The development of new categories of fiber-reinforced composites aim to satisfy the necessities of transport and construction sectors, to increase both material performance and process sustainability. Since 2010, the laboratory has been developing many innovative solutions, and possesses unique pilot lines and facilities for materials characterization and component qualification, including tests in simulated operating conditions. The laboratory carries out its activities within national and international networks, by identifying objectives, partnership and implementation path on a case-by-case basis. Excellent results were achieved about low weight, high temperature and fire-resistant composites, focusing on the development of new semi-finished products, preceramic prepregs in particular, secondary raw materials and easy to transfer processes.
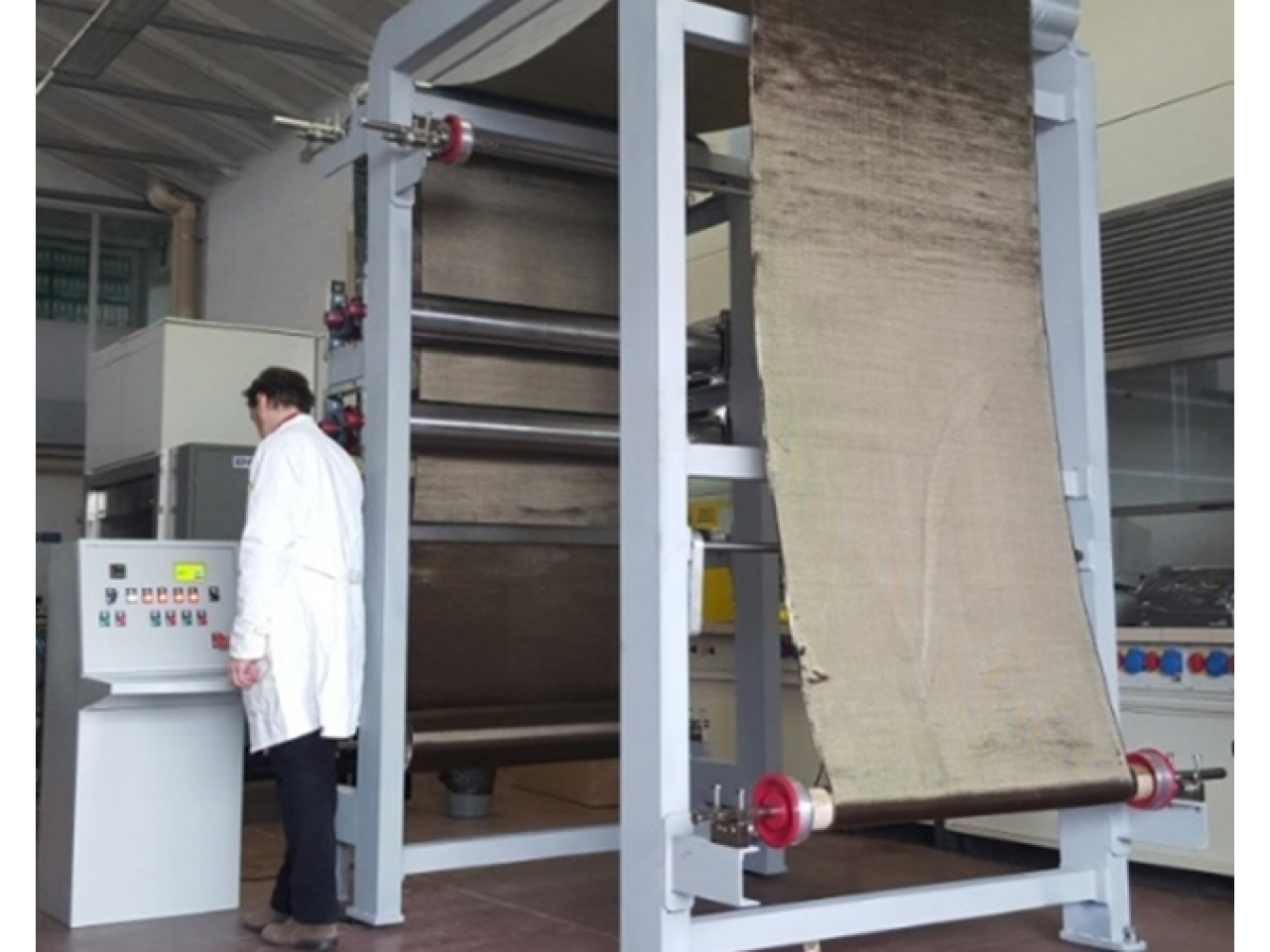
Composite material with a fire-reaction comparable to the one of inorganic materials, obtained without pyrolysis and sintering treatments. High eco-sustainability is ensured by the low Embodied Energy, the use of secondary raw materials and the possibility to recycle the mineral fibers. The manufacturing process starts from preceramic prepregs, an innovative semi-finished product compatible with all current industrial processes for complex shape components manufacturing. The proposed solution is studied both alone and engineered in multimaterial systems.
