The mechanical characterization leads to define the limits of use of a material for a specific application, identifying its mechanical properties. This activity is performed as an essential part of the development of new processes and materials, and for service activities targeted at industry. The acquired expertise and facilities of the ENEA Faenza research laboratories, allow to test materials and components, even at high temperature, under operating or accident conditions. The typologies of materials mainly characterized are: monolithic ceramics and composites, polymeric matrix composites, metals and building materials. Activities include: quasi-static and dynamic standard tests, data processing and statistical analysis of results. Moreover, designing and developing mechanical testing, even non-standard, can be performed, also with the support of finite elements calculations and reliability analyses.
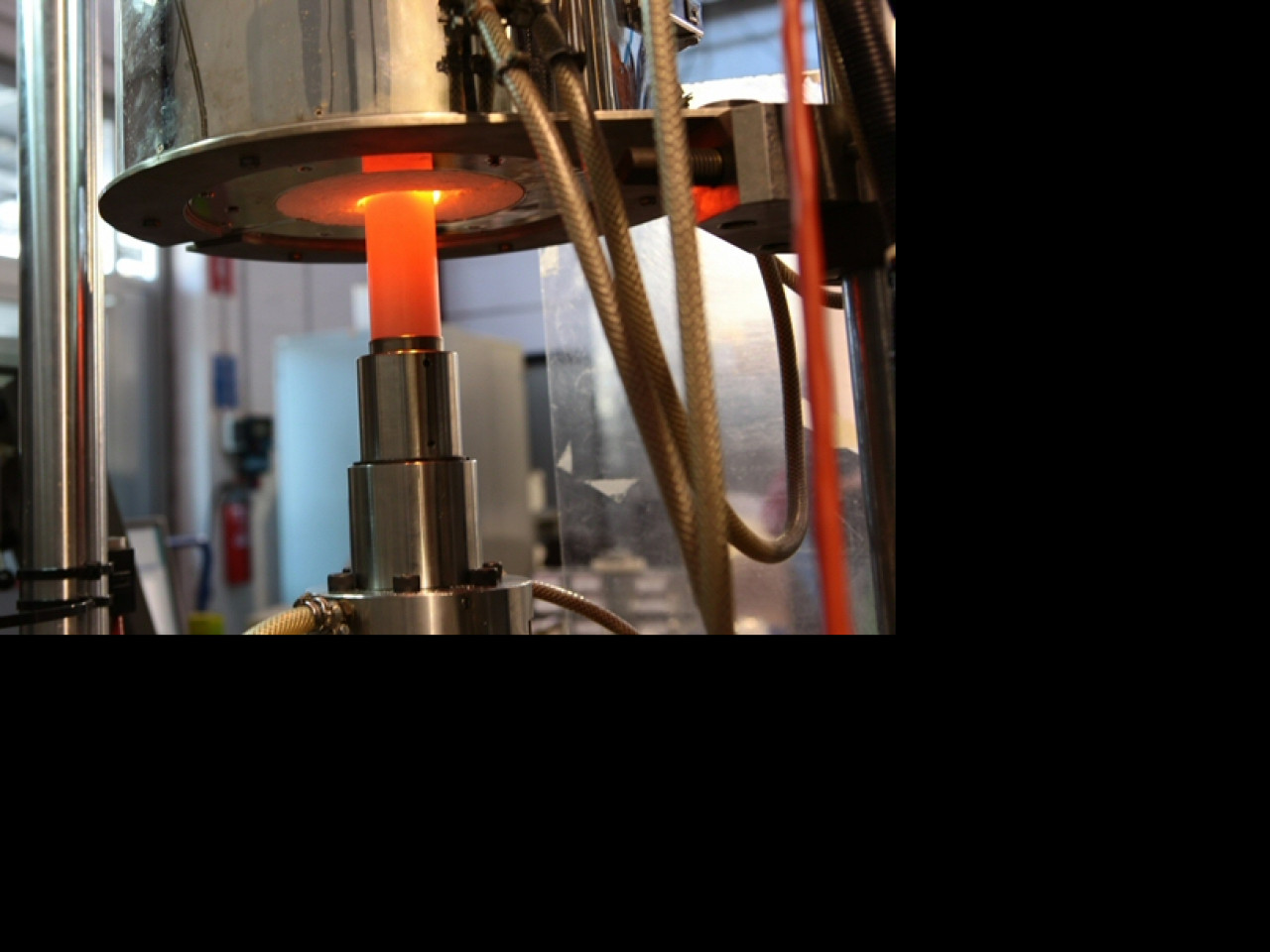
The mechanical characterization allows to detect the mechanical properties and the constitutive equations of a material also at high temperature. The study of the mechanical behaviour of new materials, the experimental qualification of new structural components and the validation of numerical models, allow the development of new production processes. The knowledge of mechanical properties leads to correctly design and realize components and structures, and subsequently allows to verify, by qualification tests, their mechanical behaviour, under standard or operating conditions.
