The use of 3D printing as a net-shape forming technique for technical ceramics opens the doors to the application of these materials even in sectors where high manufacturing costs prejudiced against their use. The most suitable AM techniques for dense technical ceramics are Stereolithography (SLA) and its variant "Digital Light Processing" (DLP), in which the component is obtained by polymerization of successive layers of a photo polymeric resin. The ENEA-TEMAF Laboratory in Faenza has the know-how necessary to develop photopolymer slurries loaded with ceramic powders, constituted by zirconia (ZrO2) and alumina (Al2O3) and their composites for the production of prototype components for multiple sectors. ENEA-TEMAF also owns the instruments for the characterization and qualification of these components.
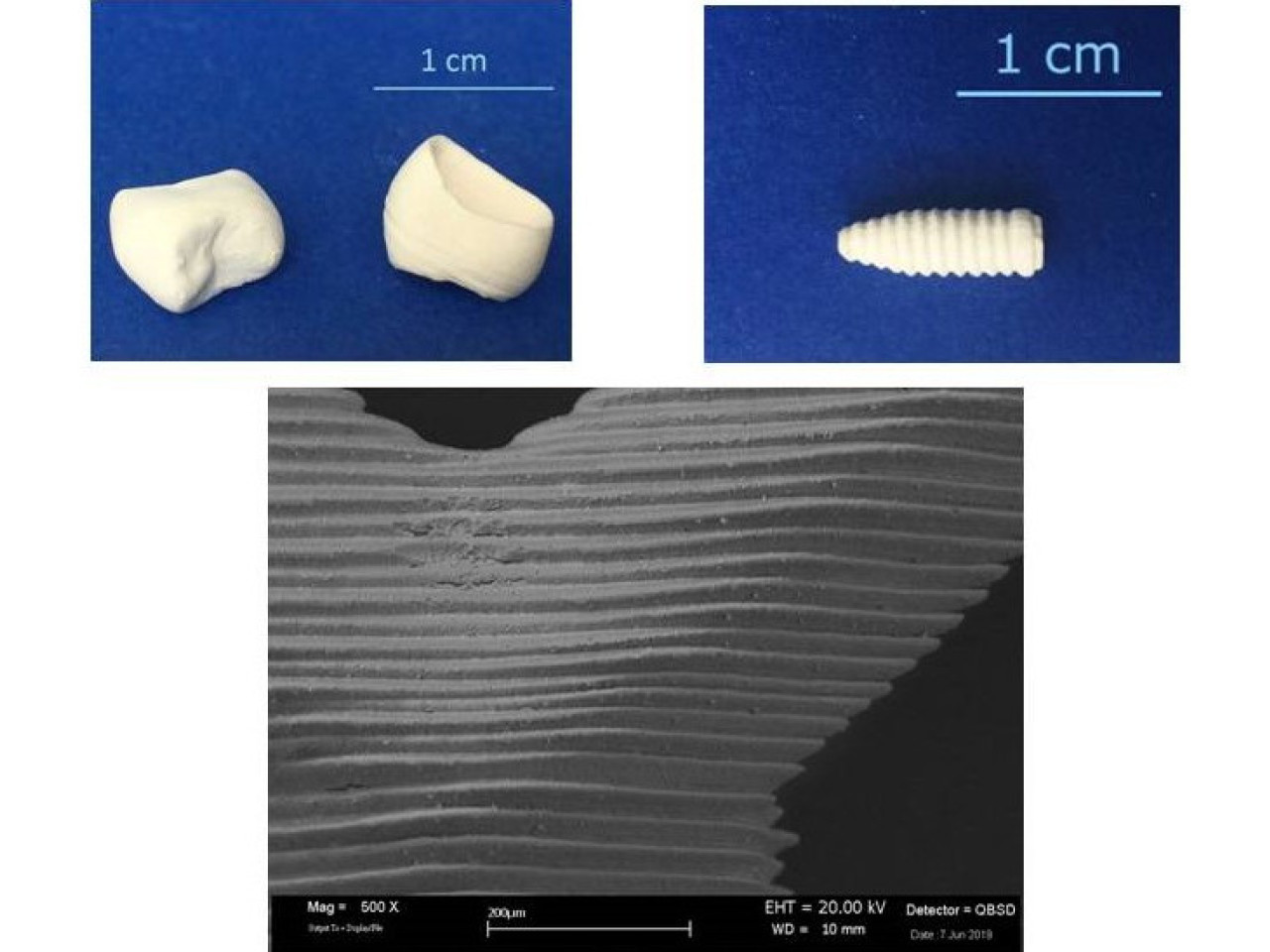
3D printing (Additive Manufacturing (AM)) is promising both in terms of productivity and versatility and constitutes a real revolution in the sector of technical ceramic materials. 3D printing allows to "form" net-shape components, and hence opens the doors of the market to technical ceramics, which have been rarely used in the industrial field until now, mainly due to the high manufacturing costs. The AM of ceramic components is proposed as a winning manufacturing methodology, which is convenient from both an economic and environmental sustainability point of view.
