This activity illustrates the design of a tubular synchronous reluctance linear motor, which mover is made by metal additive manufacturing. Tubular motors are used in industry for several advantages: zero radial force, direct linear motion (more speed and precision), reliability and low maintenance costs. To date, the most studied tubular topology is the permanent-magnet configuration due to its high force densities and dynamic performance; however, magnets imply several disadvantages: high cost, low availability and low sustainability. For this reason, synchronous reluctance motors have attracted the interest of industry.
Tubular reluctance geometry is difficult to produce with classical techniques, especially if the geometry of the flux barriers needs to be refined to increase torque. The degrees of freedom of additive manufacturing would help improve the design of flux barriers to maximize the generated torque.
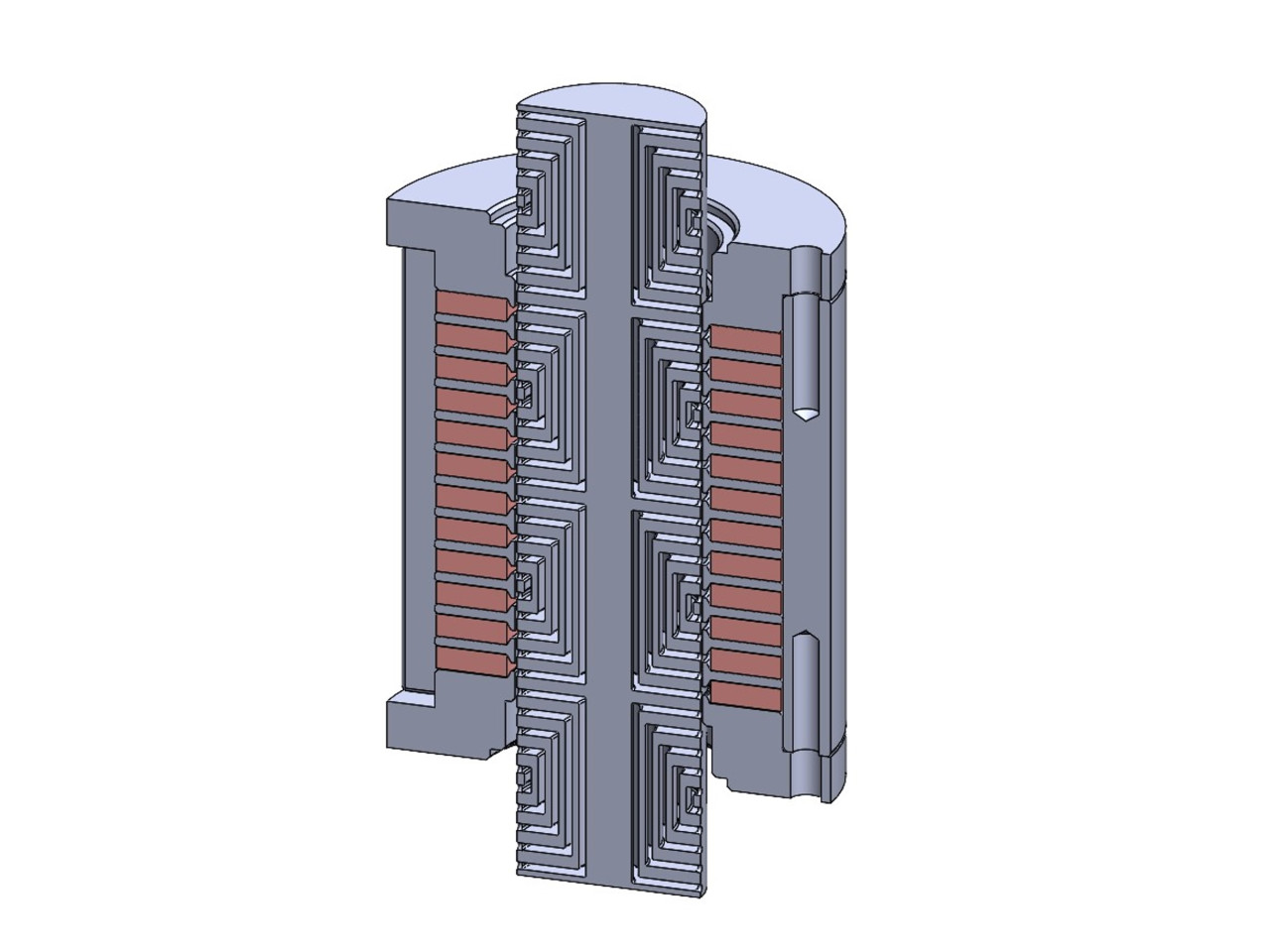
Initially, a theoretical study was carried out to optimize the shape and the number of barriers for the tubular geometry. A lumped-parameter analytical model was devised for an estimate of the performance based on the analyzed geometry.
Subsequently, 2D finite element simulations were performed; in fact, the tubular geometry can be represented as an axisymmetric 2D problem. From these simulations it was possible to further optimize the geometry by trying to minimize the ripple of the generated force.
In the end, an optimized geometry of the tubular motor’s mover was obtained, capable of providing acceptable performance, considering the fact that the rare-earths were completely removed. This geometry can be manufactured through innovative production techniques such as additive manufacturing which allows for infinite degrees of freedom in the design phase, therefore extensive optimization of the geometries with the aim of maximizing performance. Thanks to the additive manufacturing process it is possible to manufacture the designed complex geometry; furthermore, a production process is more sustainable, since it does not produce waste.
