In the field of automatic machines and Robots with high dynamics the need for velocities higher and higher collides with the requirements of precision and reliability. This is mainly caused by the motion control systems that are not able to track reference signals with a frequency spectrum too wide and by the kinematic chains that transmit the motion, which are often sources of vibrations due to structural elasticities. For this reason in the choice of the reference signal it is necessary to go beyond the traditional approach that takes into account only kinematic constraints (on speed and acceleration) and to consider the dynamic characteristics of the actuation system and motion transmission. In this perspective new motion profiles and new analytical tools have been developed, which allow to generalize the double-S trajectories, which are de facto a standard in the industrial field, and to optimize the choice of motion profile parameters in order to minimize vibrational phenom
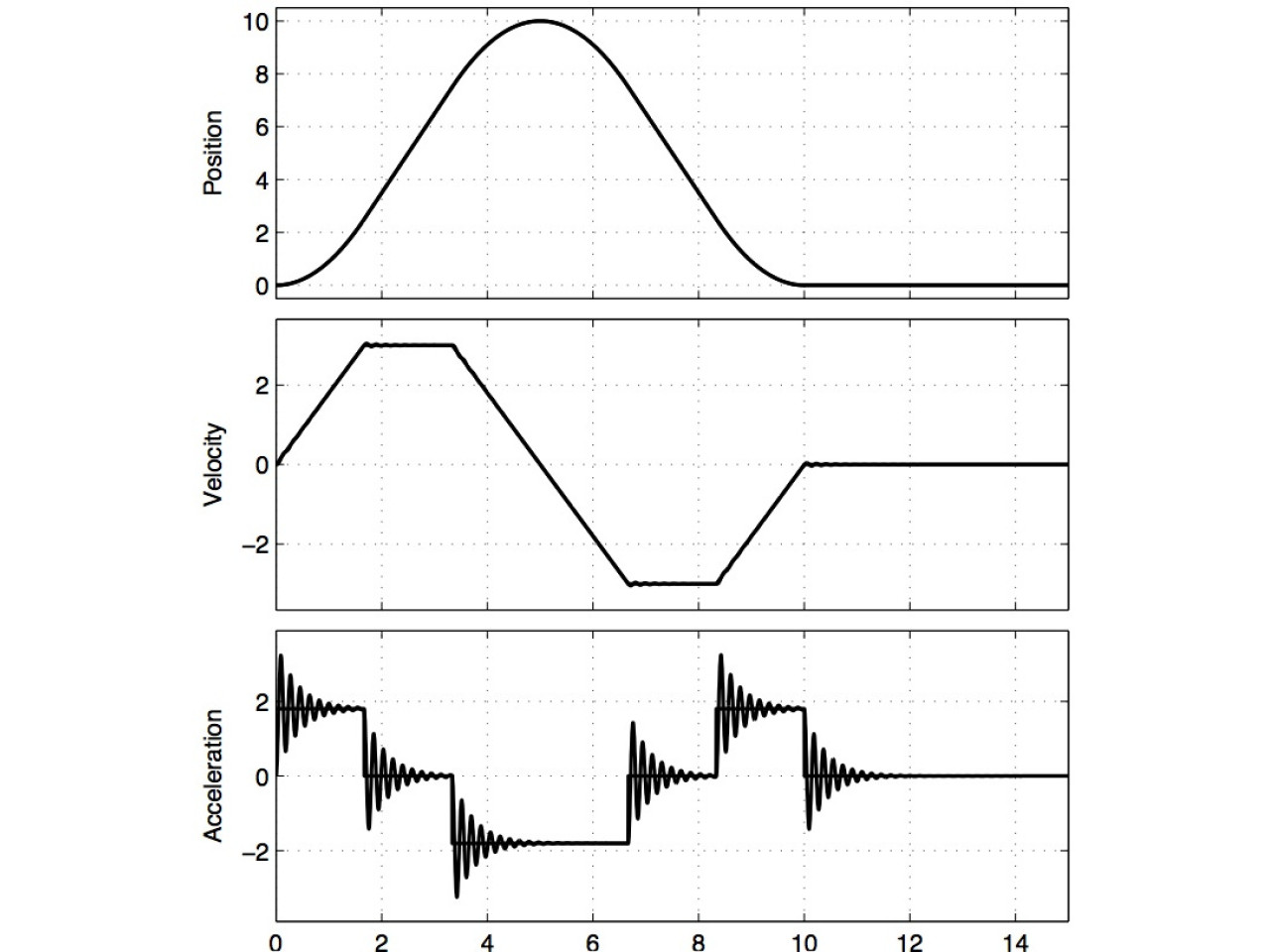
The proposed techniques for trajectory generation are an improvement of double-s trajectories, commonly used in the industrial practice, for two main reasons: 1) They allow to plan the motion profile in real time, for instance when an external signal is activated. Furthermore, the proposed trajectory generator combines a very high level of flexibility with an excellent computational efficiency, since the computational burden required by the proposed method is comparable with that of the double-S trajectory based on its analytical expression. 2) The proposed trajectory generator provides motion profiles compliant with kinematic limits on speed and acceleration, but also with dynamic constraints that may descend from the actuation system and the plant, e.g the eigenfrequencies of the whole system.