The mechanical characterization is performed on ceramics, fibre-reinforced composites (ceramic or polymer matrix), metals and building materials. The main mechanical tests, carried out at room and high temperature, are: tensile, compression, bending, fracture toughness, creep, fatigue, torsion and pressurization. The qualification of components and prototypes, targeted to the industrialization of the product, is carried out by means of resistance tests (quasi-static and/or dynamic), also at high temperature, simulating operating or accident conditions (up to rupture).
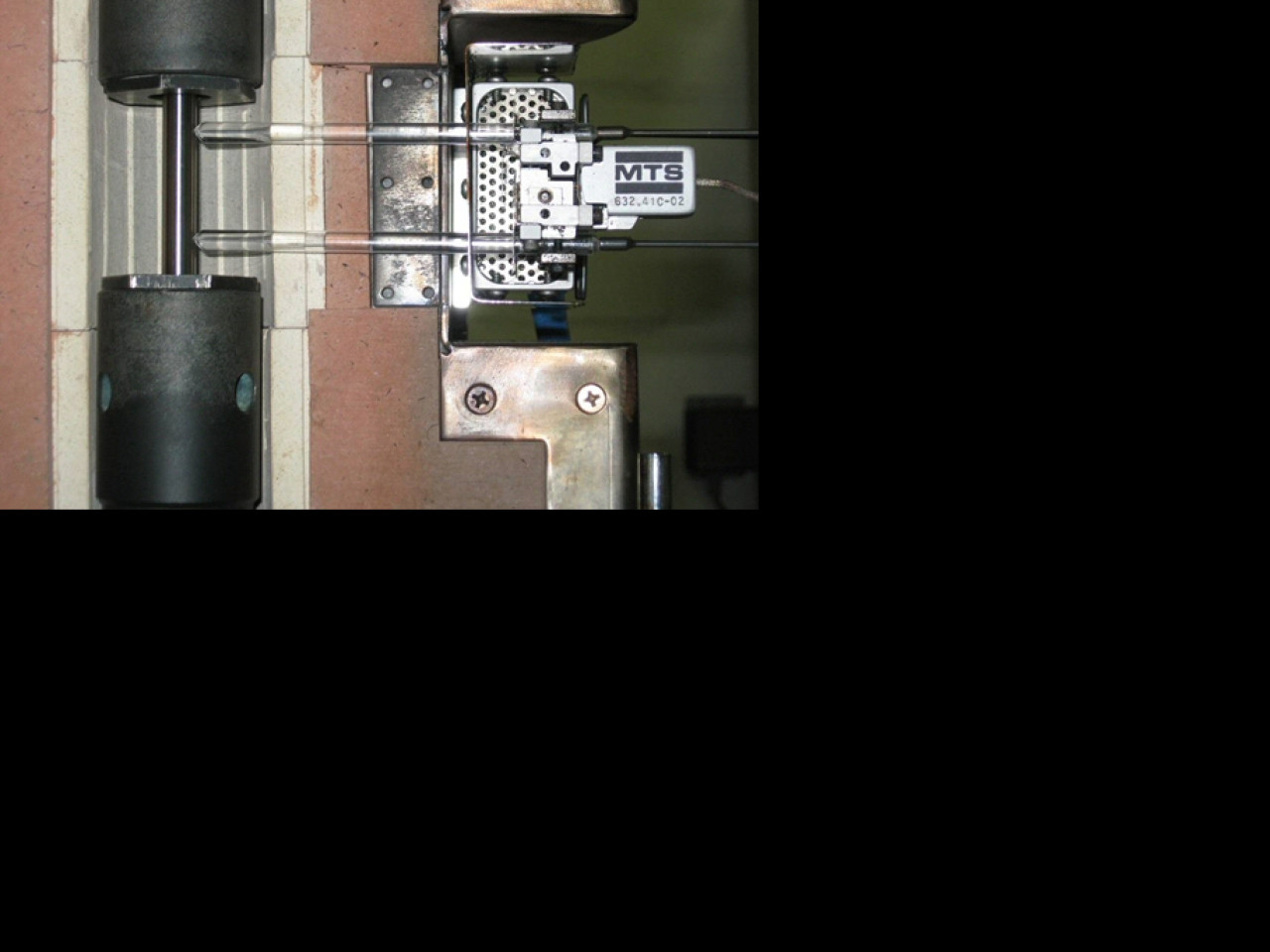
Formula 1 Side Intrusion Test
The Side Intrusion Test is a qualification test performed on composite panel, in accordance with FIA. The test method aims to represent the conditions by which the survival cell structure is loaded during a side impact. A conical impactor represents the loading conditions of a Formula 1 nosecone during a side impact accident. The tested panel is a composite system, generally consists of an inner core of aluminium honeycomb, coated on both sides with plies of prepreg with long fibres of carbon, glass, kevlar, zylon, etc. The panel is approved if no abnormal ruptures are present and if the requirements of FIA standards are satisfy, in terms of achieved maximum load and of energy absorption in the first 100 mm of intrusion. The Side Intrusion Test is conducted in ENEA Faenza from several years, on demand of Italian race car industries. This represent an example of activities that allow to maintain a strictly collaboration with companies producing race cars, opening up the possibility for joint research activities. The specific sector is characterized by an increasing development, with continuously research in new performance materials. Moreover one of the ENEA institutional tasks is to provide advanced services and place the expertise and instrumental equipment at enterprise's disposal.
