Industrial robots are seldom capable to provide high precision in a mechanical machining process, thus are limited in their industrial use. The LaPIS laboratory @ INTERMECH-Mo.Re. proposes an integrated method for designing robotic systems, with high flexibility and reconfigurability, which are capable to integrate innovative technological solutions, increasing the dimensional and geometric precision of machining. Several novel systems for machining complex automotive and aeronautical components have been introduced, which use both the generation of suitable working trajectories (in an offline mode) and the real-time correction of dynamic errors (online mode). These novel systems have showed a significant higher performance in comparison to state-of-the-art.
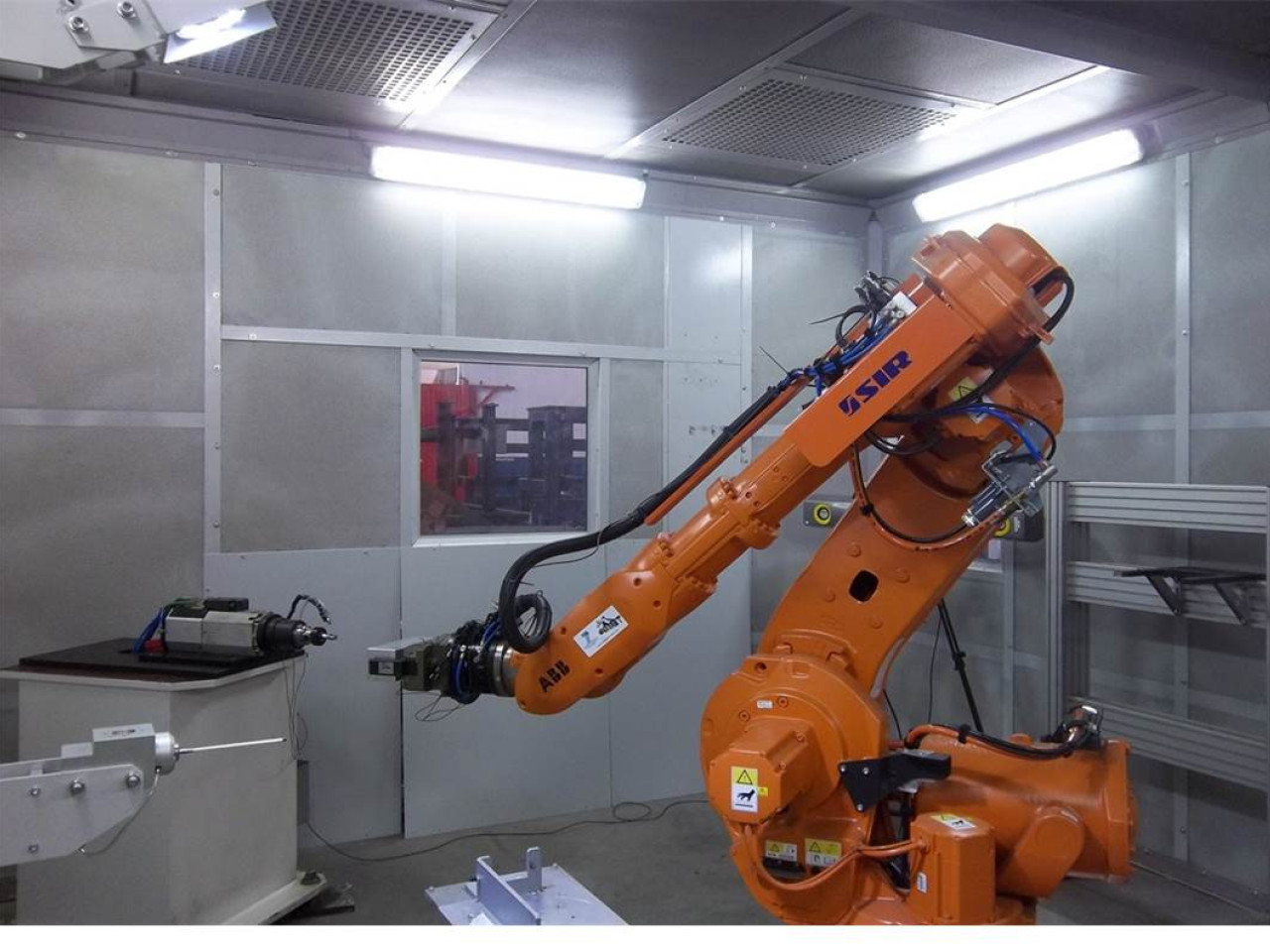
The system architeture provides the integration of various enabling technologies, starting from standard industrial robots: - Innovative programming and 3D simulation interface for the creation of machining paths (prediction of the robot axes singularity, collision detection, management of machining strategies and process parameters, generation of the work’s profile) - Parametric model of the static and dynamic behaviour of the robot under working condition, to identify the unique kinematic characteristics and mechanical properties. - Optical tracking system able to evaluating the deviations of robot’s axes by the programmed positions, real time calculation and communication of the correction of positioning errors to the robot, in quasi-static and dynamic conditions - High response compensation system, able to lower the effects of machining vibrations
Roughing, finishing and deburring of complex components: automotive, aeronautics, agricultural machinery, earthmoving, ceramics sanitary, house and other more.
