In innovative-design automatic machines, the motion laws of the end-effectors (EEs) may be varied by programming motion profiles imposed by electrical drives. However, EEs normally have one degree of freedom only and cannot change the type of movement they perform. The replacement of EEs with robotic heads with several degrees of freedom, which assure the utmost versatility of the trajectories to be executed, allowed a prototype of automatic machine of greater flexibility to be developed. A limited set of robotic heads acts as a set of modules the machine consists of. These modules have high dynamic performance, by virtue of low-inertia parallel robotic architectures (motors are located on the frame) and the optimization of servomotors, transmission and stiffness. The modules comply with the cleanliness requirements set forth by the pharmaceutical-sector regulations (automatic machines may be possibility used in clean rooms).
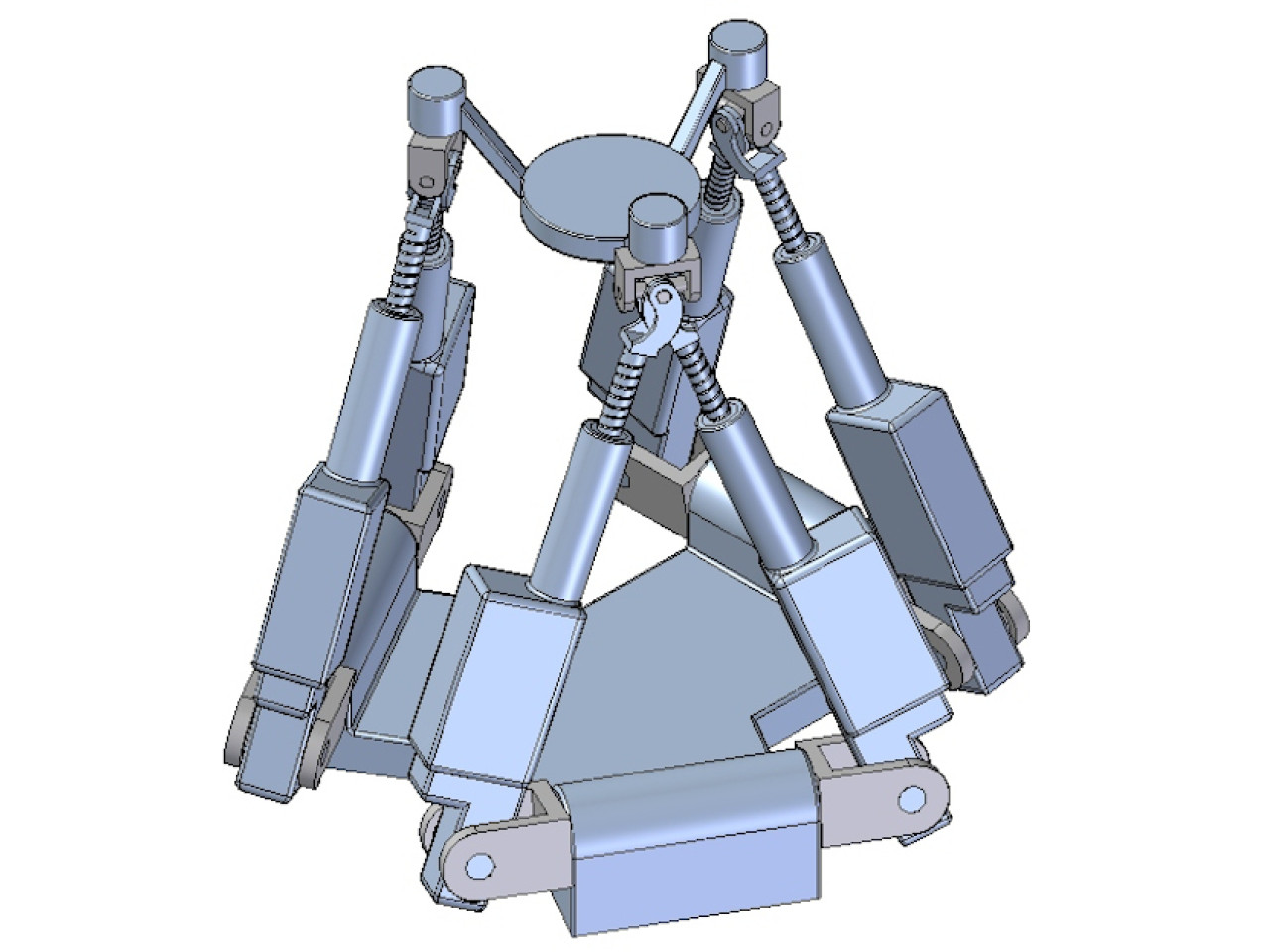
In a traditional automatic machine, in spite of the widespread use of servo-controlled motors, functional assemblies are typically designed in order to perform specific operations, which are suitable to the task to be carried out. A 1 degree-of-freedom (dof) drive allows the end-effector motion law to be changed, but not the type of movement to be performed. This requires the design of tens/hundreds of specialised groups.