The DLP technique allows producing dense ceramic components, with a high degree of detail and surface finishing, which can be advantageously applied in the biomedical field (bone scaffolds) and in the sector of metal-free dental restoration (endosseous implants and dental crowns), in electrotechnics and microelectronics (sensors), in the field of watchmaking, jewelry, and luxury goods, in the energy production and aeronautics sectors (for the production of cores for the investment casting of turbine blades).
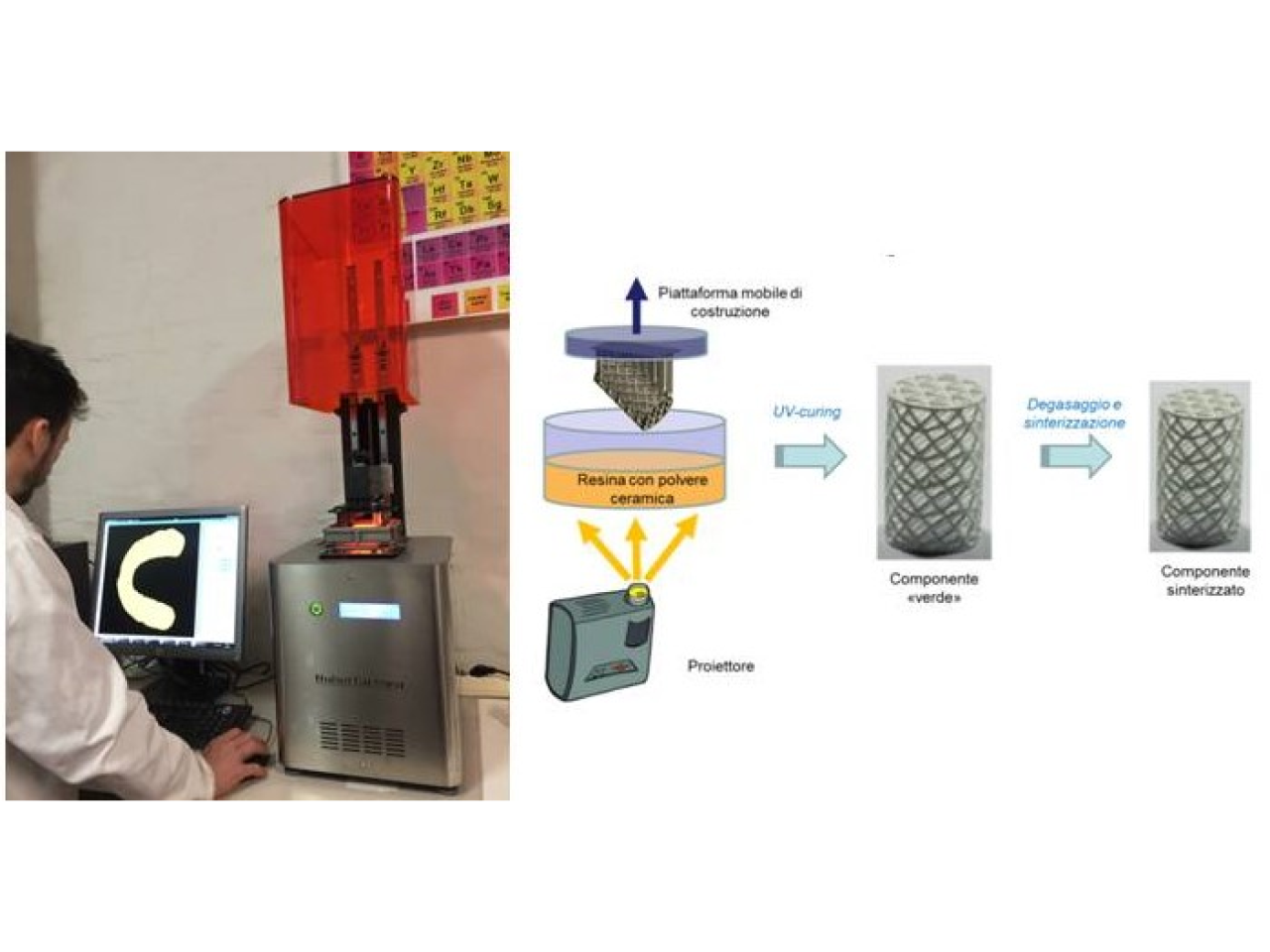
Ceramic dental crown
Among the various applications of DLP technology for printing ceramic materials, a dental crown made of biocompatible ceramic is certainly a component with the optimal characteristics, as it has low thickness and a concavity that would require the use of expensive mechanical machining, if made with traditional subtractive techniques. The virtual model of the tooth to be replaced is acquired by means of an intra-oral scanner, and it is then processed by a software which provides the virtual prosthesis file in STL format. This is used by the 3D printer software to make the supports for component manufacturing and slicing, i.e. the decomposition into layers of component and supports. The component is then printed using a photosensitive resin loaded with biocompatible ceramic powder (e.g. based on Zirconia) and subjected to post-curing and thermal cycles of dewaxing and sintering in order to remove the resin and densify the material. This process has been positively applied at ENEA-TEMAF laboratory, where the feasibility of ceramic dental prosthetic components was demonstrated using a special photosensitive resin - ceramic powder mixture.
