Motion planning for robotic manipulators is usually considered a problem with well-settled solutions. However, also in this field, new applications, often non-standard, pose new challenges. Among them, the transporation/manipulation of liquid materials is a problem of great significance because of the wide application range and its peculiarity. As a matter of fact, the handling of liquids needs a specific care in order to avoid the spilling caused by the sloshing phenomenon. The trivial solution consists in a severe reduction of velocities and accelerations, but the adoption of proper techniques, such as the ones developed in this project, leads to performances similar to the ones that can be achieved with solid materials.
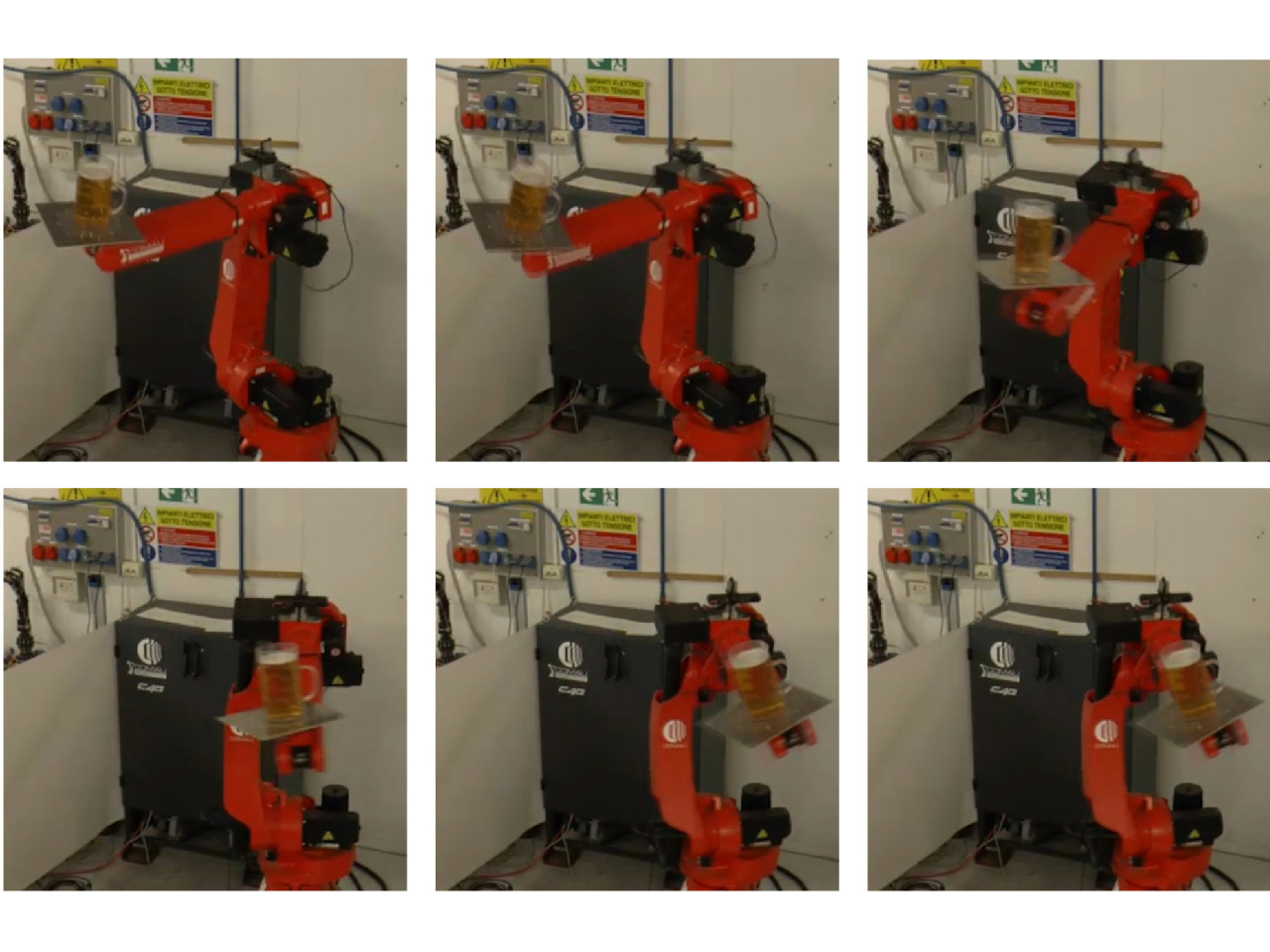
The proposed technique allows to safely manipulate containers with liquids in the same manner of solid objects, being able of drastically reducing sloshing phenomena. This approach exploit the orientation of the robot end-effector that in pick-and-place operations is usually kept fixed, exploiting in this way all the degrees of freedom of the manipulator. Moreover, the proposed method allows to move objects that are not constrained by the end-effector but that simply lie on a support located at the robot tip.
