Remote monitoring and control of automatic machines and systems is one of the most interesting ICT application sectors at industrial level. The i-Maintenance platform by CenTec allows monitoring and control, diagnostics and prognostics, configuration and recovery operations of automatic machines to be performed remotely. i-Maintenance also makes it possible to restructure maintenance processes optimising servicing (phone fix and first-time fix) and reducing machine downtime. With i-Maintenance machine operation is always under control, fostering the development of new business models based on the offer of machine fleet management services (servitisation). The use of COTS (Components Off The Shelf) hardware and software solutions, allows i-Maintenance to make large scale monitoring and control affordable, also for low cost machines (food processors, vending machines, etc.).
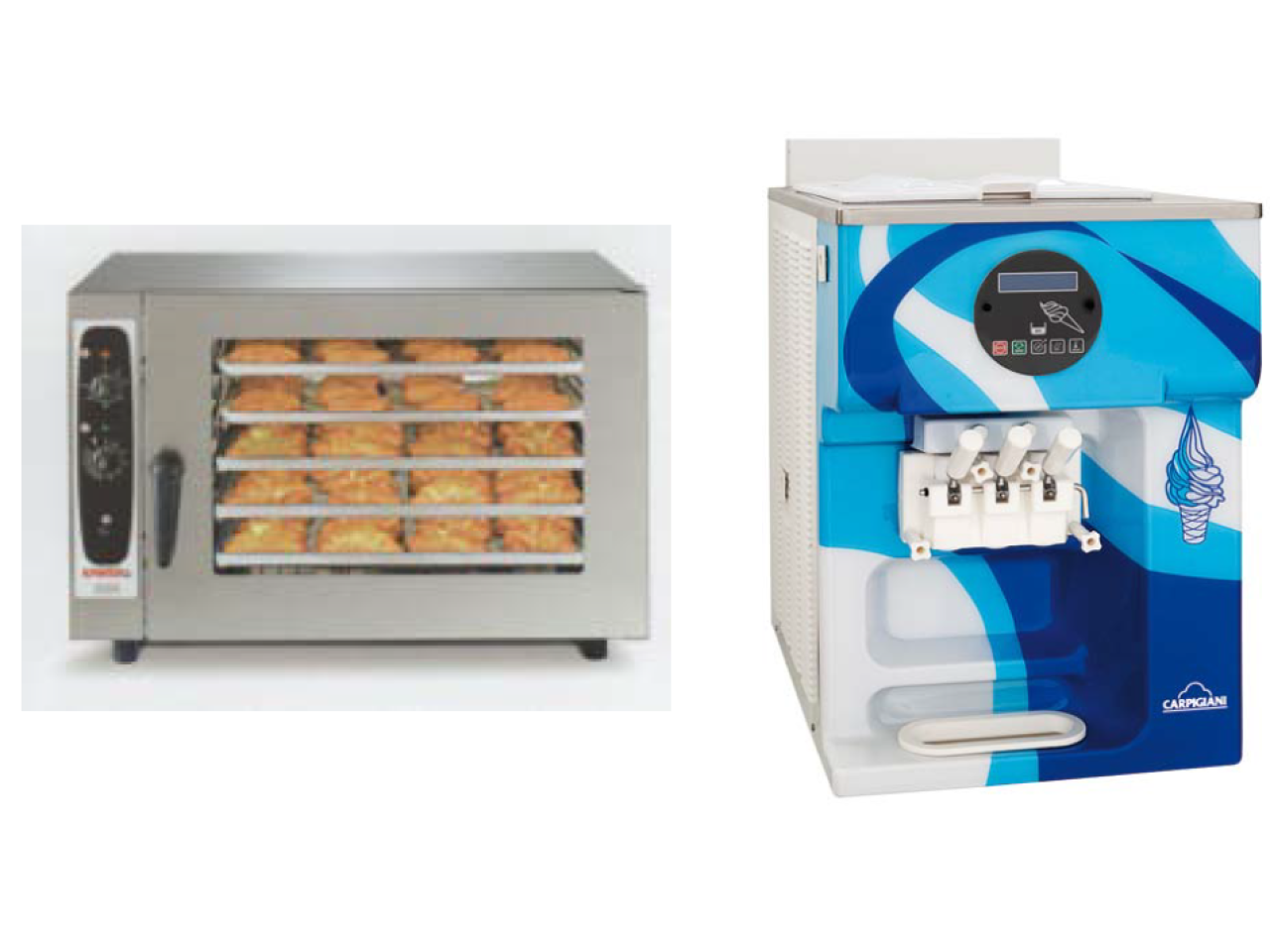
i-Maintenance brings to the manufacturing sector the most modern information technology used on the Web and Internet: COTS hardware and software components (e.g. boards with ARM processors), the Linux embedded operative system, Open Source software components, communication standards that have fostered the development of modern Web-based services. This technological innovation is conducive to reducing the costs of individual control kits and of the overall i-Maintenance platform, which may be easily adopted for large scale remote monitoring and control of a wide range of automatic machines, such as food processors, vending machines, industrial washing machines, etc. Furthermore, modern Web 2.0 technologies allow i-Maintenance to be easily integrated with company information systems. i-Maintenance gathers maintenance information in a Cloud system which may be configured as public or private depending on company strategies. The monitoring data can then be used on any device and platfor
The i-Maintenance platform may foster the switch from a business model based on the supply of products to one based on the provision of services. Customers no longer purchase a machine, but sign a service agreement which assures machine operability with certain levels of service. This new business model allows companies to diversify the offer with lower investments and therefore improve their competitive advantage. The first applications of i-Maintenance have made it possible both to improve the allocation of human resources devoted to maintenance, allowing technical support personnel to monitor and service machines remotely (phone-fix), and to suitably plan any on-site servicing, optimising times and costs and increasing the likelihood of machine repairs with one visit only (first-time-fix).
