Three-dimensional reconstruction of the surrounding environment is needed in a number of industrial sectors: from access control to Automatic Guided Vehicles for goods handling. 3DV is a product which stems from VisLab's many years of experience in developing intelligent vehicles; it is a system based on the use of two video cameras able to provide an accurate three-dimensional reconstruction of the observed scene. The system also provides a real time interpretation of the environment, identifying existing obstacles and supplying an accurate reconstruction of the surface of the terrain.
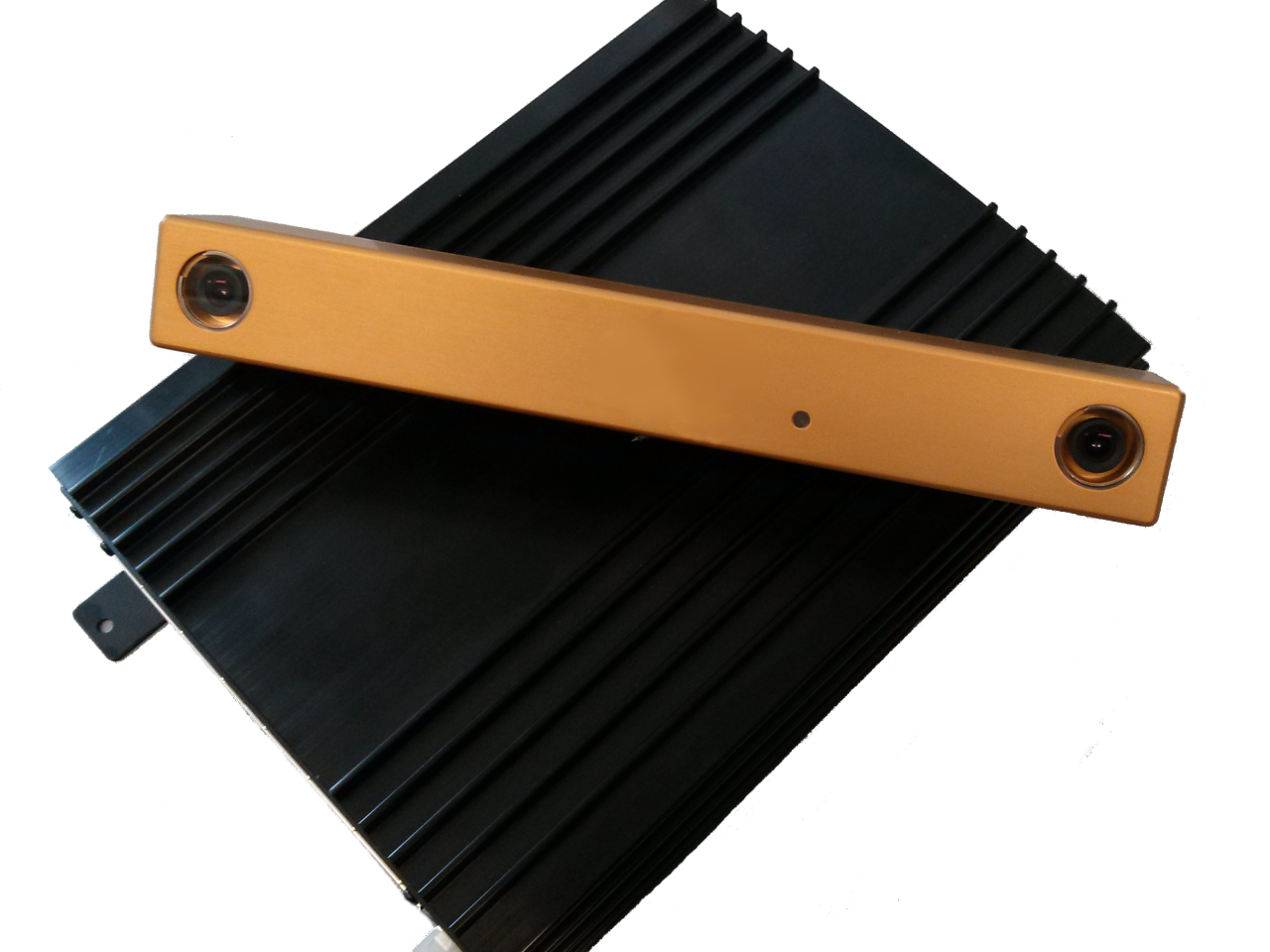
The system is able to perform real time three-dimensional reconstruction, using a passive sensor such as the video camera, using an algorithm for processing stereoscopic images which is state of the art in research. Furthermore, 3DV supports simultaneous reconstruction of 480 levels, producing up to 3 million 3D points per second, markedly higher than normal single plane industrial laser scanners
This product may be applied in all sectors where perception of the surrounding environment is required: it may be used as a perceptual system in autonomous vehicles as demonstrated in the PROUD test 2013, in Unmanned Aerial Vehicles or in industrial applications such as video surveillance to establish the flow of people in a particular access.
