Engineering components, in relative motion under load, dissipate energy due to friction and and suffer surface damage due to wear. In order to limit these phenomena, a new discipline called “tribology” has been developed. The importance of a tribological approach may be evaluated considering that: • about 1/3 of energy production is dissipated due to friction; • a better use of available knowledge on tribological processes (both in the maintenance and in the design phase) allows saving between 1 and 4% GDP of an industrialised country, due to the improved efficiency and reliability of tribological systems. Tribology investigates the contacting bodies from a mechanical and chemical-physical point of view, integrating the most recent technological innovations for surface modification, in order to increase service life or to extend load ranges.
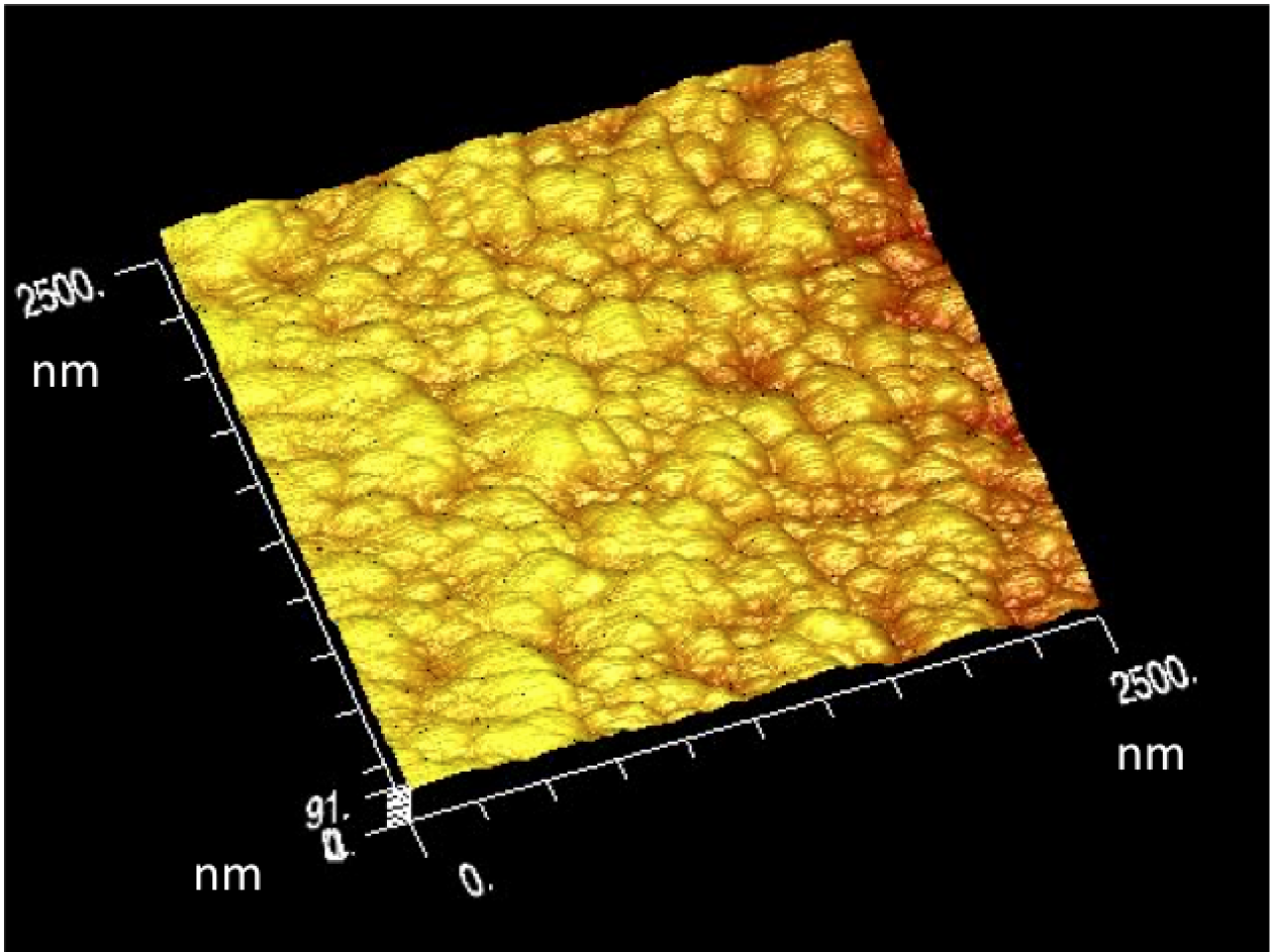
The integrated approach, typical of tribology, allows the complete identification of the factors that influence the response of the system in terms of friction and wear. Based on these data, it is possible to optimize the components involved, with higher efficiency and shortened time than in the conventional trial-and-error approach.