The proposed planning and filtering methods can be applied in all those activities in which robotic systems are used for the manipulation of liquid materials, in particular, in the field of food processing. Additionally, the algorithms can be applied to the robotic tasks in which the objects to be moved cannot be grasped.
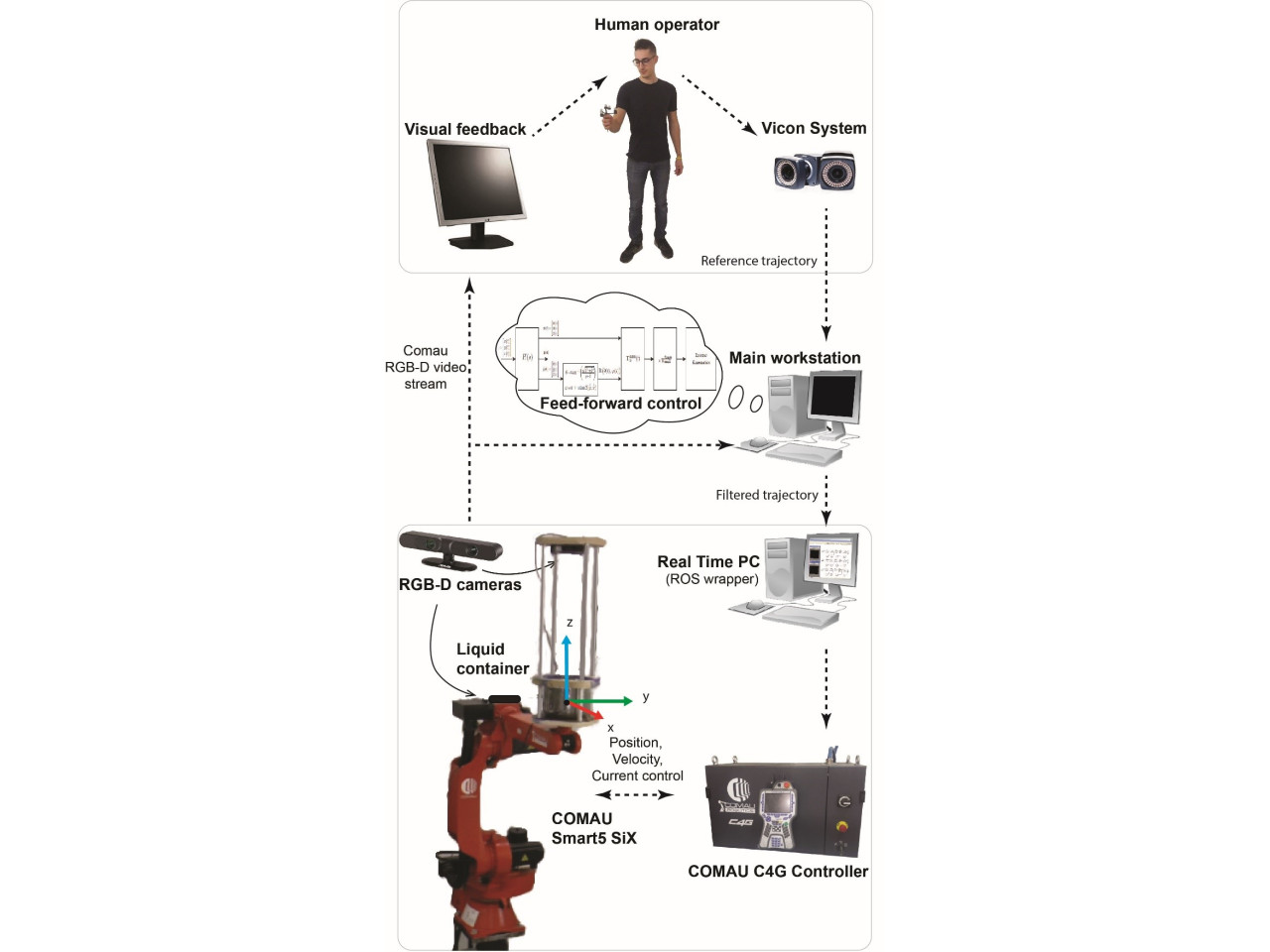
The proposed techniques for motion planning with sloshing suppression capabilities have been used to design a sort of robot waiter able to move a container filled with liquid without spilling on the basis of the user commands.
