A casting component must be developed considering promptly the critical issues arising from the manufacturing process. Uninformed component design inevitably causes problems in the production stage, resulting in the need for deep geometric review with high marked impacts on lead time, costs and quality. The contribution of designers, FEM analysts, quality, machining, buyers etc. should pivot on correctly implemented process simulation from the very early design stages - immediately after the "blank sheet" one - in a simultaneous and concerted approach. Functional design therefore goes hand in hand with design focused on manufacturing and with cost reduction, thanks to the possibility of generating comprehensible information on which everyone may work quickly and effectively.
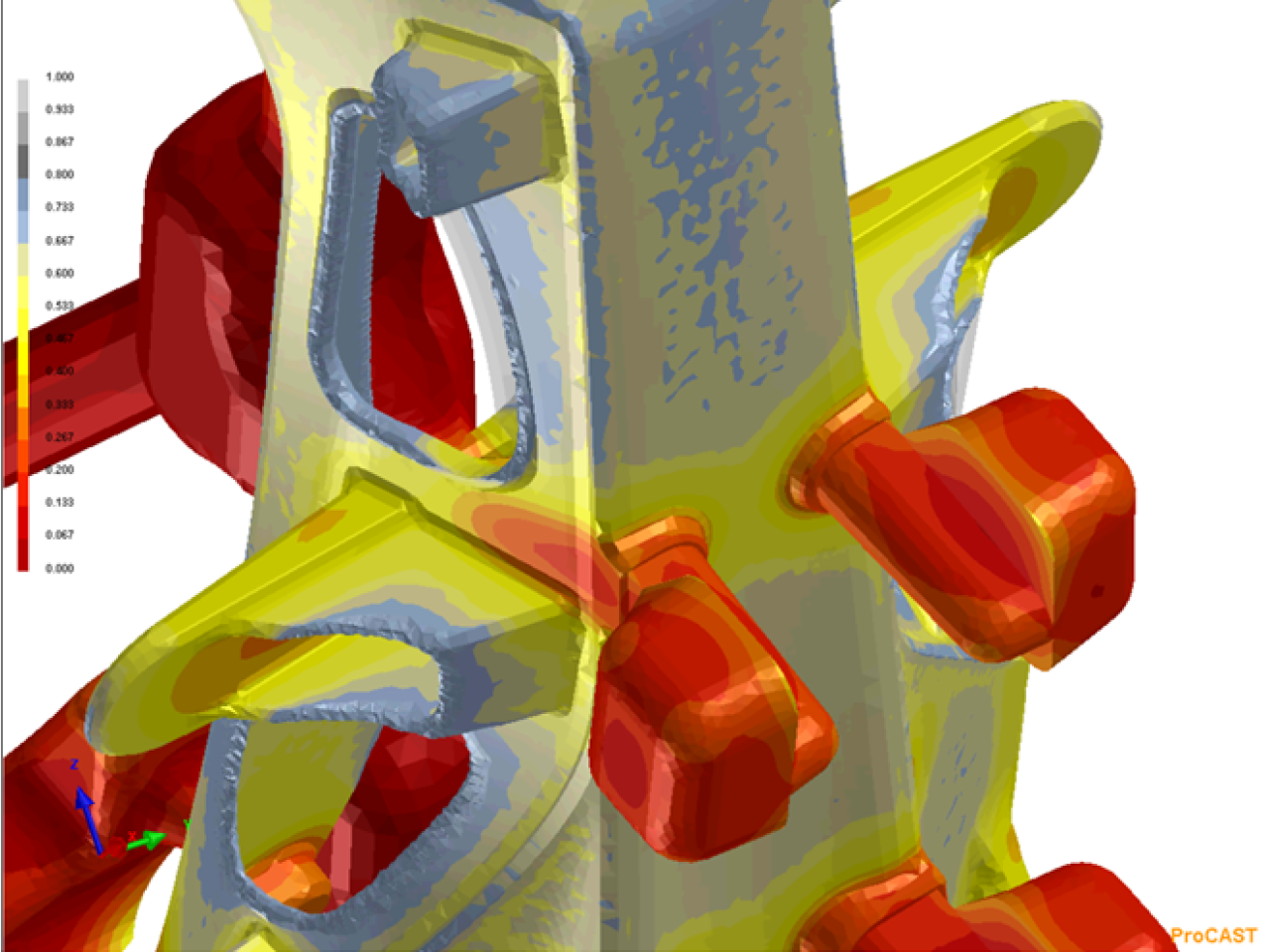
Although the fundamental concepts of Concurrent Engineering have already been formalised for some time, the meeting point between design and manufacturing - in the case of components produced by casting - is late in being identified and properly used. Casting process simulation technologies have reached such a degree of maturity that they may be effectively used as a shared development and discussion tool during the design process: for example, the comparative results of two different functional-geometric solutions can highlight the pros and cons of each, not only in terms of effectiveness of the component in service, but also quality, production difficulties and process robustness (and therefore final component cost), compatibility with subsequent processing etc.
