Mechanical parts are affected by geometric and dimensional variations. This variability affects the products’ final quality in terms of performance, process costs, reliability, and customer satisfaction. Geometric Product Specification (GPS) research field aims to optimize the calculation and management of 3D tolerance stacks. The LaPIS laboratory @ INTERMECH-Mo.Re. proposes a CAD-based integrated design method, in which GPS is managed since the initial design stages, in order to avoid expensive revisions and redesign activities. Hence, this method improves the accuracy of calculation by a 3D approach, which is able to catch the 3D complexity of the problem from several aspects (parts, assembly fixture, process). Also, the implementation of this method in an integrated CAD-based environment allows to create a virtual tool that significantly decreases the dispersion of data and eases the management of information.
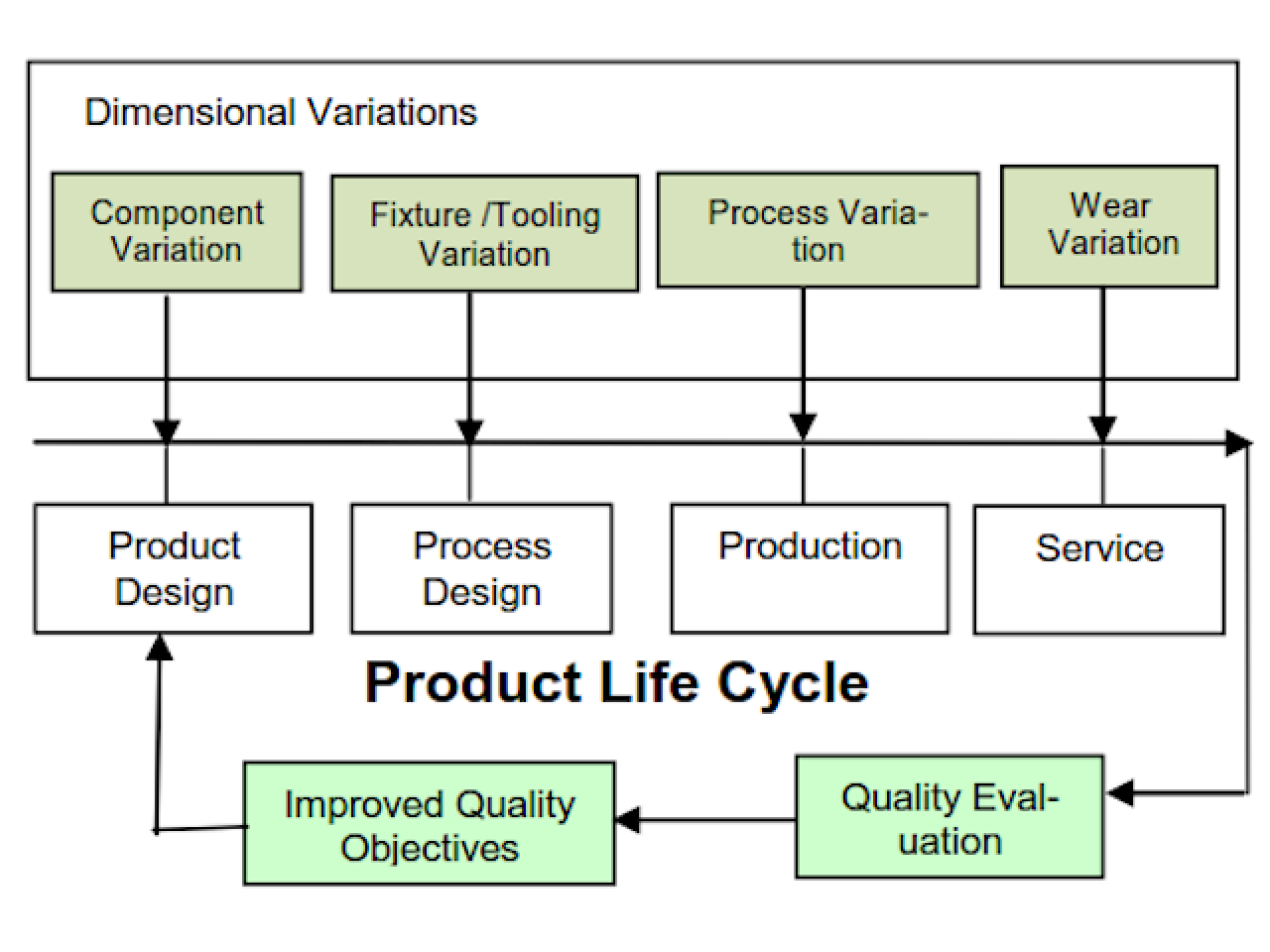
The analysis uses a 3D method based on a Monte-Carlo approach and the analysis of sensitivity of contributors. This allows to statistically calculate the variability measure points. The information related to the components are embedded into 3D models, allowing: the direct access from the design platform, the reduction of the dispersion of data and of the time to market of the product. The production equipment are parametrized inside a virtual environment, in order to evaluate their influence to the products quality, especially due to the locators’ type and layout. That allows to optimize the process of referencing components. The integration within a CAE platform, allows to take into account the deformations during the assembly phases and thus, to find the most suitable assembly strategy.
