ENEA-TEMAF offers a complete service for the development of advanced ceramic components obtained by 3D printing with the technique based on paste extrusion. The printable ceramic pastes are water-based and characterized by a low organic content (<3%), with low environmental impact, good green densities and low sintering shrinkage. The rheological behaviour of the pastes leads to the printing at room temperature without deformation of the object.
The printer set-up is implemented and the work job is optimized by slicing software chosen on the basis of the component design, which can also reach large dimensions.
Thanks to the experience gained in the sector, the DfAM is applied to advanced ceramic components and the complete characterization is performed, starting from the development of the printable ceramic pastes up to the qualification of the sintered component. The explored applications include the heat and power production also from renewable sources.
3D printing of advanced ceramics allows to explore their use even in applications previously excluded from the limits of design and costs of conventional manufacturing processes. In particular, it is possible to realize complex geometries, more and more required in the optimization of fluid dynamics, lightweighting and for the coupling of components, offering also custom solutions. One of the 3D printing techniques used at ENEA-TEMAF is the LDM (Liquid Deposition Modeling), a low cost technique based on the extrusion of ceramic pastes.
New formulations of ceramic pastes, based on oxide (alumina, zirconia, aluminium titanate, etc.) and non oxide ceramics (silicon carbide, molybdenum silicides, etc.), are developed including composite formulations. The paste is prepared by mixing ceramic powders with suitable rheological additives in an aqueous medium, until the rheological behaviour suitable for printing is reached.
The components are then printed, starting from the CAD drawing of the designed component, taking into account the constraints of the printing technology; the G-CODE file obtained by the slicing of the CAD, is used by printer to make the green component, layer by layer. The component printed at room temperature is then sintered in furnaces also available at pilot scale. Prototypes and small series are realized and the characterization is carried out up to the thermomechanical qualification of materials and components.
The 3D printing of advanced ceramics is a promising net-shape forming method, aimed at greatly reducing the high costs of mechanical grinding, typical of pressing processes, and the limits of shape by mould processes, barriers for a wide use despite the well-known performance advantages of advanced ceramics. The development of AM for advanced ceramics is a potential answer to the demand of more competitive and sustainable materials, characterized by high performance, but at the same time with low density. The market needs for new and sustainable solutions in the production of advanced ceramics, alongside conventional manufacturing processes, could be also satisfied by extrusion based 3D printing. Liquid Deposition Modeling (LDM) technology requires low investment costs, allowing large series production. The aqueous and high-solids pastes developed by ENEA-TEMAF involve a sustainable process with the printing at room temperature and thermal cycle up to sintering with low emissions (organic content < 3%) and low energy consumption.
The offered service is addressed to both 3D printer users and manufacturers and also to end-users interested in custom and/or limited series production of advanced technical ceramic components for applications where chemical inertia, high resistance/specific weight ratio or thermal shock resistance are required. Potential applications cover various industrial sectors such as power production (e.g. burners, braziers, turbines), lightweight solutions for automotive and aerospace, filters or catalytic media for industry.