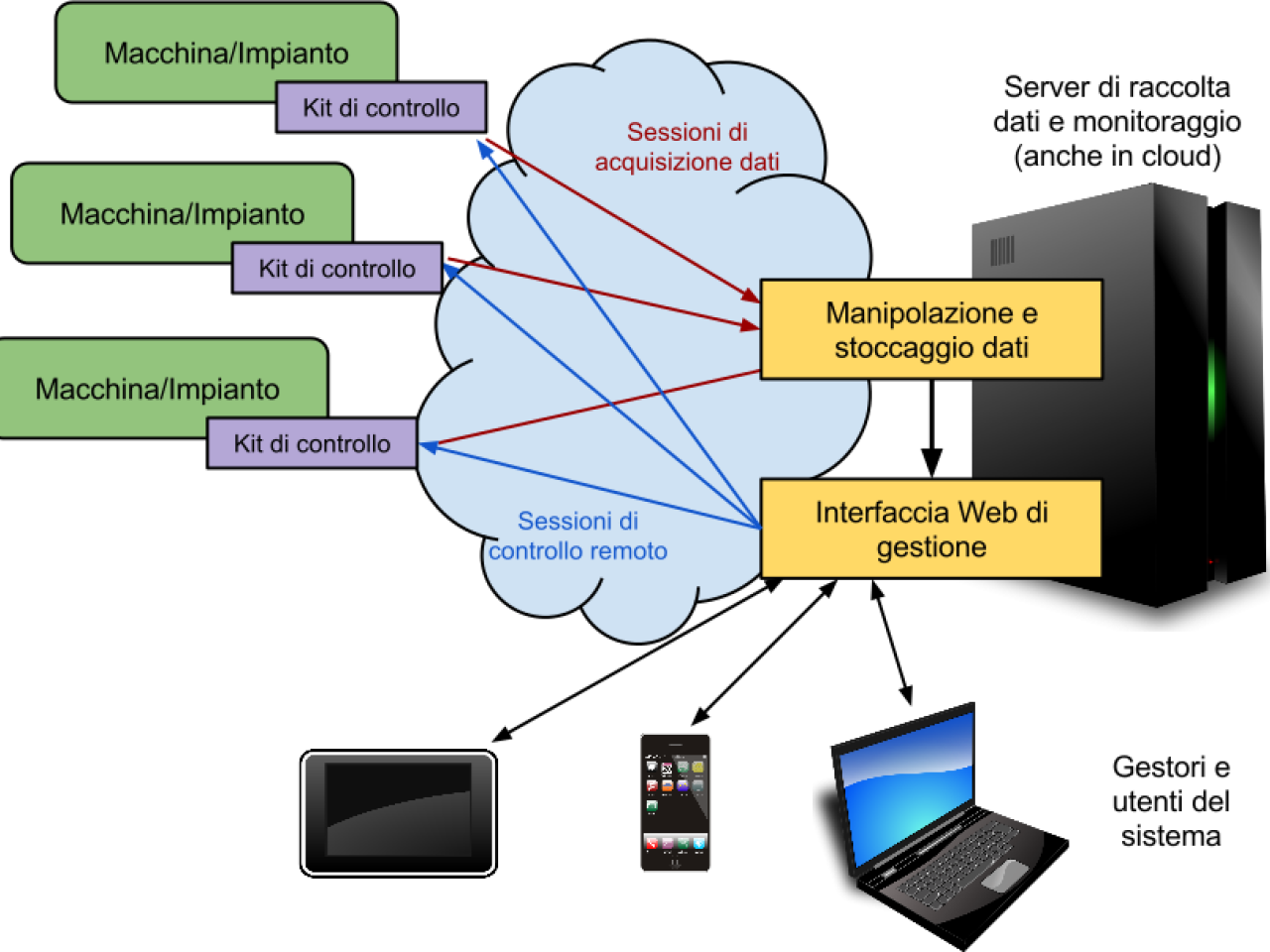
Teorema: the Carpigiani e-Maintenance platform
Carpigiani machines operate within widely distributed ice-cream shops and their downtime may cause a significant loss of income. That is why Carpigiani has always paid the utmost attention to the maintenance process, which traditionally, has always operated dealing with breakdowns and regular checks. The geographic position of ice-cream shops on a global scale makes the maintenance service organisation complex, with quite significant costs compared to the cost of machines. The cooperation with CenTec has allowed Carpigiani to develop its own e-Maintenance platform, called Teorema, which allows machines to be remotely monitored and controlled, with innovative diagnostics and prognostics features and integrated within the corporate CRM. An iPhone App provides a business interface to the system, allowing Carpigiani's customers to fully appreciate the functionalities and economic advantages provided by the Teorema platform. Currently Teorema controls about 5,000 machines in more than 20 Countries and has allowed Carpigiani to completely reorganise the after-sales service with significant savings. Teorema allowed Carpigiani to improve the maintenance process, increasing the percentage of remote problem solving(phone-fix)and with a single on-site visit(first-time-fix). This led to a 25%+ after-sales service costs reduction.The modern computer technologies adopted for Teorema made inroads at Carpigiani:the new ice-cream machines include a new board with ARM processor and COTS and Open Source technologies not only for monitoring but for machine operability as well.