The application fields requiring light-weight and fire resistant materials are, for example, ventilated facades for buildings, insulating panels for transports (e.g. marine and rail transports), heat shields for battery protection in the automotive. Sensors (including thermolabile ones) can be easily included inside the components during manufacturing (e.g. thermocouples or strain gauges). The innovative characteristics of processes and materials make it possible future application to mass production, which is currently difficult employing commercially available solutions.
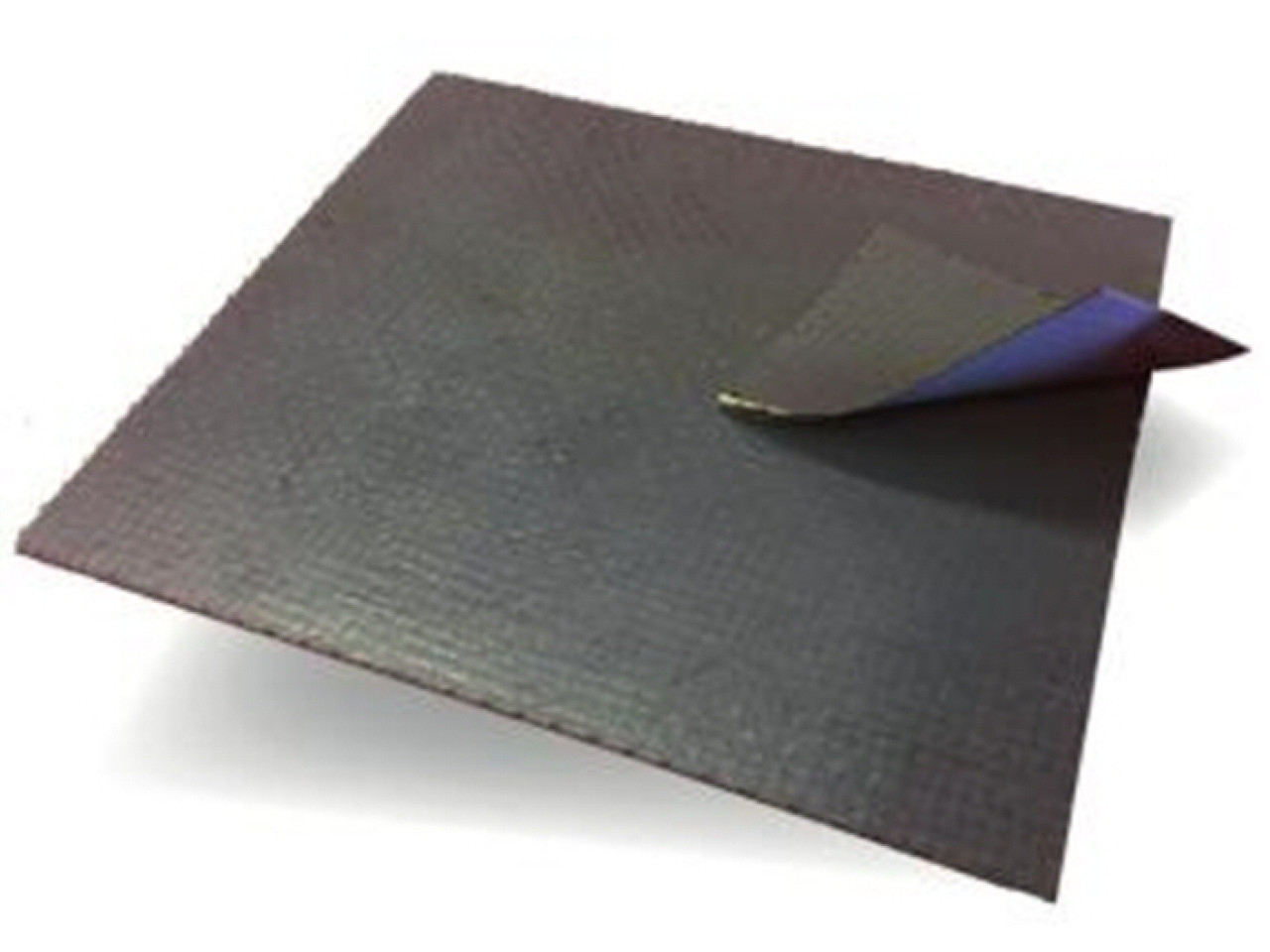
Prototype panels and complex shape components for heat and fire shield applications.
