An automatic system for laser marking was developed in cooperation with Robby Moto Engineering (RME), by adding a vision system to a LASIT commercial marker. The system is able to recognize the pieces inserted in the machine and autonomously complete the marking process.
The operator is therefore relieved of manual positioning and handling operations of the laser head, maintaining the role of process supervisor.
Within the HUMANS - HUB research project was developed a solution that allows to automate a process of marking on small artifacts object.
The goal was to create a product capable of automatically recognize and mark the pieces present within the work area. From the MUSP consortium it was created a prototype by integrating a commercial machine LASIT with an array of 3 cameras and an automatic machine control software.
The process is therefore very simple: the operator put the workpieces on the machine and initialize the procedure, the machine then takes a picture of the working area and by segmenting the images it recognizes the objects present and performs the required processing.
The only additional data required are the CAD drawings of the parts involved with the position where the marking should be performed, and the Job file to be executed, prepared with the software LASIT FlyCAD, in which the geometry to be marked and the process parameters are reported.
With the introduction of a vision system inside the machine, consisting simply of 3 cameras, it is possible to automate the marking process, this makes the system easily retrofittable on any similar machine, therefore it is not limited to the LASIT model under consideration .
A second innovative aspect is the fact that it is not necessary to train the vision system for the recognition of the pieces, therefore it is not necessary to acquire a dataset of images of the models involved. The only input of the system, indeed, are the CAD models of the pieces to be recognized and the system can autonomously recognize if they are present in the work area.
The time used for the creation of supports and references to make the marking on each piece repeatable is eliminated with this system. Indeed it is possible to work on several pieces without having to manually adjust the position of the laser head.
With the cameras it is also possible to automatically carry out the quality control of the result obtained directly in the machine and to give feedback to the operator on the processing parameters to be corrected in the event of failure.
The recognition software is obviously independent of the type of application for which it was develped. In fact, this setup, consisting of a fixed vision system, allows you to automate a multitude of processes where the pieces to be machined do not have to be fixed further. Other robotic laser processing, pick and place of objects, automatic painting systems, etc. In case it was also possible to obtain the CAD models of the supports, the use of the system could also be extended to other mechanical machining in which it is necessary to know the position of the piece to carry out the machining
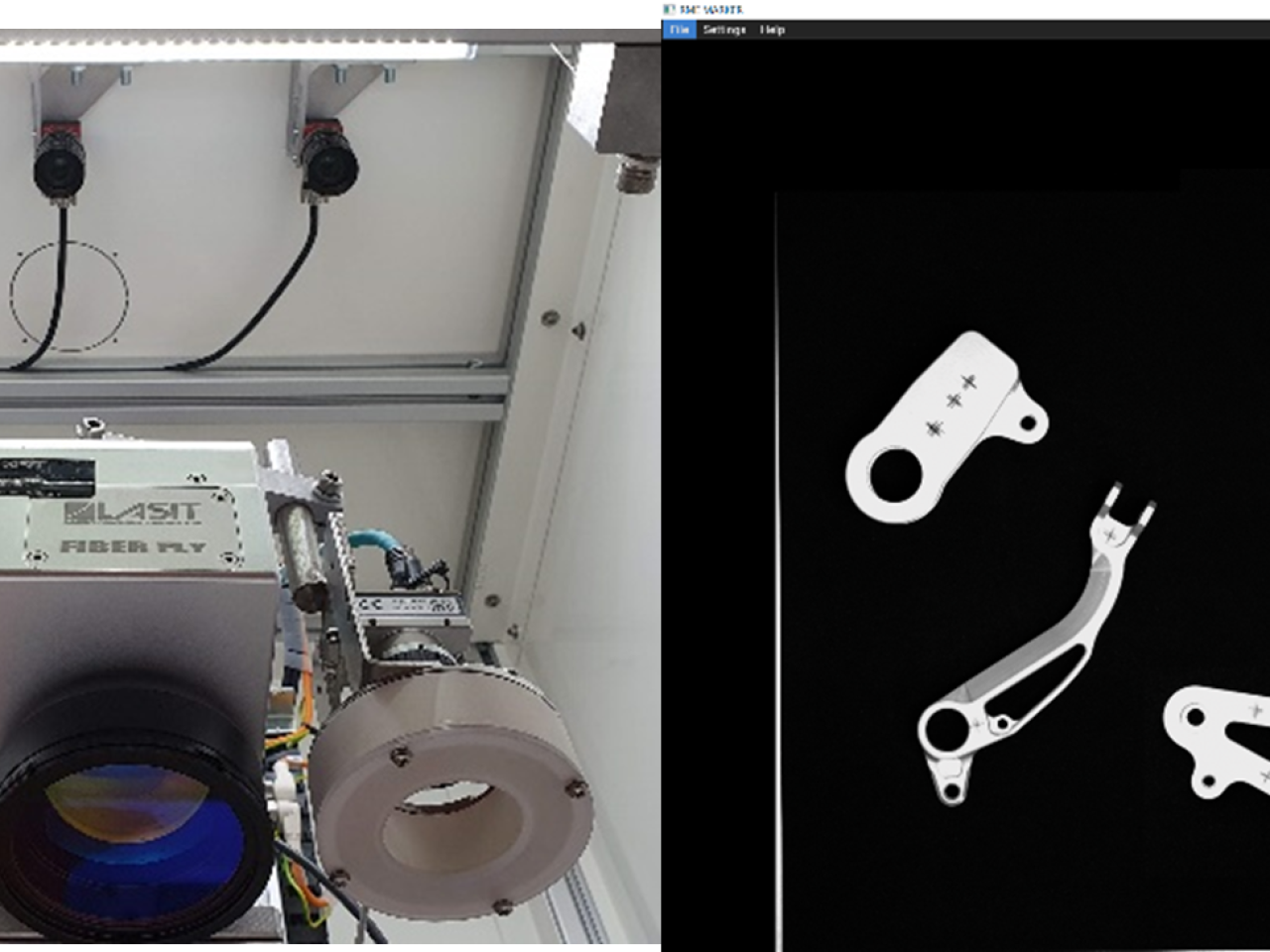
Traceability of production lots
The solution developed by MUSP was tested within a local SME, Robby Moto Engineering (RME), partner of the HUMASN-HUB project, and inserted within their production chain to allow the traceability of production lots. On each piece produced, RME needed to indicate a code that would allow the entire production cycle to be traced.
