The new method makes it possible to reconstruct hollow shapes, namely the inner surface of a prosthetic socket, starting from the images photographed from various viewpoints using a common camera. The software allows a three-dimensional model to be generated, in a file format commonly used by numerical control machines to make the final product. A new quick and practical approach, which does not require special expertise and training by the operator, versatile and easy to use. Most currently marketed acquisition and Reverse Engineering systems, designed to survey outer surfaces, although compact in size (30-50 cm) are not however very convenient for hollow and deformed geometries. Using a compact sized or miniaturised device (e.g. camera) effectively addresses the problem.
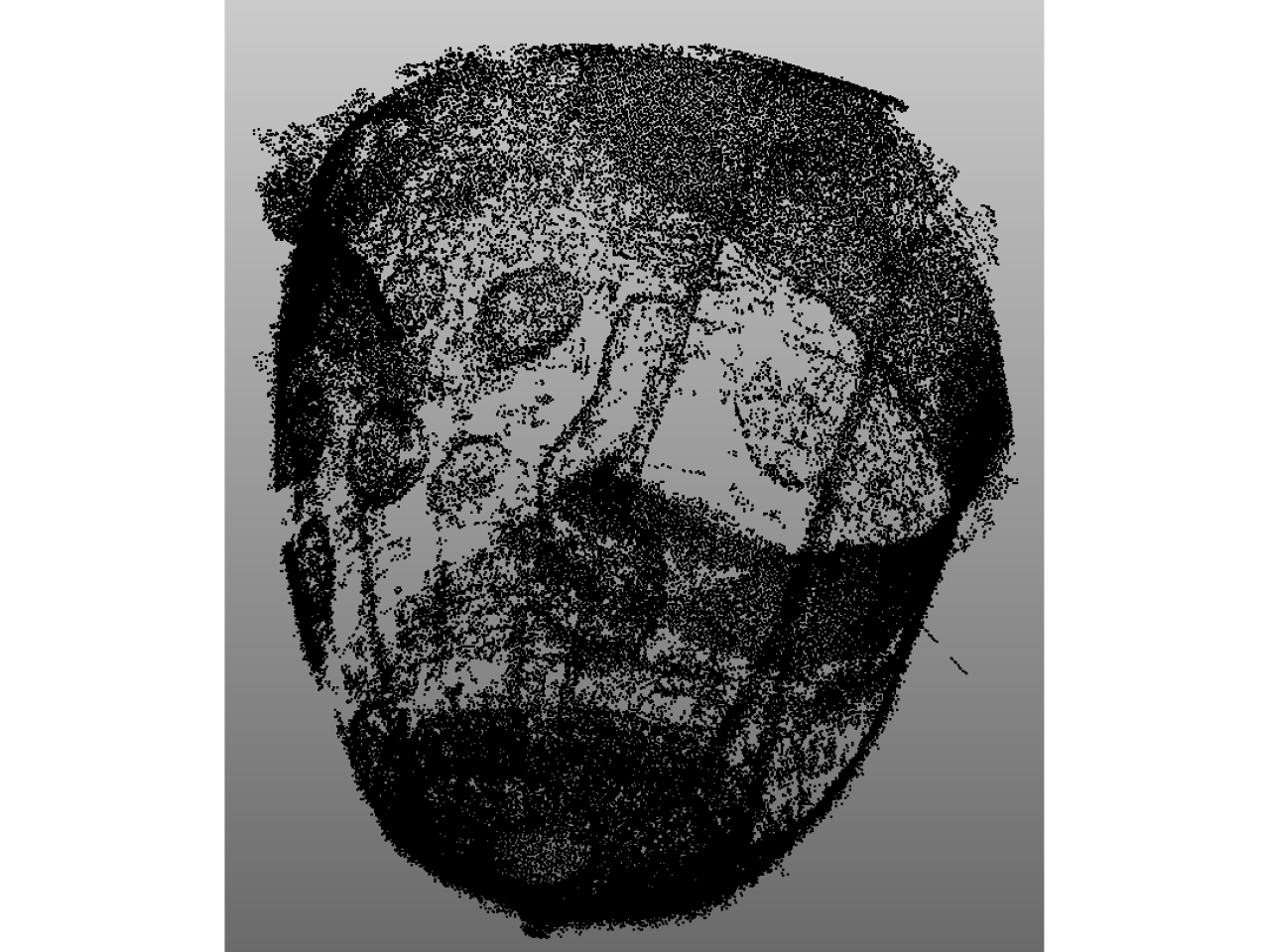
Reproducing a socket quickly makes it possible to reduce the timing and costs of the production chain in the event of renewed supply to a limb amputee. In this case, since it is not required to create a product from scratch, it is sufficient to "copy" the socket already customised on the patient, avoiding to reconstruct it with the traditional method.
The ability to acquire complex geometries and to reach small areas is the strong point of this integrated system. Therefore, in addition to acquiring and reproducing standard objects, like other tools, it is particularly suited to reconstructing hollow objects or which include difficult to reach areas (e.g. prosthetic sockets).