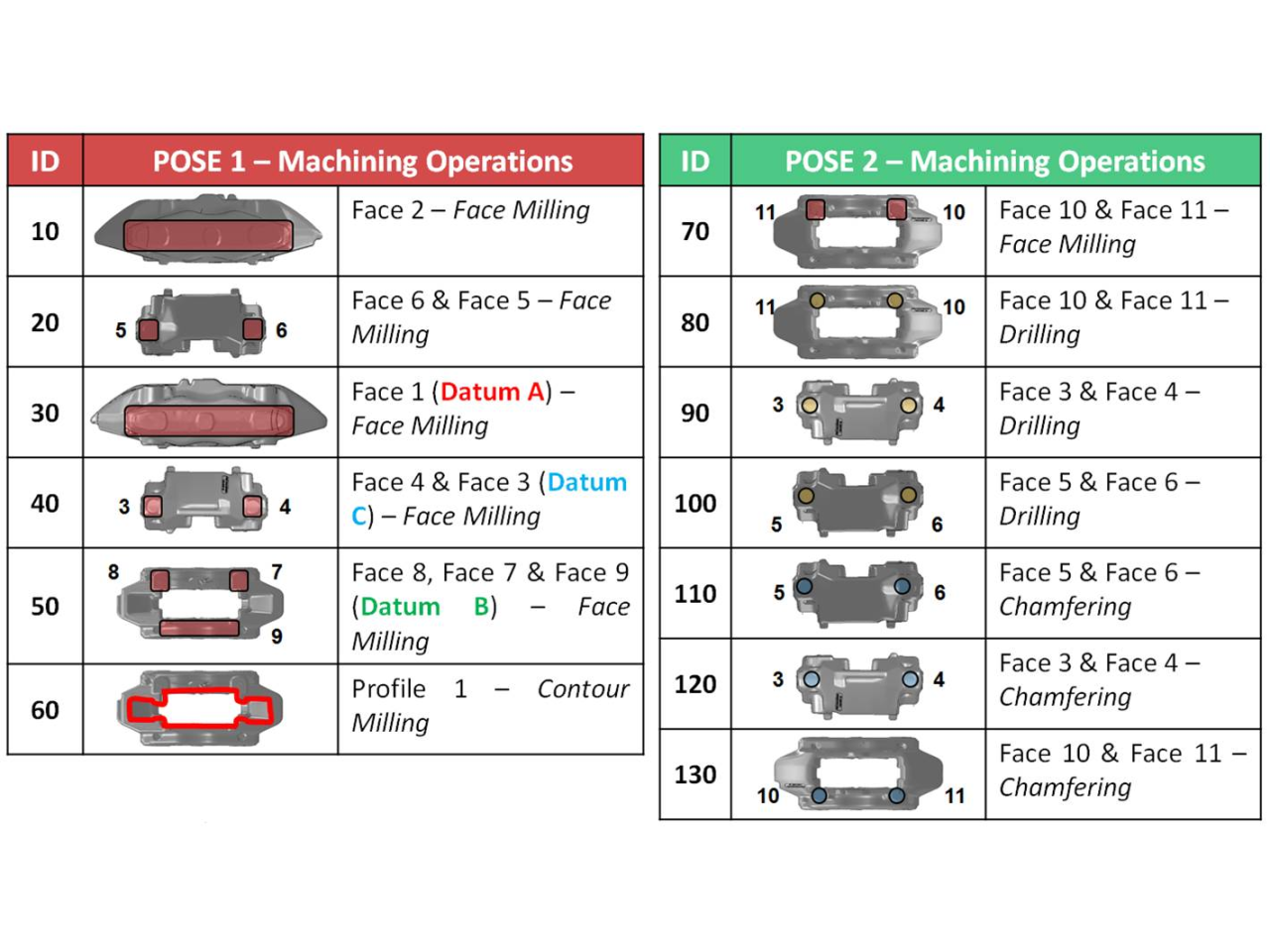
Robotic finishing and deburring on an automotive brake caliper with integrated robot guidance and dimensional control by artificial vision.
The part machined was a brake caliper (dimensions 290mm x 155mm x 80mm) made of aluminum alloy AlSi7Mg0.5. Weight ~ 2,7kg Geometric and dimensional requirements are: - ISO 2768 - f for dimensional tolerance - ISO 2768 – H for geometric tolerance The brake caliper was obtained by subsequent machining steps from a semi-finished aluminum cast. The machining cycle was composed of 15 different processes, such as drilling, milling, smoothing and chamfering, arranged on different sides of the component. Machining was defined by a unique geometric reference, Datum A, B and C, also used for the quality control. Before starting the work cycle, an experimental campaign was performed for the identification of the optimal cutting parameters. The revolution speed in face milling operations was 7100rpm, feed speed 5mm/s. The cut depths was varied from 1mm for roughing to 0,25mm for the last passes. During finishing the spindle speed was increased to 9000rpm. The drilling was processed with a feed speed of 5 mm/s and 6000 rpm. In chamfering, the speed values were: 16000rpm for the spindle and 15mm/s for the feeding. The geometric and dimensional requirements were respected, with a significative enhancement of the machining accuracy, if compared to the standard robotic systems. The production cost by using a robotic system was lower than a CNC production (small production batches with high variability), due to the reduction of time for manual operations.
