The project idea is based on the consideration that a significant part of energy losses in volumetric machines is due to friction between moving parts. The need to provide, especially at low speed, hydraulic lift for a correct lubrication is a primary cause to mechanical and volumetric losses. This is the cimbined effect of the contrasting needs to provide good lubrication and to keep the mechanical compliance between parts as low as possible. The project applied a nanostructured surface superhydrophobic functional layer to the slippers of an axial piston pump. Results obtained during the first two years of the project indicated a potential reduction in friction losses between 30 and 50%, especially in off-design working conditions.

The project exploits the well known "lotus effect" in order to make the slippers surface superoleophobic (contact angle approx 150°). This way the lubrication layer acts like a bearing at molecular scale, dramatically reducing the interface friction, thanks to the vitual elimination of the no-slip boundary layer. The ricduction in estimated friction factor achievable with this technology is between 20 and 30%, depending on the operating conditions. The fiunctionalization process does not require complex technology or the use of harmful materials. Its industrial cost is estimated to be in the range 1-5 Euro/m2.
Friction reduction in fluid power componets having parts in relative motion (slippers, swashplate, distribution plate, valve spools, cylinder rods)
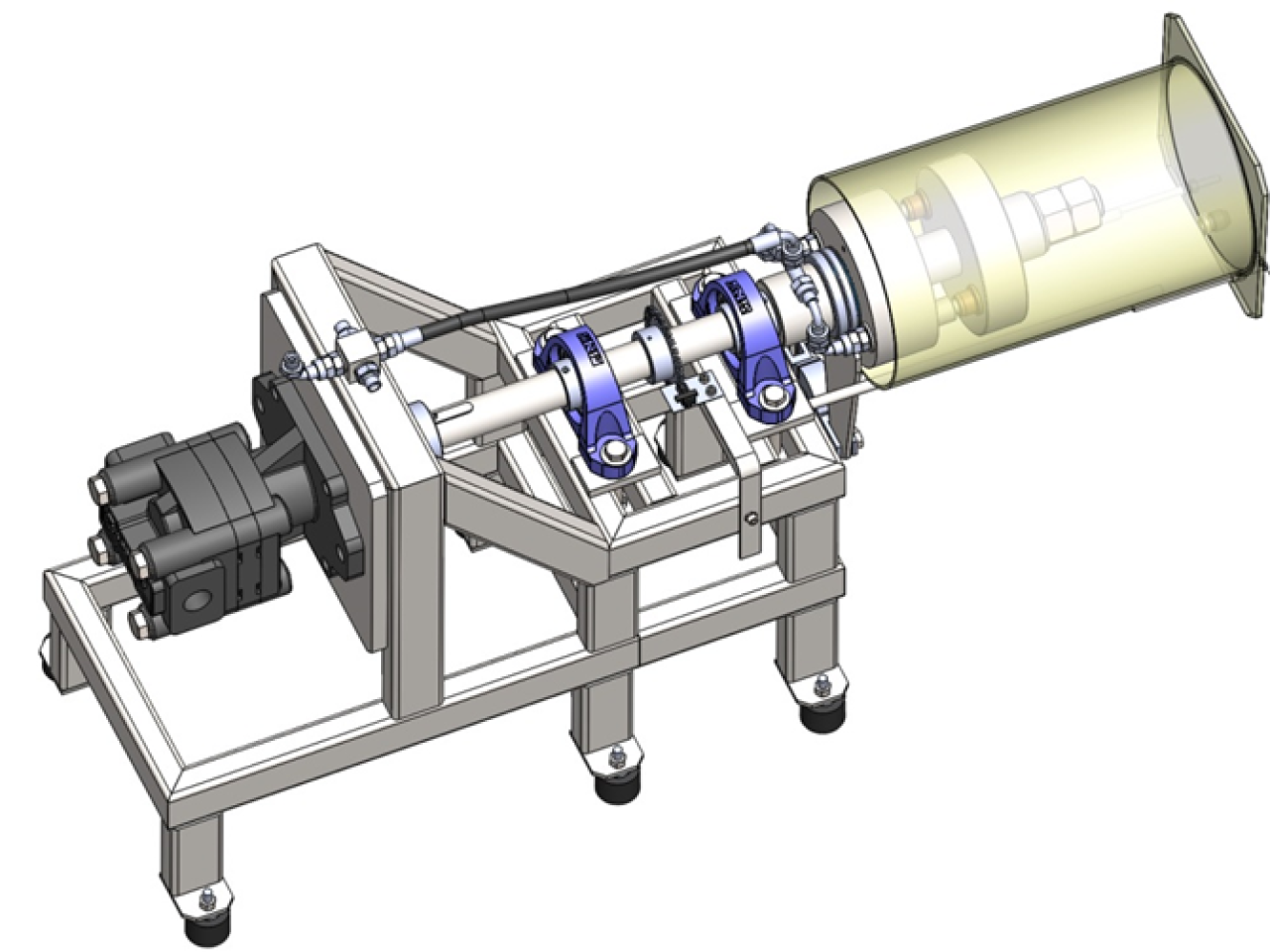
axial piston pump slippers
The superhydrophobic functional layer was applied to the lower surface of the slippers in an axial piston pump. The slipper must provide adequate lubrication in the relative motion between pistons and swashplate. Thanks to the application it was possible to achieve a significant reduction in the friction in operating points typical of a standard component, with a significant impact on the expected overall efficiency of the pump. Reduction in friction coefficient between 20 and 30%. Improvement in the mechanical wear resistance on the functional layer. Industrial feasibility of the functionalization process.