Replica of a prosthetic limb socket
Should you wish to replicate an existing socket, already customised and adapted to the patient following the normal procedure, you would need to take the measurements of the stump by hand again, create a negative mould, then a positive one in plaster and finally, from the latter, reconstruct the provisional socket geometry, which will then undergo adaptations and modifications to achieve the final product. Through the acquisition of detailed, high resolution images one may significantly shorten the duration of the previous operation, reducing most of the productive chain, since the three-dimensional model - from which the item is easily produced with modern technologies - may be created directly. Specifically, using at least thirty pictures of the socket, the software recognises the zones thanks to natural and/or artificial patterns, then processes the shared points in the various pictures and calculates the depth of each in space. The whole of these points forms a cloud - in the jargon - from which the 3D surface is obtained, i.e. the socket surface. After the 3D model has been obtained, it may also be modified at will with the various types of Reverse Engineering software, to achieve the desired shape based on the stump's anatomical shape. In the event you should not wish to make any changes, the file is already 3D-printing ready.
3DFLOW srl (VR)
As well as being used to replicate sockets, the methods may be extended to Reverse Engineering of other items whose geometries are difficult to acquire with traditional techniques. Furthermore, direct entry into the orthopaedic market is planned, with the aim of supplying orthopaedic workshops which may wish to implement the new technique to reduce their production timing and consumption.
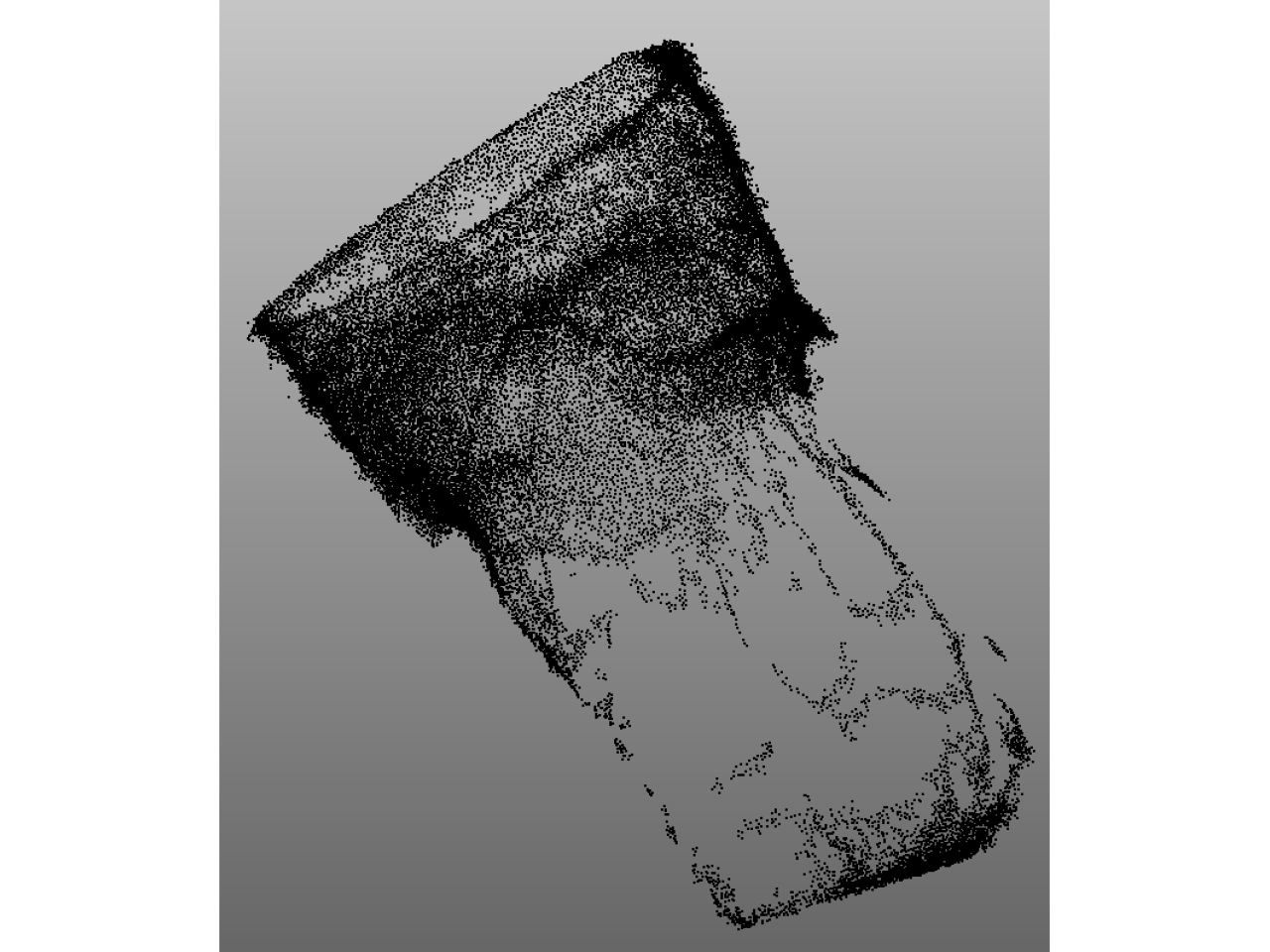