In all the automatic machines working at high speeds the use of the proposed algorithms for trajectory generation would have the advantage of reducing the vibrations being the cycle time equal or reducing the cycle time for a given level vibrations which is considered tolerable. In the design phase of the machine, the use of the proposed algorithms for motion planning along with new tools for the design/analysis, such as multi-body simulators and software for numerical analysis and dynamic simulation, would lead to a global optimization of the plant. Finally, it is worth noticing that the proposed trajectory generator, which works in real-time, can be profitably used in all those applications where a given movement depends on external events not predictable a priori.
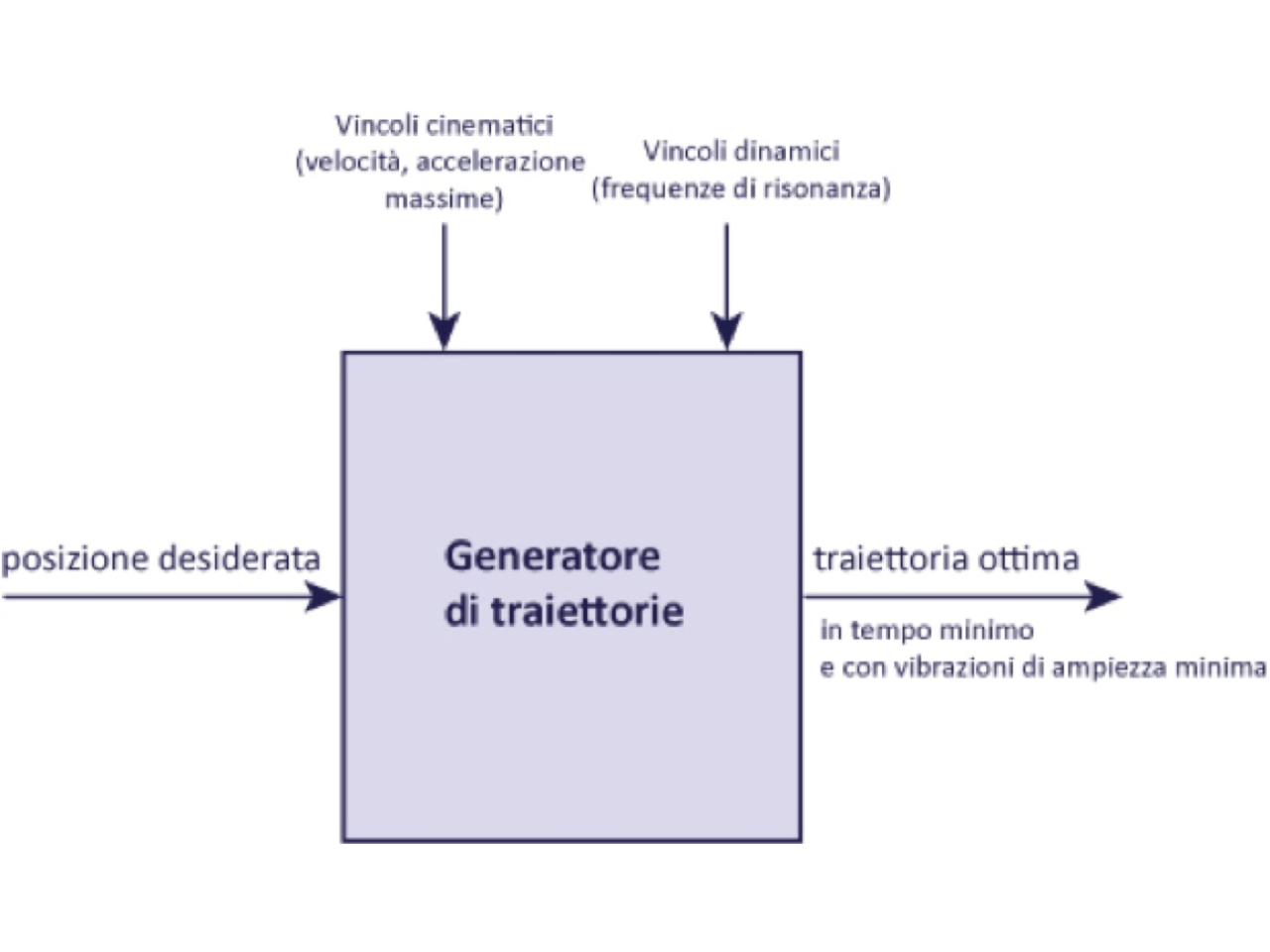
Motion laws for the vibrations minimization in a robotic application for pick-and-place
In this application a Delta robot is used for pick-and-place operations. Because of the noticeable accelerations, the robot induces vibrations in the carrying structure. These vibrations can damage the structure itself. The standard solution to the vibration problem consists in increasing the rigidity of the structure, in order to raise the resonance frequencies, with a consequent increase of the overall dimensions and costs, or in increasing the cycle time of the operations in order to reduce the frequency