Carpigiani Group, Anzola dell’Emilia (BO) CenTec
The collaboration with Carpigiani has led CenTec to developing the required skills and expertise to develop innovative e-Maintenance platforms. i-Maintenance stems from this experience, and is therefore a mature service made available to companies for large scale remote control and monitoring of a wide range of automatic machines, systems and devices.
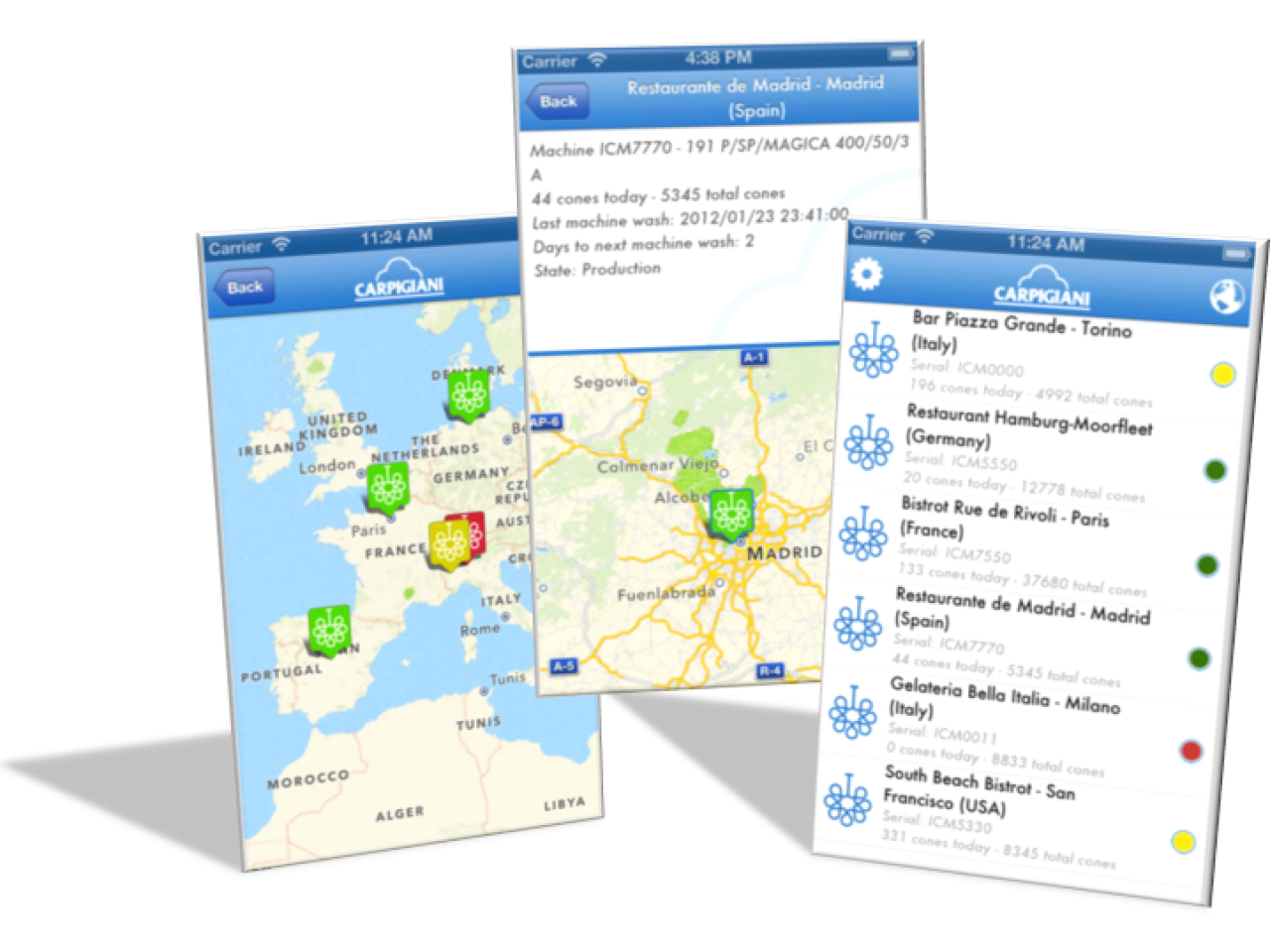