Many engineering components involve sliding motion (such as in automotive systems, bearings, cam - follower contacts, tools for metal cutting, guides (textile industry, food and packaging), disc-brake pads, molds and dies, drawing, extrusion, prosthetic joints ...). Through a complete tribological study it is possible to optimize the components involved, extending the service life or widening the range of applied stresses.
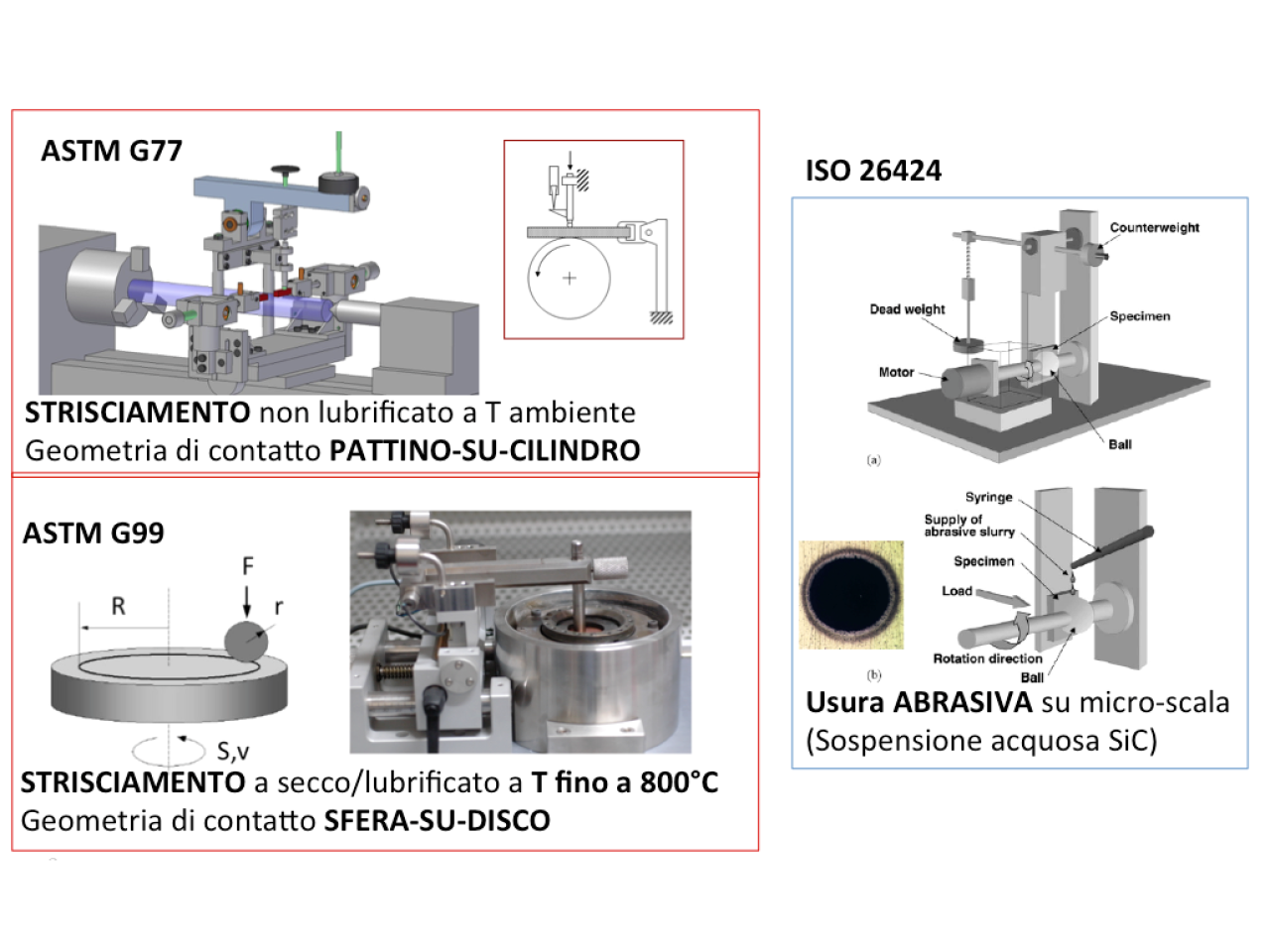
Stainless steel disk for distribution systems subjected to sliding motion
The investigated system includes a distribution disk (currently produced in austenitic stainless steel, coated with a medium thickness metal layer), subjected to discontinuous sliding in the absence of lubrication against another austenitic stainless steel. The contact type is a non-conformal line contact. The prevailing wear mechanisms, identified by failure analysis on real components are (i) adhesive wear of the counterfacing steel, (ii) mild tribe-oxidative wear of the coating on the distribution disk, with moderate tendency to brittle fracture. The ultimate goal is the identification of alternative materials and/or surface treatments, in view of a improvement of system performance. Identification of an innovative thermochemical treatment as an alternative to the metallic coating currently employed
Packaging company
Activities similar to that exemplified here were carried out in collaboration with several companies in the area, leading to the identification of the main tribological parameters and/or the development of alternative solutions to those currently used, in order to improve the performance of tribological systems under investigation. The service is provided in the form of research or consultancy contracts.
