Additive manufacturing (AM) affords design freedom, topological optimization and ability to develop material/component combinations with “site-specific” properties. AM therefore is an effective tool to meet the growing needs of both high competitiveness (with reduced time to-market) and transition to circular economy, through the production of increasingly more durable and recyclable components.
However, the full potential of AM can only be exploited by the correct choice of materials and their functionalization through optimised heat treatments and/or surface treatments and coatings, which take into consideration the peculiar microstructures of additively manufactured materials.
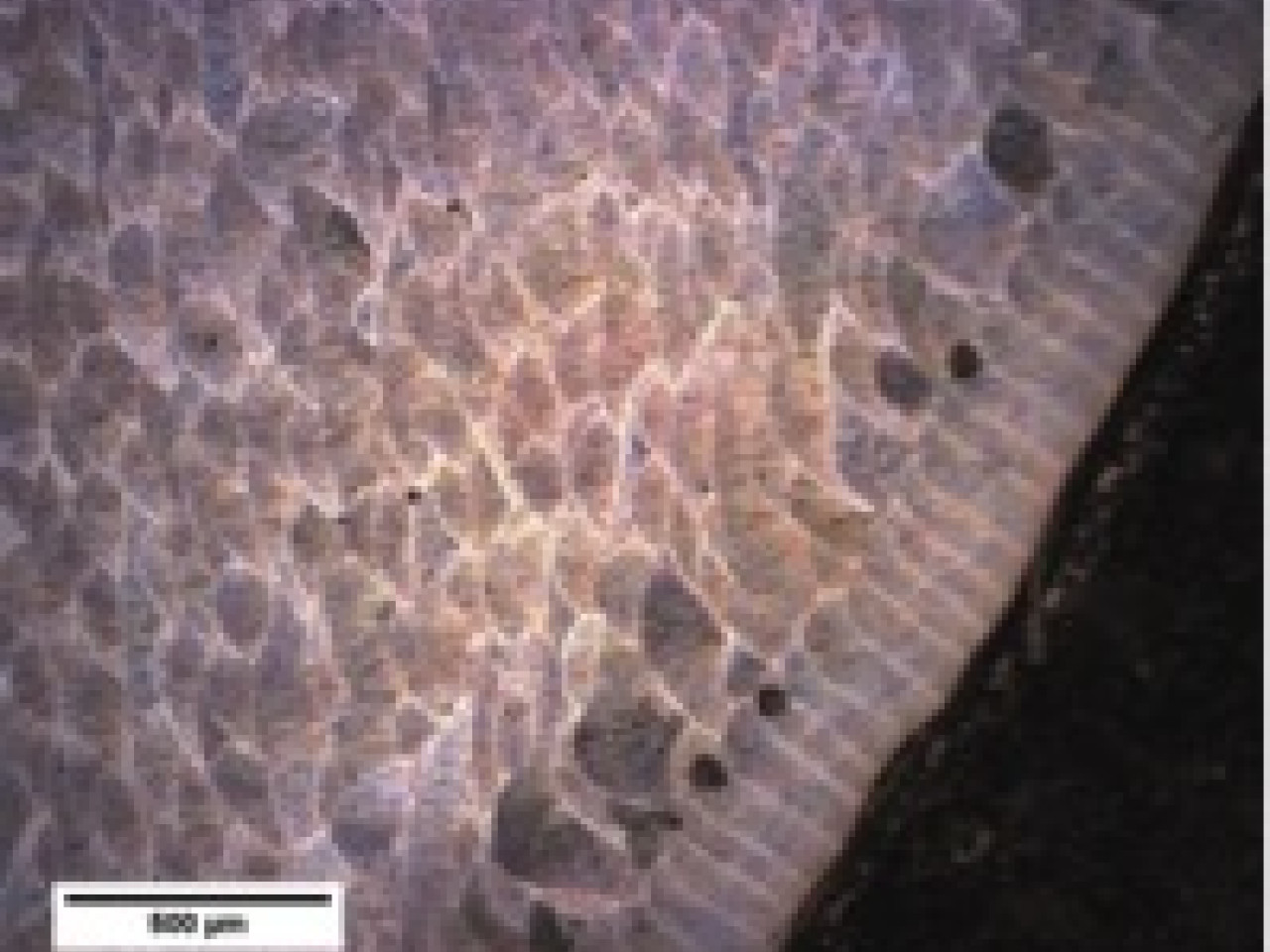
Our integrated approach allows to evaluate, on the basis of the component specifications, the most appropriate materials and coatings to be used, followed by optimization of AM process, coating and heat treatment parameters, with less time-consuming and more effective results than by a trial-and-error approach.