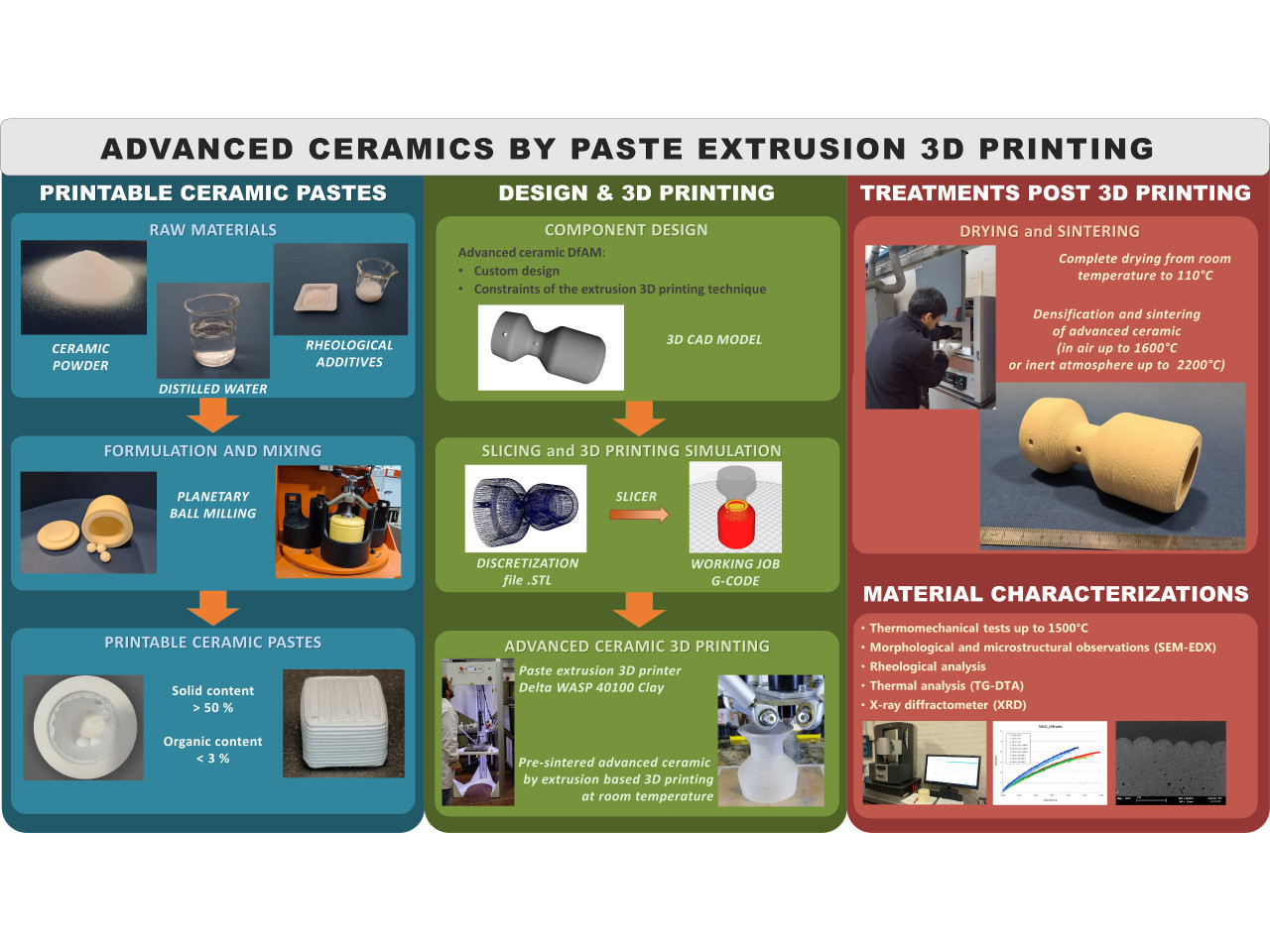
Advanced ceramic components extrusion based 3D printing to improve the sustainability of household heating.
Development of ceramic pastes for extrusion 3D printing, DfAM co-design, 3D printing and sintering of advanced ceramic brazier and testing for pellet stoves.
Producers looking for solutions to improve efficiency and reduce emissions from household and industrial plants based on biomass.
The braziers are the "core" of pellet stoves where the combustion takes place and the conditions are heavier. The conventional braziers are made of cast iron, a low cost material and with good technical properties, but the production by casting in mould limits the design for the combustion optimization. Advanced ceramics, more refractory and with better thermal properties, obtained by low cost 3D printing technique were proposed. A new aluminium titanate (tialite) ceramic paste with rheological behaviour suitable for 3D printing was produced. The design of the brazier with fluid dynamics optimized for combustion was developed, by applying DfAM for advanced ceramics and taking into account both the needs of the end user and the constraints of 3D printing. The job file was obtained with the slicer Cure from the CAD project. 3D printing of the green brazier was carried out at room temperature followed by drying at 60 º C and sintering in air up to 1500ºC. Laboratory tests showed that the tialite obtained by 3D printing, compared with to the same pressed material, shown a moderate reduction of Young’s modulus and bending strength. The tialite based brazier got through the preliminary tests in real conditions in pellet stove.
The collaboration with a company leader in household heating based on woody biomass, has allowed to develop and co-design the new advanced ceramic brazier and to test both materials and 3D printed prototypes within their labs equipped to reproduce the real working conditions.
