Spiral Bevel Gears (SBGs) play a significant role in transferring power between non-parallel shafts. Thanks to the high contact ratio, SBGs are smooth, quiet, and have the ability to bear high levels of torque and power; although, their complex geometry requires recognizing the parameters which affect the transmission vibration, efficiency and durability. Vibration is one of the main issues since it affects the stress distribution, contact pressure, and the fatigue life of a geartrain. Several parameters, such as the time-varying mesh stiffness and the gear mesh transmission error, exert a prominent influence on vibrations and these are some of the sources of driveline noise. Therefore, Mesh Stiffness (MS) and Transmission Error (TE) are the two key parameters, which can be calculated through the loaded tooth contact analysis (LTCA) using different methods, e.g., finite element method (FEM), experiments or analytical formulae. In the last decade, different software packages have been released for the LTCA. These software employ FEM, standards (for instance, ISO), or both methods to extract MS/TE for different gear sets.
Dynamic analyses and nonlinear phenomena are still an issue for commercial software; therefore, this is the application field of our products/methods.
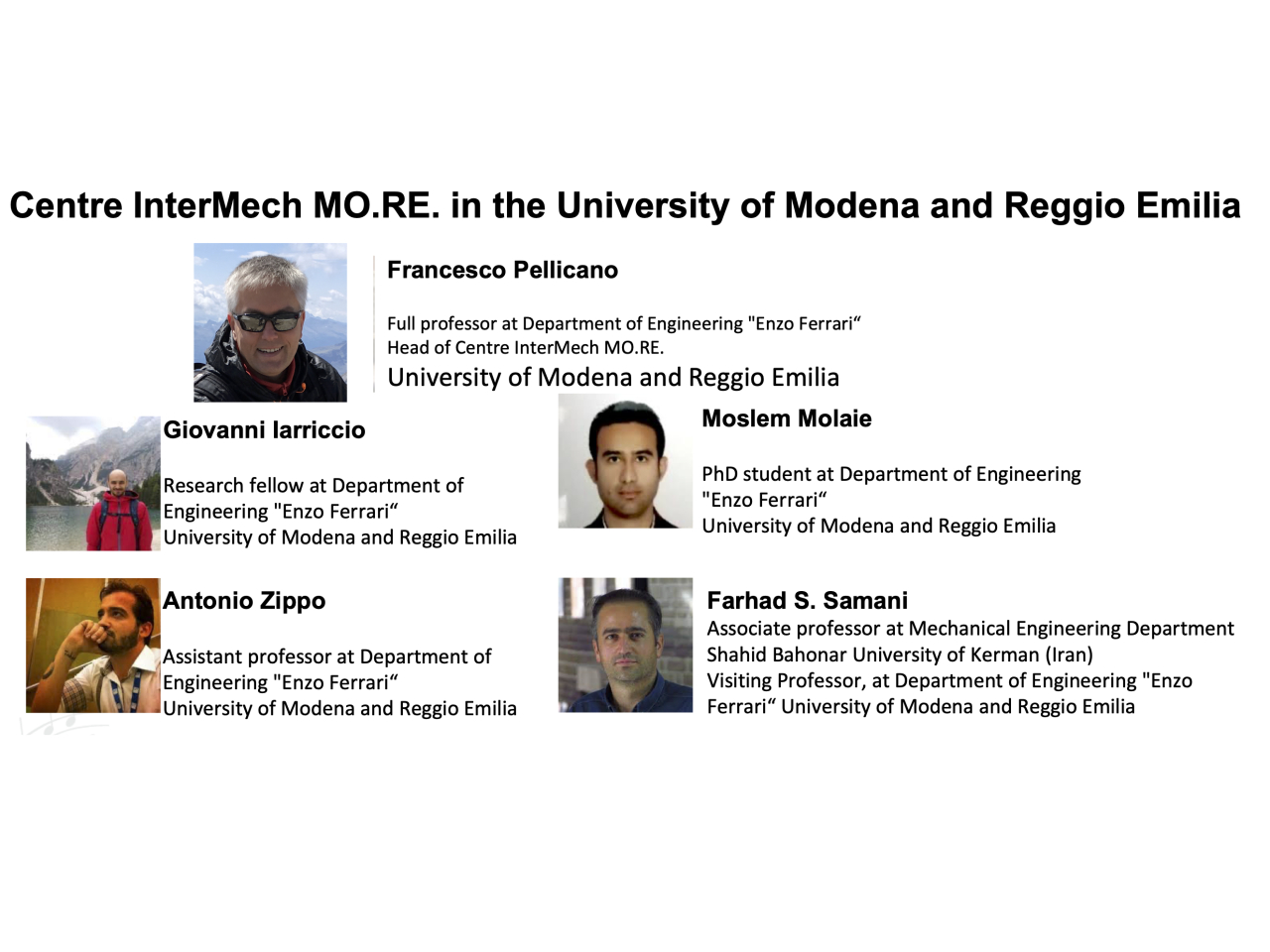
The product consists of a combination of numerical methodologies allowing to predict the vibrational properties of gearboxes and allowing the customers to optimize their gearboxes toward mitigation of the mechanical noise. The calculation protocols include an intensive usage of nonlinear finite elements, combined with ISO/AGMA standard based procedures, followed by in-house software for vibration analysis/prediction.
