In a recent project involving the RER and four large companies in the district, the Tecnopolo Mario Veronesi (TPM) acquired the skills and equipment needed to build a Plant Pilot for the production of porous polypropylene (PP) hollow fibers and to study their functional performance and mechanical and chemical-physical characteristics. The Plant Pilot implements the TIPS (Thermally Induced Phase Separation) process, which involves mixing PP with natural oils, spinning it in a medium that determines its solidification by heat, and obtaining a fiber whose surface has a porosity that allows oxygen and CO₂ to pass through it, but not plasma in artificial blood oxygenation.
At the end of the project, the first oxygenators were realised. It is now possible to optimise the properties of the fibers produced by the Plant Pilot for filters to be applied in other industrial contexts.
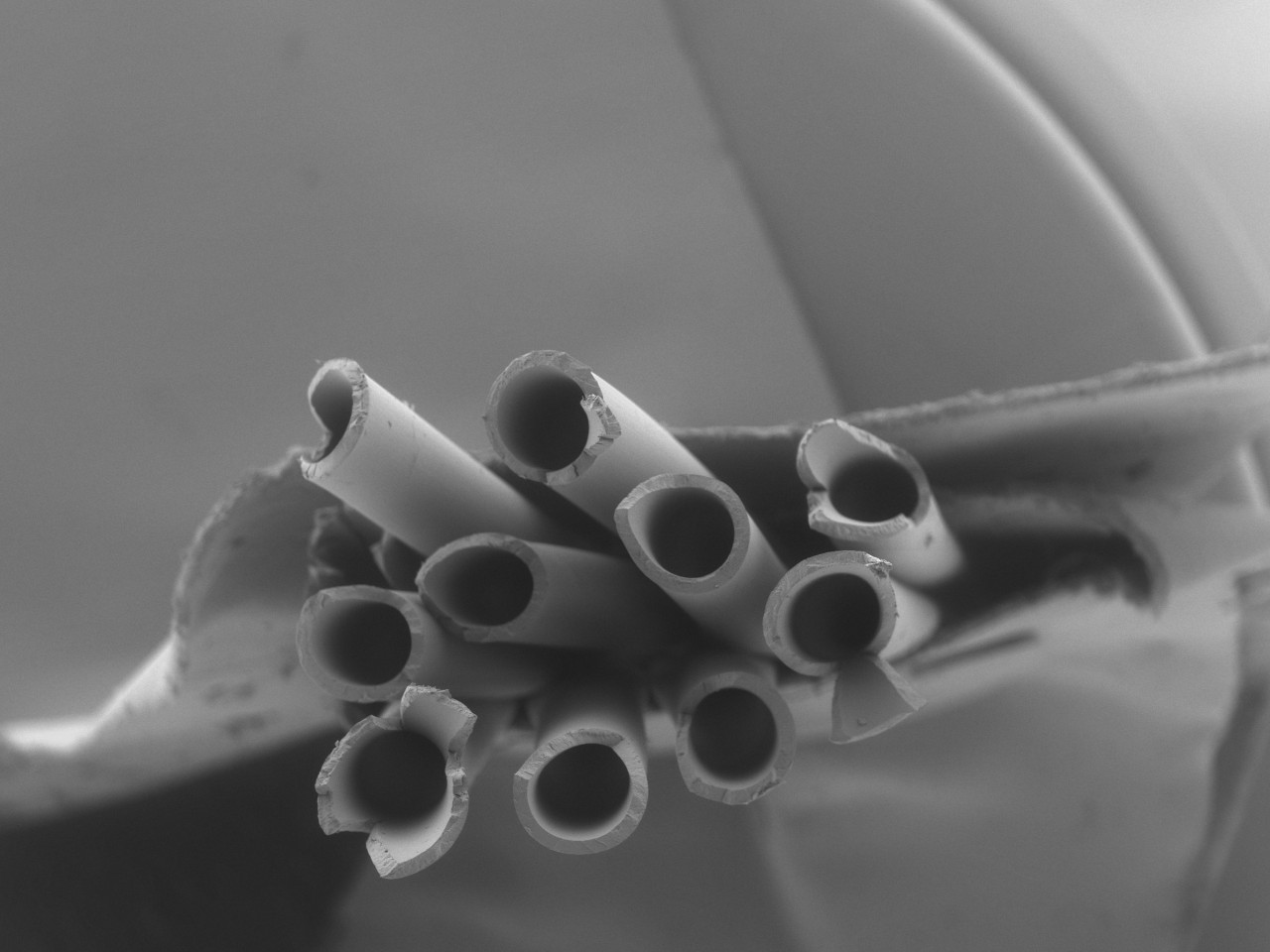
Through this project, TPM and the partner companies have acquired relevant knowledge for the specialization of the material and the TIPS process in order to produce a porous hollow fiber capable of forming the functional unit of blood oxygenators used in cardiothoracic treatments involving extracorporeal circulation.