Istituto Macchine Agricole e Movimento Terra (IMAMOTER-CNR), Istituto per la sintesi e le tecnologie dei materiali ceramici (ISTEC-CNR), Istituto per l'eneregtica e le interfasi (IENI-CNR)
The project, entirely funded by the Italian Ministry for University and REsearch (MIUR), will progress with a tentative industrialization phase in cooperation with Bondioli&Pavesi group.
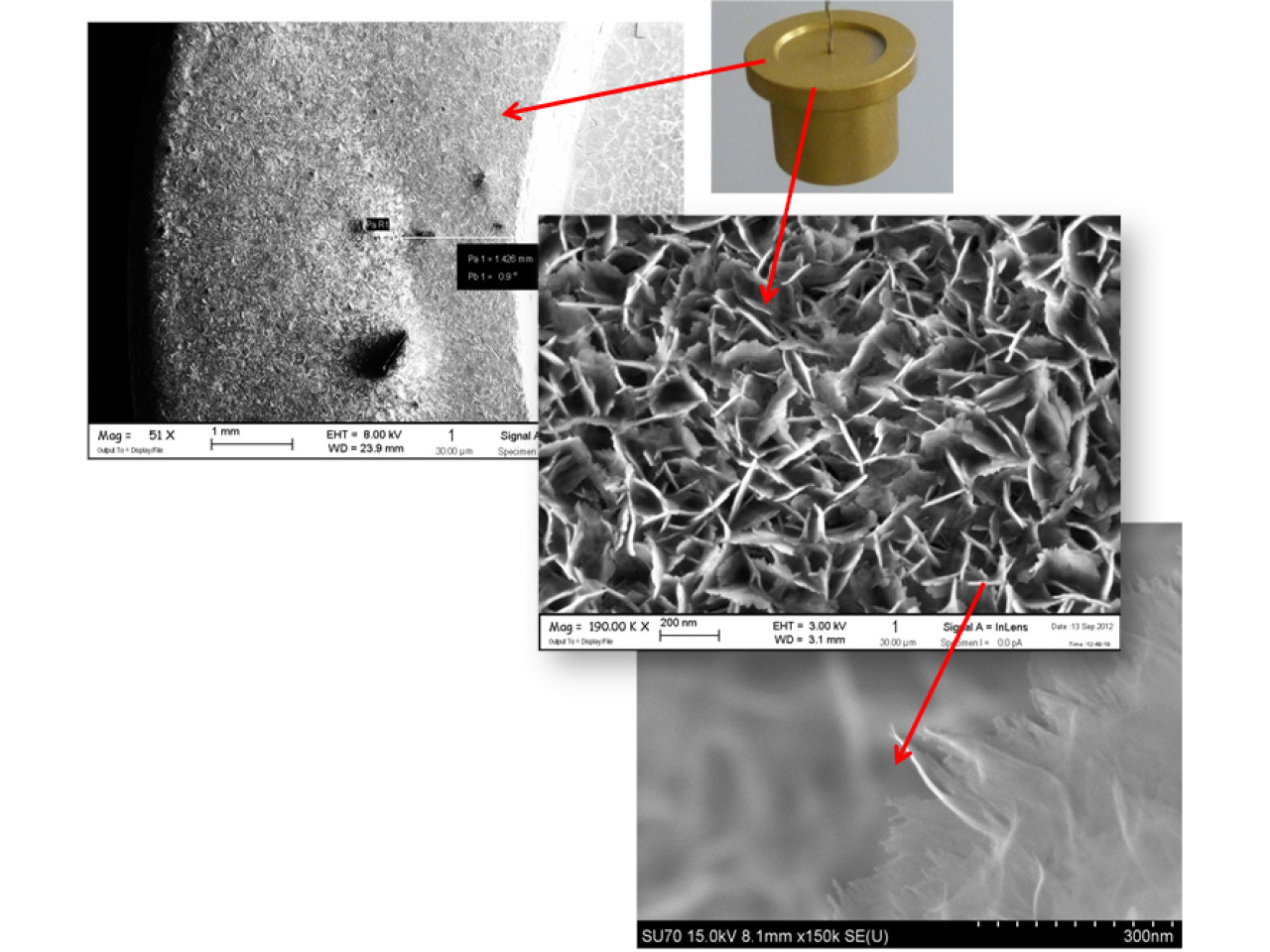