The typical users of our applications are highly skilled designers, specialized in gear design, operating in the fields: Aerospace (geared turbofan, helicopters), Automotive, Heavy Industry.
The present technology includes novel approaches for the dynamic analysis of gearboxes: dynamically loaded tooth contact analysis; imbalance due to nonlinearities; full dynamic scenario investigation.
At the present no commercial software are able to carry out fully nonlinear dynamic analyses and optimizations, the limitations of the actual commercial technologies limit the designers to static analyses. However, the new challenges of industries, for example, electric vehicles, ask for more and more efficient, lightweight, and silent gearboxes.
Aerospace. Geared turbofan: the turbine is connected to the fan (first stage) through a geartrain. Helicopters: the turbine (up to 20.000rpm) furnishes power to the main rotor (a few hundred rpm) through a complex geartrain. Reliability is the major designer concern, mechanical noise is an important element for commercial flights.
Automotive, green transition, electric transition. Electric motors are inherently silent, therefore, the unpleasant mechanical noise produced by gears is no more masked by the beautiful sound of ICE. On the other hand, elimination of gearboxes through direct drives is a chimere and all designers are going to use light and high-speed electric motors. This requires new silent, lightweight and durable gearboxes.
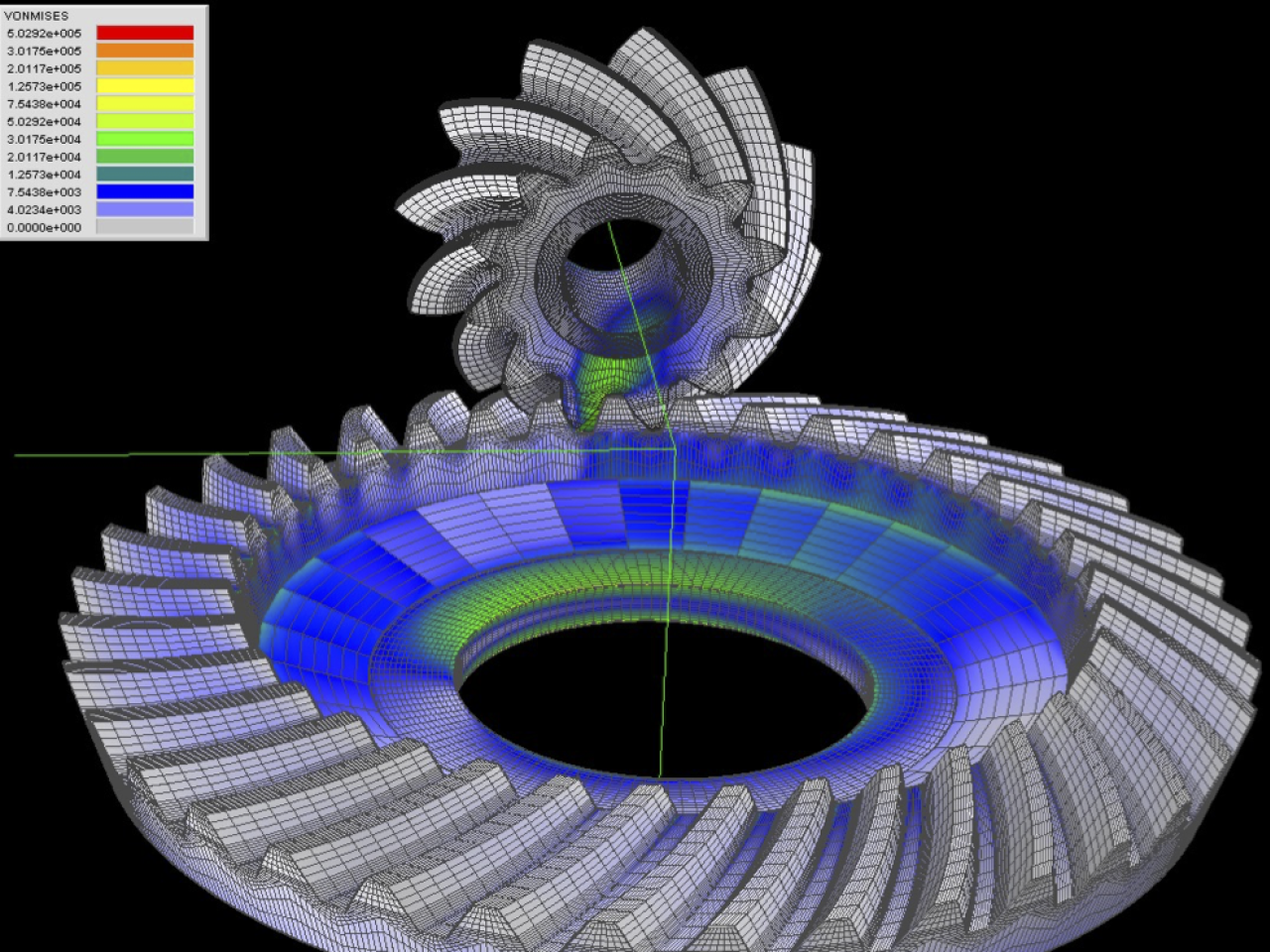
The main goal of the application example was to calculate the mesh stiffness by LTCA and the vibrations of an aerospace spiral bevel gear. For this purpose, two powerful software, which is based on FEM, are used to calculate the mesh stiffness with a possible high accuracy. After achieving the mesh stiffness, the vibrations produced by the spiral gear pair under different situations such as operating in presence of misalignments or tip/root modifications are analyzed.