This achievement was also made possible by the use of tools such as the porometer, dynamometer, contact angle goniometer, SEM, HPLC, DSC, and MFT, which enable the characterization of the fiber's geometry, mechanical properties, morphology, surface wettability, and spongy structure, as well as the assessment of the membrane's ability to be permeable to gases such as oxygen and CO₂, but not plasma. Consequently, it has become possible to offer a service for the optimization and specialization of hollow fiber properties, providing unique know-how in Italy.
Porous hollow fibers are an innovative technology for large-scale applications with higher efficiency and lower costs in extremely compact units, widely studied and applied today in contexts such as:
- CO₂ capture with gas-liquid membranes in high greenhouse gas emission facilities, such as biogas production plants;
- Water purification for industries requiring ultrapure water, such as the pharmaceutical sector;
- Gas mixing in carbonated beverages.
The project has allowed the acquisition of knowledge-intensive know-how, since to date the production and marketing of this type of fiber in Western countries is monopolised by a single company. The knowledge of the complex and articulated fiber production process achieved is therefore of extreme interest for the regional production realities as it is oriented at the structural strengthening, improvement of competitiveness and quality of one of the leading products of the biomedical district. Not only that, the Plant Pilot can now be used to study the production of specialised fibers from a physical, mechanical, geometric and functional point of view for new industrial sectors of extreme interest such as the removal of CO₂ or the control of gases dissolved in water or beverages.
The membrane offers a fixed interface for gas/liquid mass transfer without spreading one phase into the other, while the hollow fiber structure offers the maximum surface area per volume of the device.
