The design decisions of many small and medium-sized companies that produce turbomachines in specific sectors are based more on experience than on an analytical approach. In fact, fluid dynamics simulation software often requires very costly licences, and one does not always have the experience to validate the models and correctly interpret the results, all the more so if working in specific conditions or with special fluids. The fluid dynamics optimisation service offered by the MechLav Laboratory fulfils these needs, by using sophisticated CFD (Computational Fluid Dynamics) simulation techniques and the skills of a team specialising in fluid dynamics design. The service is not limited to conducting simulations or defining new geometries, but provides support to company personnel and transfer of the necessary know-how for further product development with an analytical approach.
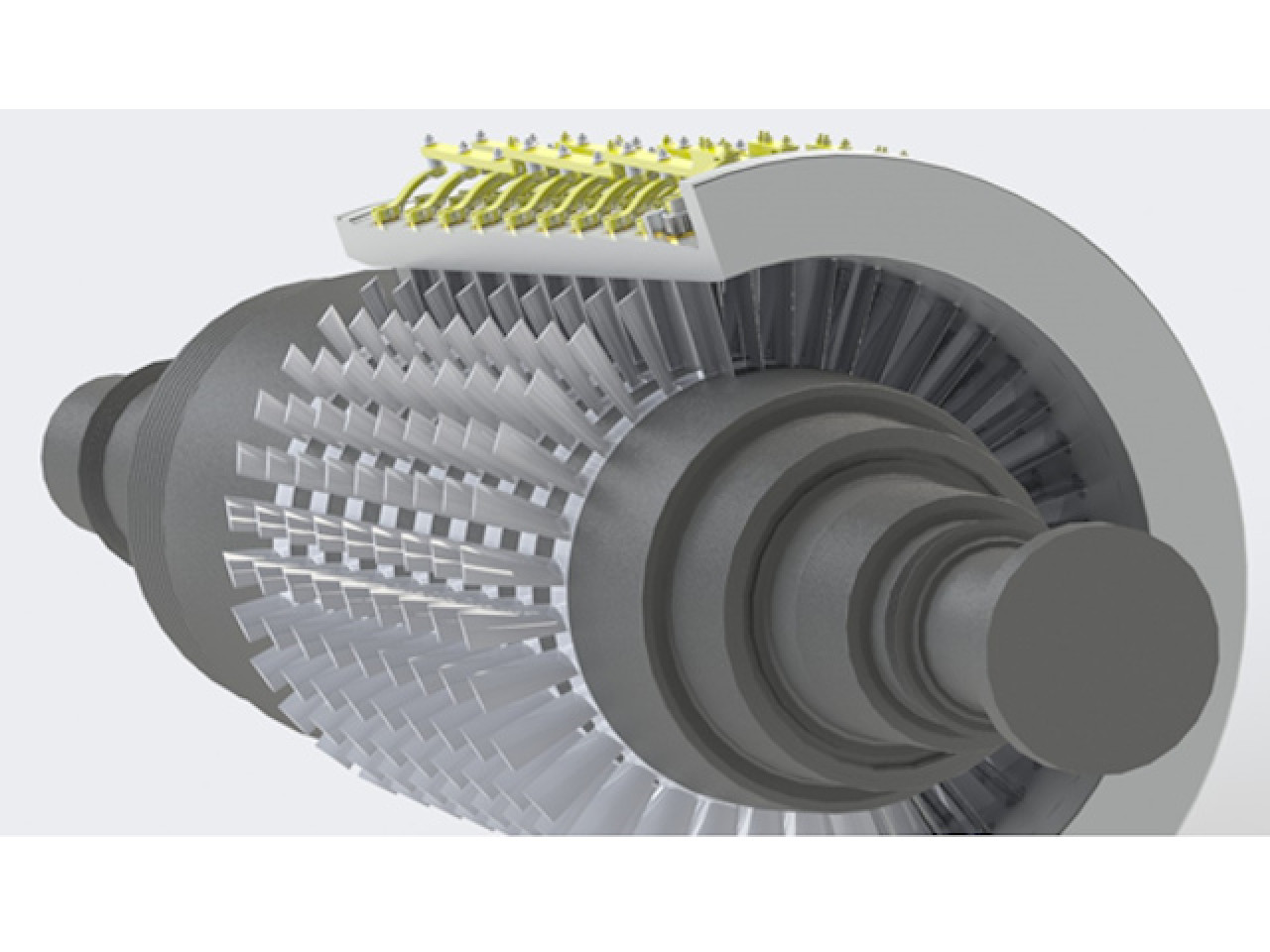
Fluid dynamics simulation of a machine allows its behaviour to be estimated with no need to make a prototype; it is also conducive to making a reliable estimate of a set of otherwise inaccessible data, such as precise or average measurements of pressure, speed, density at each point of the machine CFD also makes it possible to estimate machine performance in any condition, including those operating with special fluids, such as non-Newtonian or high density and temperature fluids, for which testing turns problematic or even infeasible (cost of the testing equipment, availability of the fluid, etc.). Geometric and fluid dynamic Reverse Engineering represents a unique aspect in that it combines the expertise of researchers dedicated to accurate and detailed geometry analysis through 3D scanner measurement techniques, with the know-how relating to the design criteria and fluid dynamics of turbomachines.
