The assessment of product quality using objective techniques and the identification of defects or malfunctions during testing play an increasingly dominant role in enterprises. These objectives may often be pursued by studying the vibratory signal, which may enclose invaluable information on the machine/product's health status. This is the framework for the development of dedicated hardware and software systems, to detect defects, malfunctions and for end-of-line quality control through the analysis of vibrations. Dedicated and customised solutions are provided, which include: adequate vibration sensor to be used, acquisition system, user-friendly software designed according to the company's specifications, know-how transfer to the company's personnel.

• Total customisation of software and users' graphic interfaces; • Ability to identify defects and malfunctions with non destructive testing • Ability to implement the most advanced analysis techniques for very complex systems.
The product may be used for quality control and early diagnosis of defects in various types of mechanical systems. To date, MechLav has developed these systems in the following sectors: detection of pitting defects, of errors of pitch, profile, eccentricity in gear wheels and gearboxes; detection of defects in bearings also linked to poor lubrication and wear; monitoring of the health status of automatic machines and belt handling machines.
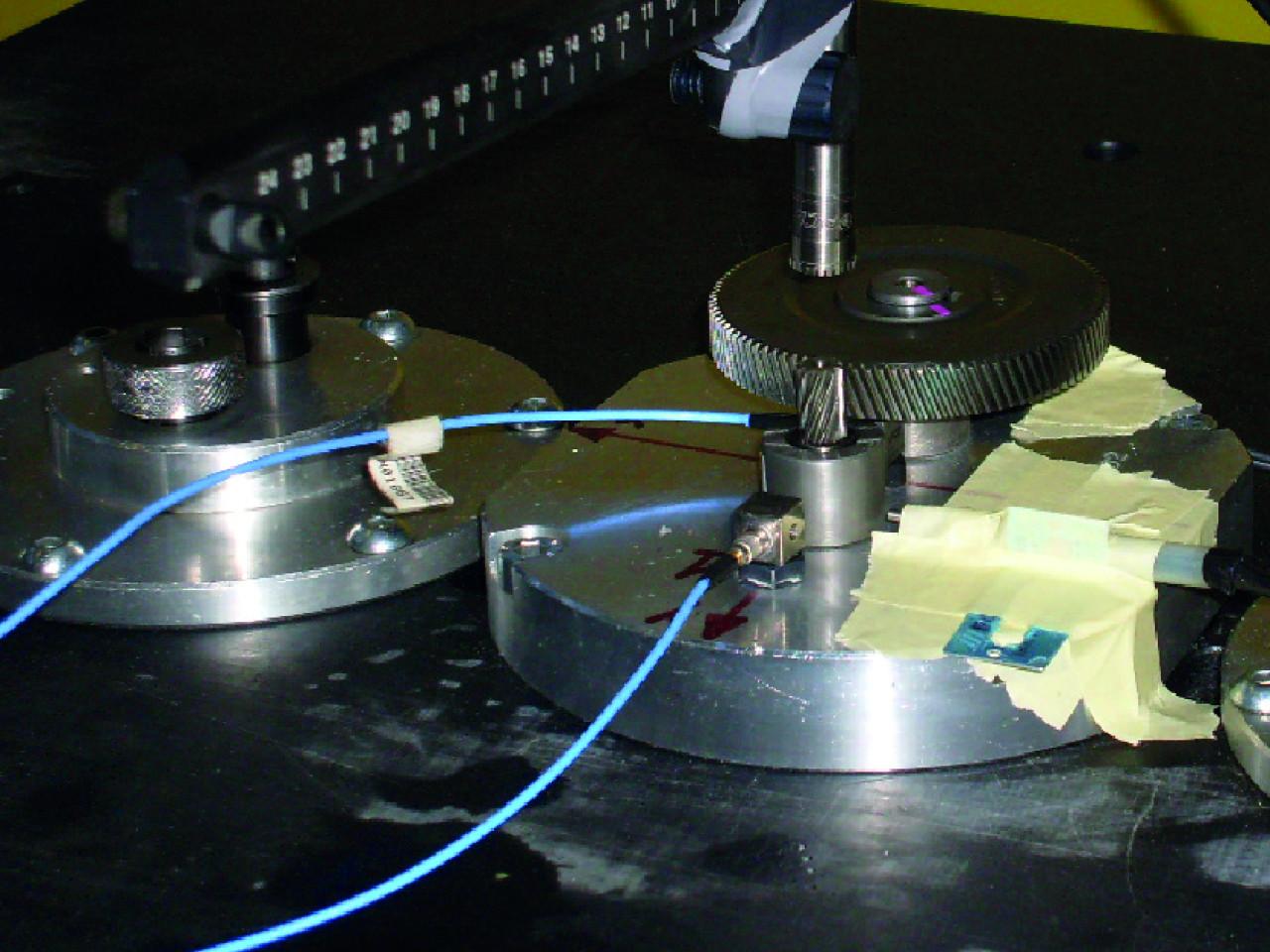
Quality control of polyurethane wheels
A hardware and software system for quality control of industrial conveyance polyurethane wheels was developed for the company Tellure Rota. Specifically, the company's requirement was to identify with non destructive tests possible bonding defects between the polyurethane tread and the cast iron hub. The use of a vibration sensor and a tachometer sensor to detect the wheel's instantaneous velocity during the test, and adequate post-processing, have allowed all possible defects to be detected. The user interface of the software developed was customised based on the company's requirements. High automation of testing processes; reduction of product development times and costs; objective defect detection.