New collaborations with other partners to explore the potential of advanced ceramics obtained by extrusion-based 3D printing are expected:
• end-users of different application fields (e.g. power production, automotive, aerospace, chemical industry, etc.);
• producers of ceramic pastes for 3D printing;
• co-designers to implement the DfAM of advanced technical ceramics.
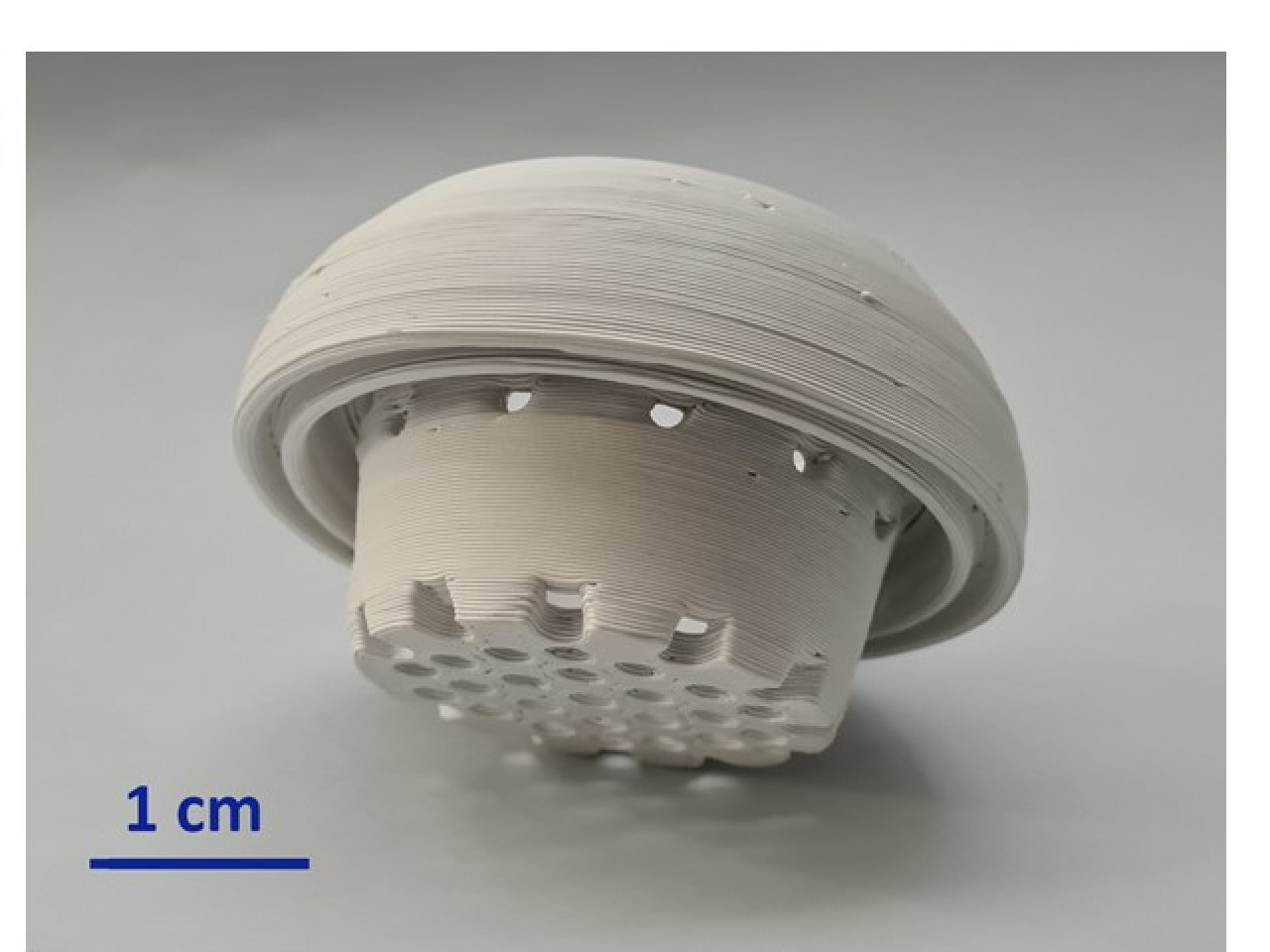