One-dimensional design methodologies enable sound sizing of axial and centrifugal machines for an extremely wide range of applications. Furthermore, the use of CFD allows all variants not foreseen by classic design to be assessed and analysed: unconventional operative fluids such as oils, muds, bentonite, concentrated tomato paste and liquid foodstuffs in general; design constrained by special shapes and dimensions, such as reduced scroll dimensions, improved resistance to cavitation; geometric constraints imposed by the production process, for example developing fluid-dynamically efficient geometries simple enough to be made ​​with sheet metal or injection moulding of polymeric material.
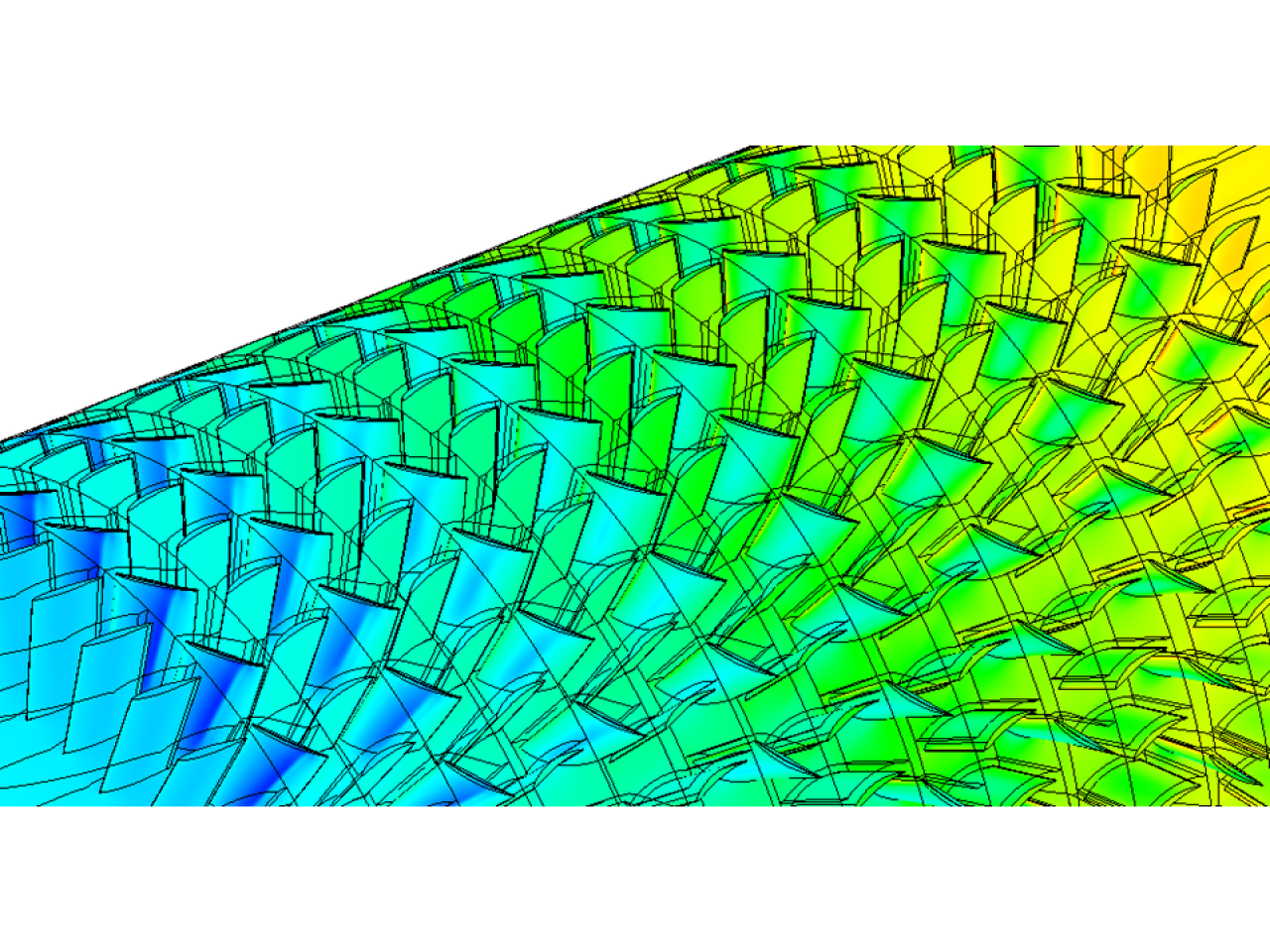
Optimisation of a mixed flow operating machine for concentrated tomato paste
The need for continuous redesigning also exists for products already appreciated by the market to increase their performance, in order to achieve or increase their competitive advantage. Rossi & Catelli has decided to contact the MechLav laboratory of the Ferrara Tecnopolo to be assisted in optimising a pump for processing concentrated tomato paste. Redesigning went through a sophisticated procedure involving: acquisition of the current geometry by using an arm instrumented with laser sensor; reconstruction of the CAD model and simulation of the current geometry to identify critical geometric details for performance improvement. This simulation took into account the actual features of the fluid processed by the machine, starting from rheological analyses of concentrated tomato paste specifically carried out for the case in question. The MechLav research team and the Company closely collaborated throughout the entire redesign to define design specifications and issues, in order to take into account production requirements and their impact on performance (definition of surface finish, keyways, end clearances etc.) The work made it possible to: obtain information on the current design status assess a number of design solutions, put forth by both parties, based on fluid dynamics design assess the results of the analyses with the research team's support and thus identify the most effective solution meet the market's requirements, drastically reducing their product's time-to-market
Rossi & Catelli - CFT Group (PR)
MechLav is interested in developing this type of projects with other Companies, aimed at fluid machines optimisation and/or redesign - by using innovative analysis methodologies and tools and with know-how transfer to the company's personnel.
