Instrumented test rig for fine-tuning and optimization of servomechanisms and/or single functional components, in particular precision reducers, servomotors and compensation joints.
The servomechanisms can be validated on specific load laws with maximum torques up to 2,000 Nm (torquemeter measurement limit).
2 high-precision encoders, 2 torque meters and temperature probes and sensors for detecting energy consumption allow to measure all efficiency parameters, motion accuracy and energy consumption with high accuracy.
A digital twin of the system allows you to plan the tests and acquire all the data with high sampling frequency
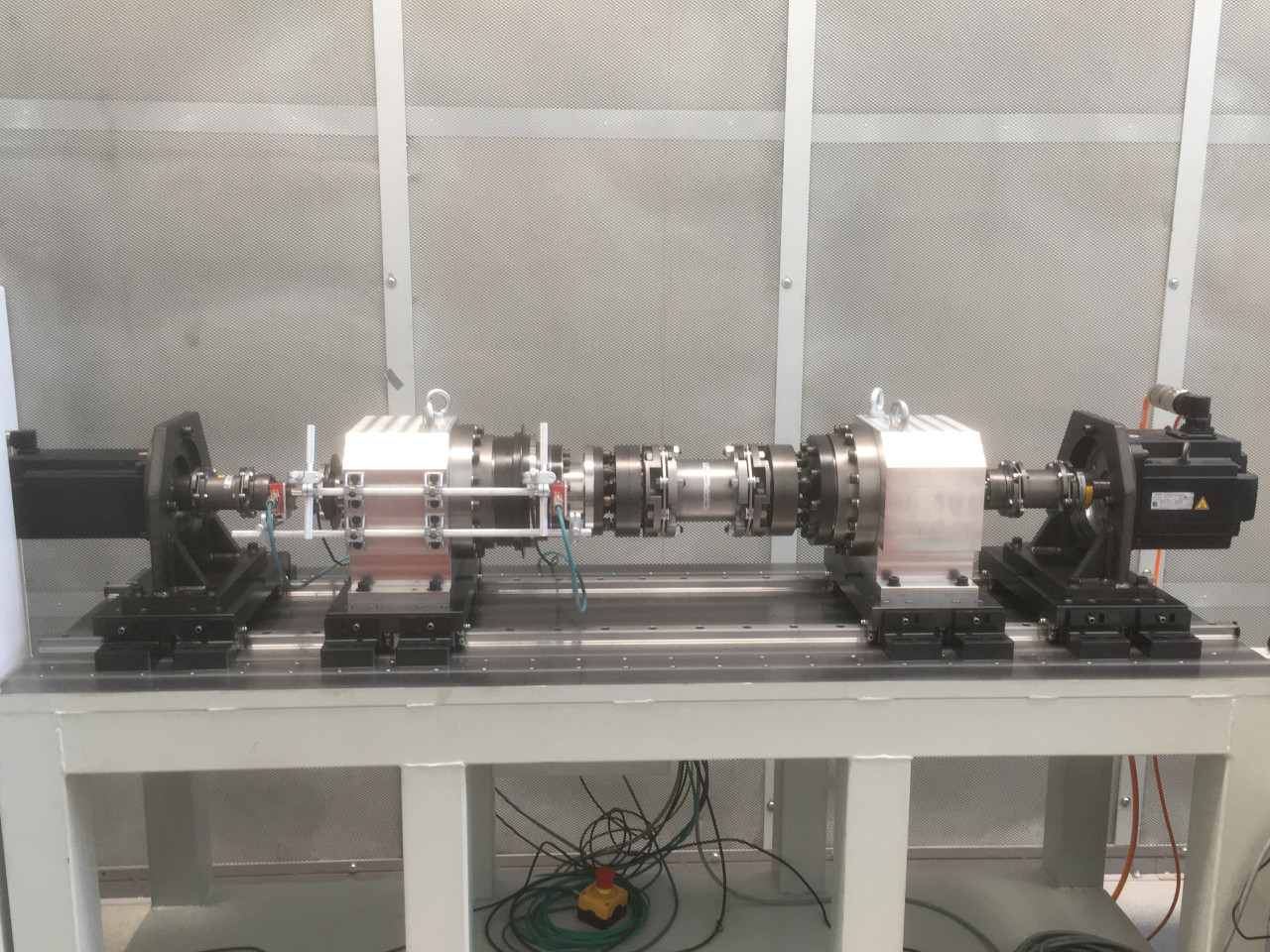
Instrumented test rig for the development and optimization of servomechanisms and/or their individual components, in particular precision gearboxes, servomotors and compensation joints.
The servomechanisms can be validated on specific load laws with maximum torques up to 2,000 Nm (torquemeter measurement limit).
2 high-precision encoders, 2 torque meters and temperature probes, sensors and energy meters allow measuring all efficiency parameters, motion accuracy and energy consumption with high accuracy.