In order to prove the effectiveness of the proposed method, several tests have been performed with an industrial robot carrying a container filled with liquid. In the proposed planning and control architecture the position of the container is directly commanded by the human operator. In this way the complete independence of the filter for sloshing suppression from the reference position is guaranteed. The filter is designed on the basis of the liquid characteristics and, besides a smoothing action on the input trajectory, it changes the orientation of the container in order to compensate for lateral accelerations. In this way, the motion of the liquid surface is drastically reduced. The same compensation acts on the inertial forces acting on the container, which therefore can be simply leant on a tray connected on the robot flange without grasping mechanisms. This approach can be profitably adopted for designing a sort of robot waiter.
LIAM - Laboratorio Industriale Automazione Macchine per il packaging IMA - Industria Macchine Automatiche SACMI Imola
The algorithms developed in the SINERGIE project have been presented in the main international conferences on robotics. A video, showing the achieved results, is available in the online magazine IEEE Spectrum (https://youtu.be/JMVJ9w7KFQg).
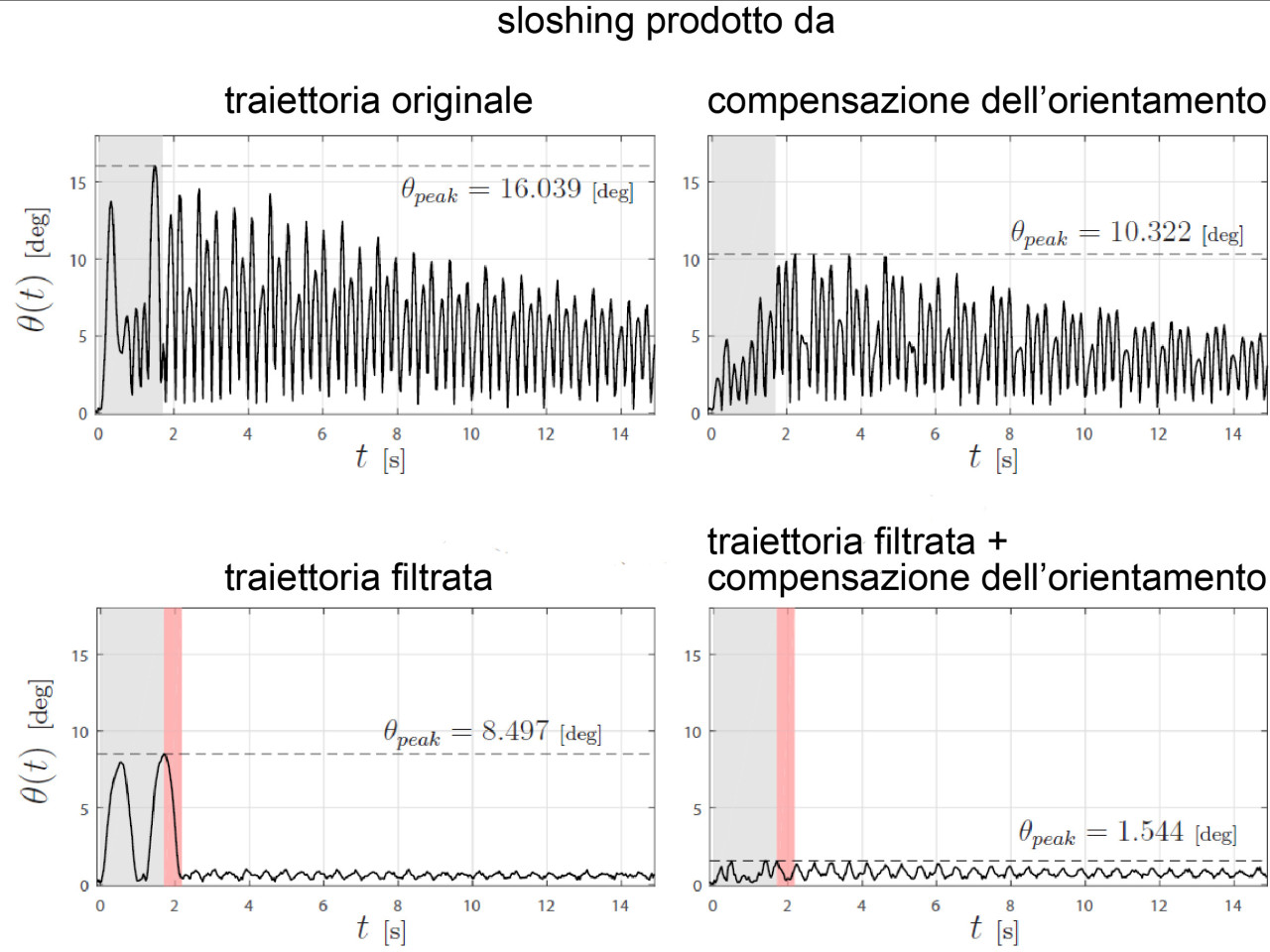