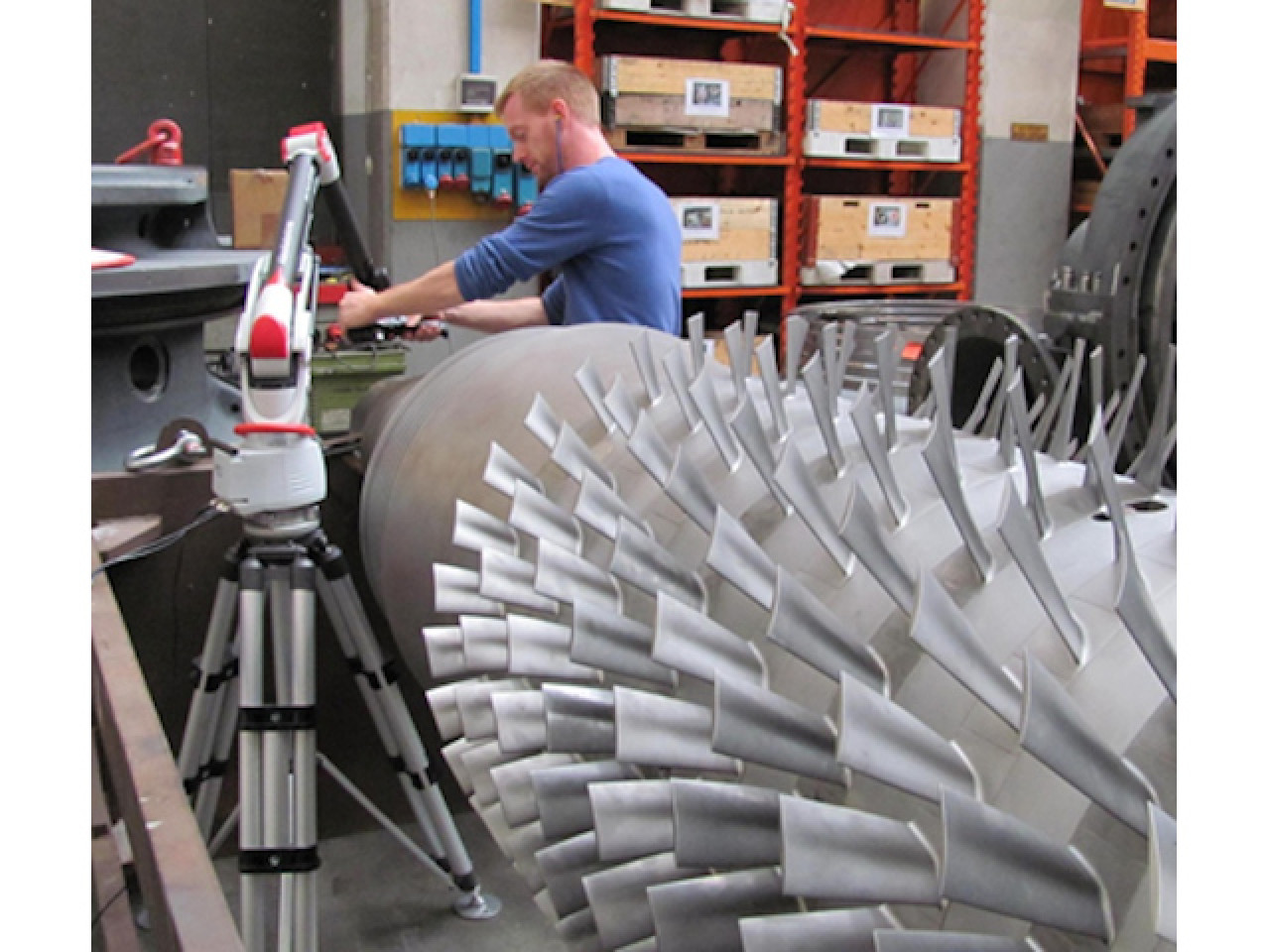