The service puts forth a common discussion platform, on which to base the development of any product produced by casting, be they low or high technological content products. In the former case it is possible to achieve significant compression of time to market and product development costs; in the latter the approach used makes it possible to produce state-of-the-art components.
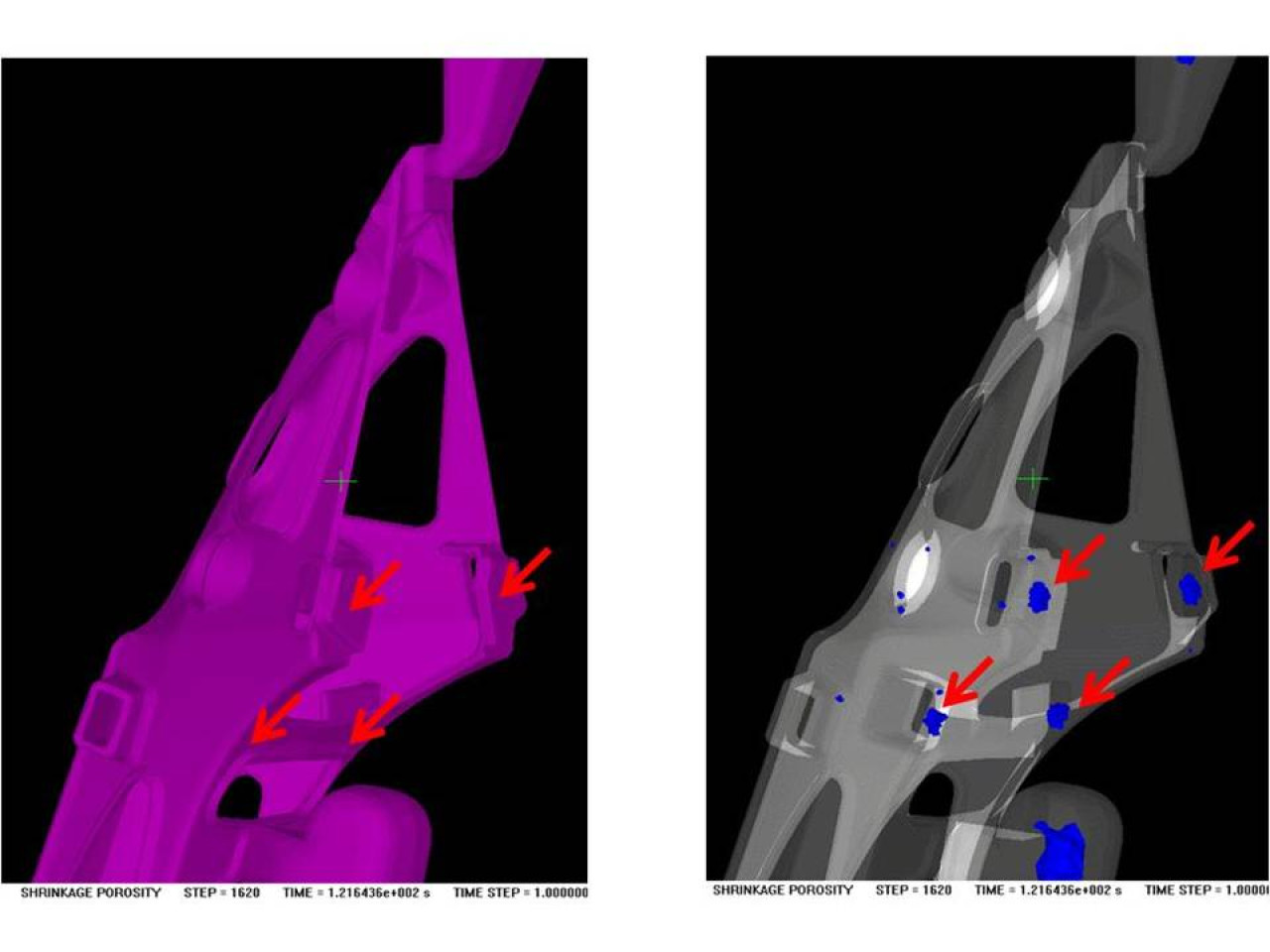
Rear motorbike subframe
The rear frame of Ducati 1199 Panigale features a great geometrical complexity, very thin thickness and extremely low weights, to be combined with very high mechanical and safety performance. Such extreme features had never been required on an aluminium component obtained by casting intended for serial production. Starting from the initial component geometry, a first set of simulations was carried out assuming different manners of laying the component in the die. This first set of simulations highlighted the critical areas of the casting in terms of solidification defects; consequently correct positioning and sizing of the risers was hypothesized. The collaboration among the foundry, the mechanical modelling company, the machining firm company and Ducati technicians led to identifying parting lines of the mould that would not hinder functional and production requirements, and made it possible to "set" the mould geometry. The subsequent assessment steps were carried out using the casting "cluster" geometry worked out by the modelling maker, plausible for actual start of production of the component. Recursive optimisation of the geometries was carried out in a short time and resulted in a producible component complying with functional specifications, that today is fitted on one of the most extreme motorbikes on the market worldwide.
