The choice of a light alloy for the production of mechanical components implies, also, the choice of the most suitable heat treatment. Even if heat treatment parameters are defined in the international standards, microstructure, induced in the alloys by production processes, strongly influences their effectiveness. Moreover components, that undergo different operating condition (e.g. temperature and/or environment), can improve their performances by means of customized heat treatment. For these reasons more and more companies are going to modify heat treatment parameters in order to completely take advantage of light alloys properties, increasing components reliability, optimizing production processes and consequently reducing production costs.
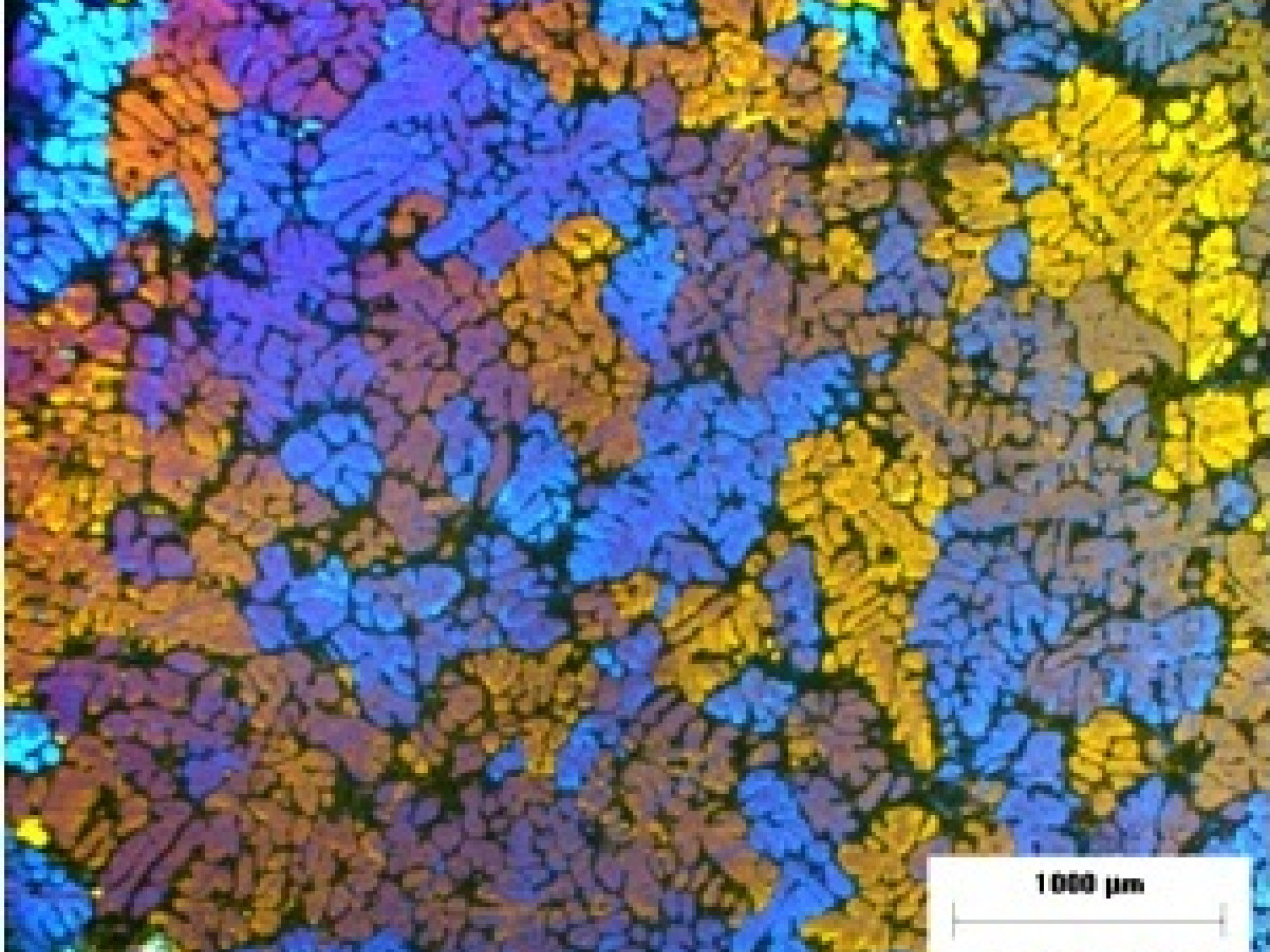
The approach allows implementing in process simulation software new correlations among: production process, microstructure and heat treatment. The integrated design, based on this software, is able to define the effect of production processes, heat treatments and alloy compositions on mechanical properties of components with complex shape. Designer could quickly design reliable components, reducing time for products development and costs.