Identitalia Group, partner of the AMACO and PRODE Projects, funded by the Chamber of Commerce of Ferrara, under the call for Digital Vouchers I4.0
To date, there are very few commercial resins already mixed with ceramic material, and the development of these slurries represents the critical phase of the printing process. Collaboration with other research centres or universities, specializing in photosensitive compounds, can help in the optimization of innovative photosensitive resins to be loaded with ceramic powder.
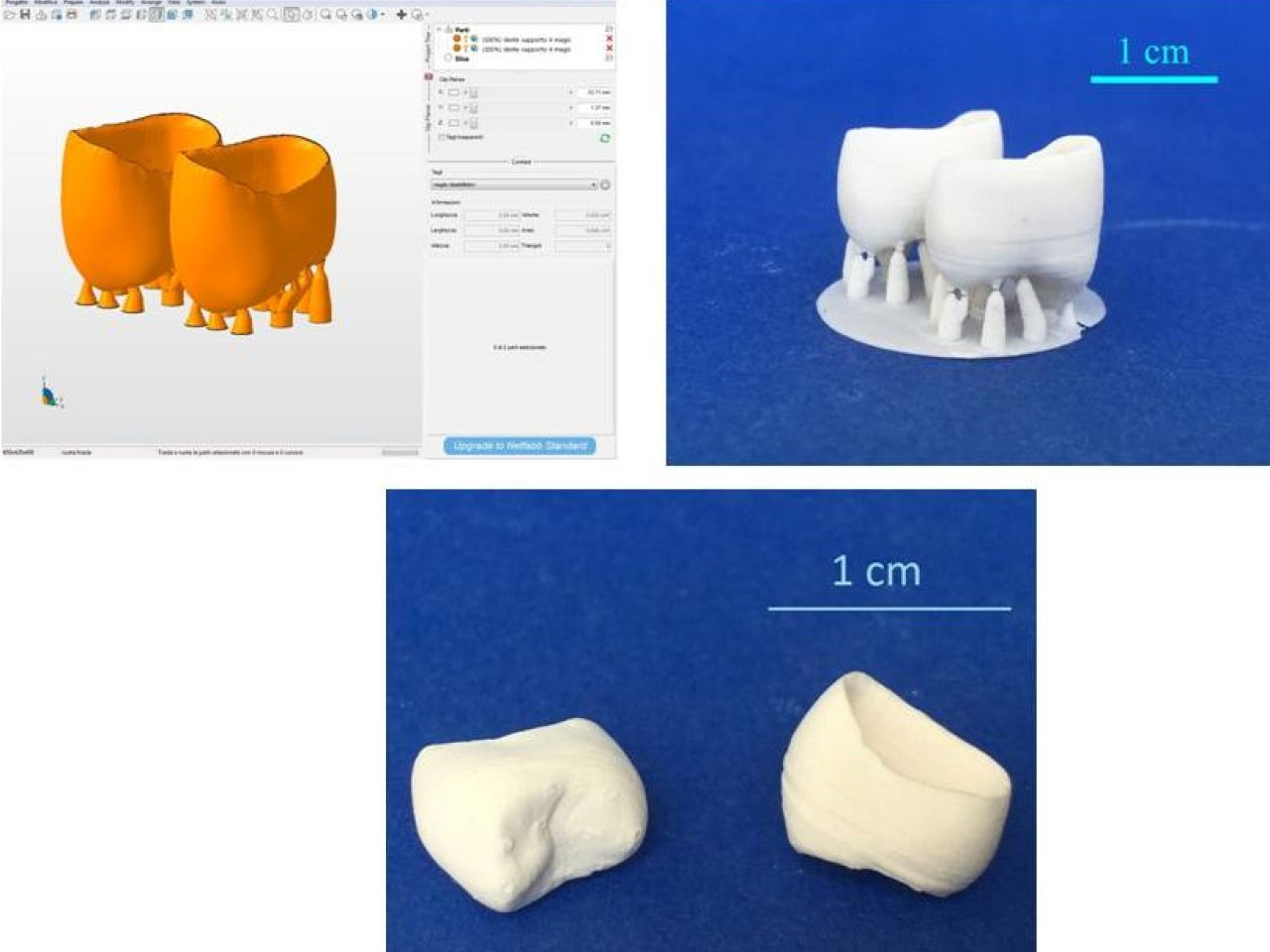