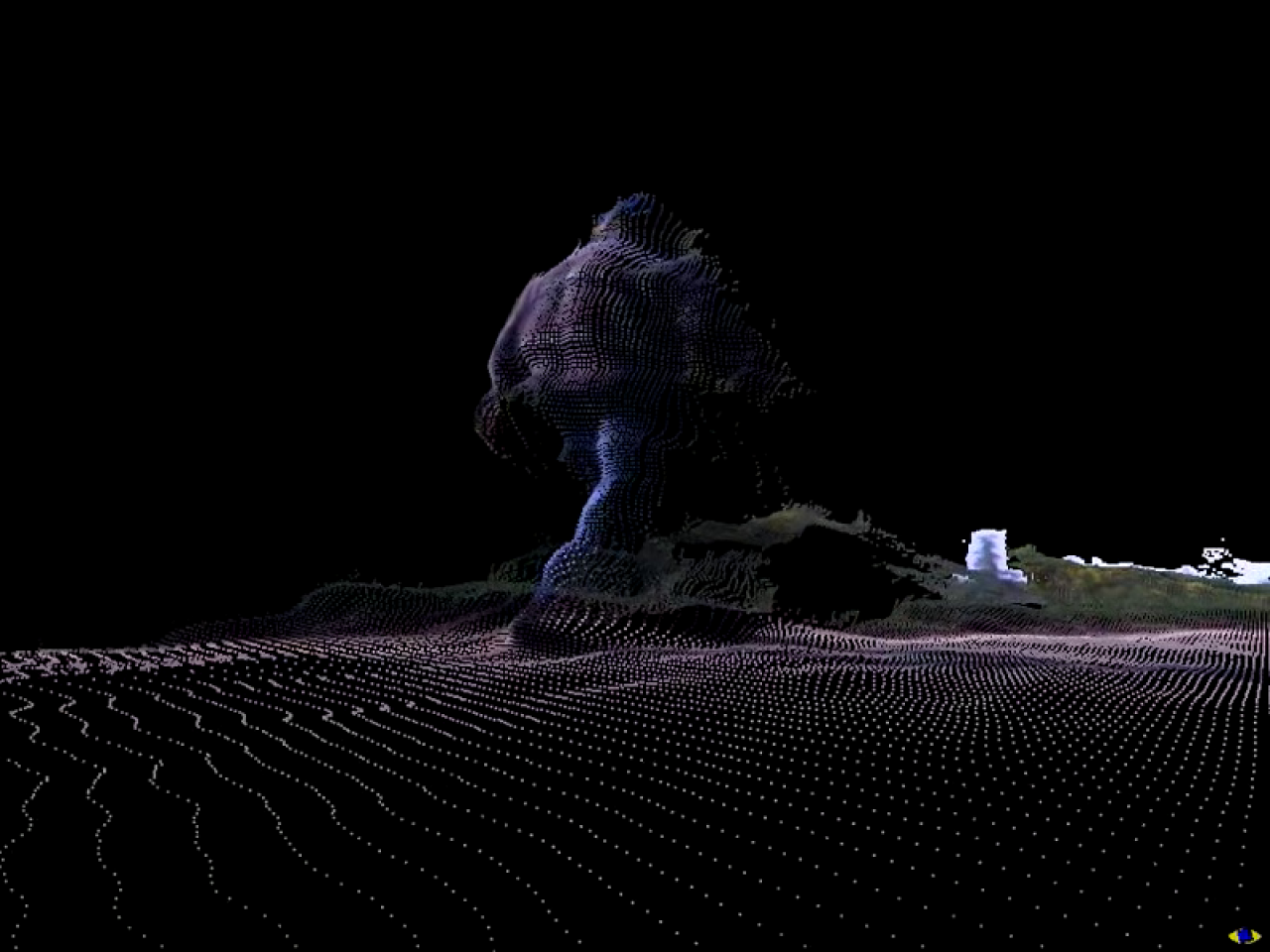
Perception system for AGVs
AGVs are automatically guided vehicles mainly used in the industrial field to handle products inside or outside a production facility. These vehicles typically use various laser scanners as sensors to perceive the surrounding environment. Using the 3DV application in place of the laser scanners offers a number of advantages in terms of cost, reliability and functionality. First and foremost, the use of a passive sensor such as video cameras means there are no moving parts, thus reducing system wear, as well as affording reliable semantic interpretation of the observed scene, such as the identification of certain objects or people. The system is simultaneously able to reconstruct 480 levels and this makes it possible to identify any suspended loads, which cannot be identified with a single plane laser scanner The system developed is able to provide to Automatic Guided Vehicles accurate perception of the surrounding environment, identifying both static and dynamic obstacles. In developing this application, we have aimed at covering issues which are hard to be solved with traditional perception systems, such as identifying suspended loads.