spectrum of the trajectory at high frequencies. Active vibration damping would require a modification of the robot controller and is usually infeasible in commercial robots. Therefore, the only degree of freedom remains the optimization of the reference position. For this aim, a program that performs both multi-body simulation (for the simulation of the robot) and finite element analysis (to study the behavior of the support) has been used to analyze the influence that the choice of a particular trajectory has on the mechanical system. By generalizing the techniques proposed for the suppression of vibrations in automatic machines to the multi-dimensional case, a considerable reduction of vibratory phenomena has been obtained by maintaining the cycle time unaltered. The optimization of the motion profiles and the dynamic analysis led to a twofold result: the motion profiles used allowed a reduction of the cycle time of the 50% with the same amplitude of the vibrations general guidelines for the design of the carrying structure have been deduced; a symmetric structure, with the same resonant frequencies along the different directions of the plane, allows a better optimization of the trajectory
IMA SpA Companies working in the field of automatic machines
The proposed methods for trajectory planning have been successfully applied to a number of motion control systems
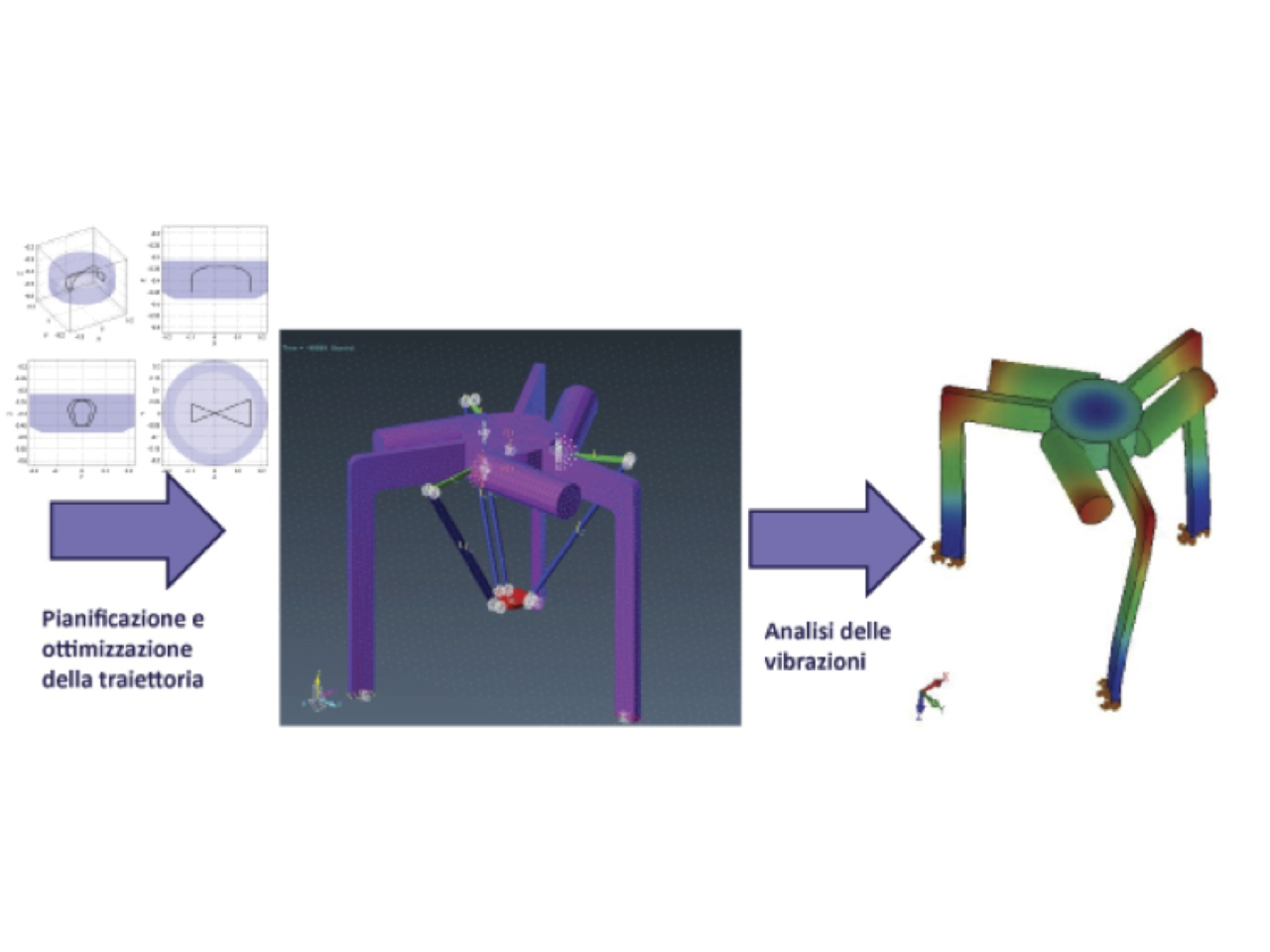