A digital twin of the system enables to plan the tests and acquiring all the data with high sampling frequency.
The system measures a large number of parameters at high frequency and with greater precision to characterize, validate and optimize servomechanisms, reducers and servomotors based on programmed load and/or motion laws.
The load is active and energy regenerative , and allows to validate and optimize servomechanisms of robots and automatic machines in safe conditions
The system has been employed to improve the accuracy and energy consumption of robotic arms
1. Characterization of precision gearboxes, analysis and optimization of motion transmission errors, product optimization (manufacturers of gearboxes and power transmissions)
2. Optimization of the motion precision of robotic arms, compensation algorithm of the transmission error and vibration reduction (robotic system integrators)
3. characterization of servomotors
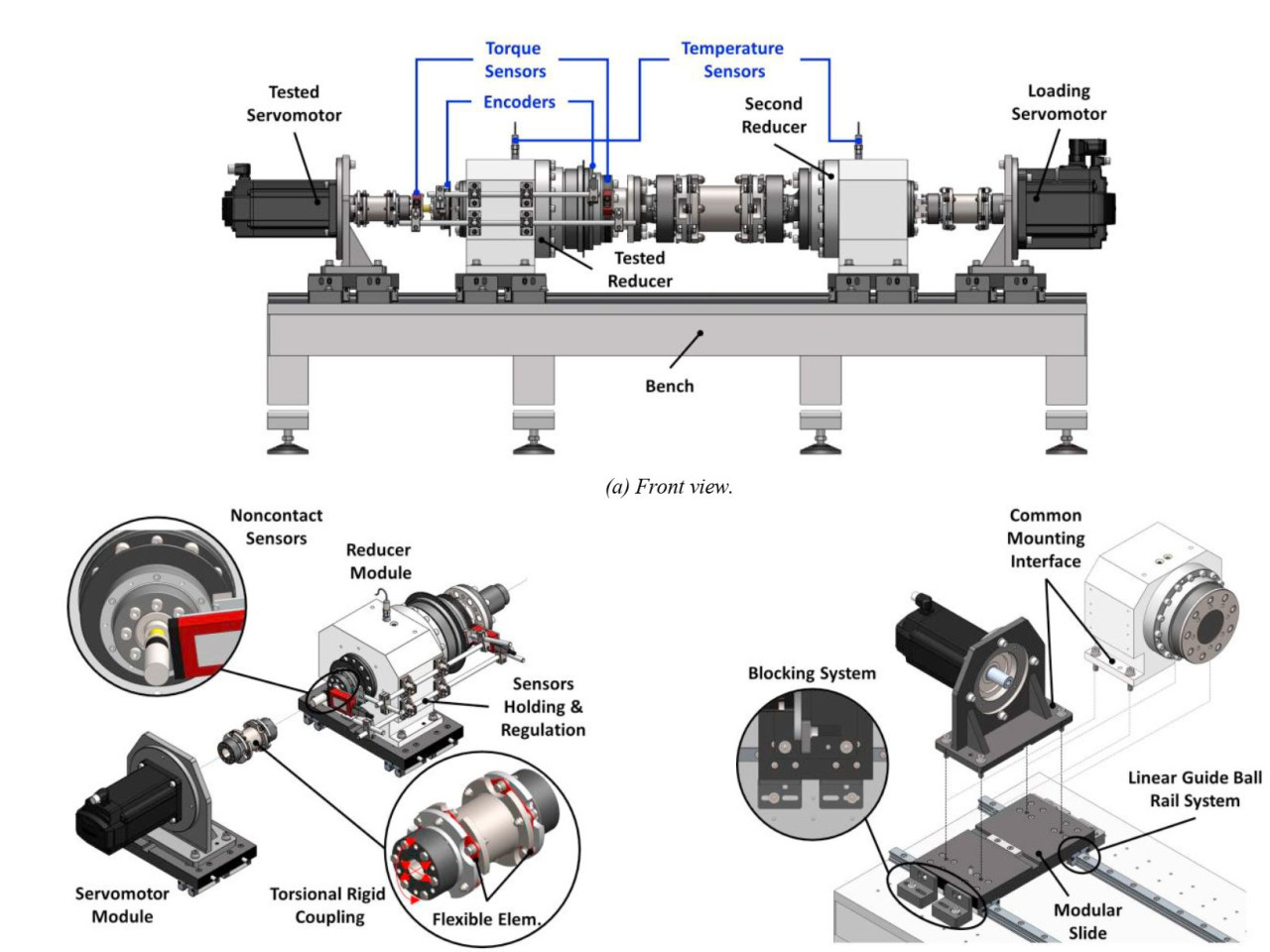
1. Characterization of precision gearboxes, analysis and optimization of motion transmission errors, product optimization (manufacturers of gearboxes and power transmissions)
