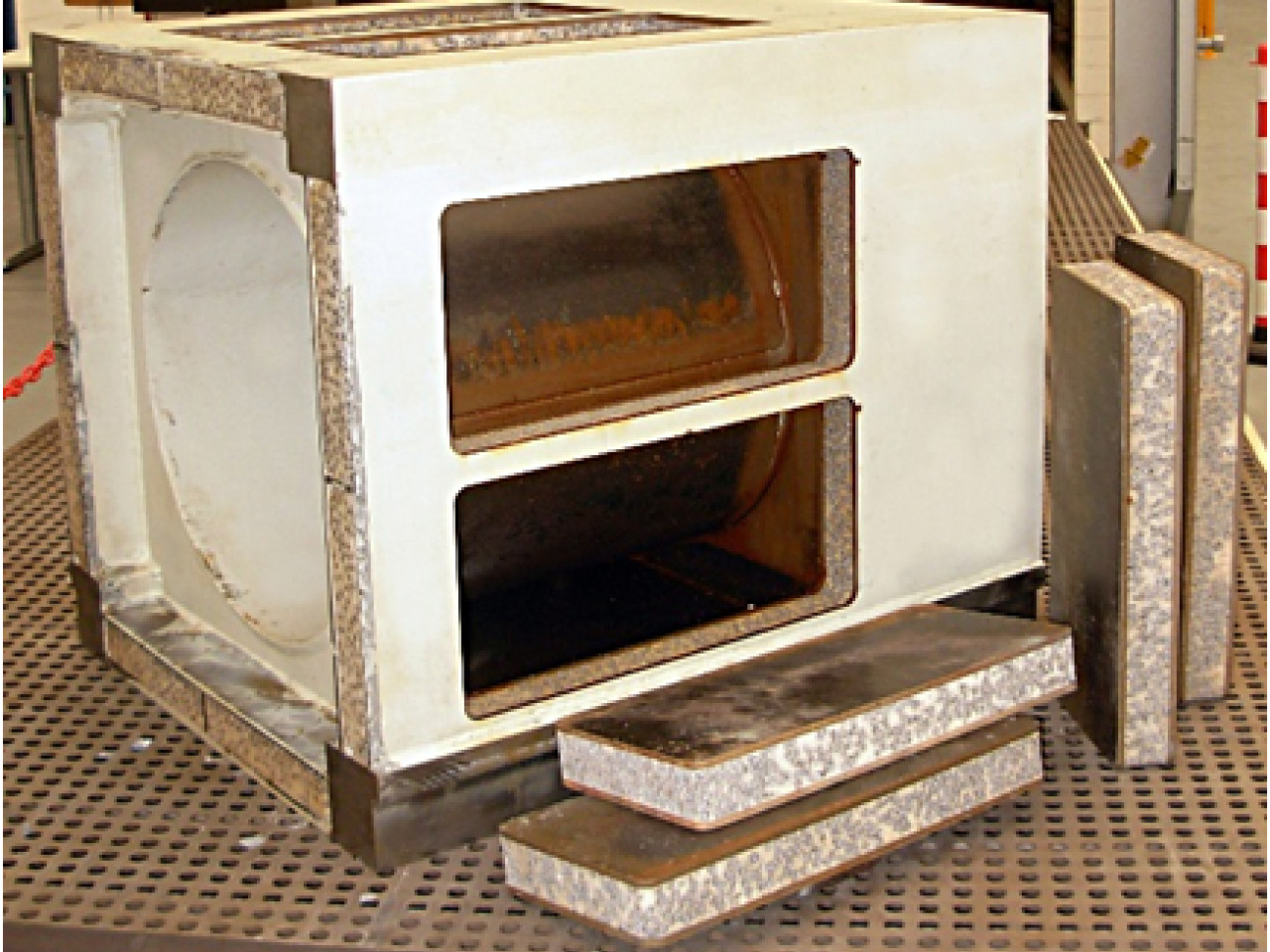