Modular, flexible automatic machines with high dynamic performance, to be employed in the pharmaceuticals, cosmetics, food, beverage and tobacco industries.
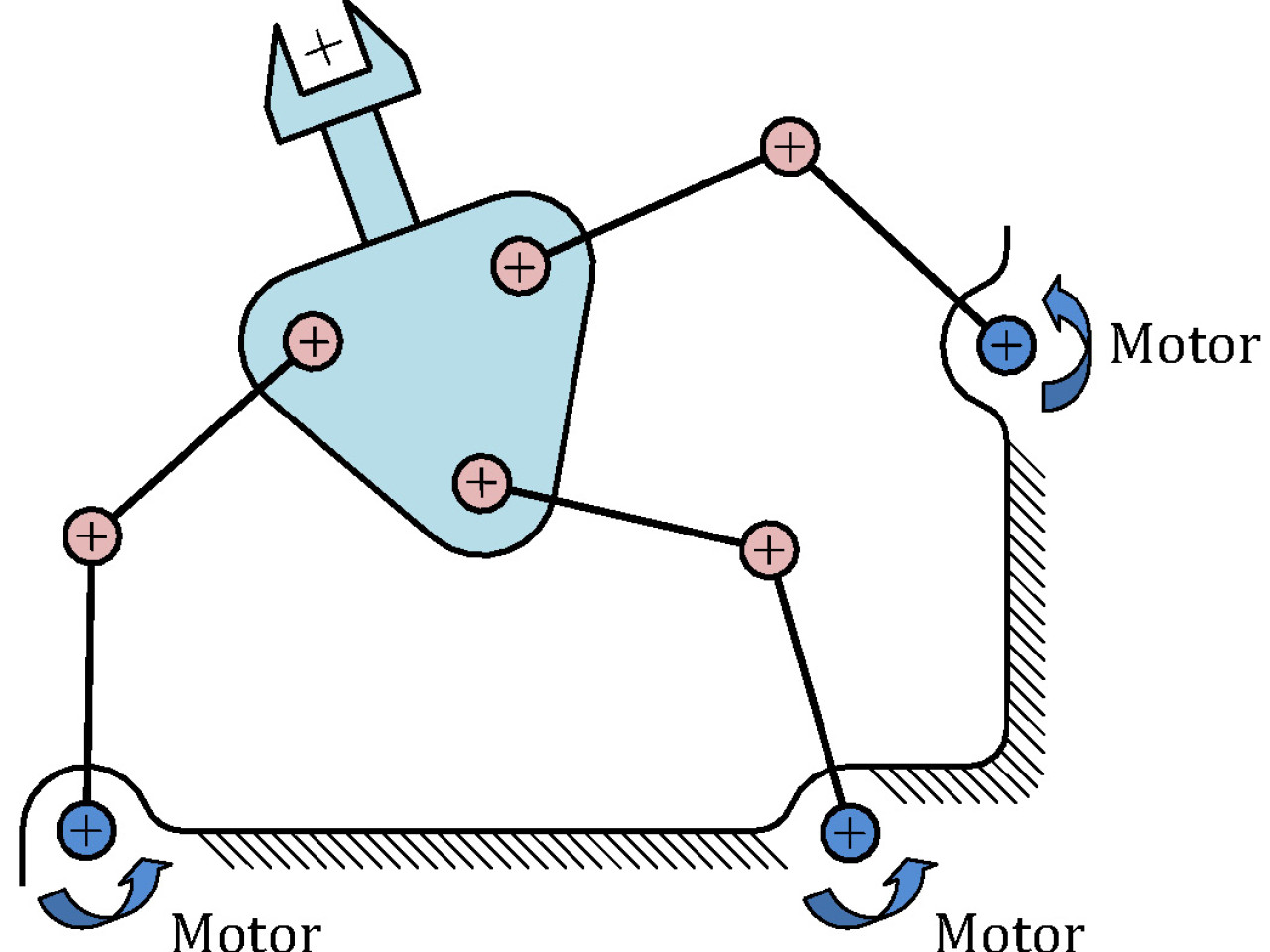
Robot with 3 degrees of freedom for component assembly
The first robotic module to be designed has 3 degrees of freedom: two translations in the plane and a rotation around an axis perpendicular to the plane. The robot is suitable to performing complex assembling movements in the plane, including movements that entail a rotation (very frequent in case of interlocking components). The end effector may be adapted based on the specific application. It is connected to the frame through three dyads. Each dyad consists of two rigid members and exclusively contains revolute kinematic pairs, i.e. rotational joints. The latter is an essential requirement for using the robot in the pharmaceutical sector, where the cleanliness and asepsis requirements restrict the use of rail guides. The robotic module geometry is optimised in order to maximise kinematic and dynamic performance, that is: the widest possible working space for allocated overall dimensions, smaller drives with less power requirement than the motors used in current pick&place mechanisms, maximum flexibility of the trajectories to be performed, low mechanical stress of members and transmission parts. The robotic module is able to cover a working area corresponding to a rectangle sized 200mm x 100mm. In every point of the rectangle, the end effector may perform rotations up to 90°. The prototype is currently being constructed.