SIR SpA (Modena)
http://www.sir-mo.it
The LaPIS laboratory @ INTERMECH-Mo.Re. proposes a collaboration with companies interested in the investigation and development of innovative machining solutions by means of reconfigurable robotic systems, with high flexibility for improving geometric and dimensional precision of their industrial processes (ex: machining). [COMET project: Plug-and-produce COmponents and METhods for adaptive control of industrial robots enabling cost effective, high precision manufact. in factory of the future].
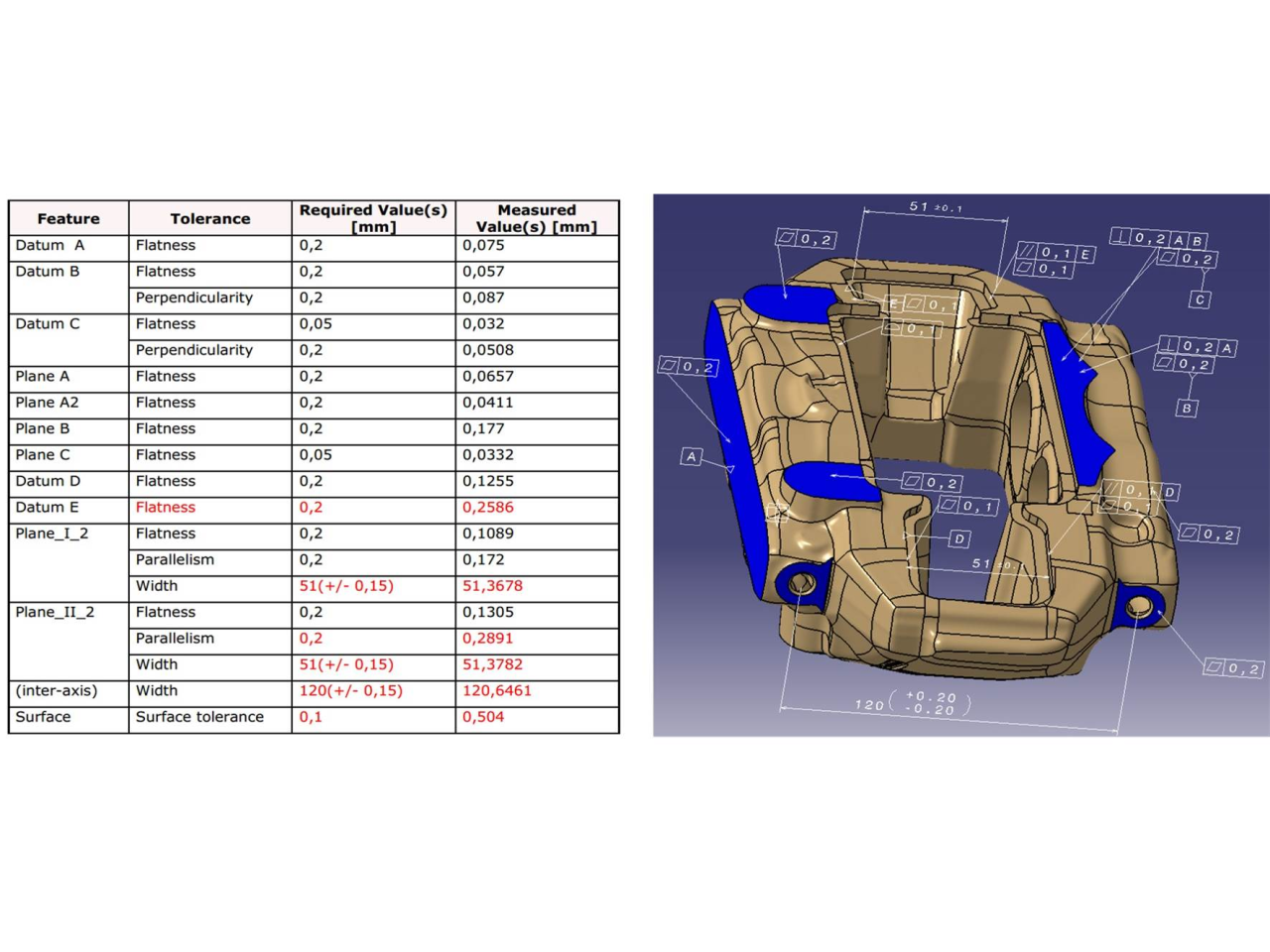