2. Optimization of motion accuracy of robotic arms, transmission error compensation algorithm and vibration reduction (system integrators)
3. characterization of servomotors
1. Characterization of precision gearboxes, analysis and optimization of motion transmission errors, product optimization (manufacturers of gearboxes and power transmissions)
2. Optimization of the motion precision of robotic arms, transmission error compensation algorithm and vibration reduction (robotic system integrators) for precision assembly and measurement applications on large components (aerospace)
Companies in the field of mechatronics
Barbalab srl
1. Characterization of precision gearboxes, analysis and optimization of motion transmission errors (manufacturers of gearboxes and power transmissions)
2. Optimization of the motion precision of robotic arms, transmission error compensation algorithm and vibration reduction (robotic system integrators) for precision assembly and measurement applications on large components (aerospace)
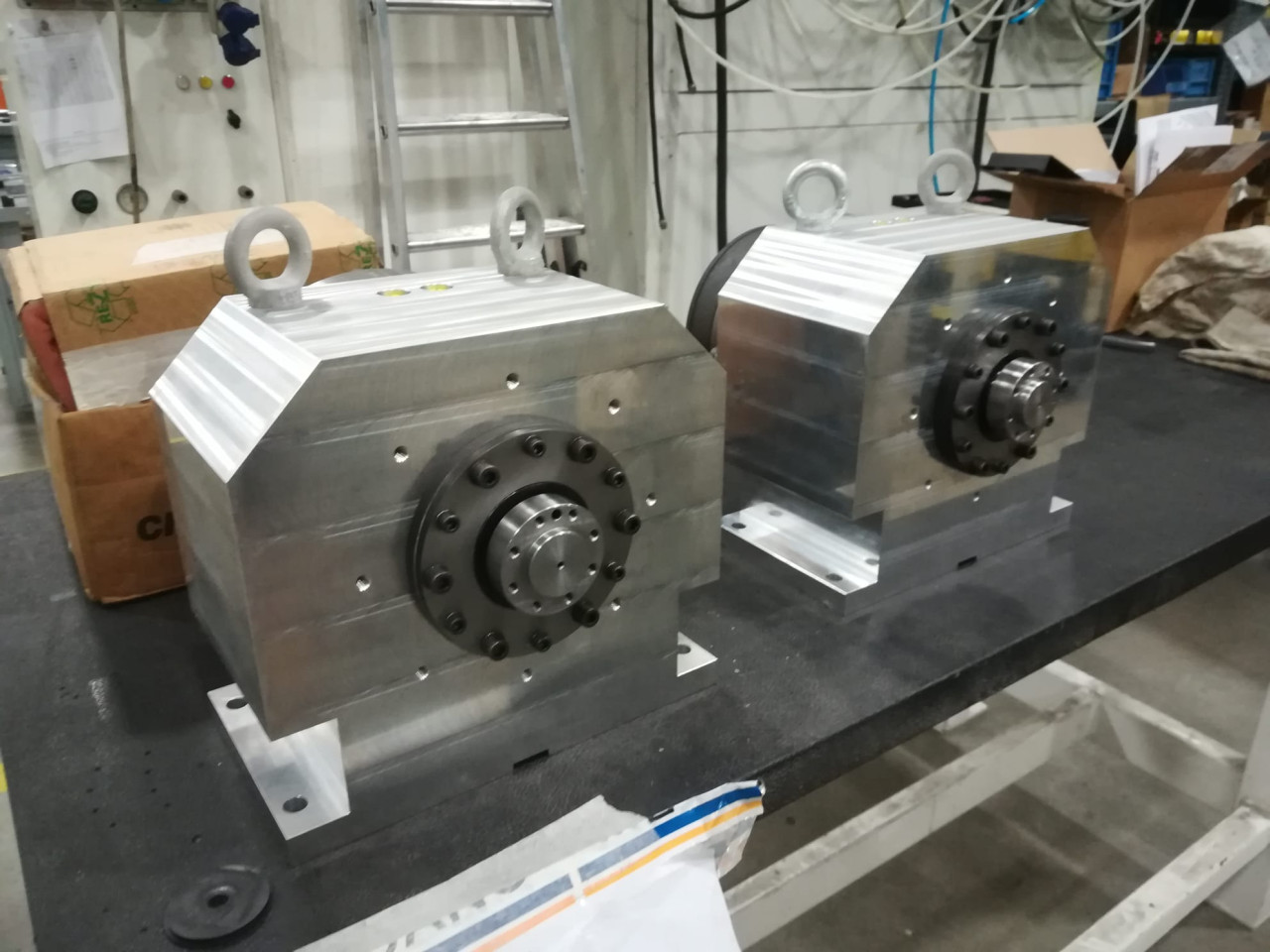