The output of this application example is a significant step for understanding the behavior of an actual SBG aerospace system. The influence of several parameters such as misalignment, tip/root modification, and crowning, has been clarified.
Main softwarehouse
Cooperation with softwarehouse.
Publications on technical journals (forthcoming): Tecniche nuove, Organi di trasmissione
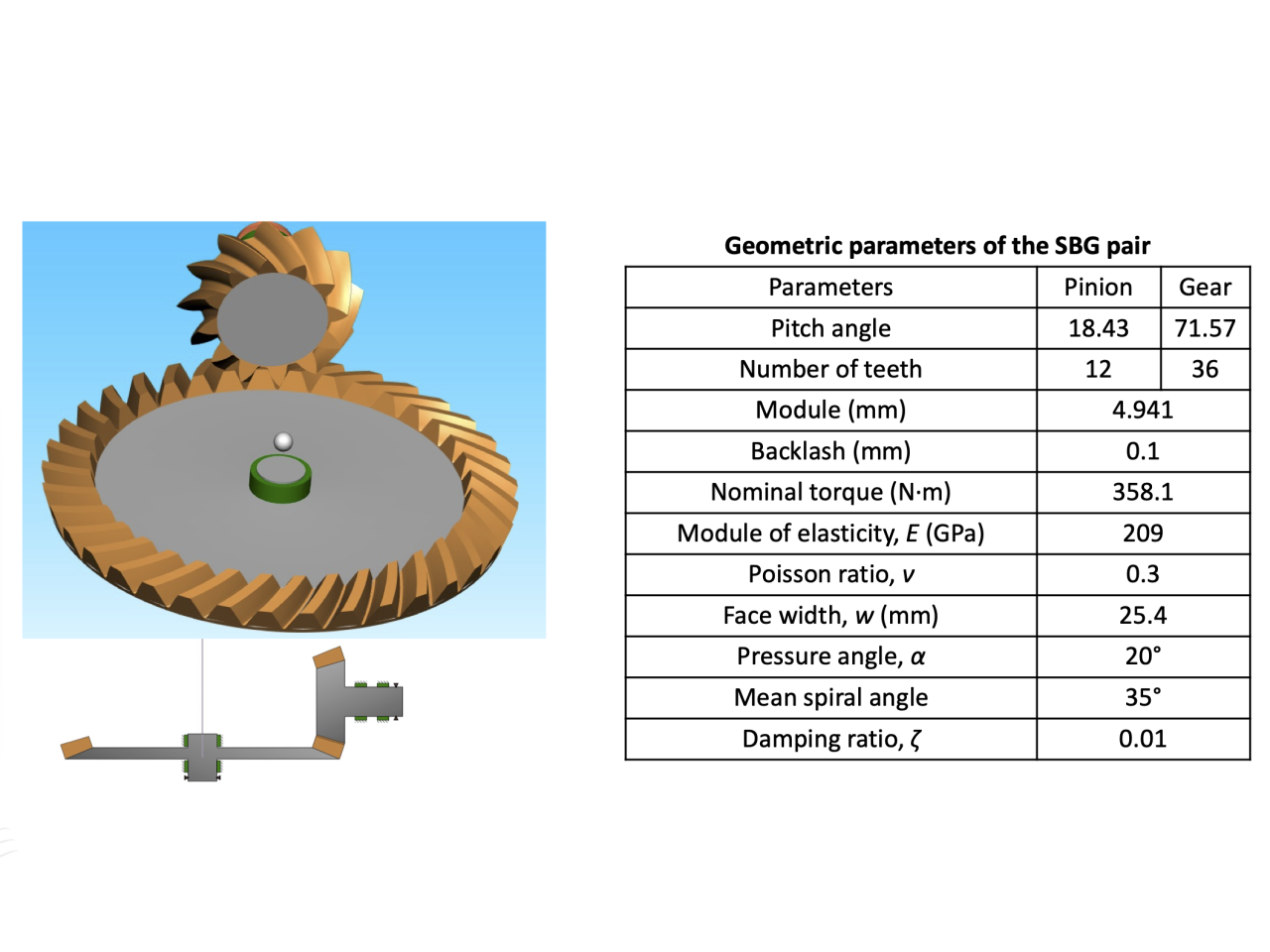