GIMA S.p.A., IMA Group, leader in the Automatic Machines sector.
The robot has been developed in cooperation with a company that produces machinery for the pharmaceutical sector. Owing to its versatility, the robotic module may be employed in all sectors where assembly operations are performed.
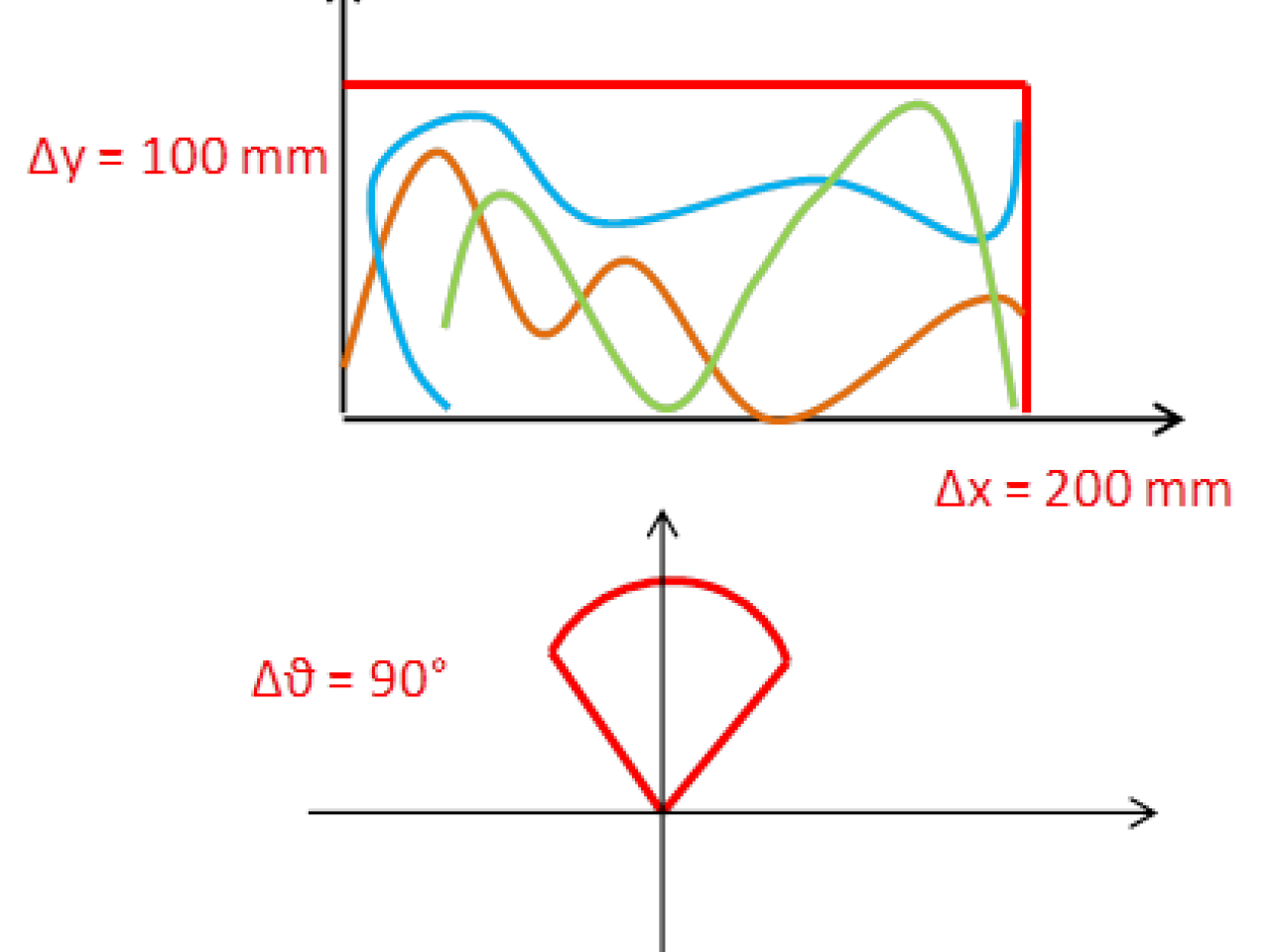