Elettric80
The system has been tested in various facilities managed by Elettric80 spa.
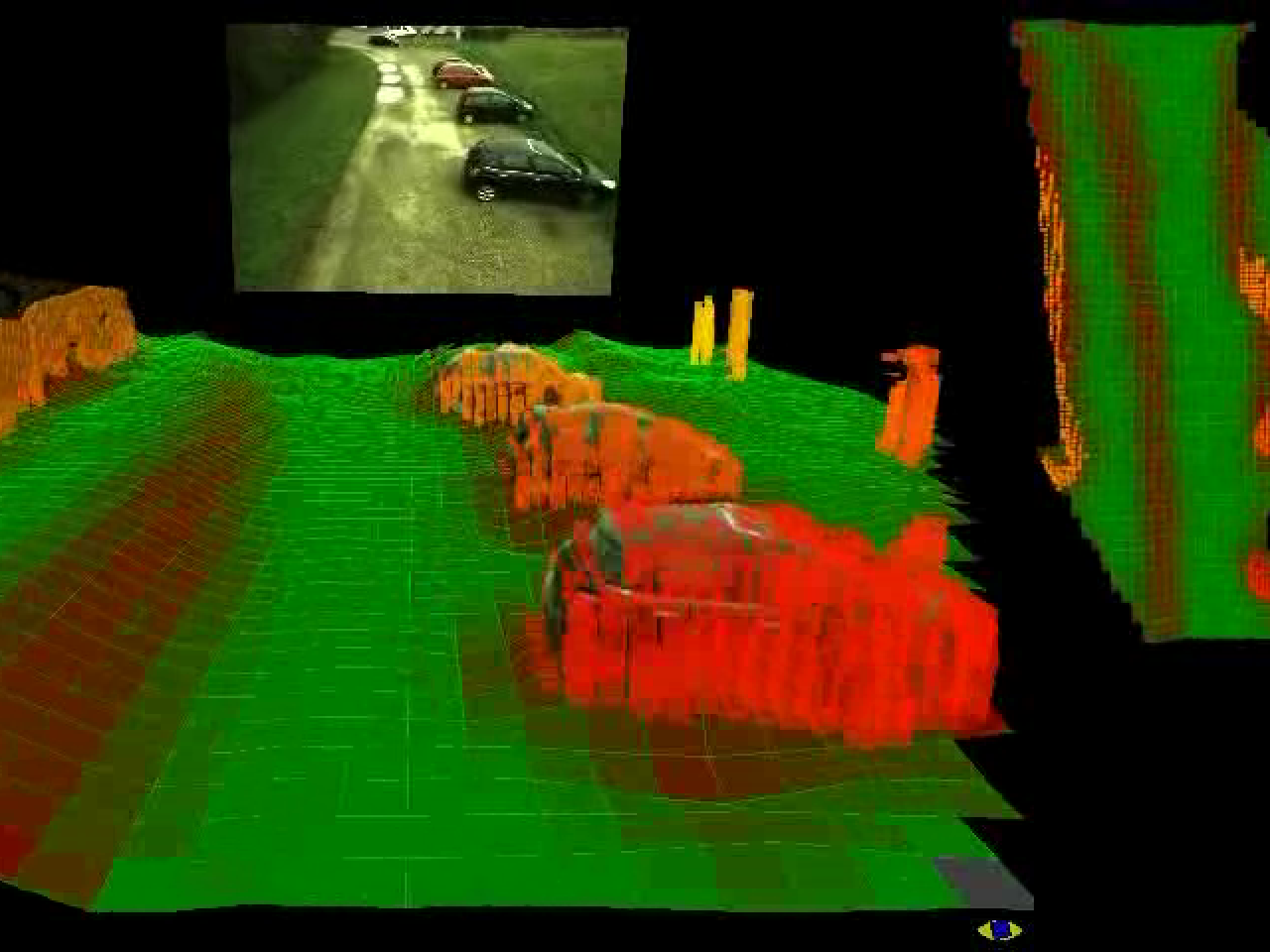