Design and assembly in high complexity systems, also characterized by high numerosity of components, such as: automotive, aerospace, precision engineering.
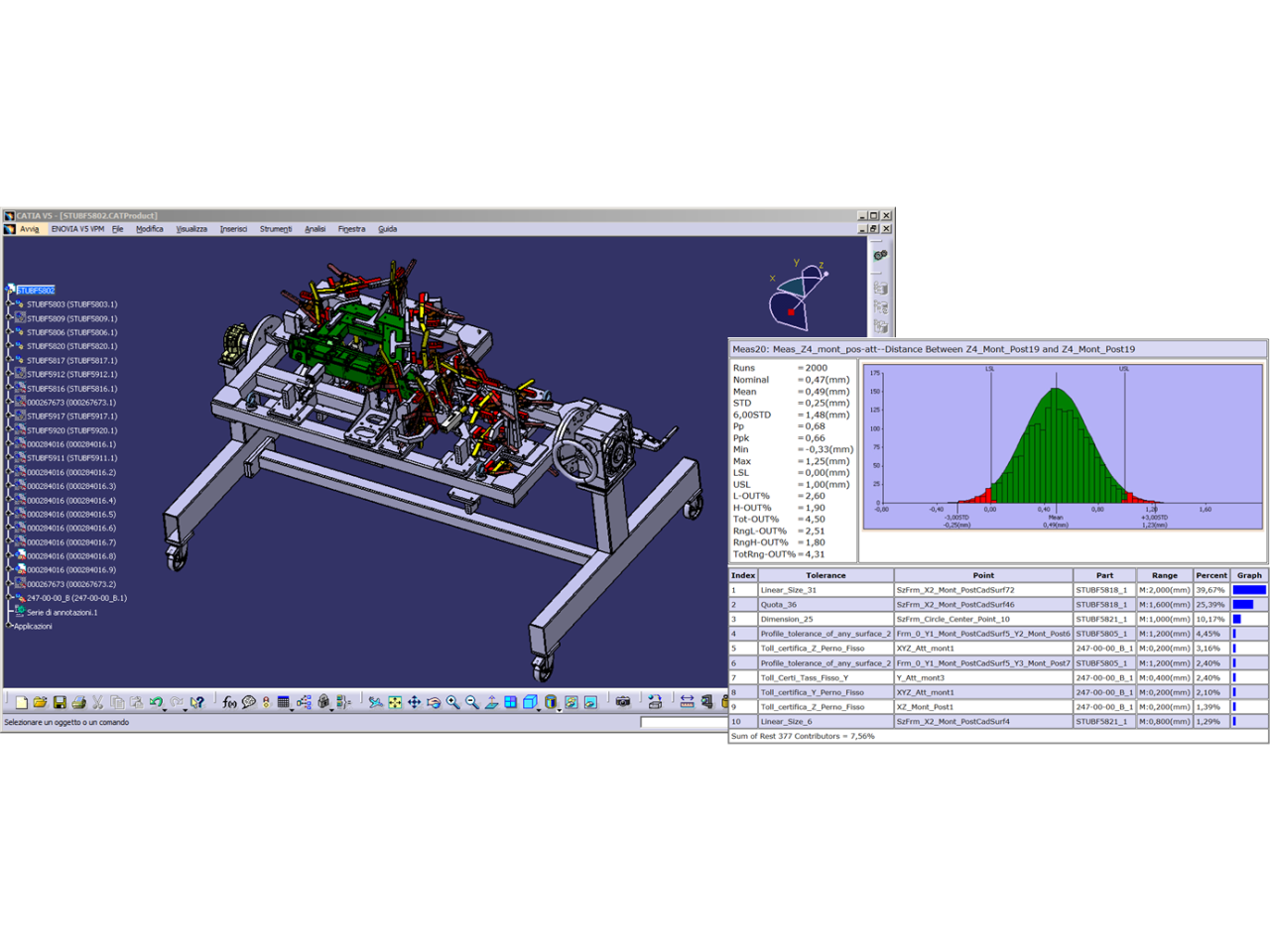
Assembly of automotive chassis subgroup, with verify: loading on assembly in jigs and assembly requirements
The analyzed assembly is a subgroup of an automotive chassis, obtained from semimanufactured parts, referred by assembly equipment or best-fit positioning. The project requirements are: avoidance of geometrical and dimensional interference conditions, for a correct assembly; respect of the maximum allowable gap during the assembly process (welding). The CAD assembly is analyzed on the basis of its component’s functions. Hence, a strategy model for defining the components localization on the assembly fixture is built. Then are defined the components surface connection and the necessary measure for verify the process requirements. The geometric and dimensional tolerances and datum, for components and assembly fixture are allocated in the CAD-based environment. The components loading sequence, on jigs, are modeled and simulated inside the virtual environment. This it was made for different configurations. The tolerance stacks analysis, for different measure points, allows to obtain: - Graphic. The results are displayed directly on the 3D model, improving the analyst’s ability to visualize the effect of variation on the design. - Statistic. A distribution curve is calculated, and shows which tolerances most influence the variability of the measure. Development and optimization of tolerances allocation and calculation of tolerance stacks. This is gained through the integration of 3D features, relative to positioning and assembly. High integration of the method into the industrial field, by a robustCAD-based environment, which allows the use of theorical an experimental data for a rapid and precise distribution of information.