The vision system was then installed on their LASIT marking machine, within the production line, and tested to evaluate its operation on the tracking of orders by automatically applying a code to a series of parts.
It is currently in the testing phase and the level of positioning accuracy of the marking is ± 1mm. With further iterations in the calibration of the system or hardware modifications of the vision system we can aim to further improve the obtainable accuracy.
LABORATORIES:
- TECNOPOLO – MUSP
COMPANIES:
- RobbyMotoEngineering
- REI - Reindustria Innovazione
Together with the project partners we are in contact with the marker manufacturers to evaluate the integration of the MUSP software in the related control systems and to further optimize and improve the system.
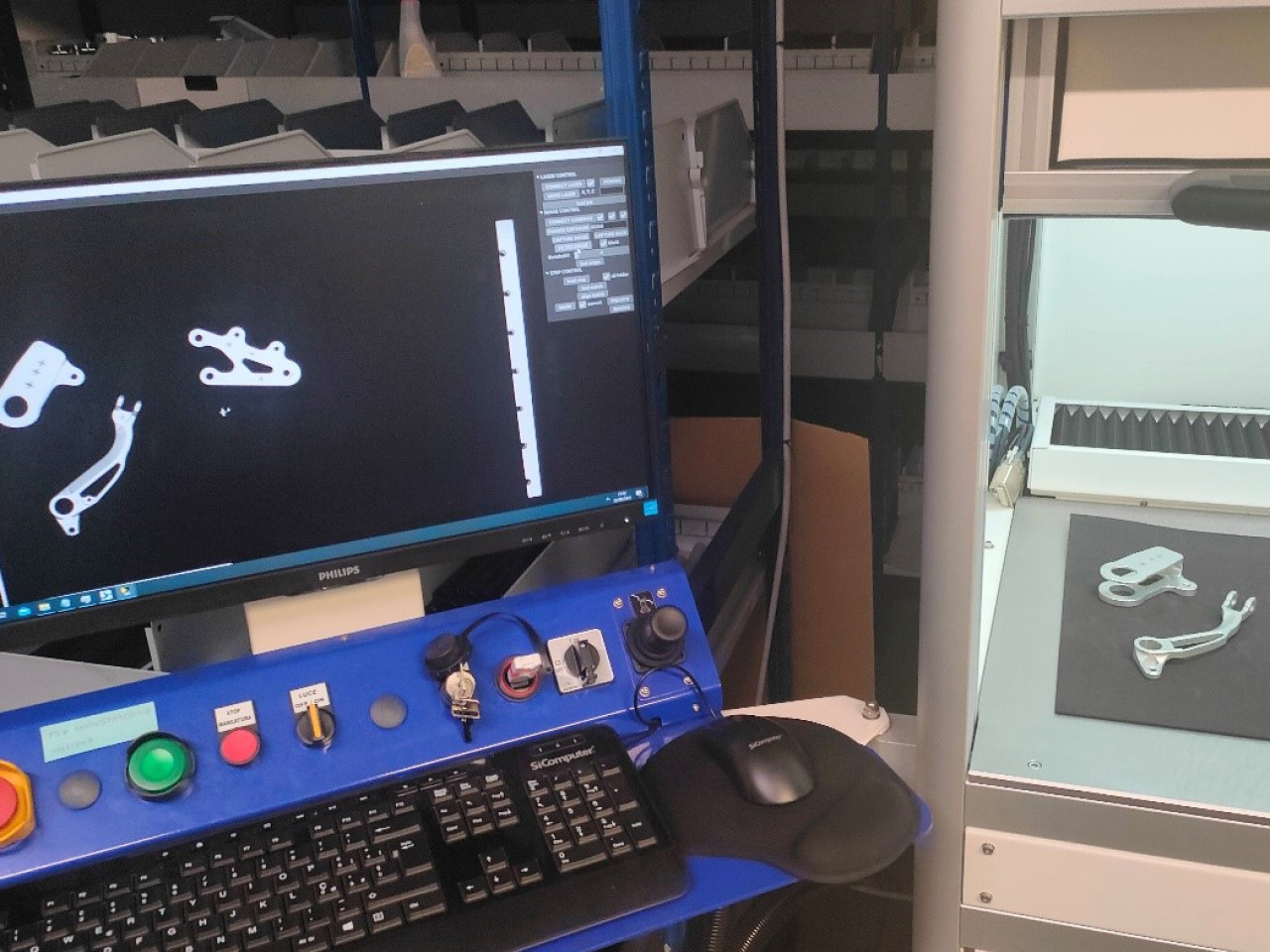