Fonderia Scacchetti, San Felice sul Panaro Ducati Motor Holding, Bologna Machining company of the Bologna area Mechanical modelling of the Bologna area CIRI MAM
The activity was carried out in collaboration with leading companies of the region and deployed a number of different skill sets in a coordinated and proactive manner. CIRI-MAM is continuously seeking partners to tackle new and exciting activities.
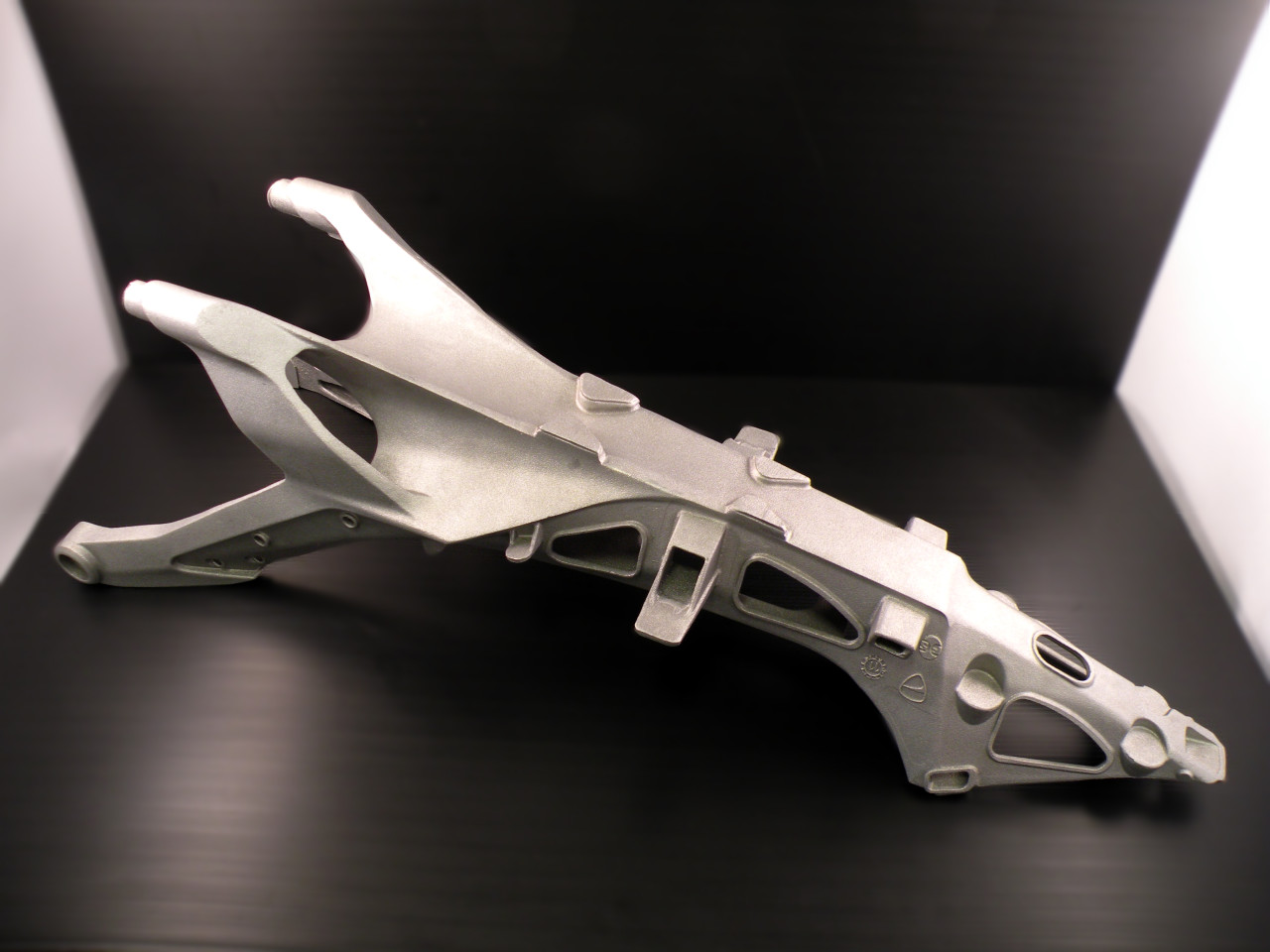