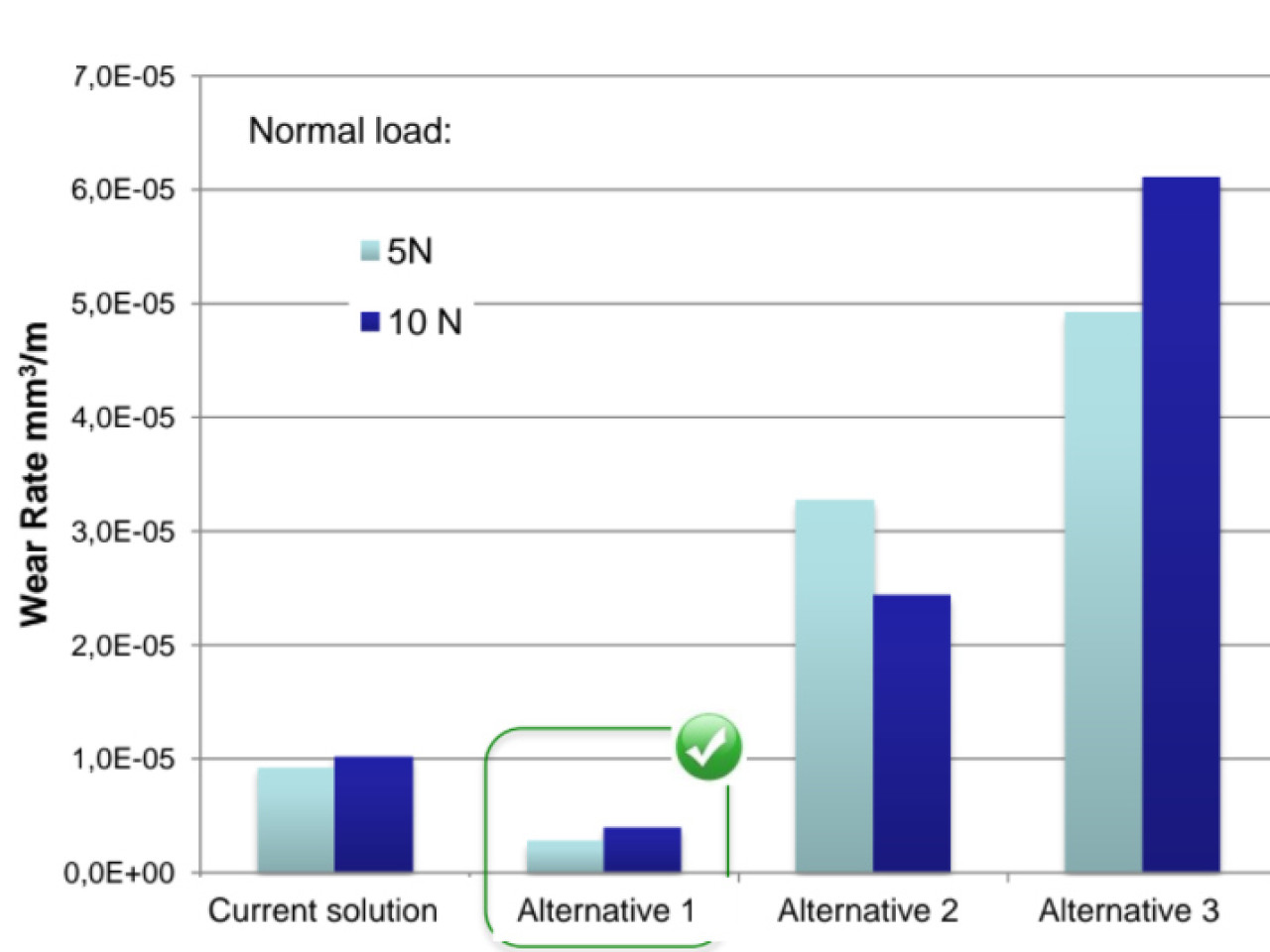