Optimization of heat treatment and surface treatments/coatings for AM components is a transversal issue to all industrial sectors in which there are mechanisms and components which, in addition to having to withstand static and dynamic stresses, are involved in tribological contacts. Through an in-depth study, it is possible to optimize the components involved, extending their service life or widening the range of applied stresses.
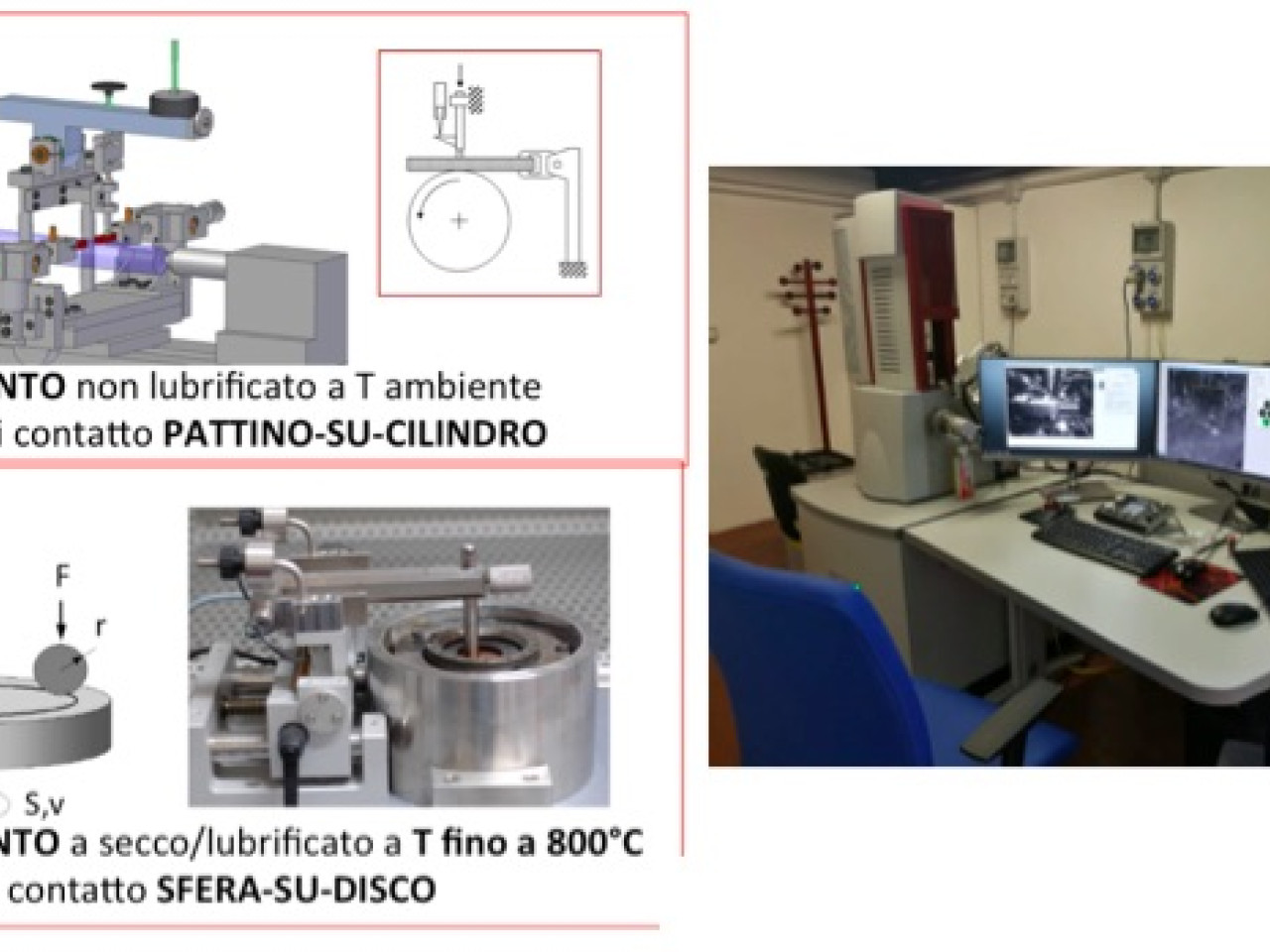
Optimization of heat treatment for the AlSi10 Mg alloy produced by Selective Laser Melting (SLM)
The above-described method was applied within the PORFESR - RIMMEL Project (https://rimmel.nano.cnr.it) for the optimization of heat treatment for the AlSi10Mg alloy produced by SLM, also in relation to the subsequent deposition of multifunctional coatings. The activity initially included the determination and comparison of the aging curves for the alloy both in the as-built conditions and after solubilization, followed by the mechanical characterization of the material. The solubilization conditions were determined by evaluating the effects of the treatment on the microstructure (in particular on the Si network surrounding Al-rich cells, as well as on the size of pores and defects).