-Optimization of both heat treatment parameters and components design, in order to obtain components with appropriate microstructure, high mechanical properties and reliability. - Lightening and increased reliability of mechanical components for applications in automotive, aerospace and automation
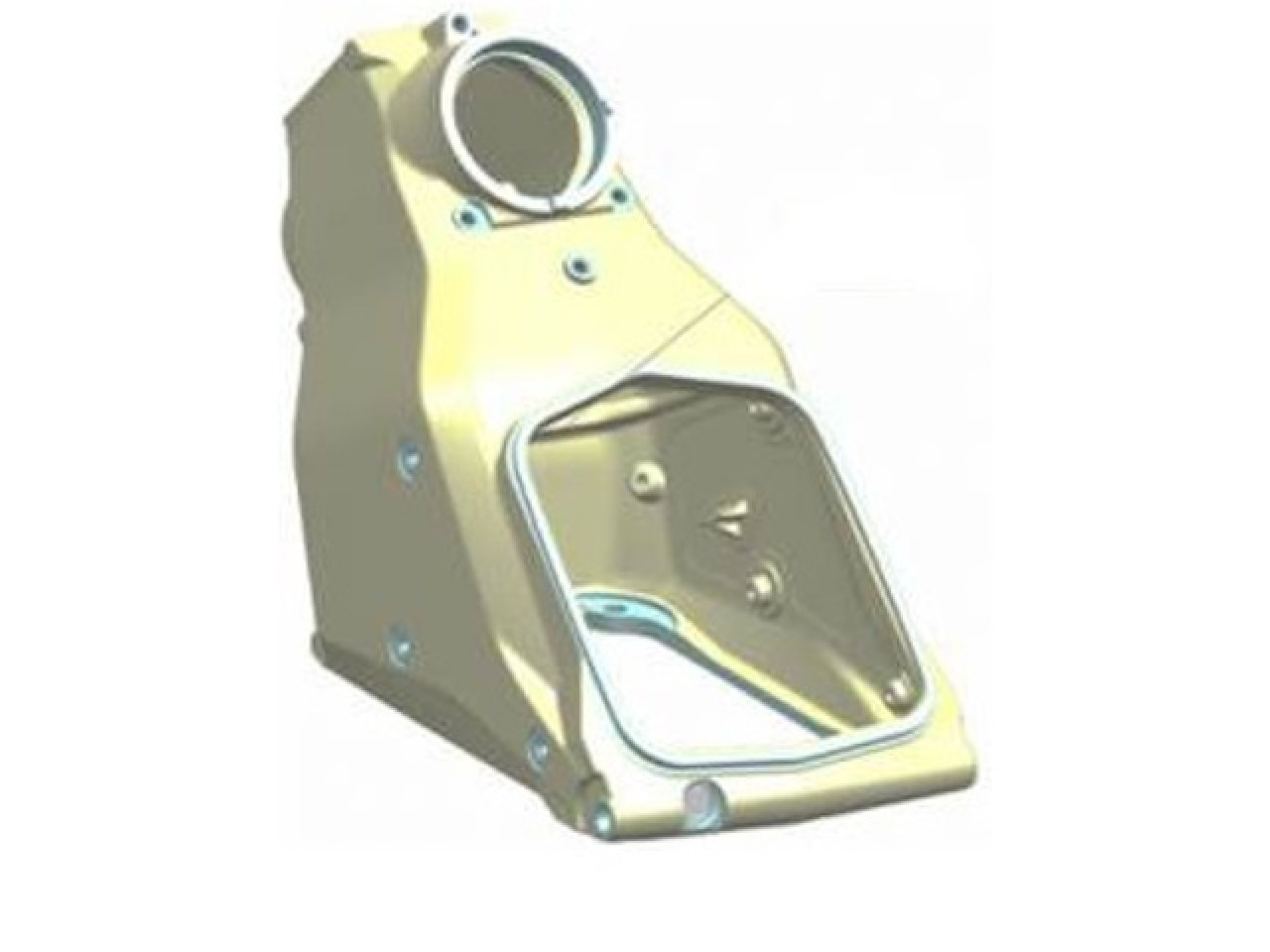
Effect of pre-aging duration on mechanical properties of A356 alloy after T6 heat treatment.
