The need has recently arisen in the industrial sector to provide systems and products with operative autonomy. For instance, in the field of logistics, automatic forklifts (AGV, Automatic Guided Vehicle) handle goods in total autonomy. The DIRO’ laboratory -Regional mobile robotics district- has developed a control platform, based on industrial PCs and ROS software (Robotic Operating System), which may be applied in a wide range of industrial and civil applications in a number of operative frameworks. The control system performs all the required operations to make a manual or semi-automatic control device fully autonomous. Examples of this technology are gardening robots, goods handling vehicles, etc.

The robotic platform supports application generality and flexibility, since the computational platform is an industrial PC equipped with a number of input/output interfaces. The control software has been developed in a scalar and modular manner around a robotic research platform (ROS, Robotic Operating system). The entire system has therefore been designed to be deployed on a variety of applications, from industry to the home, in a straightforward, swift and inexpensive way, offering the ability to endow manual products and systems with operative autonomy.
Applications in the industrial sector are manifold, for instance the platform may be used to control mobile surveillance robots, gardening robots, autonomous goods handling systems in warehouses, mobile robots to measure tyre toe-in in garages, etc.
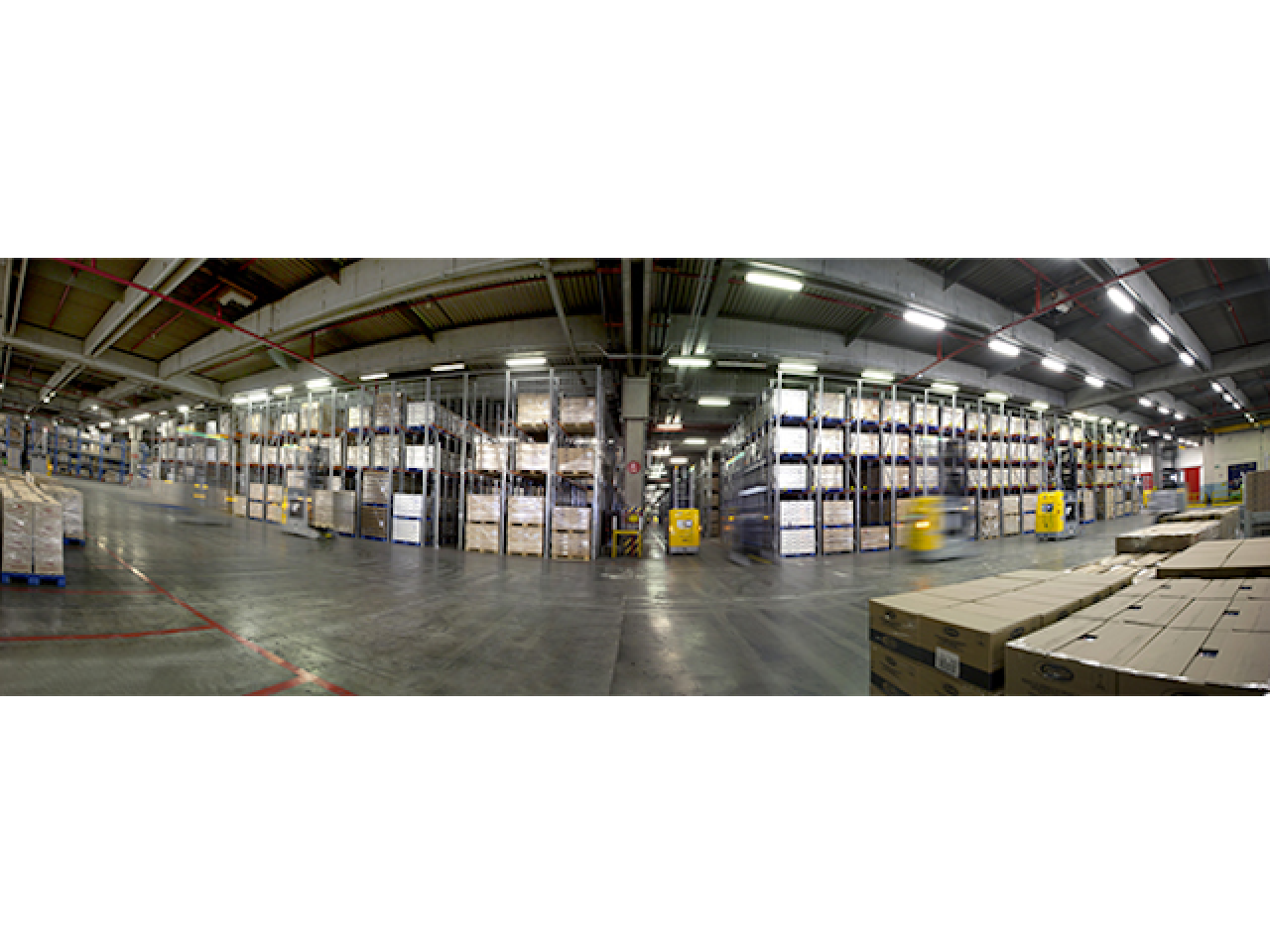
Mobile robot to measure tyre alignment
The application consists in a fully automated robot able to measure without any target, the alignment of cars with wheels up to 30 inches, be they super low profile, off-road lug tread or mounted on wheels used to rubbing against the town's pavements (i.e. in poor condition). A video camera is installed on the robot, which performs detection and 3D reconstruction of the tyre; the lasers identify the position of the bridge and wheel, after which the robot moves to the other axle (in an offset manner so that the lasers never cross). All the data are sent to the central computer and a full scan of the vehicle's alignment is produced in less than two minutes, including any anomalies in the car's geometry. The automation platform automatically guides the system inside the garage to allow the robot to take the correct position to make the measurements. During the project, a mobile robot was developed, able to automatically make tyre measurements in an unstructured setting (garage). This was possible thanks to the development of a control and tracking platform for work environments.