Ferrari SpA, Group OMR SpA
The LaPIS laboratory @ INTERMECH-Mo.Re. proposes a collaboration with companies which are interested in the investigation and development of solutions, to enlarge and improve the tolerance analysis method for different industrial assembly process.
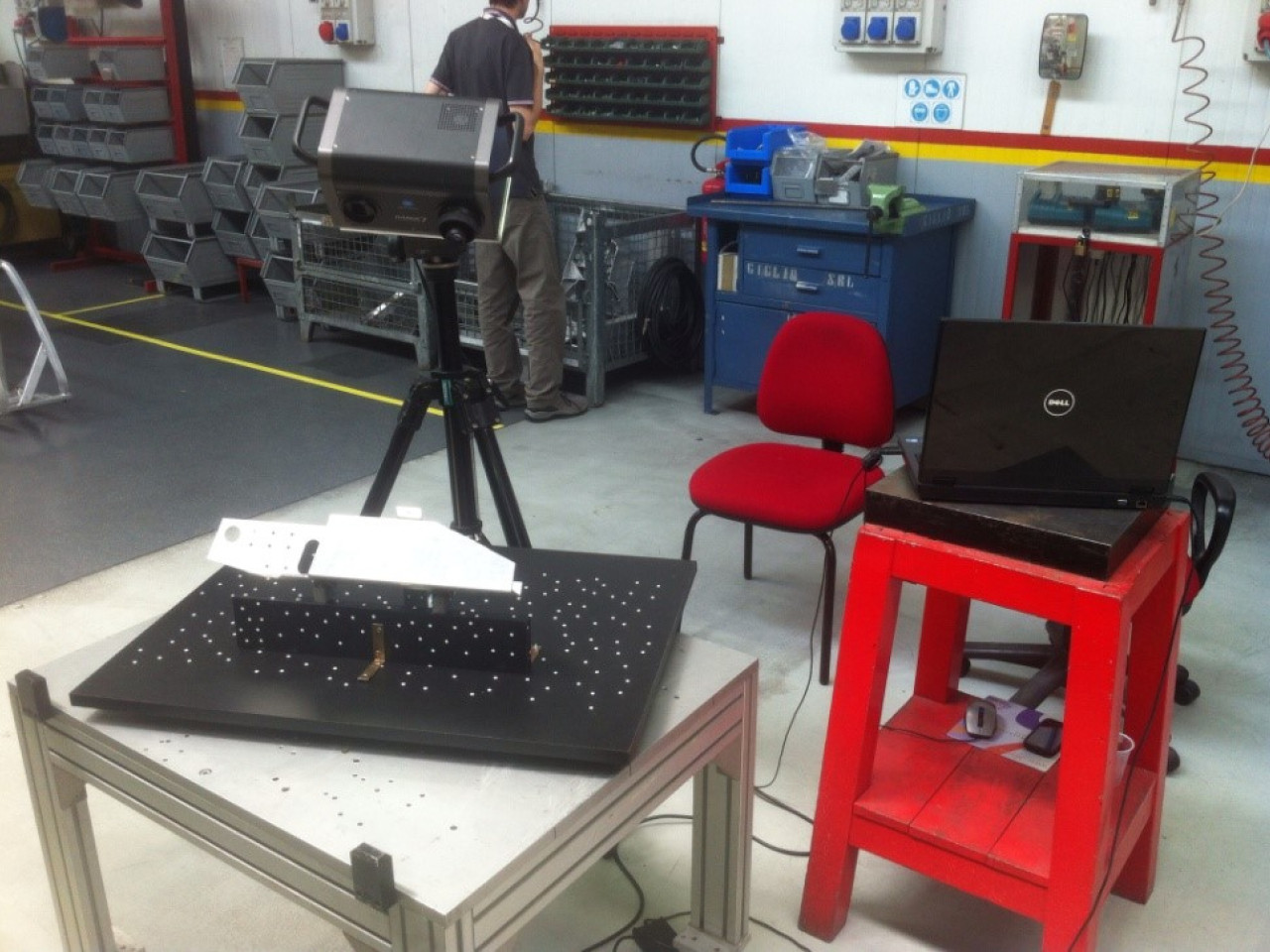