Heat treatment to increase strength of aluminium alloys is a three-step process: solution heat treatment (between 500 and 540°C); quenching; age hardening at room temperature (natural aging) or elevated temperature (artificial aging at temperature between 150 and 210°C). While quenching is carried out immediately after solution, artificial aging is carried out with delay (up to 2 hours) respect to quenching. Even if this delay, called pre-aging time, has a strong effect on A356 mechanical properties after heat treatment, it isn’t considered by standards. The main goals of the study were: - To evaluate the effect of natural pre-aging durations up to 2 h on the tensile properties of samples with different microstructures - To assess the accuracy of heat-treatment guidelines, generally followed in industrial practices, optimizing heat treatment and production process The study lead to: - Reduce the duration of the heat treatment cycle of 1,5 hours - Increase mechanical properties of the alloy of about 10%.
Companies of the automotive sector
Similar activities have been carried out in collaboration with several companies of the region. These studies lead: to identify the heat treatment and production process parameters that influence light alloys mechanical properties; to develop innovative heat treatment and processes.
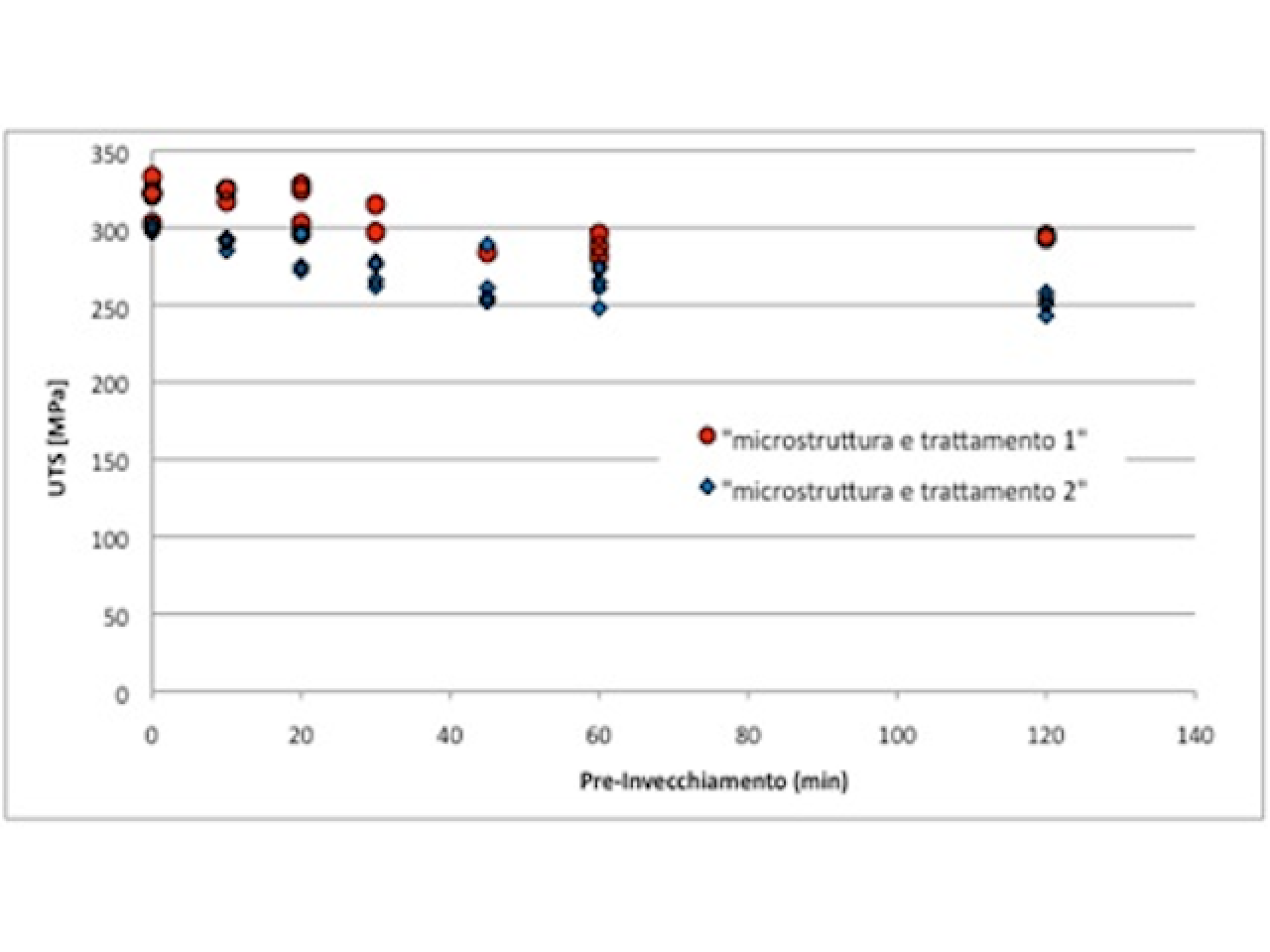