Membrane modules made of porous hollow fibers enable the transport of components between gas and liquid phases by providing an interface that prevents direct mixing and dispersion of the phases. The hollow fiber produced by the Plant Pilot can therefore be used in various industrial sectors for efficient gas exchange (such as CO₂ sequestration in polluting plants), to be balanced (such as in carbonated beverages) or to be separated (such as biomethane production) by exploiting its hydrophobicity.
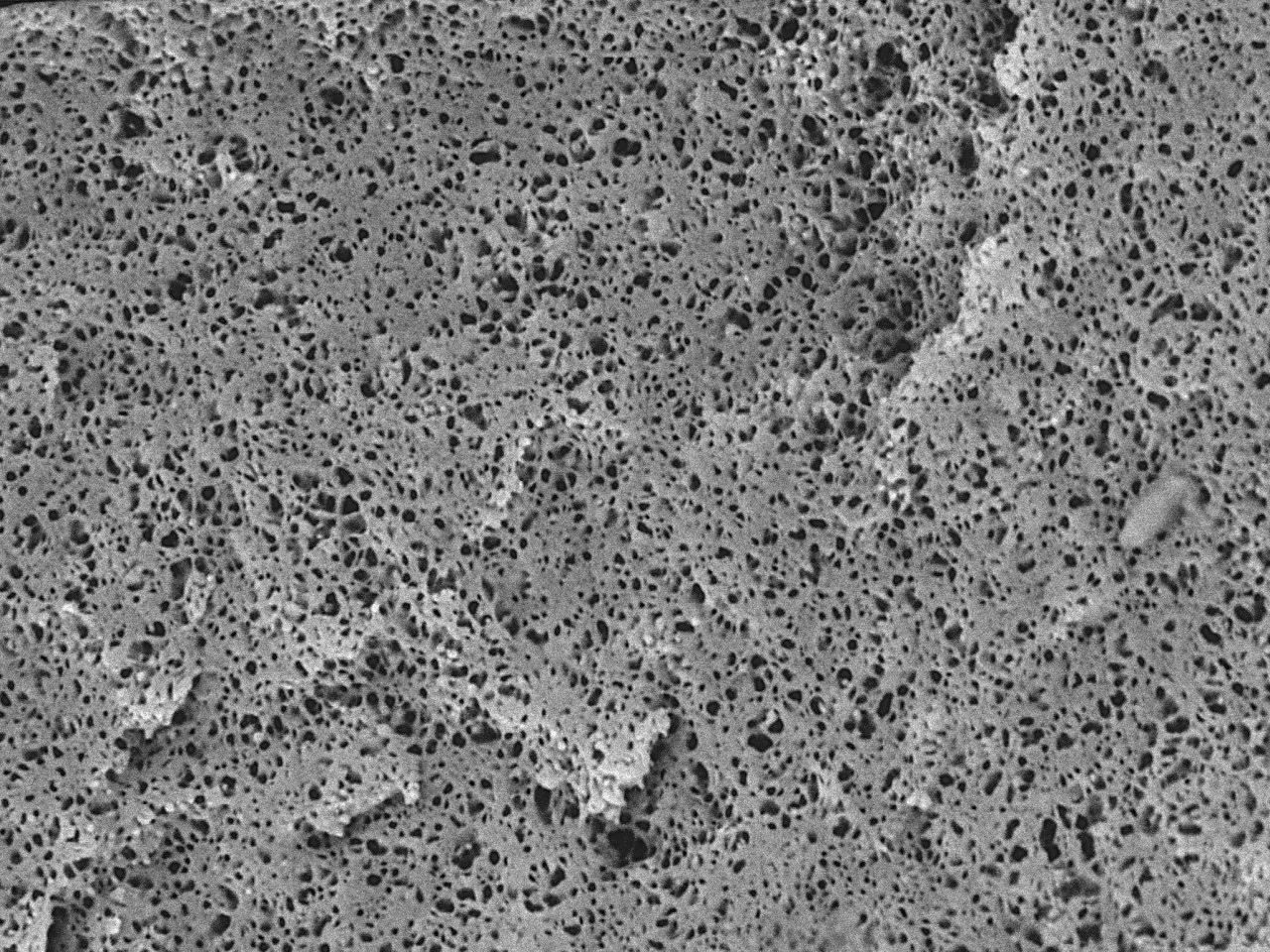
The fiber produced by the Plant Pilot can be specialised in the following sectors, for example:
- Biomedical sector: for the production of oxygenators;
- Pharmaceutical sector: water with conductivity <1.3 µS/cm thanks to the removal of CO₂;
- Oil and gas refineries: transfer or removal of gas from liquid phases;
- Beverage production: addition or removal of O₂, CO₂, N₂.
The Plant Pilot is now being used to specialise the recipe required for the production of porous PP hollow fibers used in the manufacture of oxygenators used in extracorporeal blood circulation during cardiac surgery treatments. In addition, during the project that saw the realisation of the Plant Pilot, procedures for oil extraction and solvent stripping were studied and protocols defined for the analysis of all its technical characteristics. For the latter purpose, a laboratory equipped with state-of-the-art instrumentation was set up for the characterisation of plastic materials, their surface properties, permeability, wettability and biocompatibility, given the direct contact of the fibers with blood.
All this was made possible thanks to the fruitful and intensive collaboration and exchange of knowledge and expertise that took place between the industrial partners, the European consultants and the Technopole.
The knowledge gained can now be exploited in other areas where the fiber is increasingly being used, such as in biomethane production plants, water purification plants, research and analytical laboratories, and the production of sparkling beverages.
Four big companies based in the Biomedical Valley.