Corghi S.p.A.
ARSControl is seeking technical and commercial partners with the aim of developing mobile automation platforms to increase autonomy, hence the added value, of final products in a shared manner.
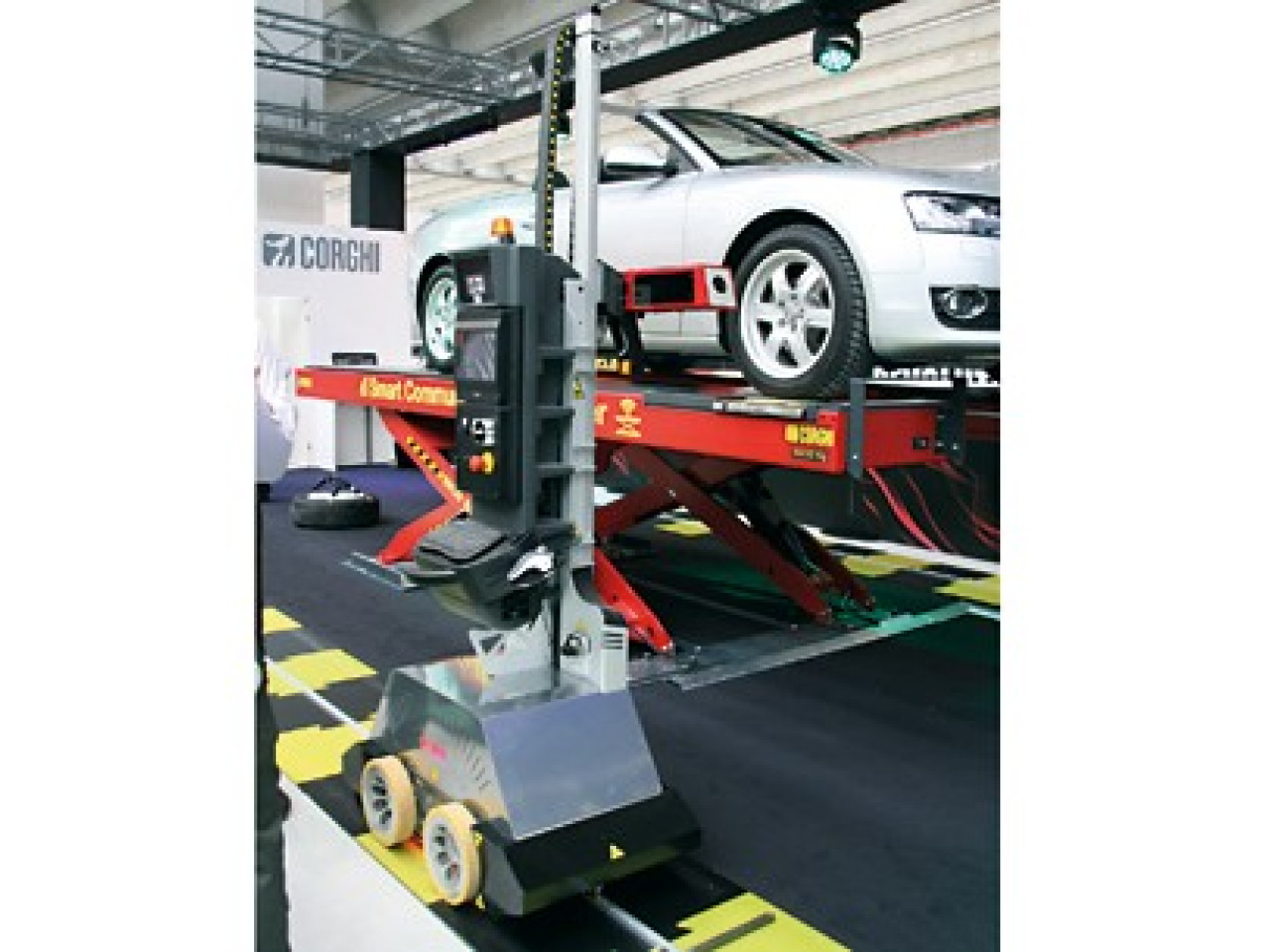