CNR NANO S3
Istec CNR
UNIMORE-INTERMECH–MO.RE
Laboratorio Mechlav
BEAMIT Spa
Next Coating Srl
STS Srl
Optimization of the alloy heat treatment, so as to ensure a proper combination between mechanical strength and ductility of the material and to allow the subsequent deposition of PVD coatings.
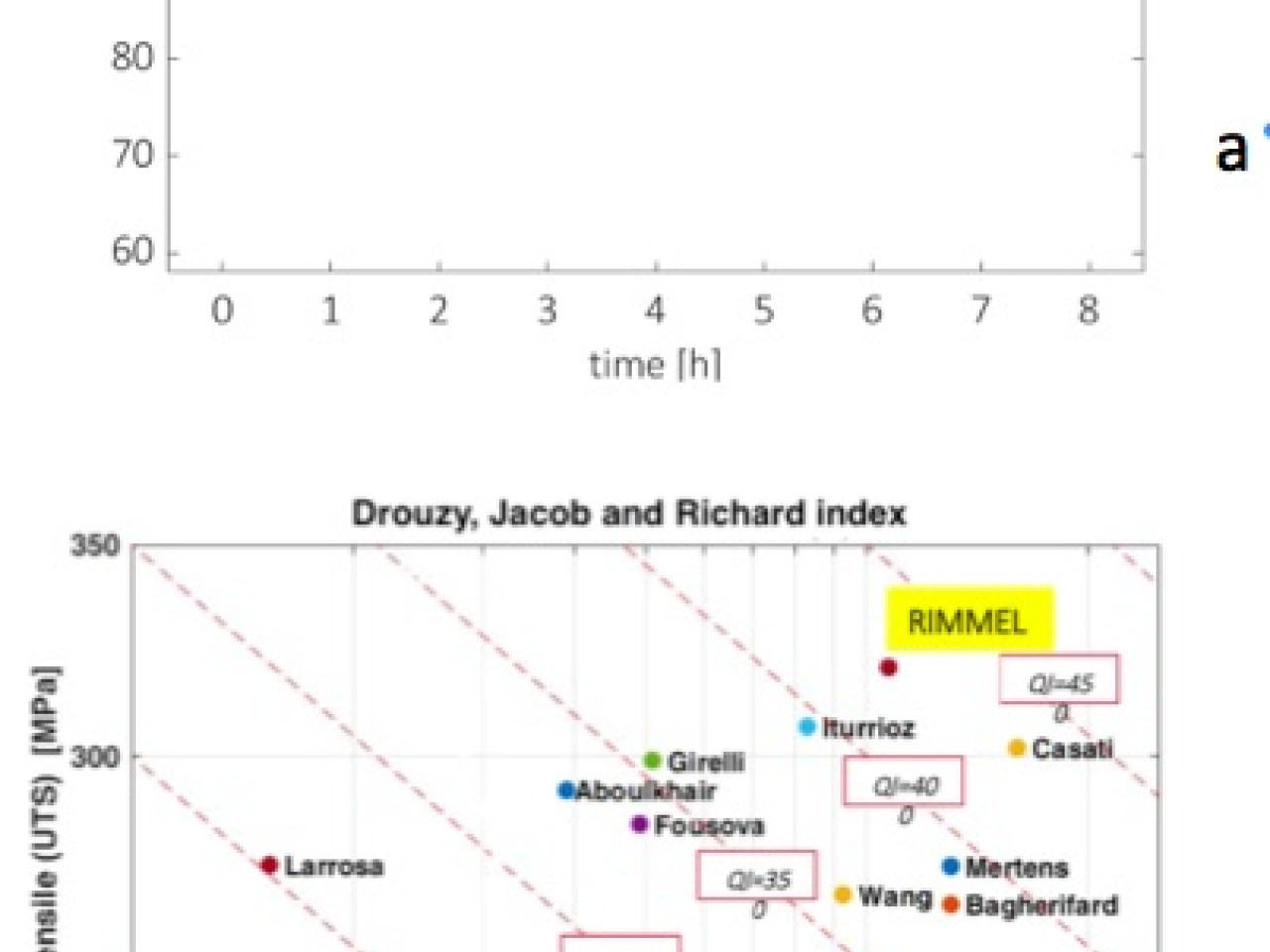