Today, there is a strong industrial demand for integrating new functions on machines and plants, to make them more and more intelligent. In this context, condition monitoring is a crucial point. Using techniques that allow evaluating the state of health of machines and plants in working conditions, is it possible to schedule an early maintenance intervention, implementing a predictive maintenance strategy. SMEDIP project aims to develop sensors and methods for predictive diagnostics in the field of automatic machines, in particular in the packaging sector. This complete condition monitoring system is extremely appealing for mechanical factories, in particular in the field of motors and machines.
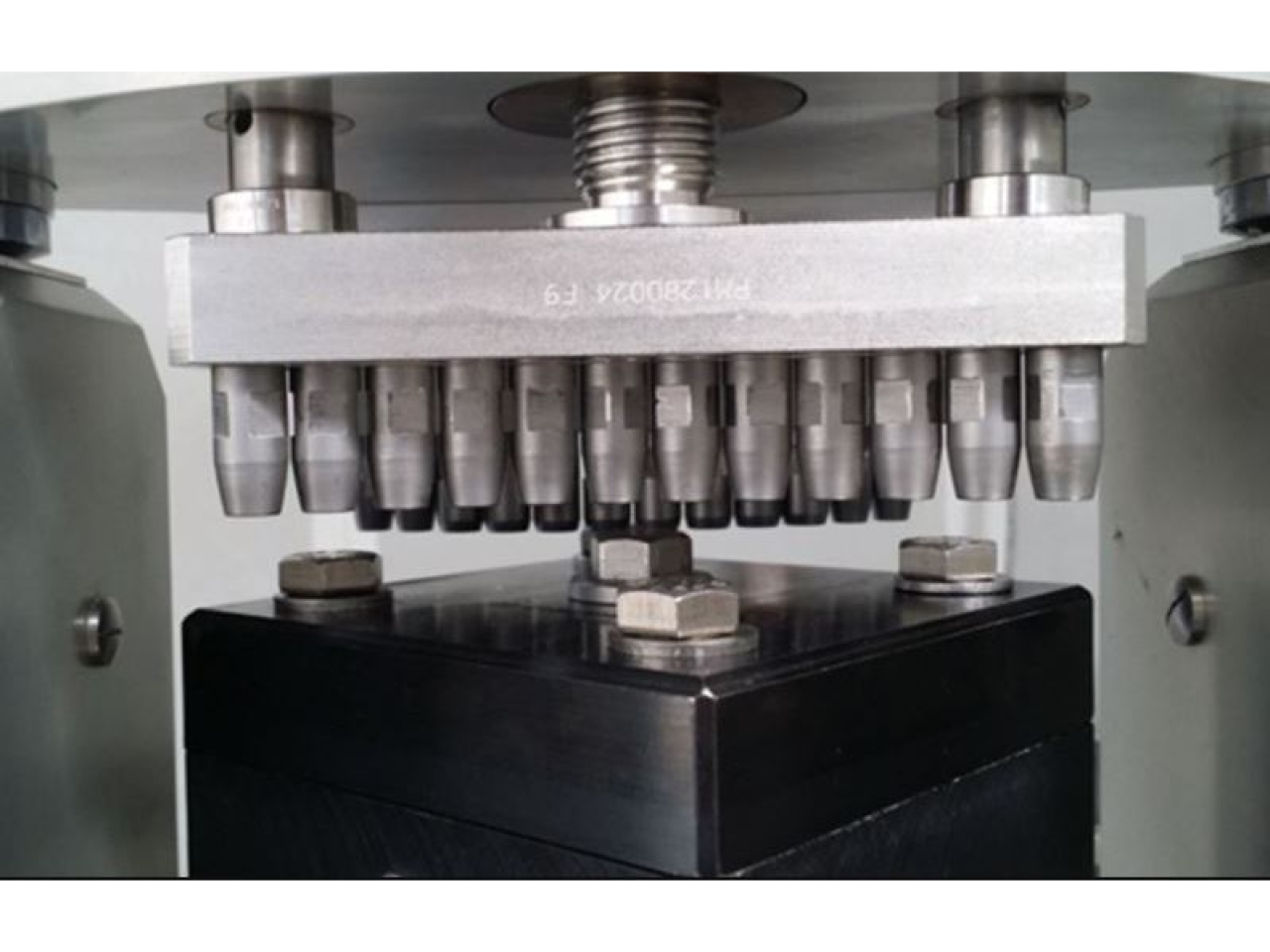
The system developed in this project features aspects that make them unique at the moment. Technical characteristics like the range of accelerations, measured along 3 orthogonal directions, the frequency band, the precision, and the wireless communication cannot be found together in a single device. The realized software includes advanced diagnosis algorithms that analyze the signal and relates it to the state of health of the machine.
The applications of the know-how developed within the project range in the whole mechanical sector, but they go also further because monitoring the vibrational state of whatever productive system that involves mechanical components is like making a snapshot of the system. A correct interpretation of the collected data in conjunction with suitable diagnostics algorithms can provide a predictive-diagnostics system that works in different industrial fields.