Scuderia Toro Rosso, Ferrari, Dallara Automobili, HP Composites, Ycom, ARS-Tech.
The number of intrusion test performed in ENEA Faenza research laboratories, is considerably increased in recent years. The collaboration with race car companies led to a diversification of the services provided, and to an increase in applications for high-tech services with new companies.
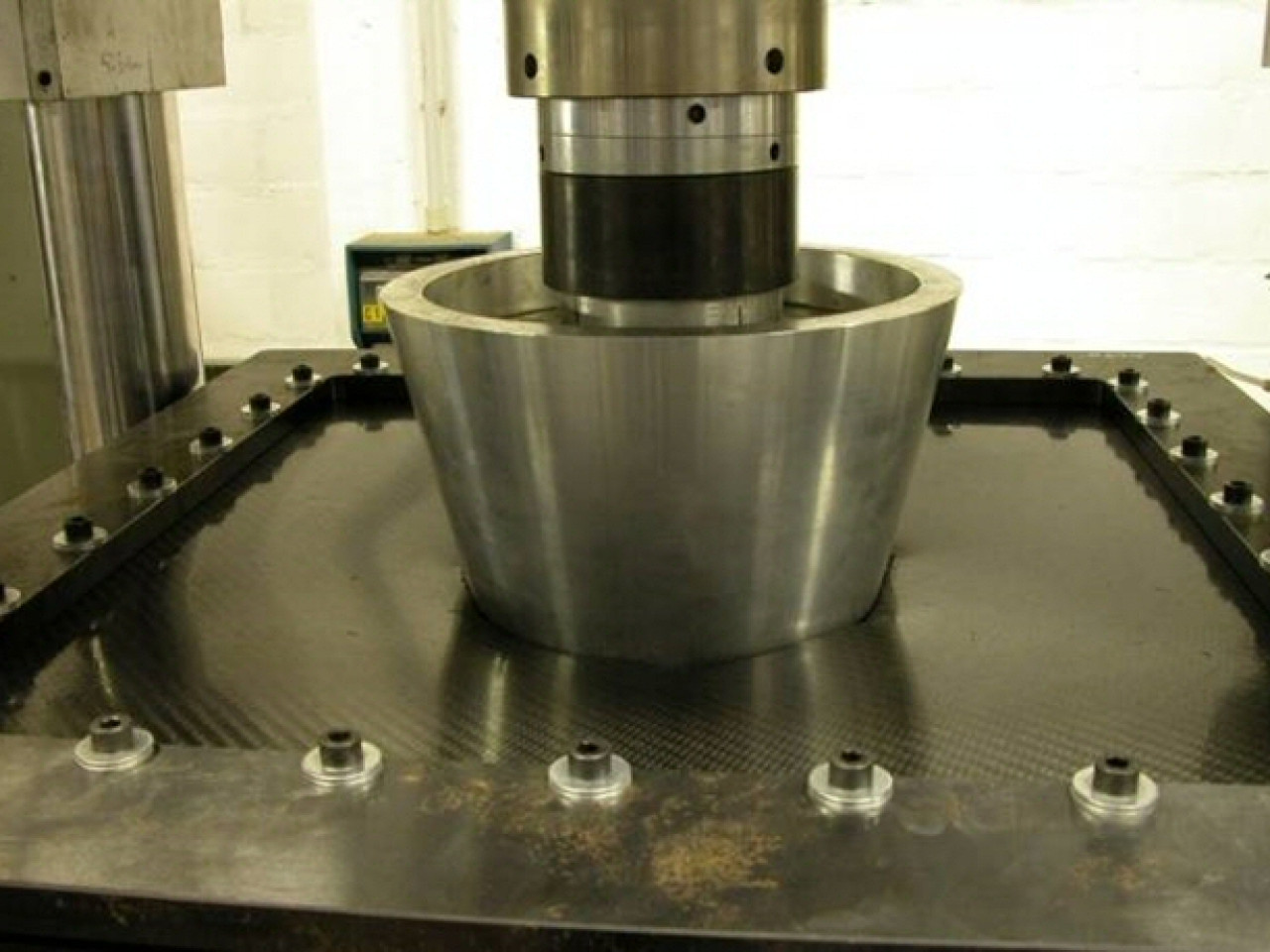