The know-how acquired will be at the service of partner companies in the biomedical sector and beyond that use PP hollow fiber to carry out R&D analyses and implement fiber quality characteristics according to their needs.
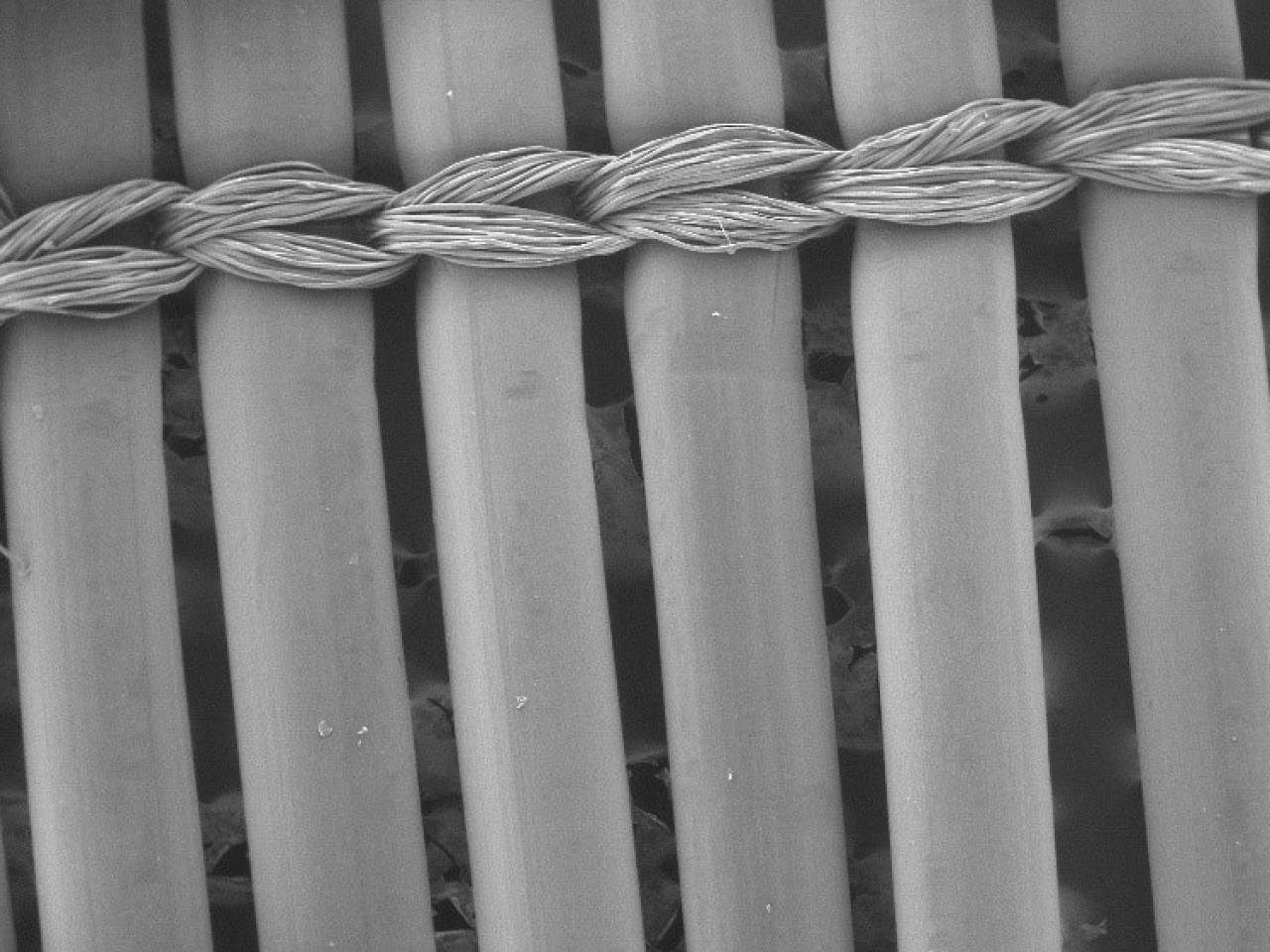