Wireless diagnosis system can be applied where the geometry of the machine does not allow wired instrumentation, like for example rotating parts.
A SMEDIP sensor prototype was tested in SACMI, on a typical packaging machine, a plastic cap maker with a rotor equipped with 64 molds. The sensor worked in parallel with a PCB Piezotronics sensor to compare with. Measurements on a pump resulted in agreement both in amplitude and frequency distribution. The most significant measurement was that on the revolving part, where no comparison was possible since the reference instrumentation is wired and it cannot be mounted on that part of the machine. Results were very satisfying, indeed radio connection was very stable during the rotation and it was collected data from one whole cycle, which took few seconds. Single molds were detected, with intensity proportional to the distance from the sensor, and analyzed with Fourier analysis.
MIST E-R REDOX Consorzio LIAM Fondazione Democenter-Sipe SACMI
No patents were registered. At the moment the system was showed to few companies and it will be used to evaluate vibrational levels in the machines
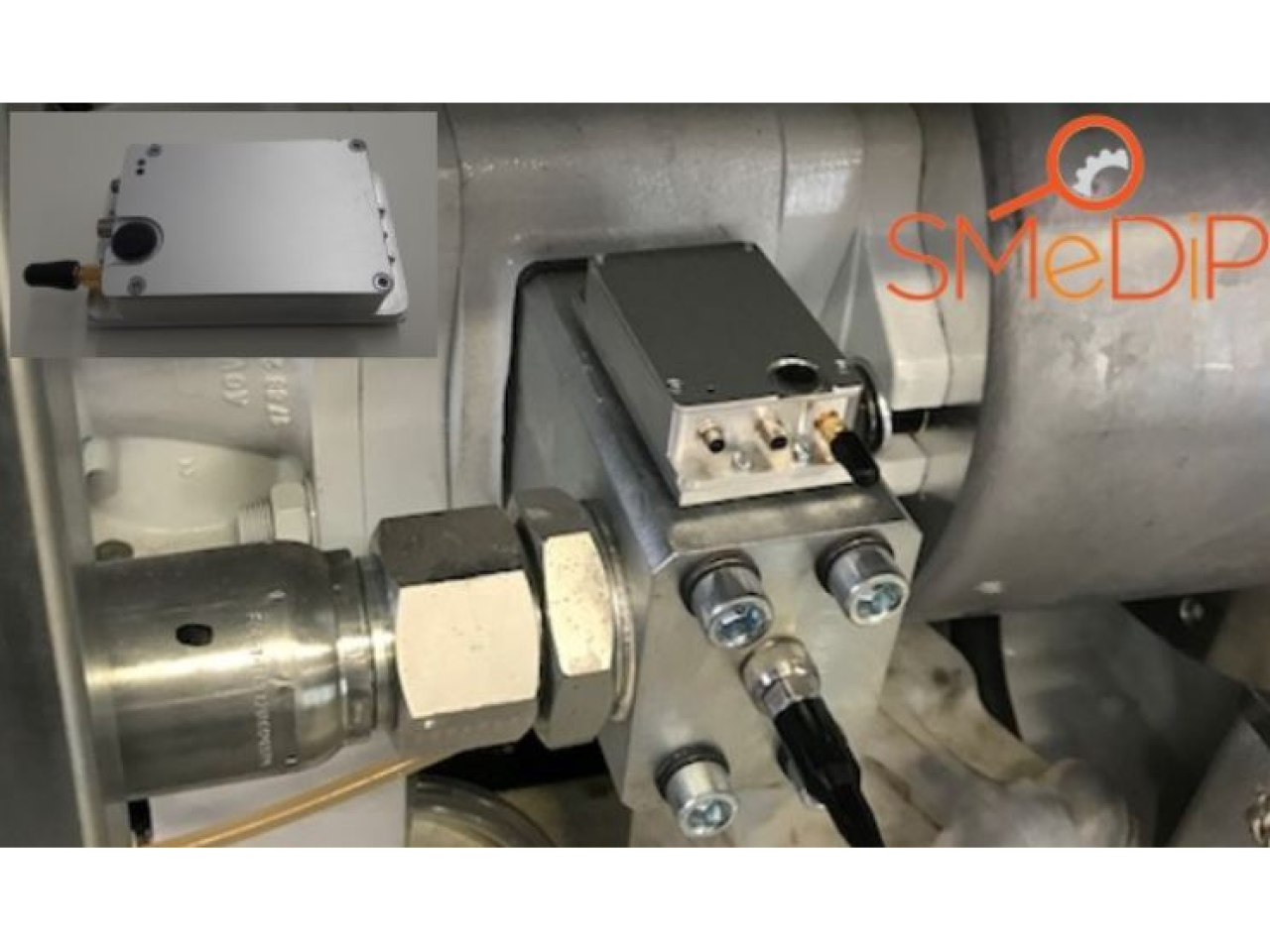