The innovative aspects of the proposed solution are the use of additive manufacturing for the mover and, consequently, the optimization of the design of the mover geometry. Generally, these types of motors use permanent-magnets due to the difficulty in the manufacturing process with traditional techniques. Thanks to additive manufacturing it is possible to overcome this limitation and design an optimized geometry for a synchronous reluctance linear tubular motor. There are also several advantages from a sustainability point of view, since the use of rare-earths is avoided and additive printing is an almost waste-free production process.
The designed motor can be used in various industrial applications where a linear actuator is needed and where space constraints are particularly stringent. In this way it is in fact possible to directly obtain linear motion without the need for additional mechanical parts.

Linear actuator for applications in the medical, aerospace or military fields where the use of magnets is not permitted or is severely limited.
The linear actuator can be used in industries such as aerospace and military. Generally, magnets are often considered unreliable as they are subject to demagnetization phenomena. Thus, reluctance actuators thus constitute an excellent sustainable solution for such applications.
Furthermore, additive manufacturing is still a fairly expensive technology, so highly specialized sectors requiring tailor-made designs such as these are, at the moment, among the few that can afford processing with such a level of precision and freedom.
Raw Power S.R.L e M4P material solutions GmbH
- Partners to explore topics such as:
- characterization of metal powders for magnetic circuits;
- study of how additive manufacturing processes influence the magnetic properties of materials;
- improve the manufacturing techniques of iron-silicon powders;
- Search for potential end users to orient the design towards industrialization of the product.
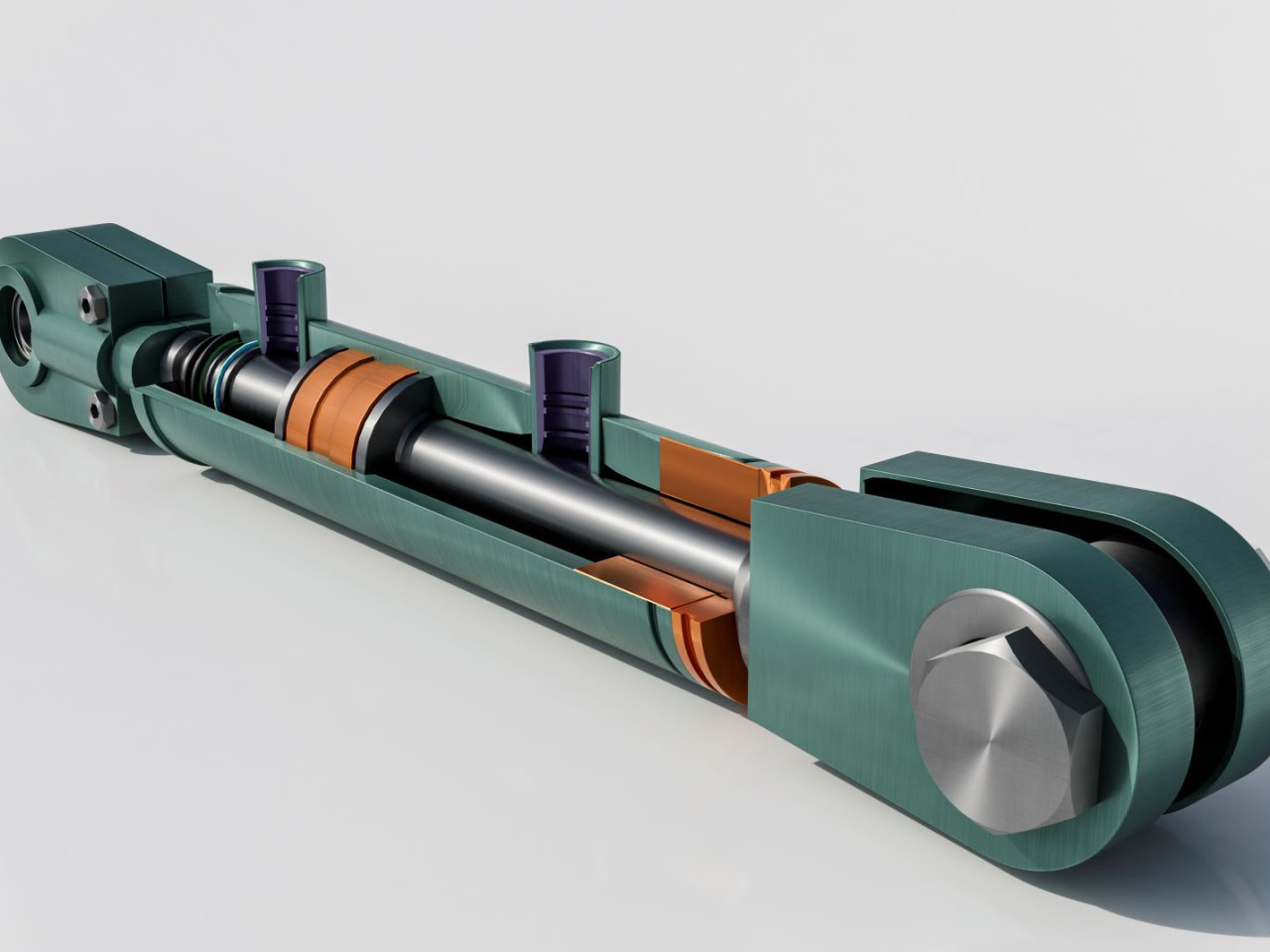