The proposed material was called “BasKer-PMC”, a promising material due to its continuous long-term temperature resistance up to 400°C, tolerance to environmental aging and "incidental" fire exposition. The interest about BasKer-PMC comes from lower weight compared to competitor materials (e.g. aluminum or steel) and much higher performance in temperature (e.g. standard PMC). The flame retardant characteristics were qualified according to the EN 13501/1 standard, which foresees an exposure for 30 minutes at 700°C (qualification carried out with the calorimeter cone in collaboration with CIRI-MAM). The material is classified as “A1”, that is the same class of inorganic materials, and it means that the material does not undergo combustion. This result was obtained through the use of preceramic polymers, associated with an innovative fire retardant formulation. The easy applicability to mass production of panels and components of complex shape makes it an ideal solution for various applications such as case batteries, elements to protect power electronics, able to contain if needed, a fire or outbreak of fire. The collaboration with end users is very close, in order to explore new applications together, with joint research activities. ENEA provides its know-how and facilities for the development and qualification of customized solutions.
GS4C srl Bellotti SpA RIBA Composites srl Carbon Line srl SIC, Società Italiana Compositi Aliva srl
Three patent applications were presented: one became an Italian patent (in co-ownership with RIBA) and another is being converted into a European patent (about the production of heat shields in complex form). The patent application about the production of preceramic prepregs was withdrawn before disclosure, because it was not guaranteeing proper know-how protection.
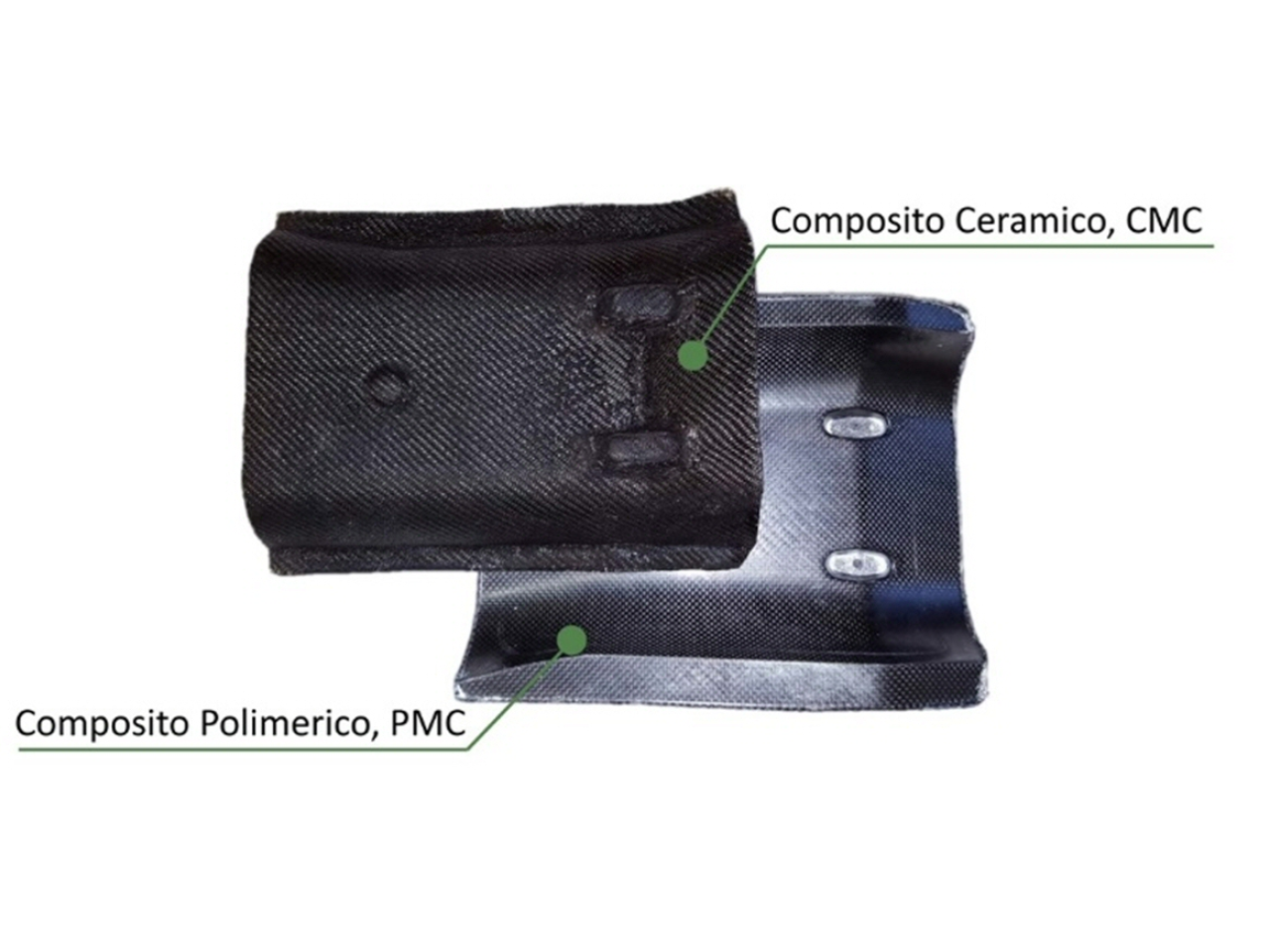