Tellure Rota SpA – 41043 Formigine (MO)
MechLav is interested in developing this kind of projects with other companies, with the aim of developing hardware and software systems for diagnostics and quality control to best address the company's needs, identified with close interaction with the company's research engineers.
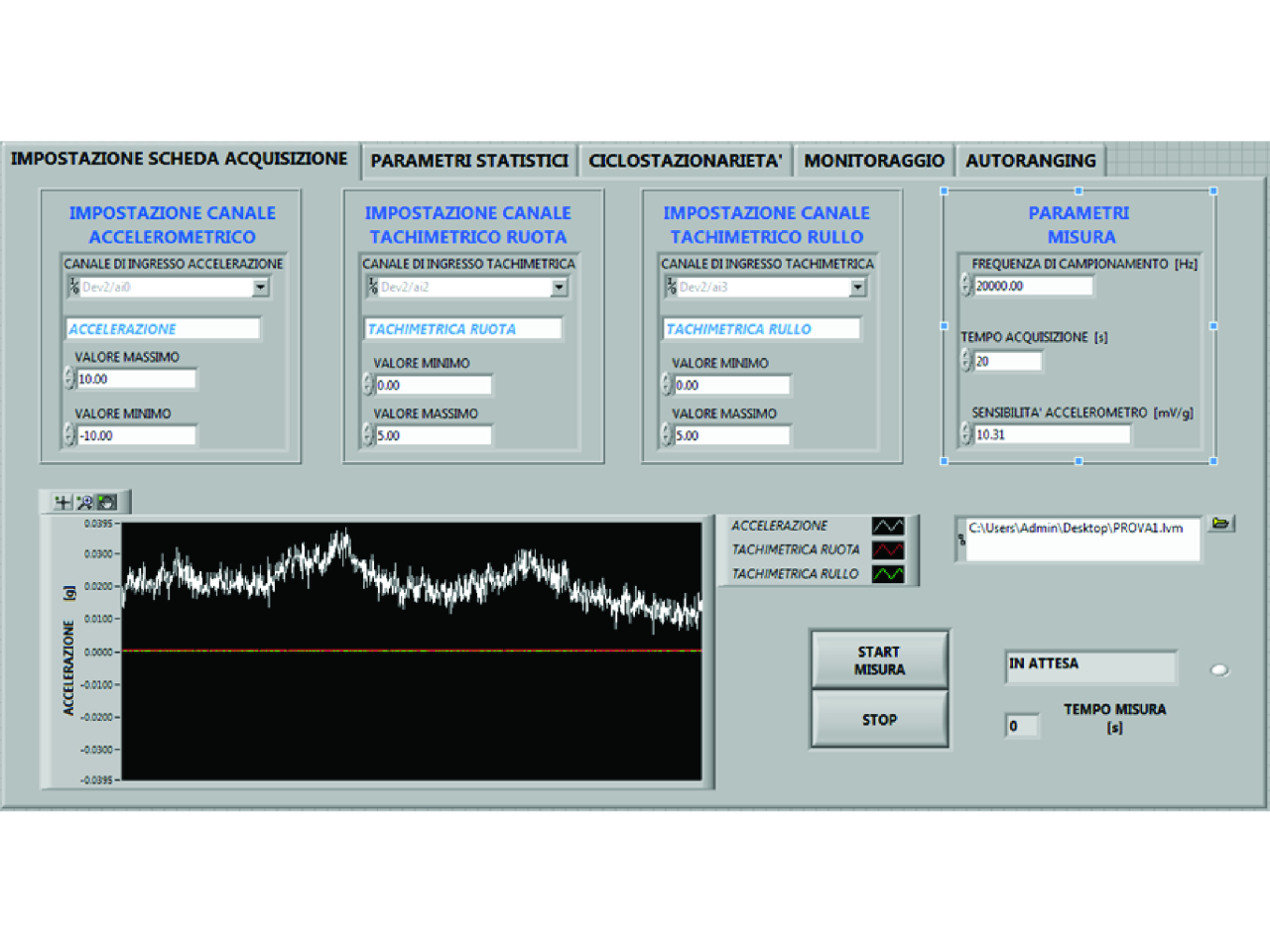